
Суперфинишные станки для автомобильной промышленности
..pdf
Аналогично находим проекцию |
2 смещения |
|
′ |
на направ- |
||||||||
|
2 |
|||||||||||
ление угла α2 из треугольника ОA2В2: |
|
|
|
|
|
|
|
|||||
2 |
= R − |
r 2 |
+ (R |
+ r )2 |
− 2r (R |
+ r )cos(β |
2 |
− α |
2 |
) . (6.11) |
||
2 |
2 |
2 |
0 |
2 |
2 |
2 |
|
|
|
После базирования центр заготовки сместится в точку О1 и расстояние от него до центра левого валка будет равно А1О1 =
= R1 + r0 + 1, а до центра правого валка А2О1 = R2 + r0 + 2. Центр заготовки последовательно движется по левому валку по
дуге окружности радиуса А1О1 и по правому валку по дуге окружности радиуса А2О1. Пересечение этих траекторий и будет новым положением центра заготовки О1. Определим координаты точки О1 из совместного решения уравнений данных окружностей в проекциях на оси X и Y:
−(R1 + r0 )cosα1 + (R1 + r0 + |
1)cosϕ1 = |
|
|
||||||||||||||||
= (R |
+ r )cosα |
2 |
− (R |
+ r + |
2 |
)cosϕ |
; |
|
|
||||||||||
2 |
|
0 |
|
|
|
|
2 |
|
|
0 |
|
|
|
2 |
|
|
(6.12) |
||
−(R + r )sin α + (R |
|
+ r |
+ |
1 |
)sin ϕ = |
|
|
||||||||||||
1 |
|
0 |
1 |
|
|
1 |
|
|
0 |
|
|
1 |
|
|
|
|
|||
= −(R |
|
+ r )sin α |
2 |
+ |
(R |
|
+ r |
+ |
|
2 |
)sin |
ϕ |
2 |
, |
|
||||
2 |
|
0 |
|
|
|
2 |
|
0 |
|
|
|
|
|
||||||
где ϕ1 и ϕ2 – углы |
наклона |
отрезков |
А1О1 |
и |
|
А2О1 |
к оси X |
||||||||||||
(см. рис. 6.5). |
|
|
|
|
|
|
|
|
|
|
|
|
|
|
|
|
|
|
|
В уравнениях (6.12) первые слагаемые в левой и правой частях представляют собой проекции центров окружностей валков, а вторые слагаемые– проекции радиусовтраекторийцентразаготовки.
Решение системы уравнений (6.12) дает выражения для расчета погрешности базирования:
|
= |
(R1 + r0 + |
1)2 |
+ (R1 + r0 )2 − |
|
|
|
|
|
|
|
|
|
|
||||||||
|
−2(R1 + r0 |
+ |
1 )(R1 + r0 )cos(α1 − ϕ1 ); |
|
|
|
|
|
||||||||||||||
|
|
|
|
|
|
|
||||||||||||||||
|
|
|
|
|
|
|
|
|
|
|
|
|
|
|
|
|
|
|
|
|
|
(6.13) |
|
|
|
−ac − |
(ac) |
2 |
− (c |
2 |
− b |
2 |
)(a |
2 |
+ b |
2 |
) |
|
|
||||||
ϕ = arccos |
|
|
|
|
|
, |
|
|||||||||||||||
|
|
|
|
|
2 |
|
|
|
2 |
|
|
|
|
|
|
|
|
|||||
1 |
|
|
|
|
2(a |
+ b |
) |
|
|
|
|
|
|
|
|
|
||||||
|
|
|
|
|
|
|
|
|
|
|
|
|
|
|||||||||
|
|
|
|
|
|
|
|
|
|
|
|
|
|
|
|
|
|
|
|
|
|
|
где a = (R2 + r0 )cosα2 + (R1 + r0 )cosα1 ;
181
Стр. 181 |
ЭБ ПНИПУ (elib.pstu.ru) |
b = (R2 + r0 )sin α2 − (R1 + r0 )sin α1 ; |
|
|
|
||||
|
(R + r + |
2 |
)2 − (a2 + b2 ) − (R + r + |
1 |
)2 |
||
c = |
2 |
0 |
1 |
0 |
. |
||
|
|
|
2(R1 + r0 + 1) |
|
|
||
|
|
|
|
|
|
|
Исследуем траектории движения центра заготовки при ее вращении в зависимости от наладки бесцентрового суперфинишного станка. В табл. 6.1 приведены расчетные траектории центра при одном обороте заготовки со средним радиусом r0 = 8 мм, имеющей отклонение формы в виде 2-, 3-, 4- и 5-й гармоник с амплитудамиа2 = а3 = а4 = а5 = 1 мкм.
