
ЛАБ.ПРАКТИКУМ (ИвТИ-2006)
.pdf
= 31,6 A
S x Tp ,
где А - эмпирический коэффициент.
С изменением линейной плотности ровницы от 588 до 100 текс коэффициент А изменяется от 13,8 до 10,2.
При постоянной толщине слоев текущий диаметр намотки
d = dk + 2кδ ,
где к - число слоев; δ - толщина ровницы.
Но на текущий диаметр намотки d влияют изменение натяжения в процессе наматывания, крутка ровницы и ее упругие свойства, сплющивание ровницы и др.
Сплющивание ровницы в каждом новом слое уменьшается из-за уменьшения давления лапки рогульки на ровницу и уменьшения нормального давления, создаваемого натяжением ровницы, которое с увеличением радиуса намотки уменьшается. Кроме того, внутренние слои ровницы испытывают большое суммарное давление последующих слоев.
Ровница наматывается на катушку благодаря разности между частотой вращения катушки nк и рогульки nв .
Первое условие наматывания. Число витков, наматываемых на катушку в минуту, составляет
n0 = nк − nв .
Длину одного витка определяют по формуле
l = (π d)2 + h2 .
где d - диаметр намотки, мм; h - шаг намотки, мм.
Длина ровницы, наматываемой на катушку в минуту, т. е. скорость наматывания, составляет
υ = l(nк − nв ) .
Длина ровницы, выпускаемой в минуту передним цилиндром, т. е. скорость выпуска
υ вып = π dцnц ,
где dц - диаметр переднего цилиндра, мм;
nц - частота вращения переднего цилиндра, мин-1.
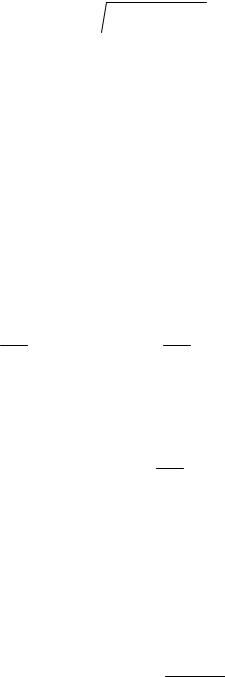
Пренебрегая вытяжкой между передним цилиндром и катушкой (е = 1,03 - 1,05), получим, что υ = υ вып , или
(nк − nв ) (π d)2 + h2 = π dцnц .
Так как h весьма малая величина по сравнению с π d , ею можно пренебречь. Тогда
(n − n )d = d n и |
n |
= n |
+ |
dцnц |
. |
|
|
||||||
к в |
ц ц |
к |
в |
d |
||
|
|
|
|
|
Это и есть первое условие наматывания, которое показывает, что с увеличением диаметра намотки при постоянных nв и nц частота вращения катушки
должна уменьшаться.
Второе условие наматывания. Скорость перемещения верхней каретки
υ к = n0h.
Учитывая, что n0 = πυd , получим υ к = πυ dh .
Величиной h пренебрегаем. Тогда
υ к = πυd .
Это и есть второе условие наматывания, показывающее, что с увеличением d скорость каретки уменьшается.
Третье условие наматывания. Это условие состоит в том, что для образования верхнего и нижнего конусов катушки необходимо уменьшать размах верхней каретки на определенную величину. Уменьшение размаха верхней каретки пропорционально изменению диаметра намотки, поэтому
H = Hn − dtg−ϕdк ,
где Н - высота слоя намотки при диаметре намотки d, мм; Hn - высота полной намотки, мм;
dк - диаметр катушки, мм.
Следовательно, третье условие наматывания показывает, что высота намотки Н зависит от диаметра намотки d, так как угол ϕ и диаметр пустой катушки dк —
величины постоянные.
Из условий намотки видно, что между скоростью каретки и частотой вращения катушки существует пропорциональная зависимость. Это позволяет осуществить передачу к катушкам и каретке от одного и того же вариатора, которым
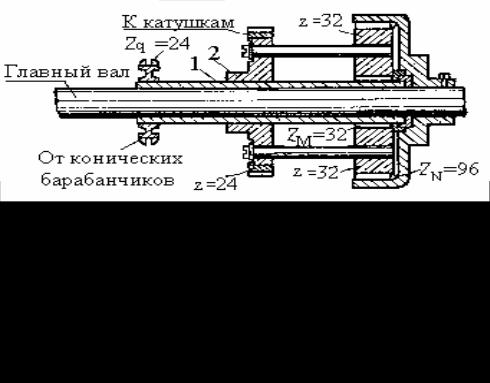
на ровничной машине являются конические барабанчики. В передачу к катушкам включен дифференциальный механизм.
