
переработка
.pdfvk.com/club152685050 | vk.com/id446425943
Таблица 8.6 — |
Влияние химического состава сырья |
|
|
|||||
|
на показатели риформинга на катализаторе КР-106 |
|||||||
|
|
|
|
|
|
|
|
|
Показатель |
|
|
|
Нефть |
|
|
||
I |
|
II |
III |
IV |
V |
VI |
||
|
|
|
||||||
|
|
|
|
|
|
|
|
|
|
|
Сырье |
|
|
|
|
|
|
|
|
|
|
|
|
|
|
|
Плотность, кг/м3 |
|
744 |
|
742 |
742 |
751 |
753 |
746 |
Фракционный состав |
|
|
|
|
|
|
|
|
(объемный),°С: |
|
|
|
|
|
|
|
|
10% |
|
115 |
|
109 |
102 |
115 |
112 |
103 |
50% |
|
133 |
|
128 |
124 |
131 |
1330 |
116 |
90% |
|
160 |
|
155 |
158 |
158 |
166 |
1153 |
Углеводородный состав,%: |
|
|
|
|
|
|
|
|
ароматические |
|
14 |
|
12 |
9 |
13 |
11 |
11 |
нафтеновые |
|
20 |
|
28 |
31 |
28 |
35 |
38 |
парафиновые |
|
66 |
|
60 |
60 |
59 |
54 |
51 |
Выход,%: |
|
|
|
|
|
|
|
|
риформат |
|
84,0 |
|
86,3 |
86,8 |
87,0 |
88,0 |
90,5 |
водород |
|
1,9 |
|
2,2 |
2,4 |
2,1 |
2,3 |
2,5 |
|
|
Риформат |
|
|
|
|
||
|
|
|
|
|
|
|
|
|
Содержание ароматических |
|
|
|
|
|
|
|
|
углеводородов,%: |
|
69 |
|
67 |
68 |
68 |
68 |
67 |
ОЧММ |
|
85,6 |
|
85,0 |
85,0 |
85,0 |
84,6 |
84,7 |
ОЧИМ |
|
95,0 |
|
95,0 |
95,0 |
95,0 |
95,2 |
95,4 |
Примечания:
1.Давление 1,5 МПа.
2.Нефти:I—киркукская;II—ромашкинская;III—ухтинская;IV—самотлорская; V — нижневартовская; VI — смесь шаимской и грозненской.
Поскольку составляющие суммарный процесс реакции риформинга имеютнеодинаковыезначенияэнергииактивации—наибольшеедляре- акцийгидрокрекинга(117…220кДж/моль)именьшеедляреакцийароматизации(92…158кДж/моль),топриповышениитемпературывбольшейстепениускоряютсяреакциигидрокрекинга,чемреакцииароматизации.Поэтомуобычноподдерживаютповышающийсятемпературный режимвкаскадереакторов,чтопозволяетуменьшитьрольреакцийгидрокрекинга в головных реакторах, тем самым повысить селективность процесса и увеличить выход риформата при заданном его качестве.
Температуру на входе в реакторы риформинга устанавливают в начале реакционного цикла на уровне, обеспечивающем заданное качество риформата — октановое число или концентрацию ароматических углеводородов. Обычно начальная температура лежит в пределах 480…500°Силишьприработевжесткихусловияхсоставляет510°С.По
744
vk.com/club152685050 | vk.com/id446425943
мере закоксовывания и потери активности катализатора температуру на входе в реакторы постепенно повышают, поддерживая стабильное качество катализата, причем среднее значение скорости подъема температуры за межрегенерационный цикл составляет 0,5…2,0°С в месяц. Максимальная температура нагрева сырья на входе в последний реактор со стационарным слоем катализатора достигает 535°С, а в реакторы установок с непрерывной регенерацией — 543°С.
Давление — основной, наряду с температурой, регулируемый параметр, оказывающий существенное влияние на выход и качество продуктов риформинга.
При прочих идентичных параметрах с понижением парциального давления водорода возрастает как термодинамически, так и кинетически возможная глубина ароматизации сырья и, что особенно важно, повышается селективность превращений парафиновых углеводородов, поскольку снижение давления благоприятствует протеканию реакций ароматизации и тормозит реакции гидрокрекинга.