В качестве оптимизируемого параметра выступает суммарный угол α установки валков. Радиусы валков приняты R1 = R2 = = 62,5 мм и положение их центров А1 и А2 определено через параметры α1, α2 и r0. Так же, как и ранее, начальные фазы гармоник взяты равными нулю и углы установки валков относительно заготовки приняты равными α1 = α2.
Траектории движения центра при бесцентровом суперфинишировании похожи на траектории, полученные при бесцентровом шлифовании. Это объясняется тем, что радиусы валков многократно превышают отклонения формы заготовки и в окрестности точек контакта мало отличаются от прямых.
Для 2-, 3-, 4- и 5-й гармоник рассчитан критерий K точности базирования в зависимости от наладочных углов валков. Результаты расчета представлены в табл. 6.2. Для 2-й гармоники при углах α = 10, 15° и для 3-й гармоники при угле α = 10° имеет место провал заготовки между валками в ряде положений при ее вращении. ПоэтомукритерийK дляуказанныхслучаевневычислен.
Исследование критерия K показало, что для 2-, 3-, 4-, 5-й гармоник оптимальным углом наладки в диапазоне α = 10…60° является максимальное значение 60°. Для приведенных примеров при α = 10…60° значение критерия К изменяется от 1,0 до 4,5. По аналогии с бесцентровым шлифованием с поперечной подачей можно предположить, что оптимальные углы наладки располагаются в пределах α = 80…110°, но реализация таких углов на суперфинишном станке невозможнапо силовым ограничениям.
182
Стр. 182 |
ЭБ ПНИПУ (elib.pstu.ru) |

6 . 1 |
|
|
|
|
|
Таблица |
суперфинишировании |
|
50 60 |
|
|
|
заготовки при бесцентровом |
Угол наладки α, град |
40 |
|
|
|
движения центра |
|
30 |
|
|
|
Траектории |
|
20 |
|
|
|
|
n |
2 |
3 |
|
|
|
|
|
|
183 |
Стр. 183 |
|
|
|
ЭБ ПНИПУ (elib.pstu.ru) |
|
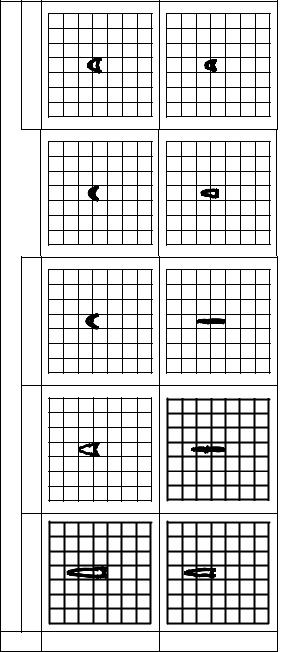
6 . 1 |
|
|
|
табл. |
60 |
|
|
Окончание |
|
|
|
|
50 |
|
|
α, град |
|
|
|
наладки |
40 |
|
|
Угол |
|
|
|
|
30 |
|
|
|
20 |
|
|
n |
4 |
5 |
|
184 |
|
|
|
Стр. 184 |
|
|
ЭБ ПНИПУ (elib.pstu.ru) |
|
|
|
|
|
|
|
|
|
Таблица |
6 . 2 |
||
|
Критерий K при бесцентровом суперфинишировании |
|
||||||||||
|
|
|
|
|
|
|
|
|
|
|
|
|
n |
|
|
|
Угол наладки α, град |
|
|
|
|||||
10 |
15 |
20 |
25 |
30 |
35 |
40 |
45 |
50 |
55 |
60 |
||
|
||||||||||||
2 |
– |
– |
3,54 |
2,67 |
2,19 |
1,83 |
1,56 |
1,36 |
1,20 |
1,09 |
1,00 |
|
3 |
2,41 |
1,92 |
1,81 |
1,79 |
1,76 |
1,69 |
1,61 |
1,52 |
1,43 |
1,32 |
1,23 |
|
4 |
– |
3,27 |
2,38 |
1,86 |
1,61 |
1,43 |
1,30 |
1,20 |
1,12 |
1,06 |
1,01 |
|
5 |
4,50 |
3,44 |
2,77 |
2,32 |
2,08 |
1,90 |
1,65 |
1,45 |
1,31 |
1,23 |
1,16 |
