
ЛАБ.ПРАКТИКУМ (ИвТИ-2006)
.pdf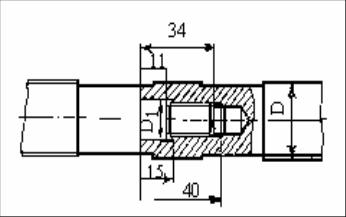
Диаметры цилиндров и нажимных валиков составляют 32, 25 и 32 мм. Разводка между передним и вторым цилиндрами составляет 50 мм; между вторым и задним - 47-55 мм. Нагрузка на нажимные валики следующая: передний - 160Н, второй - 120Н, задний - 140Н. Общая вытяжка составляет до 20.
Детали вытяжного прибора
Рифленые цилиндры являются основными деталями вытяжного прибора. Они смонтированы в виде линий, состоящих из отдельных звеньев, соединенных между собой резьбой (рис.104). Длина звена равна расстоянию между цилиндровыми стопками и колеблется от 504 до 576 мм. Число звеньев в линии зависит от числа веретен на машине и может быть от 10 до 26. К цилиндрам, согласно ГОСТ 1218875, предъявляются следующие требования:
Рис. 104. Соединение цилиндров: D = 32;35 мм; D1 = 19 мм
- достаточная прочность и твердость (не ниже HRC 55); - надежный зажим для захватывания волокон;
-высокая чистота обработки рабочей поверхности;
-наружные поверхности цилиндров должны быть хромированы;
- минимальное радиальное биение рифленых тумб не более |
0,02 мм. |
Для обеспечения прочного зажима волокон цилиндры делают рифлеными.
Длина цилиндра в собранном виде достигает 13 м, поэтому при недостаточной твердости его угол закручивания может превысить допустимую величину и вращение цилиндров будет неравномерным. Вибрация цилиндра может вызываться износом опор и увеличенным трением в них, а также недостаточной твердостью самих цилиндров.
Основными нагрузками, вызывающими изгиб цилиндров, являются усилия от принудительной нагрузки нажимных валиков, которые доходят на машинах с числом веретен 120 до 15 кН.
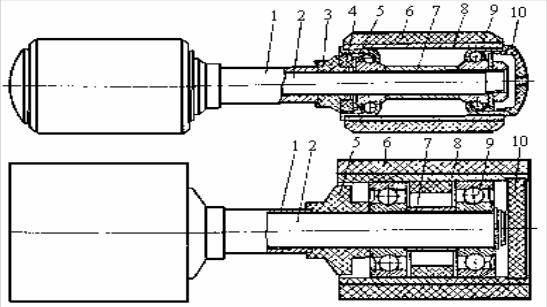
Рис. 105. Конструкции нажимных валиков:
1 - втулка валика; 2 - шпиндель валика; 3 - распорное кольцо (крышка); 4 - прокладка; 5 - шайба; 6 – покрытие; 7 - распорная втулка; 8 - втулка; 9 - шарикоподшипник; 10 - колпак (крышка)
Нажимные валики (рис.105) изготовляют из чугуна и обтягивают эластичным покрытием.
Если нажимной валик имеет эксцентриситет, он вращается неравномерно, происходит его биение, что нарушает правильное вытягивание продукта. Увеличение нагрузки на валик способствует уменьшению величины проскальзывания волокон.
В последнее время получил распространение пружинный способ нагружения валиков, который имеет ряд преимуществ:
-компактность механизма и значительное уменьшение массы машины;
-легкость обслуживания, так как разгрузка и нагрузка всех валиков производятся одновременно поворотом разгружателя, не требующим усилий.
Для нагружения валиков разгружатель 9 (рис.106) поворачивается вокруг оси 1, свободно укрепленной в отверстиях рычага нагрузки 8. Ролик 7, свободно сидящий на оси разгружателя, обкатывает при этом неподвижный кулак 6. Возникающее в результате этого усилие в оси 1 и перемещение последней относительно прутка 5 цилиндровых стоек заставляет обойму рычага 8 поворачиваться вокруг этой оси, что в свою очередь вызывает сжатие пружины, т. е. создает давление на валики при определенном фиксированном положении ролика 7. Кулак 6 свободно посажен на пруток, на котором упор 4 жестко закреплен болтом 2.