В табл. 8.7 приведены данные по влиянию давления на выход целевых продуктов при риформинге гидроочищенной фракции бензина 85...180°С на катализаторе КР-104.
Таблица 8.7 — Влияние давления на выход бензина
с октановым числом 95 (ИМ) из фракции 85…180°С гидроочищенного бензина
(V=1,5 ч–1, катализатор КР-104)
МПа |
Температура,°С |
Выход,% мас. на сырье |
Концентрация водорода |
||
катализата |
водорода |
в ВСГ,% об. |
|||
|
|
||||
|
|
|
|||
|
|
|
|
|
|
3,5 |
510 |
78 |
1,3 |
75,0 |
|
3,0 |
500 |
81,5 |
1,5 |
77,0 |
|
|
|
|
|
|
|
2,5 |
495 |
83,9 |
2,0 |
82,0 |
|
|
|
|
|
|
|
2,0 |
492 |
85,7 |
2,1 |
85,2 |
|
|
|
|
|
|
|
1,5 |
490 |
87,0 |
2,3 |
86,2 |
|
|
|
|
|
|
Однако при снижении давления процесса увеличивается скорость дезактивации (Vдез) катализатора за счет его закоксовывания (Vдез определяется как скорость подъема температуры нагрева сырья на входе в реакторы, обеспечивающая постоянство качества катализата). Как видно из рис. 8.4, скорость дезактивации катализатора приблизительно обратно пропорциональна давлению (1/р, МПа–1).
745
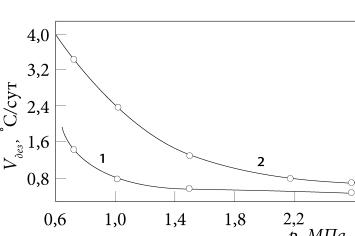
vk.com/club152685050 | vk.com/id446425943
Рис. 8.4. Зависимость скорости дезактивации Vдез катализатора КР-108 от давления при различных октановых числах риформата (ММ) (массовая скорость — 3 ч–1; отношение водород : углерод = 5:1): 1 — 87; 2 — 90
Из рис. 8.4 следует, что при давлениях 3…4 МПа коксообразование подавляется в такой степени, что установки риформинга со стационарным слоемкатализаторамогут работать без егорегенерациипрактически более 1 года. Применение би- и полиметаллических катализаторов позволяет проведение процесса при 1,5…2,0 МПа без регенерации катализатора в течение 1 года.
Кратностьциркуляцииводородсодержащегогаза.Этотпараметр определяетсякакотношениеобъемациркулирующеговодородсодержащего газа (ВСГ), приведенного к нормальным условиям (0,4; 0,1 МПа), кобъемусырья,проходящегочерезреакторывединицувремени(м3/м3).
Учитывая, что в циркулирующем ВСГ концентрация водорода изменяется в широких пределах — от 65 до 90% об., а молекулярная масса сырья зависит от фракционного и химического составов, предпочтительнее пользоваться мольным отношением водород : сырье (иногда моль водорода на моль углерода сырья). Связь между мольным отношением водород : сырье (МОТ) и кратностью циркуляции ВСГ (КВСГ) выражается следующей формулой:
МОТ = КВСГ сH Мс ρ,
где сH — концентрация (% мольн.) водорода в ВСГ; Мс и ρ — соответственно средняя мольная масса (кг/моль) и плотность (кг/м3)
сырья (КВСГ = 20 МОТ).
746

vk.com/club152685050 | vk.com/id446425943
С увеличением мольного отношения водород : сырье снижается скорость дезактивации катализаторов риформинга (рис. 8.5) и, следовательно, удлиняется межрегенерационный цикл. Однако увеличение М (т.е. КВСГ) связано со значительными энергозатратами, ростом гидравлическогосопротивления и объемааппаратов и трубопроводов. Выбор этого параметра производят с учетом стабильности катализатора, качества сырья и продуктов, жесткости процесса и заданной продолжительности межрегенерационного цикла.
Рис. 8.5. Зависимость скорости дезактивации катализатора Vдез от мольного соотношения водород : сырье H2 : С при различных октановых числах риформата (ММ)
(массовая скорость — 3 ч–1; р — 1,5 МПа): 1— 87; 2 — 90
При использовании на установках со стационарным катализатором полиметаллическихкатализаторовмольноеотношениеводород:сырье, равное 5:6, обеспечивает длительность межрегенерационного цикла до 12 месяцев. На установках с непрерывной регенерацией катализатора МОТ поддерживается на уровне 4…5 и при интенсификации блока регенерации катализатора может быть снижено до 3.
