
Литература от Абакумова ч2 / Осмотический массоперенос
.pdf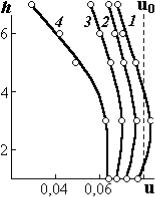
крытой грани бетонного образца. Микротензиометры имели внутренний и внешний диаметры соответственно 0,2 – 0,6 мкм и 0,1 мм, длину 4 – 5 см.
Опыты проводили при конвективно-кондуктивном подводе тепла. Бетонная смесь состояла из компонентов: портландцемент, песок, щебень, вода соответственно 400, 750, 1110, 180 кг/м3. Она укладывалась в жесткую форму (кювету) и уплотнялась на вибрационной установке. Свежесформованные образцы кубической формы помещали в камеру и подвергали термообработке. Боковые стенки образца были теплоизолированы. Снизу от нагревателя подводили тело, а сверху с открытой грани куба происходило испарение влаги в атмосферу с относительной влажностью воздуха 0,45. Режим тепловой обработки был следующим: подъем температуры от комнатной до 353 К (у нагревателя) – 3 ч; изотермическая выдержка при Т=353 К – 4 ч и охлаждение до комнатной температуры – 2 ч. Распределение влагосодержания по высоте образца в этом опыте и последующих определяли по поглощению гамма-излучения.
|
|
|
|
Поверхностные слои образца значительно осу- |
|
|
|
|
шались (рис. 5.7). Средняя и нижняя часть образца |
|
|
|
|
обезвоживалась в меньшей степени. Происходил |
|
|
|
|
неразрывный (сплошной) перенос влаги в зону |
|
|
|
|
испарения по всей высоте образца. |
|
|
|
|
Опыты с микротензиометрами проводили с бе- |
|
|
|
|
тонными смесями двух составов. В первой смеси |
|
|
|
|
(рис. 5.8а) количество портландцемента, песка, щебня |
|
|
|
|
и воды было соответственно 510, 610, 1150, 185 кг/м3; |
Рис. 5.7. Распределе- |
во второй (рис. 5.8б) – 230, 842, 1190, 138 кг/м3. |
|||
Капиллярное давление при температуре 325 К |
||||
ние |
влагосодержания |
у нагреваемой поверхности образца (h =0) быстро |
||
по высоте |
образца |
h |
возрастало и достигало ~ 0,24 МПа, а в слоях на рас- |
|
(см) |
через |
2,5 (1), |
4 |
|
(2), 6 (3), 7 (4) часов |
стоянии 2 – 4 мм от греющей поверхности до |
|||
после начала термооб- |
0,12 МПа. С увеличением расстояния h давление из- |
|||
работки |
(начальное |
менялось незначительно (рис. 5.9а). |
||
влагосодержание |
|
При более высокой температуре 358 К микро- |
||
u0 =0,08) |
|
|
тензиометры вблизи греющей поверхности отмечали |
положительное давление. Оно было вызвано парообразованием и положительным давлением пузырьков воздуха в макропорах. По мере обезвоживания и повышения температуры поверхностных слоев материала тензиометры показывали отрицательное давление.
