
Суперфинишные станки для автомобильной промышленности
..pdfШлифовать валки с поверхностью квазигиперболоида возможно на специализированных станках, многокоординатных станках с ЧПУ и универсальных круглошлифовальных станках высокой точности. Первые два типа станков не требуют специального расчета наладок, но в условиях инструментальных цехов машиностроительных предприятий невозможно проектирование таких операций из-за отсутствия данного оборудования. Поэтому актуальным становится использование универсального оборудования при изготовлении или ремонте валков. При этом необходимо рассчитать наладки круглошлифовального станка и в ряде случаев его модернизировать.
Получить поверхность валка в виде квазигиперболида на универсальном круглошлифовальном станке плоским кругом прямого профиля можно, создав пространственный разворот их осей. Также для образования требуемого профиля валка необходимы дополнительные наладочные параметры, задающие относительное положение круга в процессе обработки.
Принципиальные схемышлифованиявалковданына рис. 5.21. Вариант а предусматривает разворот шлифовального круга на углы ψ и ν за счет смещения задней бабки станка в вертикальном
игоризонтальном направлениях, вариант б – разворот на угол ψ за счет смещения задней бабки станка в вертикальном направлении
исмещение Н шлифовального круга относительно оси центров станка. Данные схемы шлифования защищены патентами на изобретения[49, 50].
Для расчета наладочных параметров A, H, ψ, ν необходимо определить поверхность валков, получаемую при использовании рассмотренных схем формообразования.
Введем в рассмотрение следующие координатные системы (рис. 5.22), соответствующие схемам на рис. 5.21: S0(X0 О0 Y0 Z0) – система шлифовального круга; S1(X1 О1 Y1 Z1) – система валка. Система координат S1 по отношению к системе S0 повернута вокруг оси Y по часовой стрелке на угол ψ и смещена по оси Y на величину А. Также для варианта а система S1 смещена по оси X на вели-
151
Стр. 151 |
ЭБ ПНИПУ (elib.pstu.ru) |

чину –Н, а для варианта б система координат S1 повернута вокруг осиХ противчасовой стрелки наугол ν.
Рис. 5.21. Схемы шлифования квазигиперболоидных валков суперфинишного станка
Рис. 5.22. Координатные схемы формообразования квазигиперболоидных валков
Расчет поверхности валка, получаемой в результате шлифования, осуществляют аналогично задаче профилирования валков. Поэтому ограничимся приведением окончательных уравнений для поверхности валка:
152
Стр. 152 |
ЭБ ПНИПУ (elib.pstu.ru) |
– вариант а:
X1 = −Rкр sin ϑ cosψ − z sin ψ; |
|
|
|
||||||
Y |
= R |
cosϑ cosν − (z cosψ − R |
sin ϑsin ψ)sin ν − А; |
|
|||||
1 |
кр |
|
|
|
кр |
|
|
|
|
Z |
= R |
sin ϑ cosν + (z cos |
ψ − R |
|
|
(5.41) |
|||
sin ϑsin ψ)cosν; |
|||||||||
1 |
кр |
|
|
|
кр |
|
|
|
|
|
|
|
ztgψ |
|
|
|
|
||
tgϑ = − |
|
; |
|
|
|
|
|||
|
Acosν + z sin ν |
|
|
|
|
||||
|
|
|
|
|
|
|
|
||
– вариант б: |
|
|
|
|
|
|
|||
|
|
|
X1 = −Rкр sin ϑ cosψ − z sin ψ + Н; |
|
|||||
|
|
|
Y1 = Rкр cosϑ − А; |
|
|
|
|||
|
|
|
|
|
|
||||
|
|
|
Z1 = −Rкр sin ϑsin ψ + z cosψ; |
|
(5.42) |
||||
|
|
|
|
||||||
|
|
|
|
Н − zctgψ |
|
|
|
|
|
|
|
|
tgϑ = |
, |
|
|
|
||
|
|
|
А |
|
|
|
|
||
|
|
|
|
|
|
|
|
|
где Rкр – радиус шлифовального круга; ϑ, z – криволинейные координаты цилиндрической поверхности круга; ψ – угол перекрещивания осей шлифовального круга и валка в вертикальной плоскости; ν – угол перекрещивания осей шлифовального круга и валка в горизонтальной плоскости; А – межосевое расстояние шлифовального круга и валка; Н – вертикальное наладочное смещение шлифовального круга.