С наибольшей скоростью дезактивация катализатора происходит обычно в последнем реакторе вследствие высокого содержания в реакционной среде ароматических углеводородов и более жесткого режима риформинга. Чтобы выровнять закоксовывание катализатора по реакторам, на некоторых моделях установок риформинга (например, магнаформинге) в последний реактор подают дополнительно часть ВСГ, в результате отношение водород : сырье составляет на входе в первый реактор (3…5) : 1, а в последний — (9…12) : 1.
747
vk.com/club152685050 | vk.com/id446425943
Объемная скорость подачи сырья влияет на процесс риформин-
га как параметр, обратный времени контакта сырья с катализатором. В соответствии с закономерностями химической кинетики с увеличением объемной скорости (т.е. уменьшением времени контакта) сырья снижается глубина реакций ароматизации и более значительно реакций гидрокрекинга парафинов. При этом понизится выход продуктов гидрокрекинга — легких углеводородных газов и кокса на катализаторе. Ароматические углеводороды будут образовываться преимущественно за счет реакций дегидрирования нафтенов, протекающих значительно быстрее других. В результате повышение объемной скорости подачи сырья приводит:
—к увеличению выхода риформата, но с пониженным октановым числом и меньшим содержанием ароматических углеводородов;
—снижению выхода ВСГ с более высокой концентрацией водорода;
—повышению селективности процесса и удлинению продолжительности межрегенерационного цикла.
Сдругой стороны, при снижении объемной скорости сырья симбатноснижаетсяпроизводительностьустановокриформингапосырью. Оптимальное значение объемной скорости устанавливают с учетом качества сырья риформинга, жесткости процесса и стабильности катализатора. Обычно объемная скорость в процессах риформирования бензинов составляет 1,5…2,0 ч–1.
Содержание хлора в катализаторе. Стабильная активность ка-
тализаторов риформинга, кислотным промотором которого является хлор,возможнатолькоприегодостаточномсодержаниинакатализаторе инизкойвлажностивреакционнойсистеме.Объемноесодержаниевлаги вциркулируемомВСГподдерживаетсяобычнонауровне(10…30)·10–6. Хлорирование и дехлорирование носителя катализатора является равновесным процессом: содержание хлора в катализаторе зависит от мольного отношения водяные пары : хлороводород в газовой фазе.
Потерихлоракатализаторомприокислительнойегорегенерациивосполняются в процессе оксихлорирования подачей хлора за 2…10 ч при 500…520°Свколичестве0,5…1,5%отмассыкатализатора.Потерихлора при пусковых операциях (сушка и восстановление катализатора, начало сырьевого цикла) восполняют за несколько часов подачей 0,1…0,3% хлора от массы катализатора в поток сырья или ВСГ при температуре 350…50°С. Для поддержания оптимальной концентрации хлора в катализаторе в сырьевом цикле хлор можно подавать периодически или непрерывно с дозировкой 1…5 мг/ кг сырья (в виде хлорорганических соединений, например CCl4, C2H4C12).
748

vk.com/club152685050 | vk.com/id446425943
8.2.4. Промышленные установки каталитического риформинга
Первая промышленная установка каталитического риформинга на алюмохромомолибденовом катализаторе (гидроформинг, проводимый под давлением водорода 4…4,5 МПа и температуре = 540°С) была пущена в 1940 г. и получила широкое развитие на НПЗ США и Германии. Основным целевым назначением гидроформинга являлось получение высокооктановых компонентов (с ОЧИМ 80 пунктов) авто- и авиабензинов, а в годы II мировой войны — производство толуола — сырья для получения тринитротолуола.
В1949 г. была введена в эксплуатацию разработанная фирмой «ЮОП»перваяпромышленнаяустановка каталитического риформинга с монометаллическим алюмоплатиновым фторированным катализатором — платформинг.
В1960—1970 гг. в результате непрерывного совершенствования технологии и катализаторов (переход к хлорированным алюмоплатиновым, разработка биметаллических платинорениевых, затем полиметаллических высокоактивных, селективных и стабильных катализаторов), оптимизации параметров и ужесточения режима (понижение рабочих давлений и повышения температуры в реакторах) появились
ивнедрялисьвысокопроизводительныеиболееэффективныепроцессы платформинга различных поколений со стационарным слоем катализатора.