О наличии зоны интенсивного парообразования свидетельствуют распределения капиллярных давлений на разных расстояниях от нагревателя. Зона интенсивного обезвоживания преимущественно крупных пор и парообразования по мере прогрева материала возрастала от нуля до 4 мм (рис. 5.9б). В слоях 4 – 10мм возникали отрицательные давления. В более
145
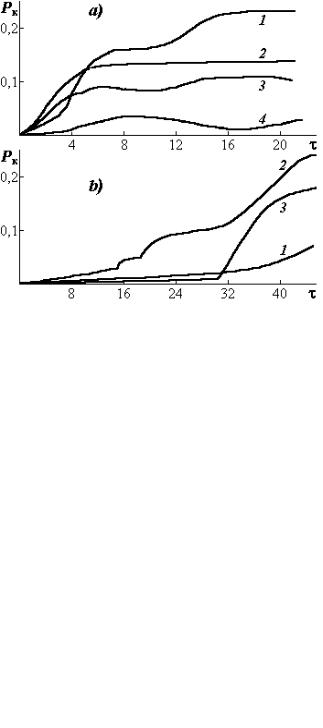
удаленных слоях давления были незначительными и мало изменялись во |
|
времени. |
|
температурах 325 (а) и 346 (б) К |
коагуляционных и затем фазовых |
|
|
контактов из-за более интенсивного перемещения частиц. |
|
|
146 |
|
В образце из второй бетон- |
|||
|
ной смеси давление у греющей |
|||
|
поверхности (рис. 5.8б, кривая 1) |
|||
|
оказалось меньше, чем в более |
|||
|
глубоких слоях. Наличие в этом |
|||
|
образце крупных пор способство- |
|||
|
вало при температуре 330 К ин- |
|||
|
тенсивному паропереносу. Поло- |
|||
|
жительное |
давление расширяю- |
||
|
щихся газовых пузырьков в мак- |
|||
|
ропорах компенсировало в тече- |
|||
|
ние продолжительного |
времени |
||
|
нагрева отрицательное капилляр- |
|||
|
ное давление в слое бетона у |
|||
Рис. 5.8. Зависимость отрицательного капил- |
греющей поверхности. |
|
||
лярного давления Р (МПа) в цементном тесте |
В более глубоких слоях в |
|||
первого (а) и второго (б) составов от времени |
связи с уменьшением температу- |
|||
τ (ч) и температуры на расстоянии от грею- |
ры по мере их обезвоживания на- |
|||
щей поверхности: а – 0,5 (1), 1,7 (2), 3,9 (3), |
блюдался |
рост |
отрицательных |
|
18,6 (4) мм, Т=325 К; б – 0,7 (1), 4,1 (2), 8,8 |
капиллярных давлений, которые |
|||
(3) мм, Т=330 К |
достигали 0,2 МПа и более. |
|||
|
||||
|
Следует отметить большую |
|||
|
продолжительность нагрева, при |
|||
|
которой наблюдался рост капил- |
|||
|
лярных давлений. Вызвано это |
|||
|
тем, что водоцементное отноше- |
|||
|
ние второй смеси 0,6 существен- |
|||
|
но больше, чем первой – 0,36. |
|||
|
Избыток влаги во второй смеси |
|||
|
требовал более продолжительно- |
|||
|
го времени для ее удаления. |
|||
|
Повышение |
температуры |
||
|
существенно влияет на процессы |
|||
|
структурообразования в цемент- |
|||
Рис. 5.9. Распределение отрицательного ка- |
ном камне. С увеличением тем- |
|||
пиллярного давления Р (МПа) в поверхност- |
пературы |
возрастает |
раствори- |
|
ном слое бетона толщиной h (мм)различного |
мость силикатов цемента. Это |
|||
времени твердения: а – 2 (1), 4 (2), 8 (3), 10 (4), |
влечет рост их концентрации в |
|||
12 (5) ч; б – 1 (1), 2 (2), 4 (3), 8 (4), 12 (5) ч при |
растворе, но снижает количество |
После термовлажностной обработки в пропарочных камерах прочность бетонных изделий ниже, чем при твердении в обычных (комнатных) условиях. Как показывают проведенные эксперименты, причиной снижения прочности является обезвоживание поверхностных слоев изделий. Это ухудшает процесс растворения цемента и соответственно уменьшает число фазовых контактов между частицами.
Защемленные пузырьки воздуха стремятся раздвинуть частицы малопрочной в начальной стадии твердения коагуляционной структуры, а отрицательные капиллярные давления, наоборот, уплотнить их. Так как их распределение вблизи нагревателя неравнозначно (см. рис. 5.8, 5.9), то возникает неравномерная усадка периферийных слоев, приводящая к нарушению сплошности материала. Образуются первичные поверхностные трещины в местах, в которых число фазовых контактов между отдельными частицами наименьшее. Последующее увеличение перепадов капиллярных давлений и температуры приводит к дальнейшему развитию трещин. По этой причине прочность бетонного изделия, прошедшего термообработку, ниже, чем при обычном твердении.
Трещинообразование при термообработке или высокой температуре и низкой относительной влажности окружающего воздуха можно уменьшить путем увлажнения поверхности изделия или увеличения относительной влажности воздуха над ним в начальном периоде твердения. Это способствует интенсивному растворению частиц цемента и росту числа фазовых контактов. В результате наблюдается увеличение прочности образующейся кристаллизационной структуры цементного камня. После набора прочности поверхностными слоями целесообразно удалить избыток влаги из бетона.