Дифференциальные механизмы
Назначение дифференциального механизма состоит в сложении двух скоростей — постоянной от главного вала машины и переменной от коноидов (вариатора) и передачи суммированной скорости катушкам. При этом вариатор передает катушкам только часть мощности, которая соответствует изменению скорости, связанному с изменением диаметра намотки. Следовательно, дифференциальный механизм значительно разгружает ремень на коноидах и облегчает его работу, так как большая часть мощности, необходимой для вращения катушек, передается главным валом.
На ровничных машинах применяют дифференциальные механизмы двух типов: с водилом, передающим движение катушкам; с водилом, получающим движение от главного вала.
Каждый дифференциальный механизм состоит из основных звеньев (центральные колеса и водило) и сателлитов, оси которых перемещаются в пространстве.
Частоту вращения звеньев дифференциального механизма любого типа подсчитывают по универсальной формуле Виллиса
n − а = ±i , m − а
где п - частота вращения последней шестерни дифференциального механизма, мин-1;
а - частота вращения водила, мин-1;
m - частота вращения первой шестерни, мин-1;
i - передаточное число между первой и последней шестернями дифференциального механизма.
Рис. 116. Дифференциальный механизм с водилом, передающим движение катушкам
При вращении первой и последней шестерен в одном направлении при передаточном числе i берут знак плюс, при вращении в противоположных направлениях — знак минус.

На рис.116 представлен дифференциальный механизм с водилом, передающим движение катушкам.
Шестерня zм = 32 зуб. — первая шестерня дифференциального механизма - жестко посажена на втулку 1, получающую движение через звездочку z3 = 24 зуб. от конических барабанчиков. Шестерня zN = 96 зуб. с внутренним зацеплением — последняя шестерня в дифференциальном механизме - жестко укреплена на главном валу. Водило 2 представляет собой звездочку (z = 24 зуб.), свободно вращающуюся на втулке 1. Оно получает суммарное движение от двух симметрично расположенных шестерен zм = 32 зуб., находящихся в зацеплении с первой zм и последней ZN шестернями.
Передаточное число дифференциального механизма
i = − |
132 32 |
= − |
|
1 |
. |
|
|
32 96 |
|
||||
|
|
|
3 |
Решая уравнение Виллиса относительно а, получим
i(m −α ) = n −α ; mi −α i = n −α ;
(1− i)α = n − mi ; α |
= |
n − mi |
. |
|
|||
|
|
1− i |
Подставляя значение i = − 13 в вышеприведенное равенство, имеем
|
n + |
1 |
m |
|
3n + m |
|
3 |
1 |
|||
|
|
3 |
|
|
|||||||
α = |
|
|
|
= |
4 |
= |
4 n + |
4 m. |
|||
|
1 |
|
|||||||||
1+ |
|
|
|
|
|
|
|
||||
3 |
|
|
|
|
|
На рис.117 представлен дифференциальный механизм с водилом, получающим движение от главного вала. Первая шестерня механизма zм = 30 зуб. жестко закреплена на втулке 3, свободно сидящей на главном валу машины и получающей движение от коноидов. Водило 2 жестко закреплено на главном валу и является одновременно кожухом дифференциального механизма. Водило имеет два свободно вращающихся шпинделя. На одном шпинделе жестко закреплены две шестерни по z = 25 зуб., на другом также две шестерни: z = 25 зуб. и z = 15 зуб.
Последняя шестерня zN = 90 зуб. с внутренним зацеплением получает суммарное движение от шестерни z = 15 зуб. Шестерня ZN сидит на втулке 1, на которой имеется звездочка z = 34 зуб., передающая движение катушкам.