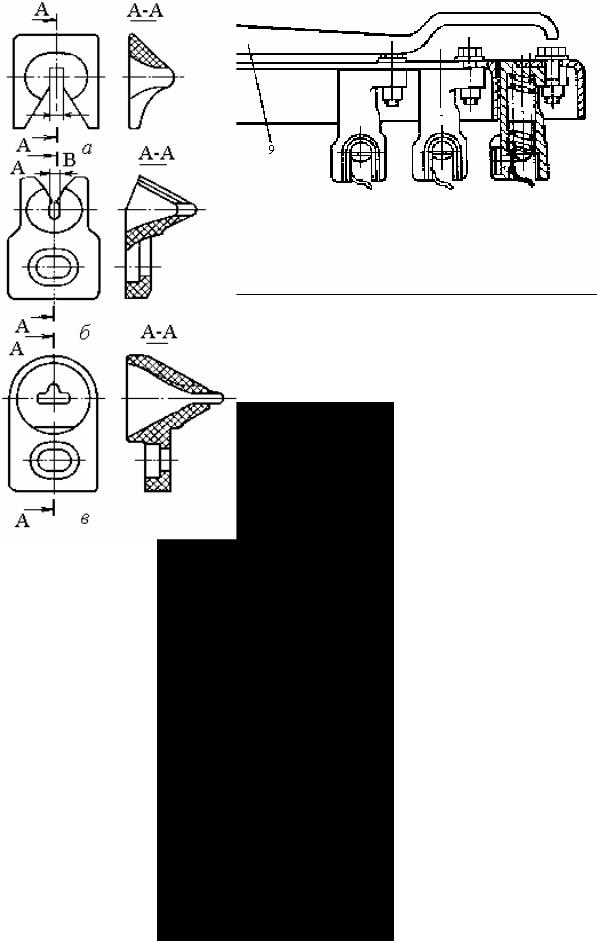
Рис. 106. Пружинное нагружающее устройство
Фиксированное положение кулака устанавливают винтом 3. Для нагружения нажимных валиков применяют цилиндрические винтовые пружины сжатия из стальной проволоки.
Рис. 107. Уплотнители
Уплотнители улучшают процесс вытягивания и ровноту ровницы. Назначение уплотнителей — сузить, уплотнить мычку, выходящую из задней зоны, не нарушая при этом параллельности волокон. При этом волокна сближаются, уменьшается количество «плавающих» волокон.
Уплотнители, изготовленные из стойких к истиранию пластмасс, устанавливаются на планке водилки и вместе с ней перемещаются вдоль цилиндра. Они могут быть различной формы.
На рис.107,а показан навесной уплотнитель, устанавливаемый перед передним цилиндром. Нижней стенке его придают вогнутый профиль, кривизна которого соответствует радиусу цилиндра. Размер В зависит от линейной плотности ровницы.
Уплотнитель, представленный на рис.107,б, устанавливают в межзональном пространстве между вторым и третьим цилиндрами и прикрепляют к планке водилки.
На рис.107,в показан уплотнитель для ленты, устанавливаемый перед вытяжным прибором. Форма и размеры входных и выходных отверстий должны быть такими, чтобы проходящий продукт достаточно уплотнялся. По исследованиям проф. А. Г. Севостьянова через конический уплотнитель лента протаскивается легче, чем через цилиндрический, но сила сопротивления при этом менее стабильна. Поэтому применяют воронкообразные уплотнители, имеющие на входе коническую и на выходе цилиндрическую форму.
Сила вытягивания представляет собой суммарную силу сопротивления волокон в процессе их движения в вытяжном поле. Сила вытягивания зависит от параметров как самого продукта, так и вытяжного прибора.
Значение силы вытягивания особенно важно знать при расчете нагрузок на нажимные валики вытяжного прибора.
Для измерения силы вытягивания в динамических условиях в МГТУ им. А.Н.Косыгина изготовлен стенд на базе прибора проф. А. Г. Севостьянова и Б. К. Кучерова. Питающая пара вытяжного прибора помещена в маятниковой системе с осью подвеса О (рис.108).
При отсутствии продукта в вытяжном приборе маятник находится в равновесии и сила, действующая на упругую балочку с тензодатчиком Т, практически равна нулю.
