
Технологии органического и нефтехимического синтеза
..pdf
3.3.4. Получение ароматических углеводородов путем диспропорционирования алкилароматических углеводородов
Диспропорционирование, или переалкилирование, толуола и триметилбензола позволяет получать бензол и ксилолы. В частности, при диспропорционировании толуола образуется смесь бензола и ксилолов:
(3.13)
Процесс идет при температуре 350–520 °С и давлении 1–1,2 МПа. Для подавления коксообразования процесс ведут в присутствии водорода. Конверсия толуола составляет около 60 %. Выход бензола по отношению к ксилолам (мольное соотношение) 0,7 : 1.
В случае применения в качестве исходного сырья триметилбензолов в продуктах реакции преобладают ксилолы.
3.4. ПОЛУЧЕНИЕ АРОМАТИЧЕСКИХ УГЛЕВОДОРОДОВ АЛКИЛИРОВАНИЕМ БЕНЗОЛА ОЛЕФИНАМИ. ПОЛУЧЕНИЕ АЛКИЛБЕНЗОЛОВ
Со времени открытия реакции алкилирования было разработано много различных методов замещения водородных атомов в молекулах бензола и других ароматических углеводородов на алкильные радикалы. Для этого используют различные агенты алкилирования
икатализаторы.
Впроцессах алкилирования ароматических углеводородов олефинами применяют катализаторы, имеющие характер сильных кислот (Н2SO4 (85–95%-я), фосфорная и пирофосфорная (Н4Р2О7) кислоты, безводный НF, синтетические и природные алюмосиликаты, иониты, гетерополикислоты).
81

Большую группу катализаторов для данного процесса составляют апротонные катализаторы (кислоты Льюиса) – галогениды металлов, которые проявляют активность в присутствии промоторов, с которыми катализатор образует продукты, имеющие характер сильных протонных кислот. Это AlCl3, AlBr3, FeCl3 и др.
Промышленное применение из них получил только AlCl3. Реакция алкилирования бензола и его гомологов описывается следующим уравнением:
(3.14)
Алкилирование бензола и его гомологов протекает по карбонийионному механизму.
Полученные алкилзамещенные бензола могут иметь различное строение алкильной группы, поскольку присоединение протона к олефину идет по правилу Морковникова, в связи с чем строение алкильной группы зависит от строения олефина.
Расчет равновесных выходов моно- и диалкилбензолов показывает, что они возрастают при увеличении мольного избытка бензола и с повышением давления при данной температуре.
При использовании в качестве катализатора AlCl3 наряду с реакцией алкилирования протекает реакция переалкилирования:
С6Н4R2 + С6Н6 → 2С6Н5R, |
(3.15) |
и устанавливается равновесный состав реакционной массы с содержанием моноалкилбензола до 50 %. При этом мольное соотношение бензол : олефин в случае использования в качестве катализатора AlCl3 должно лежать в пределах от 3 : 1 до 2 : 1, для остальных катализаторов – в пределах от 4 : 1 до 10 : 1.
Сырье для алкилирования должно быть очищено от сернистых соединений (Н2S, меркаптанов). С целью исключения разложения катализатора водой необходима осушка бензола и олефина.
82
Вкачестве сырья для процесса алкилирования применяют либо этан-этиленовую, либо пропан-пропиленовую фракции, содержащие 60–70 и 40–80 % соответственно этилена и пропилена или концентрированные этилен и пропилен.
Рассмотрим более подробно процессы алкилирования бензола этиленом и пропиленом.
3.4.1.Алкилирование бензола пропиленом
Впроцессе алкилирования бензола пропиленом получают изопропилбензол, или кумол. Для его получения широкое распространение получил процесс алкилирования на твердом фосфорнокислом катализаторе, содержащем пирофосфорную кислоту (75 %), на кизельгуре (25 %), Аl2О3 или силикагеле.