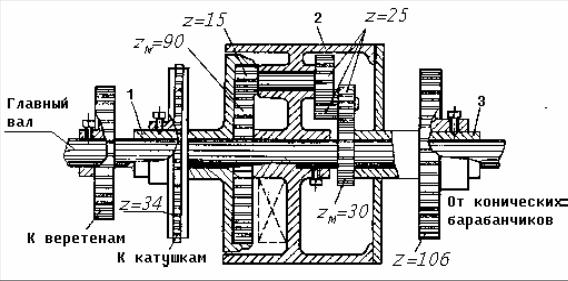
Рис. 117. Дифференциальный механизм с водилом, получающим движение от главного вала
Передаточное число дифференциального механизма
i = |
30 25 15 |
= + |
1 . |
|
25 25 90 |
|
5 |
Решая уравнение Виллиса относительно п, получим
n = α −α i + mi .
Подставив значение i, получим
n = α (1− |
1 |
) + |
1 |
m или |
n = |
4 |
α |
+ |
1 |
m . |
|
|
5 |
|
|||||||
|
5 |
5 |
|
|
|
5 |
Анализ работы рассмотренных дифференциальных механизмов показывает, что в их конструкции имеется много общего, следовательно, формулу для определения частоты вращения последней шестерни дифференциального механизма можно написать в общем виде.
Для дифференциального механизма с водилом, получающим движение от
главного вала:
n = α a + β m,
где α и β - коэффициенты, характеризующие конструкцию механиз-
ма; α = 1− i ; β = i;α + β =1;
α а - постоянная частота вращения, получаемая от главного вала
ипередаваемая катушкам;
βm - дополнительная переменная частота вращения, получаемая
от конических барабанчиков и передаваемая катушкам.

Все дифференциальные механизмы должны удовлетворять условию
α= iв , iк
где iв - передаточное число от главного вала к веретену;
iк - передаточное число от последней шестерни дифференциального
механизма к катушкам.
Разберем условие наматывания для дифференциального механизма, приведенного на рис.116:
nк = nв + π Ldк .
Запишем это условие в общем виде:
|
|
|
|
|
|
|
|
|
ni = n + |
L |
|
|
= (α a + β m)i . |
||||||||
|
|
|
|
|
|
|
|
|
π d |
|
|||||||||||
|
|
|
|
|
|
|
|
|
к |
в |
к |
|
|
|
|
|
|
|
ц |
||
|
Разделив обе части уравнения на iк, получим |
|
|
|
|
||||||||||||||||
|
|
|
|
|
|
|
|
|
α a + β m = |
nв |
+ |
L |
|
. |
|||||||
|
|
|
|
|
|
|
|
|
i |
π d i |
|
||||||||||
|
|
|
|
|
|
|
|
|
|
|
|
|
|
|
|
|
|
||||
|
|
|
|
|
L |
|
|
|
|
|
к |
|
|
к |
к |
||||||
|
Так как |
|
|
- частота |
вращения |
|
катушки, |
|
получаемая от конических |
||||||||||||
|
|
|
π dк |
|
|
|
|
||||||||||||||
барабанчиков |
и идущая на наматывание, |
то |
|
|
L |
= β m и α a = nв , откуда |
|||||||||||||||
π d i |
|||||||||||||||||||||
|
|
|
|
|
|
|
|
|
|
|
|
|
|
|
|
|
i |
||||
|
nв |
|
|
|
|
nв |
|
|
|
|
|
|
|
|
|
к к |
|
|
к |
||
α = |
, но i |
|
= |
. |
|
|
|
|
|
|
|
|
|
|
|
|
|||||
|
|
|
|
|
|
|
|
|
|
|
|
|
|
|
|||||||
|
|
в |
|
|
а |
|
|
|
|
|
|
|
|
|
|
|
|
||||
|
аiк |
|
|
|
|
|
|
|
|
|
|
|
|
|
|
|
Следовательно,
α= iва = iв . aiк iк
Для дифференциального механизма, изображенного на рис.117, формула для определения частоты вращения водила α в общем виде запишется так:
