
Суперфинишные станки для автомобильной промышленности
..pdfТаблица 4 . 3
Техническая характеристика суперфинишно-полировального автомата модели 3А875
Параметр |
Значения |
|
Максимальный диаметр вращения по оси коренных |
280 |
|
шеек, мм |
||
|
||
Максимальная длина обрабатываемого вала, мм |
1000 |
|
Максимальный диаметр обрабатываемой шейки, мм |
75 |
|
Частота вращения шпинделя изделия, мин–1 |
|
|
черновой режим |
43; 67; 95 |
|
чистовой режим |
85; 132; 190 |
|
Частота колебаний изделия, дв. ход/мин: |
|
|
черновой режим |
400; 800 |
|
чистовой режим |
200; 400 |
|
Ход осциллирования изделия, мм, мм |
0–8 |
|
Суммарная мощность электродвигателей, кВт |
16 |
|
Габаритные размеры станков с приставным оборудо- |
5500×4000×2350 |
|
ванием, мм |
|
|
Масса, т |
8,0 |
Окончание чистового режима производится при пониженных усилиях прижима брусков. Обработка детали на станках ведется по автоматическому циклу. Время обработки на черновом режиме устанавливается по реле времени.
Станок модели 3877 предназначен для последовательного суперфиниширования коренных и шатунных шеек крупногабаритных валов. В конструктивном отношении станок значительно отличается от остальных станков подобного назначения. Это связано как с габаритными размерами самого станка, так и со спецификой обработки крупногабаритных коленчатых валов.
Станок оснащен двумя суппортами. На каждом суппорте между направляющими щеками шарнирно подвешена инструментальная головка, осуществляющая прижим брусков к обрабатываемой поверхности и их осциллирование. Один суппорт предназначен для обработки коренных шеек, второй – шатунных. Суппорты могут работать одновременно или последовательно.
111
Стр. 111 |
ЭБ ПНИПУ (elib.pstu.ru) |
Они имеют возможность совершать быстрые установочные перемещения и медленные движения вдоль обрабатываемой шейки.
На базе станков моделей 3874, 3875 и 3876 выпускаются специальные автоматы и полуавтоматы, налаженные на обработку конкретного вала; число инструментальных головок, устанавливаемых на этих станках, соответствует числу обрабатываемых шеек вала. Кроме суперфиниширования шеек вала специальные станки могут оснащаться устройствами для полирования шеек, суперфиниширования галтелей и базовых торцов вала.
Суперфинишно-полировальный автомат модели 3А875 (табл. 4.3) предназначен для обработки коренных и шатунных шеек, атакже базового торцаколенчатых валов длинойдо1000 мм.
Автомат двухпозиционный. На первой позиции одновременно суперфинишируются все шейки и полируется торец, на второй позиции полируются шейки. Рабочие позиции автомата могут включаться как одновременно, так и последовательно.
Суперфиниширование производится абразивными брусками. Полирование шеек – абразивной лентой 23А3 ГОСТ 12439–79; полирование торца – алмазной лентой типа АПЛ АСО – Р9 50 % (ТУ327–68). Шероховатость поверхности шеек после суперфиниширования Rа = 0,16 мкм, после полирования торцаRа = 0,04 мкм.
Компоновка автомата следующая. На основании 1 установлена стойка 6, на которой расположены блоки инструментальных головок 4, бабки изделия 2 и задние бабки 5 первой и второй позиций. На основании размещены приводы шпинделей бабок изделий, транспортер 7 и механизмы подъема на линию центров. Внутри стойки находятся приводы осциллирования шпинделей. Гидростанция, электрошкаф и станция охлаждения вынесены за пределы автомата. Пульт управления 3 укреплен на поворотном кронштейне стойки.
Загрузка коленчатых валов производится на призмы транспортера. Транспортер перемещает вал в зону обработки первой и второй позиций. Механизмы подъема переносят вал на линию центров, где он зажимается центрами передней и задней бабок. Бабка изделия обеспечивает вращение вала и его осциллирова-
112
Стр. 112 |
ЭБ ПНИПУ (elib.pstu.ru) |
ние во время обработки. На призмах транспортера одновременно могут находиться восемь коленчатых валов. Если обработанный вал не снят с позиции разгрузки транспортера, автомат дорабатывает цикл и останавливается.