Для рассчитанного диапазона наладок критерий К принимает значения только больше единицы, что говорит о копировании погрешностей базовой поверхности и наличии тенденции к созданию новых погрешностей. При уменьшении отношения радиусов валков и заготовки наблюдается некоторое уменьшение критерия K. Однако, как будет показано далее, участие в процессе формообразования шлифовального бруска с большой площадью охвата поверхности заготовки создает условия для эффективного исправления погрешностей формы.
При оптимизации процесса бесцентрового суперфиниширования по критерию точности базирования следует учитывать геометрические, кинематические и силовые ограничения. Геометрические ограничения накладываются исходя из расчета профиля валков на этапе профилирования или расчета формообразующей траектории при наладке станка. Ограничения по силовым параметрам имеют нелинейный характер и выявляются при решении задачи силового замыкания контакта.
Помимо математической модели базирования, также разработана модель формообразования поперечного сечения заготовок при бесцентровом суперфинишировании. Предложенный подход основан на моделировании процесса съема припуска с учетом погрешностей базирования и изменения натягов в технологической системе. В качестве обобщенного критерия формообразования выступает коэффициент K1 исправления профиля, равный отношению исходного отклонения от круглости к полученному после имитационной обработки 1.
185
Стр. 185 |
ЭБ ПНИПУ (elib.pstu.ru) |

Расчетная схема формообразования представлена на рис. 6.6. Заготовка1 базируетсянадвух валках 3. Брусок 2 вприработанном состоянии имеет образующую в виде дуги окружности радиуса r3 с углом охвата 2θ. Значение угла θ зависит от соотношения ширины бруска, диаметра заготовки и величины приработки шлифовального бруска. Радиус r3 в процессе обработки меняется в пределах половины поля допуска на диаметр заготовки. В рамках предложенной модели это не имеет принципиального значения, поэтому радиусобразующей брускапринятпостоянным.
Рис. 6.6. Схема формообразования при бесцентровом суперфинишировании
Поперечноесечениезаготовкиопишемследующимобразом:
p |
|
r = r0 + t + an cos(nϕ − ϕn ) , |
(6.14) |
n=2
где t – припуск на сторону.
186
Стр. 186 |
ЭБ ПНИПУ (elib.pstu.ru) |
В процессе обработки стабилизируются натяги в ТС, созданные исходными отклонениями формы заготовки и погрешностями базирования. При определении мгновенных натягов и мгновенных съемов металла приняты следующие допущения. Изменение радиуса заготовки по отношению к номинальному вызывает изменение натягов в ТС и, соответственно, давления шлифовального бруска. При постоянной жесткости резания приращение давления прямопропорциональноприращению снимаемогометалла.
Радиальный съем металла δ в пределах длины контакта заготовки со шлифовальным бруском:
δ = r − |
r + t |
j |
|
+ χΔr , |
(6.15) |
|
|
||||||
|
|
0 |
|
|
|
|
|
|
|
m |
|
|
где j – текущий оборот заготовки (1 ≤ k ≤ m); m – число оборотов заготовки, необходимое для съема припуска t; χ – коэффициент, связанный с жесткостью резания.