Для подтверждения явления расширения пузырьков газа (воздуха) при нагреве бетонной смеси были проведены специальные эксперименты. Бетонную смесь помещали в кювету с основанием 10 ×10 см и высотой 20 см и уплотняли на виброустановке. Две боковые стенки кюветы были изготовлены из нержавеющей стали. К ним подводили переменный ток для электронагрева бетонной смеси. На стальных стенках были установлены индикаторы перемещения для фиксации изменений объема смеси в процессе нагрева. Расширение бетона происходило по высоте образца. На внешней открытой его поверхности была установлена жесткая площадка, связанная с индикатором перемещения. Температуру бетонной смеси контролировали термопарами.
Измеряли приращение объема смеси при термообработке V относительно начального V0. Затем рассчитывали изменение относительных средних размеров пузырьков воздуха от начального R0 до конечного Rк по формуле Rк/R0 =(1 + V/V0)1/3. Дифференцируя зависимость (Rк −R0)/R0 = = R/R0, можно было определить относительную скорость расширения пузырьков газа v(τ) = R/(R0Δτ).
147
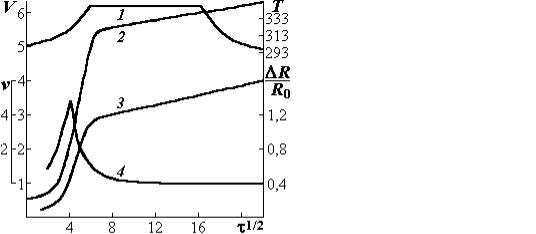
Эксперимент проводили с бетонной смесью – портландцемент марки 400, песок, щебень, вода в количестве 350 :690 :1155 :193 кг/м3. Наибольшую скорость расширения пузырьков газа наблюдали в начальный период процесса термообработки при повышении температуры от комнатной до 323 – 333 К. Относительное увеличение размеров пузырьков не превышало 1,6%.
От скорости нагрева зависит кинетика расширения пузырьков газа. При нагреве смеси в течение 20 и 60 мин (рис. 5.10, кривая 2, этим значениям времени соответствуют τ1/2 =4,5 и 7,7) от комнатной до 353 К имеет место увеличение прироста объема газа в два раза. Незначительный прирост продолжается и в период охлаждения смеси (участок кривой 2 при τ1/2 >7,7), так как давление в пузырьках воздуха превышает атмосферное.
Расширение пузырьков газа приводит к реологическому течению бетонной смеси. Чем медленнее нагрев, тем более продолжительно время перемещения частиц. Возникают необратимые деформации, в результате которых давление в пузырьках газа снижается.
Методом гаммаскопии определяли изменение плотности бетонной смеси в процессе нагрева от комнатной температуры до 353 К в течение 20 мин и последующих трех вибраций на вибростоле через каждые 20 мин.
Плотность смеси после нагрева по высоте колонки имеет большую неоднородность (рис. 5.11). Первая вибрация резко снижает неоднородность бетонной массы. Последующие две вибрации мало влияют на изменение плотности смеси.
Рис. 5.10. Изменения в бетонной смеси при электронагреве температуры Т (К) (1) и объема образца V (см3) (2), относительных значений среднего радиуса R/R (%) (3) и скорости расширения v (мин–1) пузырьков газа (4) во времени τ (мин)
Рис. 5.11. Изменение плотности бетонной смеси γ 103 (кг/м3) в процессе электронагрева в течение τ=20 мин до температуры 353 К и последующих вибраций после 40, 60 и 80 мин от начала опыта на расстояниях 3 (1), 4 (2), 9 (3), 15 (4) см от верхней грани образца; средняя плотность смеси (5)
148
В верхней части образца плотность минимальна из-за накопления пузырьков воздуха. Они «защемляются» в процессе формирования образца и практически не удаляются при вибрации. Об этом свидетельствует средняя по объему плотность (рис. 5.11, кривая 5). Она незначительно уменьшается при разогреве смеси.
Если температура была ниже 333 К, то из-за уменьшения избыточного давления в пузырьках воздуха в стадии разогрева смеси диапазон изменений плотности был меньше, чем при температуре 353 К.
