
переработка
.pdf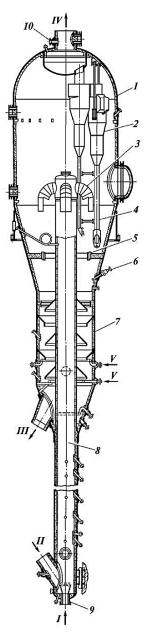
vk.com/club152685050 | vk.com/id446425943
части лифт-реактора к его диаметру обычно составляет (20…25)/1,0.
Первоначально в верхней части лифтреактора были установлены конический переходник и распределительная решетка, предназначенная для ввода и равномерного распределения катализатора в зоне форсированного кипящего слоя. При использовании более высоких температур крекинга и применении современных высокоэффективных катализаторовнежелательнодлительноеконтактирование закоксованного катализатора
ипродуктовкрекинга,таккакэтоспособствует протеканию вторичных реакций крекинга бензина. Поэтому распределительная решетка в верхней части лифт-реактора была заменена на баллистический сепаратор.
Для быстрого отделения катализатора от нефтепродуктов в верхней части лифт-реак- тора установлен баллистический сепаратор 3, позволяющий исключить нежелательную излишнюю глубину превращения сырья
иуменьшить время его контакта с катализатором. Верхняя часть лифт-реактора с баллистическим сепаратором оснащена подвижной опорой 5.
Пройдя баллистический сепаратор, катализатор поступает в десорбер 7, где отпаривается в противотоке с водяным паром. Десорбер секционирован каскадными перфорированными конусами, препятствующими созданию поршневого режима. В нижней части десорбера установлены кольцевые кол-
Рис. 6.24. Реактор с пылевидным катализатором установкиГ43-107:
1 — корпус; 2 — двухступенчатые циклоны; 3 — баллистический сепаратор; 4 — стояки циклонов; 5 — подвижная опора; 6 — форсунка для шлама; 7 — десорбер; 8 — лифт-реактор; 9 — сопло с многочисленными форсунками; 10 — штуцер предохранительного клапана. Потоки: I — сырье; II — регенерированный катализатор; III — закоксованный катализатор; IV — продукты крекинга; V — водяной пар
714

vk.com/club152685050 | vk.com/id446425943
лекторы для ввода водяного пара, в верхней части — форсунки 6 для ввода шлама, т.е. части остатка из ректификационной колонны, содержащей унесенный из реактора катализатор.
Для уменьшения уноса катализатора в ректификационную колонну и снижения количества рециркулирующего шлама в верхней части реактора устанавливаются одноили двухступенчатые циклоны 2. На спускных стояках циклонов используют устройства типа клапан-ми- галка. Клапан-мигалка обычно находится в закрытом положении и открывается только под давлением столба катализатора, скопившегося в спускном стояке.
Корпус реактора изнутри |
|
футерован слоем жаростойко- |
|
го торкрет-бетона толщиной |
|
50 мм, а циклоны защищены |
|
эрозионно стойким бетоном |
|
толщиной 20 мм, нанесенным |
|
на панцирную сетку. |
|
В корпусе реактора преду- |
|
смотрены штуцеры для ввода |
|
сырья и катализатора, вывода |
|
продуктов крекинга и закоксо- |
|
ванного катализатора, установ- |
|
ки предохранительного клапа- |
|
на и термопар, а также люк-лаз, |
|
предназначенный для ремонта |
|
и монтажа оборудования, рас- |
|
положенного внутри аппарата. |
|
Конструкция регенератора |
|
крекинг-установки приведена |
|
на рис. 6.25. |
|
Основными узлами реге- |
|
нератора являются корпус 1, |
|
коллектор ввода воздуха 2 для |
|
выжига кокса и поддержания |
|
кипящего слоя во взвешенном |
|
состоянии, топливные фор- |
Рис. 6.25. Регенератор с пылевидным катализатором: |
сунки 3 для разогрева катали- |
1—корпус;2—коллектордлявводавоздуха;3—топ- |
затора при пуске установки, |
ливная форсунка; 4 — форсунки для конденсата; |
5—двухступенчатыециклоны; 6 — сборная камера. |
|
форсунки для конденсата 4 |
Потоки: I — закоксованный катализатор из реакто- |
дляпредотвращениядогорания |
ра;II—регенерированный катализатор;III—воздух; |
IV — водяной пар; V — дымовые газы |
715
vk.com/club152685050 | vk.com/id446425943
окиси углерода в двуокись, двухступенчатые циклоны 5, сборная камера 6 и система ввода водяного пара в циклоны первой ступени и под днище сборной камеры для предотвращения догорания окиси углерода
вдвуокись. В отдельных случаях для съема избыточного тепла и упорядочения движения потока газовзвеси в зоне регенерации устанавливаются пароводяные змеевики.