При прохождении продукта через вытяжной прибор возникает сила F, создаваемая вытягивающей парой. Сила F стремится повернуть маятник по часовой стрелке вокруг оси О.
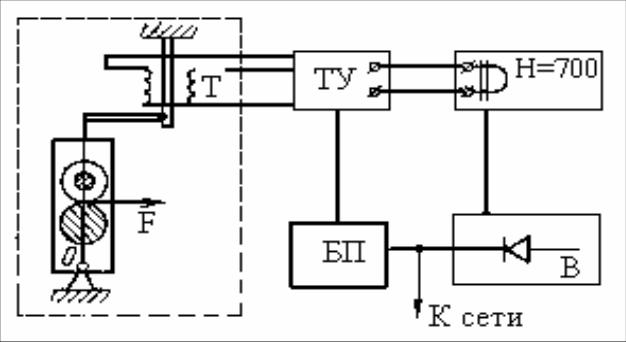
Рис. 108. Схема соединения приборов для измерения силы вытягивания
Вследствие этого упругая пластина изгибается и вызывает разбаланс мостовой схемы, в которую включены тензодатчики. Изгибающая сила пропорциональна силе вытягивания F. Следовательно, изменение силы вытягивания ∆ F преобразуется в пропорциональные изменения напряжения на выходе мостовой схемы ∆ U. Абсолютная величина этих изменений имеет порядок 10-4-10-5 В, для их усиления применяется тензометрический усилитель ТУ, к которому подключен шлейфовый осциллограф. Усилитель питается от сети через стабилизированный блок питания БП, а осциллограф Н-700 - через выпрямитель В.
Методические указания
Изучая питающие устройства, выясняют назначение направляющих валов, разделителей ленты и их конструкции. Рассматривают низкое и высокое питающие устройства, механизм автоматического останова. При изучении рамки выясняют возможность перемещения кронштейнов, установку направляющих прутков по отношению к катушке, обращают внимание на шпильки, подпятники.
Рассматривая устройство водилок, уясняют необходимость и характер их движения, конструкцию механизма движения водилок и способ регулирования их размаха.
Механизм водилки изучают на стенде и непосредственно на машине. Для этого откидывают футляр, закрывающий механизм, рассматривают соединение водилки с тягой и крепление тяги к рычагу, сцепление червяка с шестернями и соединение звеньев планки водилки. Устанавливают связь водилки с уплотнителями ленты и мычки. Изучают возможность изменения размаха водилки. Устанавливают пределы отклонения глазков водилки от середины нажимного валика в обе стороны.
Для замера полного перемещения ровницы водилкой предварительно наносят мелом полосу по образующей валика. Пускают в работу машину с заправленной

ровницей. После того как водилка совершит полный цикл, включающий нарастание и убывание ее размаха, машину останавливают и по величине стертого ровницей участка меловой полоски определяют полное перемещение ровницы вдоль валика.
Перед изучением вытяжных приборов выясняют их назначение, значение высоких вытяжек, определяют технологический и экономический эффект, получаемый в результате сокращения числа переходов на ровничных машинах. Затем изучают вытяжные приборы всех типов. При этом необходимо разобрать и собрать по одной секции вытяжных приборов нескольких типов и начертить их технологические схемы, а также схемы передачи движения в вытяжном приборе, начиная с переднего цилиндра. Далее рассматривают цилиндровые стойки, способ их крепления к брусу, подшипники, вкладыши, возможность и необходимость перемещения подшипников в цилиндровых стойках.
Изучают конструкцию цилиндров, рифли и их переменный шаг, диаметры цилиндров на машинах в зависимости от длины перерабатываемого волокна, обращают внимание на меньший диаметр второго цилиндра, способ соединения цилиндров, конструкцию уплотнителей и их движение, синхронное с водилкой, на чистители цилиндров и валиков.
Затем определяют размеры звеньев цилиндров и длину рифленой тумбочки в зависимости от типа машины и составляют таблицу по форме табл.73.
|
|
|
|
|
Таблица 73 |
|
Расстояние |
Длина |
Число |
Длина |
Число рядов |
|
между вере- |
звена, мм |
рифленых |
рифленой |
тазов сзади |
Машина |
тенами |
|
тумбочек в |
тумбочки, мм |
машины |
|
(РМВ), мм |
|
звене |
|
|
|
|
|
|
|
|
|
|
|
|
|
|
Изучают конструкцию нажимных валиков, требования, предъявляемые к валикам.