При введении добавок ПАЩ-1 до 0,2% от массы бетона после термообработки и последующей вибрации наблюдается уменьшение плотности поверхностного 3-сантиметрового слоя за счет перемещения пузырьков газа из нижележащих слоев. При введении в бетон добавок ПАЩ-1 0,4
– 0,6% и температуре 333 К средняя объемная масса незначительно увеличивается, а при Т=353 К снижается.
Из приведенных результатов экспериментов следует:
1)наибольшая скорость расширения пузырьков газа происходит при температурах 323 – 333 К в начальный период нагрева бетонной смеси;
2)скорость расширения пузырьков возрастает с уменьшением их диаметров;
3)избыточное давление в пузырьках газа приводит к упругопластическим деформациям бетонной смеси на всех этапах термообработки;
4)вибрация смеси после кондуктивного нагрева образца бетона снизу вызывает передвижение пузырьков газа и их накопление в его верхней части; это служит причиной снижения прочности поверхностных слоев бетона.
5.3.Влагоперенос в бетоне при конвективном способе подвода тепла
Односторонний конвективный прогрев торцевых поверхностей образцов тяжелого бетона проводили нагретым воздухом при температуре 353 К и относительной влажности воздуха ϕ=0,6; 0,8; 1. Время предварительной выдержки образца после формования, подъема температуры до 353 К, изотермического нагрева и остывания соответственно было равно 1 +2 +3 +2 ч. Конвективный подвод тепла близок к условиям термообработки бетонных изделий нагретым паром. Подобные условия имеют место при строительстве различных сооружений из бетона в регионах с жарким, засушливым климатом.
149
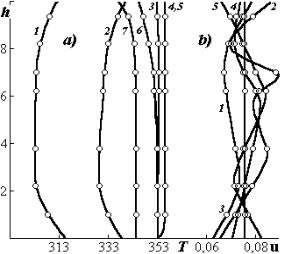
Опыты проводили с бетонной смесью, составленной из портландцемента марки 500, песка фракции 0,2 – 0,3 мм, щебня и воды соответственно в количестве 525, 605, 1080, 190 кг/м3. Для распределения влагосодержаний в свежесформованных образцах бетона применялся метод гаммаскопии. Источником излучения γ-квантов был цезий-137 с активностью 4,8 мг-экв радия.
Механизм влагопереноса в образцах бетона высотой 5, 7, 10 см и одинакового сечения 15 ×15 см аналогичен. В них устанавливается волнообразное и изменяющееся по мере нагрева и охлаждения распределение влаги. Максимальное снижение влагосодержания в конце термообработки наблюдается вблизи открытой поверхности бетонного образца. Чем меньше высота образца и относительная влажность воздуха, тем быстрее иссушаются его верхние слои.
При ϕ=1 перенос влаги из образца в окружающую парогазовую среду отсутствует. В начальный период термообработки наблюдается кон-
денсация паров воды на открытой поверхности образца. |
|
|
|
В образцах высотой 10 см на |
|
|
начальной стадии твердения бетона |
|
|
влажность нижнего слоя снижается |
|
|
за счет капиллярно-осмотического |
|
|
переноса влаги в |
поверхностные |
|
слои образца (рис. 5.12) и термо- |
|
|
влагопроводности. |
|
|
По высоте образца устанавли- |
|
|
вается непостоянное распределение |
|
|
температуры. В первый час нагрева |
|
|
градиент температуры достигает ве- |
|
|
личины 5 К/см. Во время остывания |
|
Рис. 5.12. Кривые распределения темпера- |
образца термовлагопроводность на- |
|
туры Т (К) (а) и влагосодержания u (б) по |
правлена в обратном направлении – |
|
высоте образца 10 см во времени при кон- |
от центра в периферийные слои об- |
|
вективном способе подвода тепла и отно- |
разца. |
|
сительной влажности воздуха ϕ=1; циф- |
Температура |
поверхностного |
рам на графиках соответствует время τ (ч) |
слоя бетона достигала температуры |
|
от начала опыта |
внешней парогазовой среды только в |
|
|
период изотермического нагрева материала. Температурные кривые имеют экстремумы. Они возникают в процессе массопереноса в определенных слоях образца, где более интенсивно происходят процессы испарения влаги с поглощением тепла, а также гидратации цемента с его выделением.