a = α n + β m,
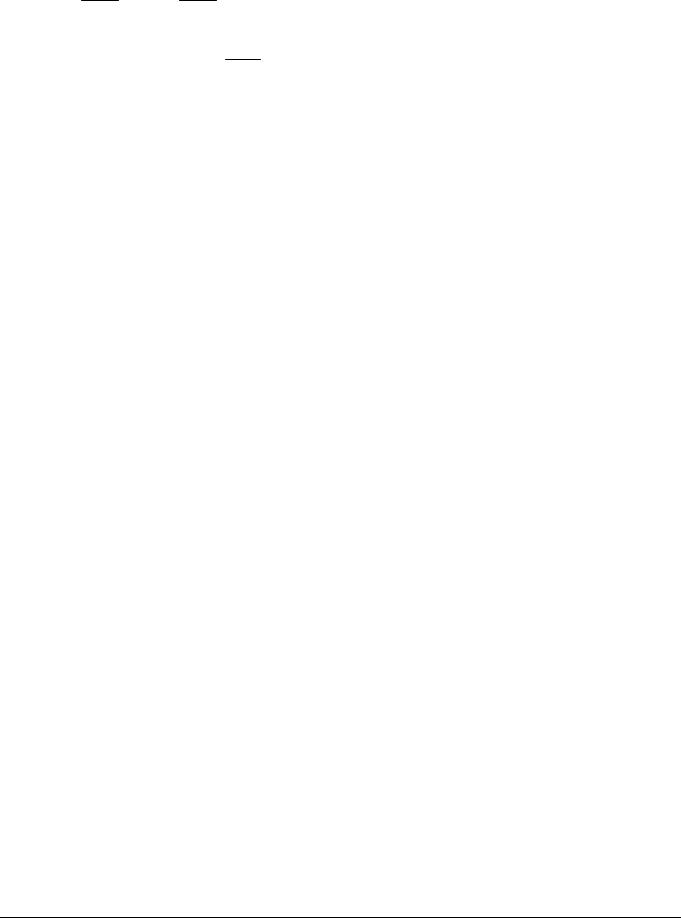
где α = 11− i , β = 1−−ii , α + β = 1.
Формула nк = nв + π Ldк будет иметь вид
|
|
|
α i |
= n |
+ |
|
L |
= (α n + β m)i . |
|
|||||||||
|
|
|
|
|
||||||||||||||
|
|
|
|
к |
в |
|
π dк |
|
|
|
|
|
к |
|
||||
Разделив обе части вышеприведенного выражения на iк, получим |
||||||||||||||||||
|
|
|
|
|
|
α n + β m = nв |
+ |
|
L |
. |
|
|
|
|||||
|
|
|
|
|
|
π d i |
|
|
|
|||||||||
|
|
|
|
|
|
|
|
|
|
i |
|
|
|
|
|
|||
|
|
|
|
|
|
|
|
|
|
к |
|
|
к |
к |
|
|
|
|
Так как |
|
L |
= β m , то α n = nв |
или α |
|
= |
nв |
, но i |
= nв . |
|||||||||
|
|
|
|
|
||||||||||||||
|
π dкiк |
|
|
|
|
iк |
|
|
|
|
|
|
в |
n |
||||
|
|
|
|
|
|
|
|
|
|
niк |
||||||||
Следовательно, α |
= |
iвn |
|
= iв . |
|
|
|
|
|
|
|
|
|
|
|
|
||
ni |
|
|
|
|
|
|
|
|
|
|
|
|
||||||
|
|
|
i |
|
|
|
|
|
|
|
|
|
|
|
|
|||
|
|
|
|
к |
к |
|
|
|
|
|
|
|
|
|
|
|
|
Методические указания
Перед изучением деталей крутильного механизма выясняют необходимость скручивания мычки, выходящей из передней пары вытяжного прибора, рассматривают факторы, влияющие на крутку, затем изучают органы, участвующие в кручении (веретено, рогульку, распространители крутки).
Подробно изучают устройство веретена, посадку его в подпятнике, закрепленном на нижней каретке, и вторую опору веретена – втулку, закрепленную на верхней каретке.
Рассматривают обе ветви рогульки, изучают назначение и конструкцию лапки, ее вертикальное и горизонтальное плечи. Обращают внимание на различные виды насадок. Выясняют требования, предъявляемые государственным стандартом к конструкции веретен, рогулек (уравновешивание веретена и рогульки, качество изготовления рогулек, совпадение осей веретена, втулки и подпятника, обеспечение минимального износа трущихся поверхностей, равномерность вращения веретен). Затем снимают необходимые размеры с веретен, устанавливаемых на машинах различных марок, и составляют таблицу по форме табл.75.
|
|
|
|
|
|
|
Таблица 75 |
Типоразмер |
Марка |
Подъем |
|
Размеры веретена, мм |
|||
веретена |
машины |
L |
D |
1 |
i1 |
d |
|
|
|
каретки |
|
|
|
|
|
|
|
|
|
|
|
|
|
Для определения влияния распространителей крутки на массу паковки одновременно на одной ровничной машине нарабатывают 10 катушек ровницы любой линейной плотности с насадкой в рогульках и 10 катушек без насадок. Взвешивают катушки, определяют среднюю массу в каждом случае и кратко объясняют полученные результаты.