Затем рассчитывают шаблоны. Разводку между цилиндрами устанавливают в зависимости от длины перерабатываемого волокна.
При данной длине волокна Lшт и определенном типе вытяжного прибора необходимые шаблоны для установки разводки рассчитывают по формуле
Ш = R − d1 + d2 ,
2
где Ш - размер шаблона, мм;
R - разводка (расстояние между центрами цилиндров), мм; d1,d2 - диаметры цилиндров, мм.
Все полученные данные сводят в таблицу по приведенной ниже форме
(табл.74).
Работу по исследованию силы вытягивания выполняют следующим образом: 1. За 20 мин до начала испытания включают источник питания БП усилителя
ТУ (см. рис.108).
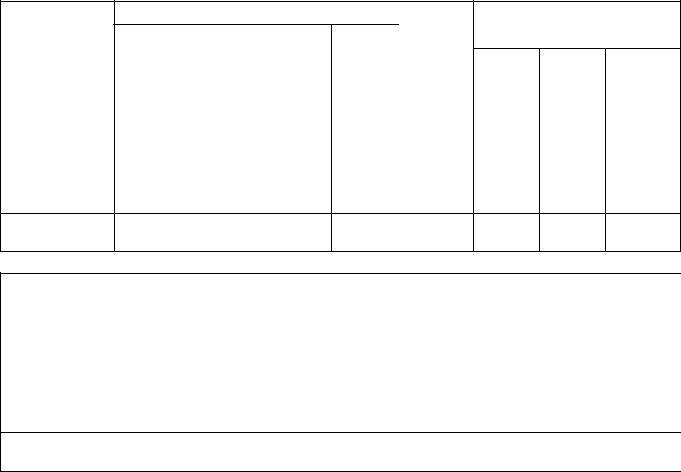
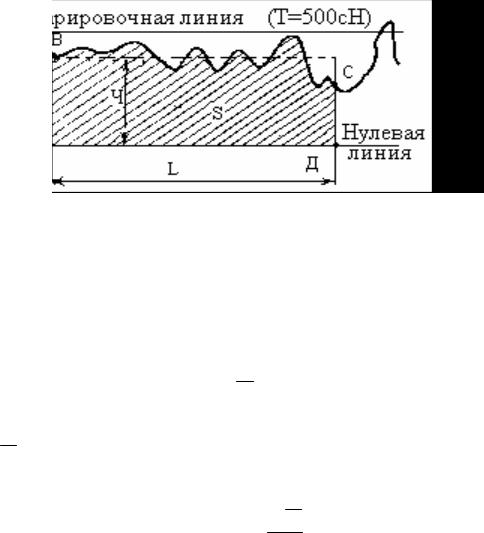
Рис. 109. Диаграмма силы вытягивания
8. После записи бумагу снимают и передают в фотолабораторию.
Среднее значение силы вытягивания проще всего получить, определив с помощью планиметра площадь S на диаграмме (рис.109), ограниченную кривой силы вытягивания и нулевой линией при данной длине диаграммы L.
Среднюю ординату (мм) кривой силы вытягивания определяют из отношения
Ч = SL .
Зная Ч , можно получить значение средней силы вытягивания F (сН) по формуле
F= TЧ ,
ЧT
где Т - масса тарировочных грузиков, г;
Ч T - расстояние между нулевой и тарировочной линиями, мм.
Определение неровноты силы вытягивания проводится методом сумм или произведений. При этом находятся среднее арифметическое значение силы вытягивания, коэффициент вариации и гарантийные ошибки коэффициента вариации и среднего арифметического значения.
Для исследования результатов вытягивания сопоставляют расчетную и фактическую вытяжки.
Работу проводят на заправленной ровничной машине по следующему плану:
1.Определяют линейную плотность ленты Тл, поступающей в ровничную машину, по массе пяти 5-метровых отрезков.
2.Определяют линейную плотность ровницы Тр, вырабатываемой на машине, по массе пяти 10-метровых отрезков.