При ϕ≥0,8 (рис. 5.13а) в конце изотермической выдержки температура образца была выше температуры внешней парогазовой среды (кривые 4, 5) вследствие выделения тепла при гидратации. Для меньших значений
150
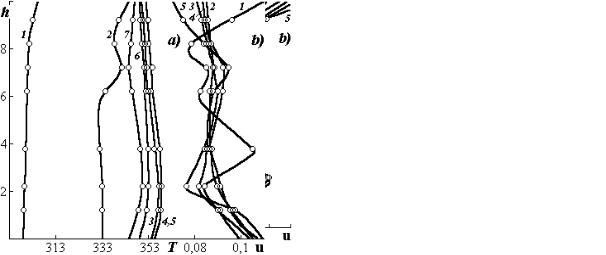
ϕ=0,6 (рис. 5.14а) из-за интенсивного испарения влаги внутри образца его температура не превышает 353 К.
В течение первых двух часов от начала эксперимента при ϕ=1 (см. рис. 5.12а) температура верхнего и нижнего слоев образца выше, чем центральных. Через три часа и до конца изотермической выдержки температура во всех слоях образца постоянная. Перераспределение влажности в это время происходит за счет градиентов влагосодержания (см. уравнение (3.7.2)), возникающих из-за неравномерного распределения влаги в начальной стадии термообработки образца (см. рис. 5.12б).
Подобное распределение влагосодержания наблюдается при ϕ=0,8 (рис. 5.13б). Увеличение влажности верхнего слоя в начале эксперимента вызвано конденсацией паров воды на открытой поверхности, так как образец к этому времени еще не прогрелся.
Затем по мере прогрева образца происходит снижение влагосодержания верхнего слоя и повышение его в нижележащих слоях за счет термовлагопроводности, направленной во внутрь образца. По мере снижения градиентов температуры термоперенос влаги уменьшается. После четырех часов от начала эксперимента происходит перенос влаги к торцам образца.
Аналогичная картина влагопереноса имеет место при относительной влажности воздуха ϕ=0,6 (рис. 5.14б). Вначале происходит понижение влагосодержания поверхностного слоя образца, а затем вследствие конденсации паров из окружающей парогазовой среды и внутреннего капил- лярно-осмотического переноса – увеличение на 0,02 – 0,04.
Рис. 5.13. Кривые распределения во вре- |
Рис. 5.14. Кривые распределения во вре- |
мени τ (ч) и по высоте образца при кон- |
мени τ (ч) и по высоте образца при конвек- |
вективном подводе тепла и ϕ=0,8: а – |
тивном подводе тепла и ϕ=0,6: а – темпе- |
температуры Т (К) при τ=1,2 (1), 2,3 (2), 3 |
ратуры Т (К) при τ=1,8 (1), 2,9 (2), 3,7 (3), |
(3), 4 (4), 5,3 (5), 6 (6), 6,8 (7) ч; б – влаго- |
5 (4), 6,3 (5), 6,9 (6) ч; б – влагосодержания |
содержания u при τ=0,8 (1), 1,5 (2), 2,3 |
u при τ=0,6 (1), 1,6 (2), 2,6 (3), 3,6 (4), 4,6 |
(3), 3,8 (4), 5,5 (5) ч |
(5) ч |
151

|
Процессы тепломассопереноса в тяже- |
|||||
|
лых и легких бетонах, керамзитобетонах, га- |
|||||
|
зобетонах, гипсе подобны. Наблюдаемые |
|||||
|
различия вызваны неадекватной пористо- |
|||||
|
стью и выделением тепла при гидратации в |
|||||
|
этих материалах. |
|
|
|
|
|
|
У образца цементно-песчаного бетона |
|||||
|
(Ц/П) с водоцементным отношением 0,45 и |
|||||
|
размером 7 ×7 ×7 см вблизи |
нагреваемого |
||||
|
торца температура |
материала |
постепенно |
|||
|
возрастала (рис. 5.15). Опыты проводили при |
|||||
|
температуре внешней |
парогазовой |
среды |
|||
|
348 К и ϕ=0,1. Возникали большие градиен- |
|||||
|
ты температур, которые вызывали при низ- |
|||||
|
ком значении ϕ=0,1 интенсивное иссушение |
|||||
|
поверхностных слоев образца, термоперенос |
|||||
|
влаги во внутренние слои и волнообразное |
|||||
|
распределение влаги по его высоте. |
|
||||
Рис. 5.15. Кривые распределе- |
Экстремумы |
на |
кривых |
влаго- |
||
содержания наблюдаются во всех опытах с |
||||||
ния во времени τ (цифры на |
||||||
кривых, ч) и по высоте образца h |
образцами бетона при конвективном подводе |
|||||
(см) цементно-песчаного бетона |
тепла. Их величина зависит от температуры |
|||||
температуры Т (К) (а) и влаго- |
и относительной влажности внешней среды |
|||||
содержания u (б) |
и вызываемой ими термовлагопроводности в |
|||||
|
направлении холодного торца, |
а также ка- |
пиллярно-осмотического переноса (отсасывания) влаги в зону испарения к открытому торцу образца.