Вданном процессе смесь бензола и пропилена при мольном соотношении (4–6) : 1 пропускается через слой катализатора при температуре 200 °С и давлении 2,8–4,2 МПа. Катализатор работает 700–800 ч, а затем теряет активность и заменяется свежим. Недостатком фосфорнокислого катализатора является невозможность протекания реакций переалкилирования с образующимися полиалкилбензолами. Кроме того, получаемый изопропилбензол содержит 0,5–1 % олефинов, которые ингибируют его окисление в фенол и ацетон, и требуется проведение специальной гидроочистки.
Внастоящее время свыше 90 % мирового производства изопропилбензола осуществляется алкилированием на фосфорнокислом катализаторе.
На отечественных заводах наибольшее применение получил
процесс алкилирования бензола пропиленом на АlСl3. Преимущество этого катализатора заключается в отсутствии олефинов в изопропилбензоле и возможности переалкилирования полиалкилбензолов, что повышает выход изопропилбензола.
Сырьем для производства изопропилбензола служит пропанпропиленовая фракция (40–80 % пропилена) и бензол после азео-
тропной осушки. АlСl3 вводится в количестве 8–10 % от алкилата. Потери не превышают 1,5–2 %.
83
Процесс алкилирования проводят в реакторе, представляющем собой пустотелый аппарат колонного типа, футерованный изнутри графитом для предотвращения коррозии. Перемешивание реакционной массы осуществляется самим газом, подаваемым в реактор. Отвод тепла идет за счет испарения части бензола, который затем конденсируется и вновь возвращается в процесс.
Условия процесса: температура 90–130 °С и давление 0,5 МПа, что связано с протеканием реакции переалкилирования полиалкилбензолов, так как сама реакция алкилирования идет с достаточной скоростью при температуре 35–40 °С.
Рассмотрим принципиальную технологическую схему процесса получения изопропилбензола на АlСl3 (рис. 3.6).
Согласно схеме бензол нагревается до 65 °С в теплообменнике 1, обогреваемом осушенным бензолом, и направляется в колонну азеотропной осушки 2, из верхней части которой отбирается азеотроп при температуре 75–78 °С, а из нижней части – сухой бензол (температура 83–84 °С). Пары проходят конденсатор 3, водоотделитель 5, где бензол отделяется от воды. Верхний бензольный слой направляется в колонну 2, а вода сливается в канализацию. Сухой бензол (содержание воды 0,001–0,003 мас. %), охлажденный до 30 °С, направляется в алкилатор 7, куда поступает АlСl3 в виде комплекса с ПАБами из емкости 6 и про- пан-пропиленовая фракция, а также ПАБы на переалкилирование.
Отходящие из алкилатора 7 газы, содержащие пары бензола, проходят конденсатор 8, где большая часть бензола конденсируется. Газы поступают в скруббер 10 на промывку ПАБами, поглощающими остатки паров бензола. Затем газ, содержащий в основном С3Н8, нейтрализуют в колонне 11, промывают водой и направляют на пиролиз.
Алкилат из верхней части алкилатора 7 идет в отстойник 9, где отделяется от катализатора, который возвращается в алкилатор. Далее алкилат охлаждается в холодильнике 12 и идет в емкость 13 для разложения водой растворенного катализатора. Смесь воды и алкилата разделяется в отстойнике 14, далее алкилат нейтрализуется щелочью в аппарате 15, промывается водой в емкости 16 и идет на ректификацию, которая осуществляется в пяти колоннах: в первой отгоняется бензол, который вновь возвращается на алкилирование; во второй отго-
84
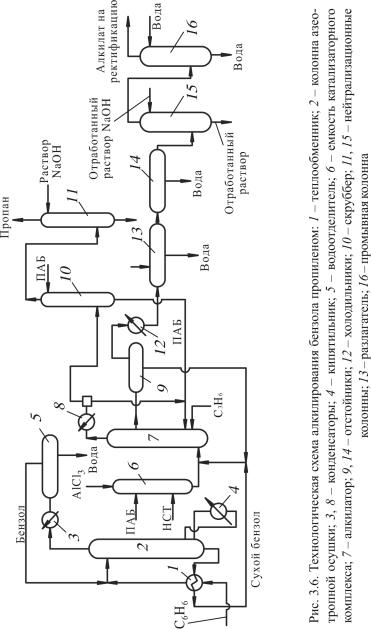
85
няется изопропилбензол с примесью бутил- и этилбензола; в третьей от остатка отгоняются ПАБы, возвращаемые в процесс; в четвертой от ректификата второй колонны отгоняется этилбензол; в пятой от изопропилбензола отгоняются бутилбензолы.