3.Определяют вытяжку по соотношению линейных плотностей ленты и
ровницы
Е= Тл .
Тр
4. По кинематической схеме находят постоянное число вытяжки const Е и рассчитывают число зубьев вытяжной шестерни по формуле
= constЕ
zв. расч. E .
5. Сравнивают расчетное число зубьев вытяжной шестерни zв.расч. с числом зубьев вытяжной шестерни zв факт., установленной на машине. В случае расхождения между значениями числа зубьев объясняют причину.
Питающие устройства
Лента из тазов выбирается медленно вращающимися питающими валами. Разделители ленты укреплены на отдельных трубах, проходящих ниже питающего вала. Для удобства обслуживания ровничных машин при использовании тазов большого диаметра, устанавливаемых в четыре ряда, два питающих вала монтируют на высоте 1770 мм непосредственно над тазами с лентой, третий крепят на станине. В этом случае за машиной между двумя рядами тазов остается проход, необходимый для обслуживания машины. Кроме того, такое расположение питающих валов уменьшает скрытую вытяжку. На машинах с питающим устройством, расположенным высоко, имеется механизм автоматического останова при сходе или обрывe ленты, состоящий из реле и сигнальных ламп, смонтированных на кронштейнах питающих валов. Если лента оборвалась или закончилась, вал самоостанова питающего прибора соединяет катушку одного из реле с землей.
Цепь питания катушки пускателя разрывается, и ровничная машина останавливается.
На ровничных машинах второго перехода, на которые подаются катушки с предыдущих машин, устанавливают рамки для катушек.
Катушки размещают вертикально на деревянные шпильки, сматываемая с них ровница огибает пруток и направляется в глазок водилки.
Водилки
Перед поступлением в вытяжной прибор лента проходит через водилку, которая, двигаясь возвратно-поступательно, перемещает ровницу вдоль цилиндров и обеспечивает равномерный износ эластичных покрытий валиков.
По характеру движения различают водилки с постоянным и переменным размахом планки. На ровничных машинах применяют водилки обоих типов.
На рис.110 показан червячно-эксцентриковый механизм водилки. Две червячные шестерни 1 и 2 получают вращательное движение от общего червяка 9, который насажен на задний цилиндр 8. Шестерня 2 установлена свободно на ступице шестерни 1, вращающейся на неподвижном валике 3 вокруг оси. На эксцентрике шестерни 1 свободно сидит шайба 4.
Шестерня 1 имеет 45 зуб., шестерня 2 - 44 зуб., поэтому шестерня 2 опережает при движении шестерню 1 и приводит в движение шайбу 4, свободно вращающуюся по эксцентрику шестерни 1 с помощью винтов 4, входящих в прорезь шестерни 2.
В прорези шайбы 4 эксцентрично укреплен шпиндель 6, на который насажана тяга 14, соединенная кронштейнами 11 и 10 с планкой 15 водилки.
Расстояние от оси шпинделя 6 до оси шайбы 4 можно менять для получения требуемого максимального размаха водилки, который во время работы изменяется за счет смещения центра вращения шпинделя 6 в результате перемещения эксцентрика шестерни 1 с шайбой 4.
На рис.111,а показан планетарно-шатунный механизм водилки. Двухзаходный червяк 1, находящийся на конце третьего цилиндра, приводит в движение червячную шестерню 2, втулка которой вращается в корпусе 3 с неподвижным зубчатым венцом 4, имеющим с внешней стороны 16 зуб. У втулки есть эксцентрично расположенное отверстие, в которое входит валик 5 шестерни 6 с внутренним зацеплением, имеющей
18 зуб.
На шестерне 6 закреплена пластина 7 с пальцем 8, на котором может поворачиваться один конец тяги 9, соединенный с планкой водилки.
За один оборот втулки шестерни 2 ось валика 5 совершает один оборот по окружности, и шестерня 6 перебирает своими зубьями 18 зубьев неподвижного венца 4, сместившись относительно него вперед на 2 зуба и повернувшись на своей оси на 3/16 или 1/8 оборота относительно венца 4. Движение валика 5, а вместе с ним шестерни 6, приводит к перемещению шпинделя 8 по окружности, который через тягу 9 перемещает водилку.