Важным этапом в развитии и интенсификации процессов риформинга являлись разработка фирмой «ЮОП» и внедрение в 1971 г. наиболее передовой технологии каталитического риформинга с непрерывной регенерацией катализатора (КР НРК).
Вотечественной нефтепереработке установки платформинга1 получили широкое развитие с 1962 г.
ХарактеристикаотечественныхпромышленныхустановокКР,работающих по бензиновому варианту, дана в табл. 8.8 (ЛФ-35-11/1000 — импортнаяустановкаКРНРК,эксплуатируетсянаАО«Уфанефтехим» в составе комплекса по производству ароматических углеводородов. В настоящее время на Ново-Уфимском НПЗ проведена реконструкция платформинга со стационарным слоем катализатора с переводом последнего, наиболее «коксуемого» реактора на режим непрерывной регенерации).
1 По разработкам ВНИИНефтехима и проектам Ленгипронефтехима.
749
750 |
Таблица 8.8 — |
Характеристика установок риформинга |
|
|
|
|
|
|||||
|
|
|
|
|
|
|||||||
|
|
|
|
|
|
|
|
|
|
|
|
|
|
|
|
|
|
|
|
|
|
|
|
Октановое |
|
|
|
|
|
Реакторы |
Параметры режима, проект |
Катализа- |
число |
|||||
|
|
|
|
|
|
|
|
|
|
бензина |
||
|
Тип установки |
|
Мощность, |
|
|
|
|
|
|
торы |
|
|
|
|
тыс. т/год |
|
|
Дав- |
Объем- |
Кратность |
Макси- |
по проекту |
|
|
|
|
|
|
Число |
|
|
|
||||||
|
|
|
|
Тип |
ление, |
ная ско- |
циркуляции |
мальная |
(факт.) |
ММ |
ИМ |
|
|
|
|
|
ступеней |
темпера- |
|
||||||
|
|
|
|
|
|
МПа |
рость,ч |
сырья, мм |
тура,°С |
|
|
|
|
|
|
|
|
|
|
|
|
|
|
|
|
|
Л-35 -5 |
|
300 |
3 |
Акс |
4,0 |
1,5 |
1500 |
520 |
АП-56 |
75 |
— |
|
|
АП-64 (КР) |
||||||||||
|
|
|
|
|
|
|
|
|
|
|
|
|
|
Л-35-11/300 |
|
300 |
3...4 |
Акс |
4,0 |
1,5 |
1500…1800 |
520 |
АП-64 (КР) |
78 |
— |
|
|
|
|
|
|
|
|
|
|
|
|
|
|
ЛГ-35-11/300 |
|
300 |
3 |
Акс |
4,0 |
1,5 |
1500 |
520 |
АП-64 (КР) |
78 |
— |
|
|
|
|
|
|
|
|
|
|
|
|
|
|
ЛГ-35-11/300-95 |
|
300 |
3 |
Акс |
3,5 |
1,5 |
1800 |
530 |
АП-64 |
85 |
95 |
|
|
|
|
|
|
|
|
|
|
|
|
|
|
Л-35-11/600 |
|
600 |
3 |
Акс |
3,5...4,0 |
1,5 |
1500 |
525 |
АП-64 |
80 |
— |
|
|
АП-56 (КР) |
||||||||||
|
|
|
|
|
|
|
|
|
|
|
|
|
|
ЛЧ-35-11/600 |
|
600 |
3 |
Рад |
3,5 |
1,2...1,5 |
1800 |
530 |
АП-64 (КР) |
85 |
95 |
|
|
|
|
|
|
|
|
|
|
|
|
|
|
Л-35-11/1000 (Л-бу) |
1000 |
3 |
Рад |
3,5 |
1,2...1,5 |
1800 |
530 |
АП-64 |
85 |
95 |
|
|
|
|
|
|
|
|
|
|
|
|
|
|
|
ЛЧ-35-11/1000 |
|
1000 |
3 |
Рад |
1,5 |
1,5 |
1200 |
530 |
КР |
85 |
95 |
|
|
|
|
|
|
|
|
|
|
|
|
|
|
ЛФ 35-11/1000 |
|
|
|
|
|
|
|
|
R-30, R-32 |
|
|
|
с непрерывной |
|
1000 |
4 |
Рад |
0,9 |
1,8...1,9 |
800....900 |
543 |
— |
100 |
|
|
|
АП-56 |
||||||||||
|
регенерацией |
|
|
|
|
|
|
|
|
|
|
|
|
|
|
|
|
|
|
|
|
|
|
|
|
|
Л-35-8/300Б |
|
300 |
3 |
Акс |
2,0 |
1,5 |
1200 |
525 |
АП-64 (КР) |
— |
— |
|
|
300 |
3 |
Рад |
2,0 |
1,5 |
1600 |
535 |
АП-64 |
— |
— |
|
|
|
|
||||||||||
|
|
|
|
|
|
|
|
|
|
|
|
|
|
ЛГ-35-8/300Б |
|
300 |
3 |