Типичный состав алкилата (мас. %): бензол – 55–60; моноалкилбензол – 30–35; диалкилбензолы – 5–10; полиалкилбензолы и смолы – до 5. Выход изопропилбензола 87 % на пропилен.
Сравнивая процессы на фосфорнокислом катализаторе и на АlСl3, следует отметить, что в первом случае аппаратурное оформление проще, менее коррозионная среда, меньше сточных вод. Поэтому процесс на фосфорнокислом катализаторе более экономичен.
3.4.2. Алкилирование бензола этиленом
Для получения этилбензола в промышленности получил применение только АlСl3. Процесс осуществляется по той же схеме, что и для получения изопропилбензола, только в качестве алкилирующего агента применяется этилен, в связи с чем несколько отличаются параметры процесса, а именно: температура 80–100 °С; мольное соотношение этилен : бензол равно 1 : 2.
Фирмой «Монсанто» был разработан процесс гомогенного высокотемпературного алкилирования бензола этиленом (температура 150 °С и выше). Особенности процесса – подача малого количества катализатора и отсутствие рециркуляции катализаторного комплекса. Рассмотрим технологическую схему данного процесса (рис. 3.7).
Наряду с реактором алкилирования в схеме имеется реактор переалкилирования 2. Катализатор в данной схеме используется однократно и выводится из системы.
Согласно схеме в реактор 1 подаются реагенты и катализатор. Тепло реакции используется для генерации водяного пара в парогенераторе 7. Из реактора 1 алкилат поступает в реактор переалкилирования 2, куда подаются и рециркулирующие полиалкилбензолы. Смесь находится в реакторе 2 необходимое для достижения равновесия время.
86
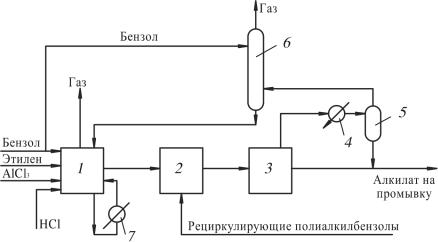
Рис. 3.7. Технологическая схема высокотемпературного гомогенного
алкилирования бензола этиленом: |
1 – реактор |
алкилирования; |
|
2 – |
реактор переалкилирования; 3 – |
испаритель; |
4 – конденсатор; |
5 |
– сепаратор; 6 – абсорбер; 7 – котел-утилизатор(парогенератор) |
Выходящий из реактора 2 продукт освобождается от газообразных компонентов в испарителе 3 за счет снижения давления
идалее направляется на промывку. Пары через конденсатор 4
исепаратор 5 поступают в абсорбер 6, где промываются бензолом. Жидкая фаза из абсорбера 6 возвращается в реактор 1, а газ отдувается.
Преимущества процесса:
–уменьшенное смолообразование и сниженные потери с катализаторным комплексом;
–уменьшение коррозии;
–уменьшенный расход АlСl3 и НСl (1,9 и 0,6 кг на 1 кг бензола соответственно).
87
3.5. ПРОИЗВОДСТВО ДРУГИХ АЛКИЛБЕНЗОЛОВ
Промышленный интерес представляют собой алкилбензолы, получаемые алкилированием бензола высшими α-олефинами. Получаемые алкилбензолы используются в основном для производства ПАВ. В качестве катализатора применяется АlСl3.