Вначале процесса при подъеме температуры, как и у тяжелых бетонов, наблюдается незначительная конденсация пара на открытой поверх-
|
ности образца. Цементно-песчаный бетон |
|
|
имеет широкий спектр пор, что способствует |
|
|
интенсивному иссушению образца. Особенно |
|
|
обезвоживаются его периферийные слои у на- |
|
|
греваемого торца. После 27 ч нагрева они |
|
|
имеют влагосодержание меньше 0,01. |
|
|
Весь процесс массопереноса в цемент- |
|
|
но-песчаном бетоне можно разделить на три |
|
Рис. 5.16. Изменение средне- |
стадии (рис. 5.16). Каждой соответствуют раз- |
|
личные значения среднего влагосодержания |
||
го по объему логарифма вла- |
образца. На участке AB наблюдается незначи- |
|
госодержания u образца це- |
тельное уменьшение влагосодержания. В на- |
|
ментно-песчаного бетона от |
чальный период происходит прогрев материа- |
|
времени τ (ч) |
||
ла, сопровождающийся испарением влаги с |
||
|
||
|
152 |
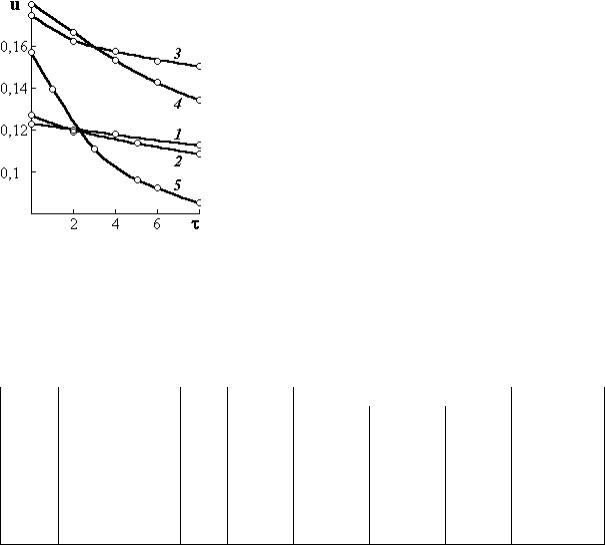
поверхностных слоев образца, и термоперенос ее в более глубокие слои материала.
На участке BC вследствие значительного обезвоживания поверхностных слоев возникает капиллярно-осмотический влагоперенос из внутренних слоев в зону испарения. Удаление влаги из крупных пор приводит к образованию связанной системы свободных поровых каналов, по которым происходит перенос влаги в паровой фазе из коагуляционно-кристал- лизационной структуры бетона. Это существенно снижает интенсивность удаления влаги из образца (участок CD). Все эти механизмы действуют одновременно, но по мере обезвоживания материала последовательно ка-
ждый из них становится превалирующим. |
|
|
|
|
|
||||
|
|
|
Серия опытов с образцами мелкозерни- |
||||||
|
|
|
стого цементно-песчаного бетона (табл. 5.1) |
||||||
|
|
|
при одностороннем конвективном нагреве с |
||||||
|
|
|
температурой |
внешней |
парогазовой |
среды |
|||
|
|
|
348 К и ϕ=0,2 подтверждает приведенный ме- |
||||||
|
|
|
ханизм тепломассопереноса. Полученные гра- |
||||||
|
|
|
фики распределения температуры и влагосо- |
||||||
|
|
|
держания по высоте образцов подобны кривым |
||||||
|
|
|
на рис. 5.15. На рис. 5.17 приведены изменения |
||||||
|
|
|
их средних влагосодержаний от времени тер- |
||||||
|
|
|
мообработки. Они имеют три участка, отмечен- |
||||||
Рис. 5.17. Изменение средне- |
ные на рис. 5.16. В зависимости от плотности и |
||||||||
водоцементного |
отношения степень |
влияния |
|||||||
го влагосодержания u |
во |
каждого из приведенных выше механизмов на |
|||||||
времени τ (ч); цифрами обо- |
массоперенос и структурообразование неодно- |
||||||||
значены |
номера образцов, |
значна. |
|
|
|
|
|
|
|
приведенных в табл. 5.1 |
|
|
|
|
|
|
|
|
|