Для исследования влияния крутки на прочность ровницы получают на ровничной машине по две катушки (несколько слоев) с минимальной и максимальной круткой, выбранной по табл.76, и определяют прочность ровницы.
Для определения прочности ровницы используют динамометр с зажимной длиной, примерно равной разводке в заднем поле вытягивания вытяжного прибора прядильной машины, где разрушается крутка ровницы. Проводят по 10-15 испытаний для каждого варианта, определяют среднюю прочность ровницы и объясняют полученные результаты.
Для анализа результатов кручения путем сравнения расчетного и фактического коэффициентов крутки проводят работу по следующему плану:
1)определяют линейную плотность ровницы Тр по массе пяти 10-метровых отрезков;
2)определяют счетчиком (или по кинематической схеме) частоту вращения переднего цилиндра nц, мин-1;
3)определяют тахометром (или по кинематической схеме) частоту вращения веретен nв , мин-1;
4)рассчитывают крутку ровницы Кф (кр/м) по формуле
|
|
|
Кф = |
|
|
nв |
; |
|
|
|
|
|
||
|
|
|
π dц nц |
|
|
|
|
|
||||||
|
|
|
|
|
|
|
|
|
|
|
|
|||
|
|
|
|
|
|
|
|
|
|
|
|
|
|
Таблица 76 |
Линейная плотность |
|
Коэффициенты крутки ровницы α Т |
при длине волокна, мм |
|||||||||||
ровницы, текс |
|
|
|
|
|
|
|
|
|
|
|
|
|
|
|
37/39 |
35/37 |
|
|
|
|
33/34 |
|
32/33 |
31/32 |
||||
|
|
|
|
|
|
|||||||||
|
|
|
Толстая ровница |
|
|
|
|
|
|
|||||
До 1125 |
6,13 |
6,82 |
|
|
8,42 8,50 |
|
8,50 |
|
8,60 |
|||||
6,26 |
6,96 |
|
|
8,60 8,69 |
|
8,60 |
|
8,69 |
||||||
1110—1020 1000— |
6,42 |
7,12 |
|
|
8,78 |
|
|
8,69 |
|
8,78 |
||||
878 |
|
6,54 |
7,24 |
|
|
8,88 |
|
|
8,78 |
|
8,88 |
|||
870—782 |
6,66 |
7,40 |
|
|
|
|
|
|
|
8,88 |
|
8,97 |
||
770—695 |
6,79 |
7,53 |
|
|
|
|
|
|
|
8,97 |
|
9,06 |
||
690 и менее |
|
Перегонная |
|
ровница |
|
|
|
|
|
|||||
|
|
|
|
|
|
|
|
9,95 |
||||||
До 502 |
7,24 7,33 |
7,90 |
|
|
9,76 9,86 |
|
9,86 |
|
||||||
500—479 |
7,43 |
8,00 |
|
|
9,86 |
|
|
9,95 |
|
10,05 |
||||
476—436 |
|
8,09 |
|
|
|
|
|
|
|
9,95 |
|
10,05 |
||
435—402 |
7,53 7,62 |
8,19 |
|
|
9,95 9,95 |
10,05 10,05 |
|
10,05 |
||||||
400—372 |
7,71 |
8,27 |
|
|
9,95 |
|
|
10,05 |
|
10,15 |
||||
370—346 |
|
8,37 |
|
|
|
|
|
|
|
|
|
|
10,15 |
|
|
|
|
|
|
|
|
|
|
|
|
|
|
|
|

Тонкая ровница |
8,78 |
|
9,55 |
|
10,81 |
|
10,90 |
|
11,0 |
До 167 |
|
|
|
|
|||||
166—132 |
8,92 |
|
9,67 |
|
10,90 |
|
11,0 |
|
11,10 |
131—118 |
9,04 |
|
9,80 |
|
11,0 |
|
11,10 |
|
11,19 |
117—95 |
9,20 |
|
9,92 |
|
11,10 |
|
11,19 |
|
11,28 |
94 и менее |
9,35 |
|
10,05 |
|
11,19 |
|
11,28 |
|
11,38 |
5) рассчитывают фактический коэффициент крутки аТ.ф по формуле
α Т .ф = Кф Т р ;
6) по кинематической схеме определяют константу крутки (constК) как передаточное число от переднего цилиндра к веретену, деленное на окружность цилиндра в метрах;
7)подсчитывают число зубьев крутильной шестерни zкр, установленной на
машине;
8)определяют расчетную крутку Кр по формуле
К р |
= |
сonstK |
; |
|
|||
|
|
zкр |
9)определяют расчетный коэффициент крутки α Т . р :
αТ . р = К р Т р ;
10)сравнивают фактический и расчетный коэффициенты крутки и при расхождении объясняют причину.