Обычно регенератор — самый крупный аппарат на установке каталитического крекинга, его объем значительно превышает объем реактора. Размеры регенератора зависят от его производительности по сжигаемому коксу (количество кокса, выжигаемого с поверхности закоксованного катализатора за единицу времени) и выбранного технологического режима процесса регенерации (температура, давление). Производительность регенератора характеризуется количеством выжженного кокса в единицу времени и определяется как произведение количества циркулирующего катализатора на разность содержаний кокса на нем до и после выжига.
Для теплоизоляции и предотвращения абразивного износа корпуса регенератора со стороны постоянно движущихся значительных масс катализатора его изнутри покрывают слоем жаростойкого торкрет-бе- тона толщиной 150…200 мм, нанесенного на панцирную сетку. Применение торкрет-бетона позволяет снизить температуру и толщину стенкикорпусарегенератора.Быстроеотделениекатализатораотпаров нефтепродуктов на выходе из лифт-реактора стало необходимым условием современных высокотемпературных установок каталитического крекинга, работающих при температурах свыше 525°С.
Для оптимального отделения катализатора от нефтепродуктов
влифт-реакторе необходимо во избежание повторного крекинга бензина предотвратить каталитический крекинг в разбавленной фазе после лифт-реактора и, сокращая время пребывания паров на участке между выходом из лифт-реактора и зоной резкого охлаждения, в главной ректификационной колонне свести к минимуму термический крекинг. Крометого,системаотделениякатализатораотнефтепродуктовдолжна обладать операционной гибкостью и не требовать повышенного внимания со стороны оператора, сводить к минимуму коксование в трубопроводах и уменьшать потери катализатора в ректификационной колонне. Наиболее полно всем этим требованиям отвечает концевое устройство лифт-реактора в виде циклонов с замкнутым потоком.
Система впрыскивания сырья оказывает решающее влияние на выходыпродуктовустановоккаталитическогокрекинга.Видеалереакции крекинга должны протекать в паровой фазе на поверхности твердого
716
vk.com/club152685050 | vk.com/id446425943
катализатора. Быстрое и равномерное смешение сырья и катализатора обеспечивает более полное испарение нефтепродуктов и лучший их контакт с катализатором на протяжении короткого времени их пребывания в лифт-реакторе.
6.8.2. Реакторы каталитического алкилирования
К аппаратам политропического типа относятся реакторы, выполненные в виде кожухотрубчатых теплообменных аппаратов, у которых обычно трубное пространство заполнено гранулированным катализатором и является, таким образом, реакционным объемом, а через межтрубное пространство пропускается агент, осуществляющий теплообмен через поверхность трубок. Такое конструктивное оформление реактора позволяет иметь развитую поверхность теплообмена и небольшую толщину слоя катализатора, а следовательно, сравнительно небольшое различие температур. Последнее обстоятельство является особенно важным для реакций, которые эффективно протекают только
вузких температурных пределах.
Ваппаратах, где реакции экзотермические и температурный режим относительно невысок, отвод тепла зачастую осуществляют водой, испаряющейсявмежтрубномпространстве.Использованиеиспаряющейся воды в качестве теплоагента позволяет иметь заданную температуру
влюбой части теплообменной поверхности, изменяя давление испаряющейся воды, можно регулировать температурный режим процесса. При изменении давления в межтрубном пространстве изменяется температура кипения воды, разность температур между теплообменивающимися средами, а следовательно, и теплосъем.
К реакторам политропического типа относятся также аппараты, конструктивно оформленные по аналогии с теплообменниками типа «труба в трубе»: во внутренней трубе размещается катализатор, а через кольцевое пространство пропускается теплоагент.
Для осуществления химической реакции в изотермических условиях необходимо обеспечить интенсивное перемешивание и высокоэффективный теплообмен в аппарате. В реакторах для таких процессов обычно используют псевдоожиженные слои катализатора или теплоносителя, применяют различные смесительные устройства (мешалки) и т.п.
Вкачествепримерареакторасизотермическимиусловиямирассмотримаппараты,применяемыедляпроцессаалкилированияизобутанабутиленами с целью получения высокооктанового компонента бензина – алкилата (изооктана).