Рад |
2,0 |
1,5 |
1600 |
535 |
АП-64 (КР) |
|
|
|
|
|
|
|
|
|
|
|
|
|
|
|
|
Л-35-12/300 |
|
300 |
4 |
Акс |
2,0 |
1,5 |
1200 |
525 |
АП-56 |
|
|
|
|
(АП-64) |
|
|
||||||||
|
|
|
|
|
|
|
|
|
|
|
|
|
|
|
|
|
|
|
|
|
|
|
|
|
|
|
Л-35-13/300 |
|
300 |
3 |
Акс |
3 |
1,5 |
1500 |
535 |
АП-64 |
— |
— |
|
|
|
|
|
|
|
|
|
|
|
|
|
com/id446425943.vk | com/club152685050.vk
vk.com/club152685050 | vk.com/id446425943
8.2.5.Установки каталитического риформинга со стационарным слоем катализатора
Установки этого типа в настоящее время получили наибольшее распространение среди процессов каталитического риформинга бензинов. Они рассчитаны на непрерывную работу без регенерации в течение 1 года и более. Окислительная регенерация катализатора производится одновременнововсехреакторах.Общаядлительностьпростоевустановок со стационарным слоем катализатора составляет 20…40 суток в год, включая цикл регенерации и ремонт оборудования. Сырье установок подвергается предварительной глубокой гидроочистке от сернистых, азотистых и других соединений, а в случае переработки бензинов вторичных процессов — гидрированию непредельных углеводородов.
Установки каталитического риформинга всех типов включают следующиеблоки:гидроочисткисырья,очисткиводородсодержащегогаза, реакторный, сепарации газа и стабилизации катализата.
Принципиальная технологическая схема установки платформинга (без блока гидроочистки сырья) со стационарным слоем катализатора приведена на рис. 8.6. Гидроочищенное и осушенное сырье смешивают
сциркулирующим ВСГ, подогревают в теплообменнике, затем в секции печиП-1иподаютвреакторР-1.Наустановкеимеетсятри-четыреадиа- батических реактора и соответствующее число секций многокамерной печиП-1длямежступенчатогоподогревареакционнойсмеси.Навыходе изпоследнегореакторасмесьохлаждаютвтеплообменникеихолодильнике до 20…40°С и направляют в сепаратор высокого давления С-1 для отделенияциркулирующегоВСГоткатализата.ЧастьВСГпослеосушки цеолитамивадсорбереР-4подаютнаприемциркуляционногокомпрес- сора,аизбытоквыводятнаблокпредварительнойгидроочисткибензина ипередаютдругимпотребителямводорода.Нестабильныйкатализатиз С-1подают в сепаратор низкого давления С-2, где от него отделяют легкие углеводороды. Выделившиеся в сепараторе С-2 газовую и жидкую фазынаправляютвофракционирующийабсорберК-1.Абсорбентомслу- житстабильныйкатализат(бензин).Низабсорбераподогреваютгорячей струейчерезпечьП-2.Вабсорберепридавлении1,4МПаитемпературе внизу 165 и вверху 40°С отделяют сухой газ. Нестабильный катализат, выводимый с низа К-1, после подогрева в теплообменнике подают в колонну стабилизации К-2. Тепло в низ К-2 подводят циркуляцией и подогревом в печи П-1 части стабильного конденсата. Головную фракцию стабилизациипослеконденсациииохлаждениянаправляютвприемник С-3,откудачастичновозвращаютвК-2наорошение,аизбытоквыводят
сустановки.