Привод вращения изделия на каждой позиции индивидуальный, состоящий из двухскоростного электродвигателя (N = 2,65/3,4 кВт, n = 1440/2820 мин–1) и коробки скоростей. Зажим изделия в центрах, осциллирование шпинделя бабки изделия, подвод и прижим инструментальных головок, а также работа транспортера осуществляются от гидропривода автомата.
4.3.Суперфинишные головки
Вусловиях индивидуального и мелкосерийного производства для окончательной обработки цилиндрических и конических поверхностей применяют суперфинишные головки моделей СФГ-50, СФГ-100 и СФГ-300. Головки устанавливают на обычные токарные, круглошлифовальные или карусельные станки так, чтобы они не мешали производить токарные или шлифовальные работы.
Для последовательной обработки коренных и шатунных шеек коленчатых валов служит суперфинишная головка СШ301 (табл. 4.4), предназначенная для установки на круглошлифовальном станке модели 3А423 вместо шлифовальной бабки. Головка может быть переналажена на полирование шеек коленчатых валов. Максимальный радиус кривошипа 105 мм.
Суперфинишная головка модели СШ-301 предназначена для последовательной обработки абразивными брусками коренных и шатунных шеек коленчатых валов и может быть налажена на полирование шеек абразивной лентой. Головка устанавливается на шлифовальный станок модели 3А 423, используемый для перешлифовки коренныхи шатунных шеекколенчатыхвалов.
Головка состоит из следующих основных узлов (рис. 4.3): основания 9, стойки 8, механизма осциллирования 3 и каретки 4. На роликовых направляющих механизма осциллирования установлен кронштейн, на поворотной оси которого подвешены каретка 4 и
113
Стр. 113 |
ЭБ ПНИПУ (elib.pstu.ru) |

инструментальная головка 1. Расположение инструментальной головки на поворотной оси обеспечивает слежение инструмента за вращением шейки во время обработки. Уравновешивание массы инструментальной головки производится пружиной 6 через цепную передачу 5. Привод механизма осциллирования осуществляется гидродвигателем 7, подвод и прижим брусков – гидроцилиндром2, установленнымнасалазках каретки.
Рис. 4.3. Головка суперфинишная модели СШ-301
114
Стр. 114 |
ЭБ ПНИПУ (elib.pstu.ru) |
|
Таблица 4 . 4 |
|
Технические характеристики суперфинишных головок |
||
|
|
|
Параметр |
Модель головки СШ-301 |
|
Диаметр обрабатываемого изделия, мм |
69–105 |
|
Число инструментальных головок |
1 |
|
Частота колебаний бруска, дв. ход/мин |
150–600 |
|
Усилие прижима бруска, Н |
до 1000 |
|
Мощность электродвигателя привода ос- |
– |
|
циллирования, кВт |
||
|
||
Габаритные размеры, мм |
1150×600×1650 |
|
Масса, кг |
510 |
Инструментальная головка 1 имеет три ползуна, в которых закреплены абразивные бруски. Ползуны системой рычагов соединены между собой таким образом, что при перемещении верхнего ползуна синхронно перемещаются боковые ползуны, производя зажим и отжим инструмента от обрабатываемой шейки вала. Для установки коленчатого вала в центрах станка и при переходе с одной шейки на другую механизм осциллирования вместе с кареткой и инструментальной головкой поднимается вверх по направляющим стойки 1. Подъем осуществляется гидроцилиндром, расположенным в стойке.
Станция гидропривода, станция охлаждения и электрошкаф расположены с задней стороны станка. Зона обработки закрыта щитком, установленным на станине станка. Для переналадки головки СШ-301 на обработку абразивной лентой с ползунов инструментальной головки снимаются державки с абразивными брусками, а на их месте устанавливаются специальные колодки для прижима ленты и два направляющих ролика: один с абразивной лентой, второй – для приема отработанной ленты.