717

vk.com/club152685050 | vk.com/id446425943
Реакция в аппарате осуществляется в жидкой фазе при температуре 5…10°С с использованием в качестве катализатора 95…98%-й серной кислоты. Концентрация кислоты в реакционной смеси в зоне реакции составляет около 50% об. при расходе катализатора, равном 10…15% массы продуктов алкилирования. С понижением ее концентрации кислотасрабатываетсявследствиепоглощенияеюнекоторыхорганических соединений и воды, растворенной в исходном сырье. Для подавления реакции полимеризации бутиленов в зоне реакции обеспечивается значительный избыток циркулирующего изобутана.
На рис. 6.26 изображен горизонтальный реактор (контактор) сернокислотного алкилирования. Исходное сырье и кислота подаются в зону наиболее интенсивного смешения на вход пропеллерной мешалки 5. Далее смесь сырья и кислоты поступает в кольцевое пространство между корпусом 1 и циркуляционной трубой 2, циркулируя по замкнутому контуру в трубчатом пучке, как это показано стрелками на рисунке. Для отвода тепла, выделяющегося при экзотермической реакции,внутрициркуляционнойтрубыразмещаетсяразвитаяповерхность теплообмена с U-образными теплообменными трубками 4. Охлаждающим агентом являются освобожденные от кислоты испаряющиеся продукты реакции. Подобные контакторы выполняются также и в виде вертикальныхаппаратовстеплообменнойповерхностью,выполненной из двойных трубок (свечи Фильда). Хладагентом в этом случае служит испаряющийся аммиак или пропан.
Рис. 6.26. Горизонтальный реактор алкилирования с турбосмесителем:
1 — корпус; 2 — циркуляционная труба; 3 — отражательные перегородки; 4 —трубчатый пучок; 5 — пропеллерная мешалка; 6 — привод. Потоки: I — хладагент; II — продукты реакции; III — кислота; IV — сырье
718

vk.com/club152685050 | vk.com/id446425943
Глава 7
ТЕОРЕТИЧЕСКИЕ ОСНОВЫ И ТЕХНОЛОГИЯ КАТАЛИТИЧЕСКИХ ГОМОЛИТИЧЕСКИХ ПРОЦЕССОВ НЕФТЕПЕРЕРАБОТКИ
В нефтепереработке из каталитических гемолитических (окисли- тельно-восстановительных) процессов промышленное применение получили следующие:
1)паровая конверсия углеводородов с получением водорода;
2)окислительнаяконверсиясероводородавэлементнуюсеру(процесс Клауса);
3)окислительная демеркаптанизация сжиженных газов и бензино-ке- росиновых фракций;
4)гидрирование-дегидрирование нефтяных фракций.
Ниже будут изложены теоретические основы и технология лишь
первых трех из перечисленных выше каталитических процессов. Процессы гидрирования-дегидрирования, осуществляемые в среде водорода и относящиеся по этому признаку, а также по специфичности катализа к гидрогенизационным процессам, будут рассмотрены в следующей главе.
7.1.Теоретические основы и технология процессов паровой каталитической конверсии углеводородов
При углубленной или глубокой переработке сернистых и особенно высокосернистых нефтей того количества водорода, которое производятнаустановкахкаталитическогориформинга,обычнонехватаетдля обеспечения потребности в нем гидрогенизационных процессов НПЗ. Естественно, требуемый баланс по водороду может быть обеспечен лишь при включении в состав таких НПЗ специальных процессов по производствудополнительноговодорода.Средиальтернативныхметодов (физических, электрохимических и химических) паровая каталитическаяконверсия(ПКК)углеводородовявляетсявнастоящеевремя
вмировой нефтепереработке и нефтехимии наиболее распространеннымпромышленнымпроцессомполученияводорода.Вкачествесырья
впроцессах ПКК преимущественно используются природные и заводские газы, а также прямогонные бензины.
Конверсия углеводородного сырья CnHm водяным паром протекает по следующим уравнениям:
719

vk.com/club152685050 | vk.com/id446425943
CnHm + nH2O |
|
|
|
|
|
nCO + (n + 0,5m)H2 – Q1 , |
(7.1) |
||
|
|
|
|
||||||
|
|
|
|
|
|||||
СО + Н2О |
|
|
|
|
|
СО2 + Н2 + 42,4 кДж/моль, |
(7.2) |
||
|
|
|
|
||||||
|
|
|
|
|
где n и m — число атомов соответственно углерода и водорода в молекуле углеводорода.