Чтобы подтвердить правильность расчета скоростного режима и заправки машины, проводят работу на заправленной машине по следующему плану:
1)определяют счетчиком частоту вращения переднего цилиндра и вычисляют
скорость выпуска мычки υ м (м/мин);
2)определяют линейную плотность ровницы Тр по массе пяти 10-метровых отрезков;
3)определяют производительность одного веретена за 10 мин Пв (г) по
формуле
υ10Т
Пв = м1000 р ;
4)делают карандашом отметку на трех катушках, пускают машину на 10 мин. Затем останавливают машину, снимают катушки, отматывают ровницу с каждой
катушки до отметки, взвешивают и определяют среднюю массу ровницы G (г), наработанной веретеном за 10 мин;
5) сравнивают полученные величины производительности одного веретена за 10 мин Пв и средней массы ровницы G, наработанной веретеном за 10 мин, и при расхождении в результатах объясняют причину.
В начале изучения структуры намотки рассматривают катушки с намотанным первым слоем ровницы и полную катушку, посадку катушки на втулку, выясняют назначение конусов намотки и как они образуются. Замеряют высоту первого и последнего слоев намотки ровницы, длину витка (среднее из пяти замеров) в первом и последнем слоях. Приложив линейку к катушке, подсчитывают число витков Sy ровницы на 1 см высоты намотки в первом и последнем слоях. Затем подсчитывают число витков Sx ровницы на 1 см радиуса намотки. Для этого замеряют длину окружности намотки на катушке, определяют радиус намотки, сматывают 15-20 слоев, снова определяют длину и радиус намотки. Число витков находят по формулам, полученные результаты сравнивают и делают выводы.
После изучения структуры намотки катушки проверяют расхождение в величине диаметров катушки при п слоях — фактическом и определенном по приведенной ранее формуле.
Прежде чем приступить к изучению дифференциальных механизмов, необходимо твердо усвоить, почему катушки не должны получать движение только от главного вала или только от конических барабанчиков. Затем последовательно по чертежам и на действующих моделях дифференциальных механизмов изучают конструкцию и отдельные детали механизма.
Сначала рассматривают главный вал машины и все смонтированные на нем детали. Затем для определения окончательной частоты вращения последней шестерни дифференциального механизма, полученной путем сложения постоянной части частоты вращения от главного вала и переменной от конических барабанчиков, раскладывают сложное движение на ряд простых.
1. Определяют частоту вращения последней шестерни дифференциального механизма в предположении, что она получает движение только от главного вала. Для этого сначала удаляют втулку с шестерней ZM и звездочкой, получающей движение от конических барабанчиков. В этом случае последняя шестерня zN будет иметь частоту вращения п1, равную частоте вращения главного вала α , т. е. п1 = а.
2. Определяют частоту вращения последней шестерни дифференциального механизма ZN. При остановленных втулке и конических барабанчиках, когда т = 0, частота вращения конечной шестерни ZN будет равна п1 = а—ai = (1—i)a, где i - передаточное число дифференциального механизма, имеющее знак минус, так как первая и последняя шестерни вращаются в противоположных направлениях.
3. Определяют частоту вращения последней шестерни ZN дифференциального механизма в предположении, что она получает движение только от конических барабанчиков. Для этого останавливают главный вал и вращают втулку, получающую движение от конических барабанчиков. В этом случае последняя шестерня ZN будет иметь частоту вращения
n2 = mi.
Полная частота вращения шестерни zN будет равна