При расчете величины δ учитывают только положительные значения, при отрицательных значениях полагают δ = 0. За j-й оборот заготовки в каждой точке профиля съем металла произойдет только один раз. Съем полного припуска t совершится за m оборотов заготовки.
При каждом текущем обороте заготовки 2jπ получаем новый профиль rj, для которого заново рассчитываем погрешности базирования. После изменения угла ϕ до 2mπ заготовку считают обработанной. Окончательный съем металла произойдет на величину, большую, чем исходный припуск t. Это объясняется дополнительным съемом металла из-за изменения натягов в ТС. Исходными данными при моделировании являются: радиус детали r0; параметры профиля n; аn и ϕn; припуск t; максимальное число m оборотов заготовки при обработке; радиусы валков R1 и R2; ширина В шлифовальногобруска; углыα1 иα2 установки валков.
Получив дискретно заданный профиль детали после имитационной обработки, необходимо найти его аналитический эквивалент и определить отклонение от круглости. Если считать, что
187
Стр. 187 |
ЭБ ПНИПУ (elib.pstu.ru) |
центры средней окружности детали до и после обработки совпадают с достаточной точностью, то параметры уравнения профиля в виде тригонометрического полинома (6.1) определяют по формулам Бесселя [61], а отклонение от круглости 1 рассчитывают по стандартной методике [62]. В случае, когда полученное значение K1 меньше требуемого [K1], проводят параметрическую оптимизацию при наличии ограничений. Единообразное математическое представление профиля детали при формообразовании и измерении позволяет проанализировать не только комплексный показатель K1, но и изменение амплитудного состава погрешностей.
Рассмотрим пример моделирования процесса формообразования при следующих параметрах: r0 = 12 мм; t = 0,004 мм;
m = 50; R1 = R2 = 60 мм; B = 12 мм; α1 [35°; 15°]; α2 [15°; 35°]. Результаты представлены на рис. 6.7 в виде поперечных профилей детали: I – исходный; II – после обработки при указанных параметрах; III – после обработки с оптимальными углами контакта (α1 = 22°; α2 = 54°); IV – после обработки с увеличенным припуском (t = 0,008 мм); V – после обработки с увеличенной шириной бруска (B = 24 мм). Профили изображены в виде наложенных друг на друга круглограмм с совмещенными центрами, одинаковым радиальным масштабом увеличения и различными средними радиусами записи (для равномерного размещения профилей в зоне записи диаграммы). Амплитуды гармонических погрешностей детали для вариантов I–IV представлены на рис. 6.8.
Исходное отклонение от круглости составило = 4,2 мкм. После имитационной обработки для вариантов II–V отклонения от круглости 1 равны 3,1; 2,2; 1,8; 1,7 мкм, коэффициент K1 исправления профиля равен 1,35; 1,91; 2,33; 2,47 соответственно. Таким образом, увеличению критерия формообразования K1 способствуют: увеличение ширины инструмента, припуска на обработку, а также оптимизация наладочных параметров станка.
188
Стр. 188 |
ЭБ ПНИПУ (elib.pstu.ru) |

Рис. 6.7. Расчетные круглограммы деталей
Анализ результатов моделирования показал, что наибольшее влияние на исправление профиля заготовки оказывают ширина шлифовального бруска и припуск на обработку. Однако наличие жестких технологических ограничений приводит к необходимости поиска других параметров оптимизации. Поэтому
189
Стр. 189 |
ЭБ ПНИПУ (elib.pstu.ru) |

наиболее актуальными параметрами при оптимизации процесса формообразования следует считать углы контакта заготовки с валками. По итогам численных экспериментов рекомендована область оптимальных углов контакта, определяемая соотноше-
ниями: α1 ≤ α2 + 5°; α1 ≥ 15°; α1 + α2 ≤ 90°, получившая применение в разработке нового способа суперфиниширования [49].
а
б
Рис. 6.8. Амплитудный состав гармонических погрешностей профиля детали: а – вариант I; б – вариант II
190
Стр. 190 |
ЭБ ПНИПУ (elib.pstu.ru) |