Естественно, что выход водорода будет тем больше, чем выше содержание его в молекуле углеводородного сырья. С этой точки зрения наиболееблагоприятноесырье—метан,вмолекулекоторогосодержит- ся 25% мас. водорода. Источником метана являются природные газы сконцентрацией94…99%об.СН4.Дляпроизводстваводородавыгодно также использовать дешевые сухие газы нефтепереработки.
Теоретические основы процесса ПКК углеводородов.
Реакция(7.1)являетсясильноэндотермической(приконверсииметанаQ1 =206,7кДж/моль)и,следовательно,термодинамическивысокотемпературной.Вторая стадияпроцессаПККуглеводородов(7.2)протекаетсвыделениемтеплаитермодинамическидлянееболееблагоприятнынизкиетемпературы.ПоэтомунапрактикепроцессыПККпроводят в две ступени при оптимальной для каждой из стадий температуре.
Давлениеоказываетотрицательноевлияниенаравновесиеосновной реакции конверсии метана, и поэтому требуется более высокая температура для достижения одинаковой степени превращения углеводородного сырья. Тем не менее предпочитают проводить процесс под повышеннымдавлением,посколькуполученныйводородиспользуется затем в гидрогенизационных процессах, проводимых под давлением. При этом снижаются затраты на компримирование газа и, кроме того, повышается производительность установки.
Помимо температуры и давления, на равновесие реакций (7.1) и (7.2) существенное влияние оказывает мольное отношение водяной
пар(т.е.окислитель):углеродсырья(δН О).Очевидно,чтоприувеличе-
2
нииотношенияδН О сверхстехиометрическогоравновесияконцентрация
2
метанавгазахконверсиибудетснижаться.Установлено,чтовпродуктах паровойконверсииуглеводородногосырьяпритемпературевыше600°С отсутствуют гомологи метана. Это обусловливается тем, что метан является наиболее термостойким углеводородом по сравнению с его гомологами. Поэтому равновесный состав продуктов паровой конверсии углеводородовпритемпературесвыше600°Собычнорассчитываютпо константе равновесия реакций
СH4 +H2OCO+ 3H2 и
СО +Н2ОСО2 + Н2
720
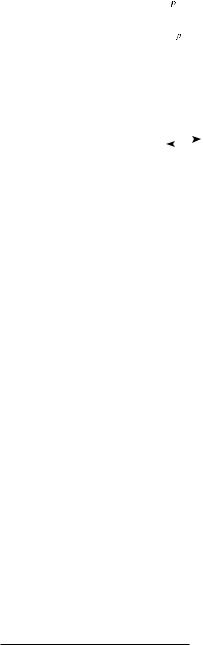
vk.com/club152685050 | vk.com/id446425943
и по уравнениям соответственно 1
lg К0 = 12,3 – 10800/Т и
lg К0 = –1,69 + 1867/Т.
Впроцессепаровойконверсииуглеводородов,помимоосновныхреакций (7.1) и (7.2), при определенных условиях возможно выделение элементного углерода вследствие термического распада углеводорода по реакции
CnHm |
|
|
|
nC + 0,5mH2 – Q3 |
(7.3) |
|
|
||||
|
|
|
Вероятность выделения этого углерода возрастает при увеличении числа углеродных атомов (n) углеводорода, повышении давления
и уменьшении отношения δН О. При этом наиболее опасен темпера-
2
турный режим 500…750°С. При температурах свыше 750°С углеобразование менее вероятно в результате усиления реакций газификации образовавшегося углерода водяным паром и диоксидом углерода. В этой связи промышленные процессы ПКК углеводородов проводят при двух и более кратном избытке водяного пара против стехиометрически необходимого соотношения.
Пароваяконверсияметанасприемлемойскоростьюиглубинойпревращения протекает без катализатора при 1250…1350°С. Катализаторы конверсии углеводородов предназначены не только для ускорения основной реакции, но и для подавления побочных реакций пиролиза путем снижения температуры конверсии до 800…900°С. Как наиболее активные и эффективные катализаторы конверсии метана признаны никелевые,нанесенныенатермостойкиеимеханическипрочныеносители с развитой поверхностью типа оксида алюминия. С целью интенсификации реакций газификации углерода в никелевые катализаторы в небольших количествах обычно вводят щелочные добавки (оксиды Са и Mg).
Паровую конверсию оксида углерода (7.2) проводят в две ступени: сначала при температуре 480…530°С на среднетемпературном железохромовом катализаторе, затем при 400…450°С на низкотемпературном цинкхроммедном катализаторе.