Таблица 5.1. Состав мелкозернистых бетонов |
|
|
|
|
|
||||
|
|
|
|
|
|
|
|||
№ об- |
Модуль круп- |
В/Ц |
Ц/П |
Расход материалов *, кг/м3 |
Плотность, |
||||
разца |
ности песка |
|
|
Ц |
П |
В |
кг/м3 |
||
|
|
|
|
|
|
|
|
|
|
1 |
2,43 |
0,4 |
1 :2,2 |
628 |
1381 |
251 |
|
2260 |
|
2 |
2,43 |
0,6 |
1 :3,7 |
422 |
1560 |
253 |
|
2235 |
|
3 |
1,04 |
0,4 |
1 :1,35 |
793 |
1070 |
317 |
|
2180 |
|
4 |
1,04 |
0,6 |
1 :2,3 |
545 |
1255 |
327 |
|
2127 |
|
5** |
1,04 |
0,4 |
1 :1,55 |
720 |
1117 |
288 |
|
2125 |
|
*Ц, П, В – соответственно цемент, песок, вода; **с добавкой СДБ 0,2%.
Взатвердевших образцах мелкопористого цементно-песчаного бетона нормального (без нагрева) твердения методом фильтрации меченой
жидкости были определены радиусы r >0,1 мкм водопроводящих пор при
153
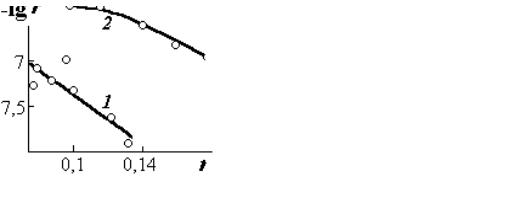
В/Ц=0,4 и 0,6. В качестве метки применяли растворы глюкозы или этилового спирта, в состав которых входил радиоактивный углерод 14.
Как отмечалось, влага в бетонной смеси расходуется на растворение клинкера и гидратацию новообразований. Остальная влага при последующем времени твердения испаряется, и в затвердевшем изделии образуются пустоты (макропоры). По этой причине в образцах с В/Ц=0,6 удаляется больше влаги, чем при В/Ц=0,4 (см. рис. 5.17, кривые 2 и 4), и размеры макропор больше (рис. 5.18, кривые 1 и 2).
В процессе термообработки вследствие интенсивной усадки при обезвоживании создается иная структура, чем в бетоне при нормальном твердении. Возникают крупные, плотные агрегаты из микрочастиц новообразований, а между ними – хаотически расположенные пустоты. Это приводит к образованию промежуточных, а также крупных макропор. С ними связана система микропор в агрегатах.
При избытке влаги возрастает подвижность микрочастиц новообразований и вероятность их перехода в компактно-коагуляционную структуру. В связи с этим возникает большая неоднородность распределения пор и увеличивается общая пористость п конечной структуры бетона.
Опыты с применением гаммаскопии позволили установить, что изменения структуры в образцах различного состава бетонов неоднозначны (рис. 5.19). В первом образце (кривая 1) при В/Ц = 0,4 вначале происходит небольшое расширение образца в связи с процессами растворения и образования коагуляционной структуры. Затем имеет место усадка, возникающая при образовании кристаллизационной структуры. При этом вода гидратных оболочек вокруг ионов частично переходит в кристаллогидраты.
Рис. 5.18. Зависимость радиусов крупных пор r (м) от пористости образцов n мелкозернистого бетона нормального твердения при В/Ц=0,4 (1)
и 0,6 (2)
Рис. 5.19. Зависимость интенсивности γ-излучения N 103 от времени τ (ч) опыта;
цифрами обозначены номера образцов по табл. 5.1
154