Технологическое оформление процесса практически не отличается от технологического оформления при получении изопропилбензола. Процесс проводят при мольном отношении бензол : олефин равном 7,5 : 1, температуре 45–59 °С, атмосферном давлении, времени контакта 45–59 мин. Выход целевой фракции составляет 87–90 %.
Глава 4
ПРОИЗВОДСТВО УГЛЕВОДОРОДНОГО СЫРЬЯ ДЛЯ ПОЛУЧЕНИЯ СИНТЕТИЧЕСКИХ КАУЧУКОВ
4.1. ПОЛУЧЕНИЕ БУТАДИЕНА-1,3
Бутадиен-1,3 – это основной мономер при получении каучуков общего и специального назначения. На его основе получают полибутадиеновые, бутадиен-стирольные каучуки, он входит в состав бута- диен-нитрильных каучуков.
В Западной Европе и Японии бутадиен-1,3 получают в основном из фракции С4 газов пиролиза, в США – на 80 % из газов пиролиза, а остальное – дегидрированием н-бутана и н-бутенов. В России бутади- ен-1,3 получают как дегидрированием, так и из газов пиролиза.
4.1.1. Получение бутадиена-1,3 дегидрированием н-бутана и н-бутенов
Дегидрирование н-бутана и н-бутенов – это последовательная обратимая реакция:
–H2 CH2=CHCH2CH3 |
|
цис |
–H2 |
CH3CH2CH2CH3 |
|
|
CH2=CH–CH=CH2 (4.1) |
+H2 CH3CH=CHCH3 |
транс +H2 |
Условия равновесия реакции дегидрирования неблагоприятны, так как для получения приемлемой глубины превращения требуются высокие температуры, которые, в свою очередь, приводят к протеканию побочных реакций. Поэтому процесс ведут при пониженных температурах, но в присутствии катализатора.
Поскольку реакция дегидрирования протекает с поглощением тепла и увеличением объема, то для нее благоприятны высокая температура и низкое давление.
89
В промышленных условиях процесс дегидрирования ведут в ограниченном оптимальном интервале температур, чтобы предотвратить протекание побочных реакций распада и уплотнения, снижающих выход бутенов и бутадиена и приводящих к образованию углеводородов С1–С3 и закоксовыванию катализатора.
Дегидрирование н-бутана может осуществляться в одну или в две стадии с возвратом в реактор непрореагировавшего сырья. Основными факторами, определяющими конструктивное оформление процесса дегидрирования н-бутана и н-бутенов, являются:
–необходимость подвода в зону реакции большого количества тепла;
–обеспечение высокой температуры и малого времени контакта;
–необходимость выжига кокса с поверхности катализатора;
–необходимость быстрого охлаждения продуктов реакции.
4.1.1.1. Двухстадийное дегидрирование н-бутана
При двухстадийном процессе н-бутан и полученные на первой стадии н-бутены дегидрируются раздельно на двух самостоятельных установках. В этом случае на каждой стадии удается создать оптимальные условия с обеспечением максимального выхода бутенов и бутадиена и максимальной селективности.
Поскольку на каждой стадии достигается за проход лишь частичное превращение сырья, а за счет протекания побочных реакций образуются побочные газообразные продукты, контактный газ после каждой стадии направляется на разделение. Поэтому помимо установок дегидрирования на заводе имеются и установки разделения продуктов.
Весь процесс дегидрирования включает следующие стадии:
–дегидрирование н-бутана до бутенов – первая стадия;
–разделение контактного газа дегидрирования первой стадии абсорбцией и ректификацией с выделением бутан-бутеновой фракции;
–разделение бутан-бутеновой фракции экстрактивной дистилляцией с возвратом н-бутана на первую стадию дегидрирования;
–дегидрирование н-бутенов до бутадиена-1,3 – вторая стадия;
90