Наоснованиимногочисленныхисследованиймеханизмаикинетики (сиспользованиемкинетических,адсорбционных,изотопныхидругих методов) установлено, что в процессе ПКК углеводородов протекают
1 Справедливо в интервале 800…1200 К.
721
vk.com/club152685050 | vk.com/id446425943
два типа гомолитических реакций через хемосорбцию реактантов на поверхности катализатора:
1.Окислительно-восстановительные реакции, включающие стадии
окисления катализатора окислителями (Н2О, CO2) и восстановления поверхностного окисла восстановителями (СН4, H2, СО):
1.1.Z + Н2ОZ0 + Н2;
1.2.Z0 + СН4Z + СО + 2Н2;
1.3.Z0 + СОZ + СО2.
2.Реакцииуглеобразования(карбидирования)—газификации,вклю- чающие стадии образования поверхностного углерода (карбида металла),метаномиоксидомуглеродаи газификацииповерхностного углерода окислителями (Н2О, СО2):
2.1.Z + CH4Zc + 2H2;
2.2.Zc + Н2ОZ + СО + Н2;
2.3.Zc + СО2Z + 2СО
где Z — активный центр катализатора; Z0 и Zc — центры катализатора,занятыехемосорбированнымкислородомиуглеродомсоответственно.
Технологическая схема установки паровой каталитической конверсии при давлении 2,0…2,5 МПа показана на рис. 7.1.
Традиционныйпроцесспроизводстваводородаэтимметодомвключает следующие основные стадии:
—очистку сырья от сероводорода и сероорганических соединений;
—каталитическую конверсию сырья;
—двухступенчатую конверсию оксида углерода;
—очистку технологического газа от диоксида углерода абсорбцией водным раствором карбоната калия;
—метанирование остатков оксида углерода.
Сырье (природный или нефтезаводской газ) сжимают компрессоромдо2,6МПа,подогреваютвподогревателе,вконвекционнойсекции печи-реакторедо300...400°СиподаютвреакторыР-1иР-2дляочистки от сернистых соединений. В Р-1, заполненном алюмокобальтмолибденовым катализатором, осуществляют гидрогенолиз сернистых соединений, а в Р-2 — адсорбцию образующегося сероводорода на гранули- рованномпоглотителе,состоящемвосновномизоксидацинка(481-Zn, ГИАП-10 и др.) до остаточного содержания серы в сырье <1ррm. В случае использования в качестве сырья бензина последний подают насосом и на входе в Р-1 смешивают с водородсодержащим газом.
722

vk.com/club152685050 | vk.com/id446425943
Рис. 7.1. Принципиальная технологическая схема установки для производства водорода:
I — сырье; II — водяной пар; III — водород; IV — двуокись углерода; V — вода; VI — водный раствор карбоната калия
Кочищенномугазувсмесителедобавляютперегретыйдо400…500°С водяной пар, и полученную парогазовую смесь подают в печь паровой конверсии. Конверсию углеводородов проводят при 800…900°С и давлении2,2…2,4МПаввертикальныхтрубчатыхреакторах,заполненных никелевым катализатором, размещенных в радиантной секции печи в несколько рядов и обогреваемых с двух сторон теплом сжигания отопительного газа. Отопительный газ подогревают до 70…100°С, чтобы предотвратить конденсацию воды и углеводородов в горелках. Дымовые газы с температурой 950…1100°С переходят из радиантной секции в конвекционную, где установлены подогреватель сырья и котел-ути- лизатор для производства и перегрева водяного пара.
Конвертированный газ направляют в котел-утилизатор, где охлаждаютдо400…450°Сиподаютна1ступеньсреднетемпературнойконверсии оксида углерода над железохромовым катализатором (Р-3). После охлаждения до 230…260°С в котле-утилизаторе и подогревателе воды парогазовуюсмесьдалеенаправляютнаIIступеньнизкотемпературной конверсии монооксида углерода в реактор Р-4 над цинкхроммедным катализатором.
Смесь водорода, диоксида углерода и водяного пара охлаждают затем в теплообменниках до 104°С и направляют на очистку от СО2 в абсорбер К-1 горячим раствором К2СО3.
Диоксидуглеродаудаляютрегенерированнымрастворомкарбоната калия в две ступени. На I ступень для абсорбции основной части СО2 подают более горячий раствор К2СО3 в середину абсорбера. Доочистку
723