751

vk.com/club152685050 | vk.com/id446425943
Рис. 8.6. Принципиальная технологическая схема установки каталитического риформинга со стационарным слоем катализатора:
I—гидроочищенноесырье;II—ВСГ;III—стабильныйкатализат;IV—сухойгаз;V—головнаяфракция
Рис. 8.7. Реактор риформинга: 1 — распределитель; 2 — штуцер для термопары; 3 — днище верхнее; 4 — кожух; 5 — корпус; 6 — тарелка; 7 — футеровка; 8 — желоб; 9 — катализатор; 10 — труба центральная; 11 — пояс опорный; 12 — опора; 13 — днище нижнее; 14 — шары фарфоровые; I — ввод сырья; II — вывод продукта; II — вывод катализатора
Часть стабильного катализата после охлаждения в теплообменнике подают во фракционирующий абсорбер К-1, а балансовый его избыток выводят с установки.
Основнымиреакционнымиаппаратами установок (или секций) каталитического риформинга с периодической регенерациейкатализатораявляютсяадиабатические реакторы шахтного типа со стационарным слоем катализатора. На установках раннего поколения применялись реакторы аксиального типа с нисходящим или восходящим потоком реакционной смеси. На современных высокопроизводительных установках применяются реакторы только с радиальным движением потоков преимущественно от периферии к центру 2.
Радиальные реакторы обеспечивают значительно меньшее гидравлическое сопротивление,посравнениюсаксиальным.
Нарис.8.7показанаконструкциярадиального реактора, применяемая в секциях риформинга КУ ЛК-6у. Поступающий в реактор газофазный поток сырья и водо-
2На Ново-Уфимском НПЗ внедрен более эффективный радиальный реактор с движением потоков от центра к периферии.
752
vk.com/club152685050 | vk.com/id446425943
рода пропускают по периферийным перфорированным желобам через слой катализатора к центральной трубе и затем выводят из аппарата. Катализатор располагают в виде одного слоя с равномерной плотностью засыпки. Верхнюю часть снабжают тарелкой, предотвращающей прямое попадание потока сырья в слой катализатора. В центре устанавливают перфорированную трубу, обтянутую сеткой. Нижнюю часть реактора заполняют фарфоровыми шарами.
В промышленности эксплуатируют реакторы с корпусами, изготовленными из биметалла типа 12 ХМ+0,8Х 18Н10Т, или защитным торкрет-бетонным покрытием.
8.2.6.Установки каталитического риформинга с непрерывной регенерацией катализатора
Принципиальная технологическая схема установки КР НРК приведена на рис. 8.8.
Четыре реактора риформинга (Р-1) располагают друг над другом исвязываютмеждусобойсистемамипереточныхтрубмалогодиаметра. Шариковый катализатор диаметром 1,6 мм свободно перетекает под действием силы тяжести из реактора в реактор. Из реактора четвертой ступени через систему затворов с шаровыми клапанами катализатор поступает в питатель-дозатор, откуда азотом его подают в бункер закоксованного катализатора узла регенерации. Регенератор (Р-2) представляет собой аппарат с радиальным потоком реакционных газов, разделенный на три технологические зоны: в верхней при мольном содержании кислорода менее 1% производят выжиг кокса, в средней присодержаниикислорода10...20%иподачехлорорганическогосоединения — окислительное хлорирование катализатора, а в нижней зоне катализатор прокаливают в токе сухого воздуха. Разобщение зон — гидравлическое. Катализатор проходит все зоны под действием силы тяжести. Из регенератора через систему шлюзов-затворов катализатор поступаетвпитатель-дозаторпневмотранспортаиводородсодержащим газомегоподаютвбункер-наполнитель,расположенныйнадреактором первой ступени. Процесс регенерации автоматизирован и управляется ЭВМ. Систему регенерации при необходимости можно отключить без нарушения режима риформирования сырья.
Поскольку процесс риформинга проводят при пониженном давлении (0,9…0,4МПа), на установках КР НРК применяют иную, чем в схеме на рис. 8.7, систему операции ВСГ: катализат после реакторов и сырьевого теплообменника подают в сепаратор низкого давления С-1. Выделившиеся в нем газовую и жидкую фазы соответственно компрес-
753