Стр. 115 |
ЭБ ПНИПУ (elib.pstu.ru) |
5. РАСЧЕТ ВАЛКОВЫХ УСТРОЙСТВ БЕСЦЕНТРОВЫХ СУПЕРФИНИШНЫХ СТАНКОВ
5.1. Общие принципы расчета валковых устройств
До настоящего времени описание геометро-кинематических аспектов бесцентрового суперфиниширования с продольной подачей сложных (в том числе конических и бомбинированных) поверхностей нашли ограниченное отражение в технической литературе. В результате на практике не всегда достигалась требуемая точность обработки, что ограничивает применение данного высокопроизводительного процесса при изготовлении сложных поверхностей.
Следует указать многочисленные работы, посвященные расчету валковых устройств бесцентровых суперфинишных станков [24, 26, 39, 40 и др.]. Большинство из них имеют приближенный характер и ряд неточностей, не позволяющих обеспечить высокую точность расчета. Поэтому разработаны новые, более строгие геометрические модели формообразования.
Общий подход к геометрическому описанию формообразования на бесцентровых суперфинишных станках основан на том, что требуемая форма продольного сечения детали однозначно определена траекторией ее движения при обработке [37, 41]. Отличия для цилиндрических, конических и бомбинированных поверхностей заключаются в математическом описании траектории их относительного движения, а также поверхности заготовки, которая по формеможетне соответствоватьповерхностидетали.
Авторский подход к решению задачи профилирования ведущего круга основан на общем методе исследования пространственных зацеплений, который построен на векторно-матричных преобразованиях функции формообразования и кинематическом условии касания поверхностей [42]. Условие касания аналитически задается как ортогональность векторов нормали и скорости относительного движения, выраженное их скалярным произведе-
116
Стр. 116 |
ЭБ ПНИПУ (elib.pstu.ru) |

нием n V = 0. В случае профилирования валков в виде тел вращения для цилиндрических и бомбинированных поверхностей применен упрощенный метод, построенный на свойствах осей зацепления. Осью зацепления называют жестко связанную с неподвижной системой координат прямую линию, через которую проходят нормали в контактных точках поверхностей. Поскольку ведущий круг и заготовка представляют собой тела вращения, то нормали к их поверхностям проходят через оси. Таким образом, в данном случае пара сопряженных осей зацепления – собственно оси ведущего круга и заготовки.
При анализе формообразующая система бесцентрового суперфинишного станка представляется эквивалентной схемой в виде пространственного механизма с перекрещивающимися осями. Расчет профиля валков опирается на положения теории формообразования поверхностей резанием. Основные предпосылки заключаются в следующем:
•профиль продольного сечения заготовки однозначно формируется траекторией ее движения относительно производящей поверхности шлифовального круга;
•исходная заготовка может иметь форму как конгруэнтную детали, так и отличную от нее;
•скорости вращения и продольного перемещения заготовки при обработке должны быть постоянными или близкими к постоянным;
•скорость вращения заготовки многократно превышает скорость продольного перемещения (кроме обработки конической поверхности);
•валки и заготовка должны иметь постоянный контакт по всей длине обработки.
На основе изложенных общих посылок методика профилирования валков состоит из следующих этапов:
•определяем форму и размеры базирующих и обрабатываемых поверхностей заготовки и описываем их аналитически (например, для бомбинированной заготовки исходная поверх-
117
Стр. 117 |
ЭБ ПНИПУ (elib.pstu.ru) |
ность, как правило, цилиндрическая, а при обработке конических деталей базирующими являются коническая и торцовая поверхности);
•составляем эквивалентную координатную схему формообразующей системы станка с учетом взаимного расположения валков и заготовки;
•на основе векторно-матричных преобразований координат из системы заготовки в систему координат валка получаем уравнения семейства поверхностей валка;
•выявляем контактную линию на семействе поверхностей, которая дает искомую поверхность валка, для чего используем кинематическое условие касания (для валка в виде тела вращения кинематическоеусловиеупрощается наоснове осей зацепления);
•описываем сечение валка или его профиль в цилиндрической системе координат для тела вращения (при числе неизвестных, превышающем число составленных уравнений, принимаем численный метод решения).
При обработке цилиндрических поверхностей заготовки перемещаются параллельно своей оси и образуют так называемый виртуальный цилиндр [43]. Ось виртуального цилиндра параллельна направлению осцилляции брусков и перекрещивается с осями валков. При обработке конических поверхностей оси валков параллельны друг другу и направлению осцилляции брусков, но перекрещиваются с осями конических заготовок. Конические заготовки совершают винтовое движение за счет винтовой канавки на валках. Обработку бомбинированных поверхностей производят с использованием валков, как гладкой формы, так и с винтовой канавкой. Заготовки, имеющие, как правило, исходно цилиндрическую форму, перемещаются по дуге определенного радиуса в осевой плоскости осцилляции брусков. Оси валков при гладкой форме перекрещиваются, а при наличии винтовой канавки – параллельны.
Использование для базирования и создания движения подачи винтовой канавки на валках способствует повышению точности обработки. Однако для бомбинированных поверхностей ва-
118
Стр. 118 |
ЭБ ПНИПУ (elib.pstu.ru) |

лок должен иметь винтовую канавку сложного профиля с изменяющимися вдоль оси параметрами. Профиль валка рассчитывают для конкретной заготовки и параметров наладки шлифовального станка, поэтому его целесообразно применять только в массовом производстве. Изготовление валков подобной формы на универсальном оборудовании затруднено, поэтому они получили ограниченное применение.
Задача профилирования валков основана на общем методе исследования, который построен на векторно-матричных преобразованиях функции формообразования и кинематическом условии касания. Условие касания аналитически задается как ортогональность векторов нормали и скорости относительного движения, вы-
раженное их скалярным произведением n V = 0. В случае профилирования валков в виде тел вращения для цилиндрических и бомбинированных поверхностей применен упрощенный метод, построенный на свойствах осей зацепления. Осью зацепления называют жестко связанную с неподвижной системой координат прямую линию, через которую проходят нормали вконтактных точках поверхностей. Поскольку валок и заготовка представляют собой тела вращения, то нормали к их поверхностям проходят через оси. Таким образом, в данном случае пара сопряженных осей зацепления– собственноосивалковизаготовки.
5.2.Валковые устройства для обработки цилиндрических поверхностей
Поверхность валков определим как тела вращения, непрерывно касающиеся виртуального цилиндра заготовок (потока цилиндрических заготовок). Введем в рассмотрение следующие координатные системы (рис. 5.1): S0(X0 О0 Y0 Z0) – система заго-
товки; S1(X1 О1 Y1 Z1) и S2(X2 О2 Y2 Z2) – системы левого и правого валков соответственно. Системы координат S1 и S2 по отно-
шению к системе S0 повернуты вокруг оси Y по и против часовой стрелки на угол λ и смещены по оси X на величину h и по оси Y на величины – v и v соответственно.
119
Стр. 119 |
ЭБ ПНИПУ (elib.pstu.ru) |
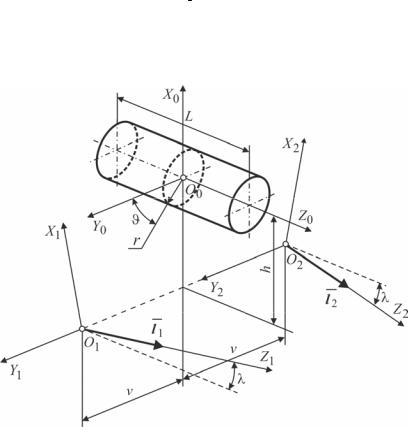
Наладочную координату h не устанавливают непосредственно на станке, а получают при заданной геометрии валка, радиусе заготовки и наладочных координатах v, λ. Поэтому вместо координаты h целесообразно задавать так называемый «номинальный» радиус R валков в точке перекрещивания. В результате значение h будет определено очевидным образом.
Поверхность цилиндрической заготовки в векторно-пара- метрической форме в системе S0 опишем уравнением
r0 = −r sin ϑ i + r cosϑ |
j |
+ z |
k |
, |
(5.1) |
где r – радиус заготовки; ϑ, z – криволинейные координаты цилиндрической поверхности.
Рис. 5.1. Координатная схема профилирования валков при обработке цилиндрических поверхностей
120
Стр. 120 |
ЭБ ПНИПУ (elib.pstu.ru) |