Алгоритм формообразования валка заключается в приближении получаемого профиля (Zi; Ri) к требуемому (Z1i; R1i) на основе оптимизации наладочных параметров: угла λ перекрещивания осей шлифовального круга и валка в вертикальной плоскости; угла ν перекрещивания осей шлифовального круга и валка в горизонтальной плоскости; межосевого расстояния А шлифовального круга и валка, вертикального наладочного смещения Н шлифовального круга. Радиус шлифовального круга Rкр выбирают из технологических соображений.
Целевая функция J при оптимизации представляет собой сумму квадратов отклонений текущего радиуса от заданного в любом конечном числе n сечений валка Zi:
153
Стр. 153 |
ЭБ ПНИПУ (elib.pstu.ru) |
n |
|
J (ψ, A, H ,ν) = (Ri − R1i )2 , |
(5.43) |
i=1
где R1i – требуемый радиус в i-м сечении валка; Ri – текущий радиус в i-м сечении валка.
Требуемый профиль валков (Z1i; R1i) может быть задан аналитически уравнениями (5.7) или таблично (табл. 5.1). Использование большого числа сечений n нецелесообразно, так как профиль представляет собой гладкую кривую с малоизменяющейся кривизной. В приводимых далее примерах для целевой функции были использованы7 сечений, соответствующихтабл. 5.1.
Численный анализ целевой функции J показал, что она является унимодальной, поэтому в качестве методов оптимизации можно применять локальные методы оптимизации, например покоординатныйспуск, наискорейший спускили методконфигураций.
В табл. 5.6 приведены профили валков, полученные при шлифовании кругом ПП с наружным диаметром 200 мм для трех вариантов из табл. 5.1. Необходимо обратить внимание, что формообразование профиля валка варианта v = 72,5 мм по схеме б невозможно.
При оптимизации наладочных параметров наименьшее расчетное значение целевой функции J = 2 10–6 было достигнуто при шлифовании профиля валка v = 72,5 мм по схеме а, а наибольшее значение J = 7 10–5 – при шлифовании профиля валка v = 68,5 мм по схеме а.
Точность изготовления валков обусловливает требования к точности расчета и установки на станке наладочных параметров. Так, изменение угла ψ на 1′ для варианта v = 72,5 мм приводит к появлению погрешности профиля валка в 0,006 мм. Аналогичное изменение угла ψ для варианта v = 68,5 мм по схеме обработки б вызвало максимальную погрешность профиля валка 0,005 мм, что соответствовало первоначальной погрешности при точной наладке. Для этого же варианта изменение угла ν на 1′ привело к образованию погрешности профиля в 0,01 мм.
154
Стр. 154 |
ЭБ ПНИПУ (elib.pstu.ru) |

155 .Стр
ru).pstu.(elib ПНИПУ ЭБ
155
Схема |
Вариант |
обработки |
профиля валка |
|
v = 72,5 мм |
а |
мм |
v71,5= |
|
|
v = 68,5 мм |
|
|
|
|
|
|
|
|
|
|
Таблица |
5 . 6 |
|
Профили валков, полученные при шлифовании |
|
|
|
|||||||
|
|
Профиль валка |
|
|
Параметры наладки |
|
||||
|
|
|
|
|
||||||
|
|
|
|
|
|
|
|
|
|
|
|
Zi, мм |
|
Ri, мм |
Ri – R1i, мм |
А, мм |
ψ |
Н, мм |
|
ν |
|
|
0 |
|
62,924 |
|
0 |
|
|
|
|
|
|
100 |
|
62,689 |
|
0 |
|
|
|
|
|
|
200 |
|
62,547 |
|
0 |
162,5 |
|
11,747 |
|
– |
|
300 |
|
62,500 |
|
0 |
2°14′38″ |
|
|||
|
400 |
|
62,547 |
|
0 |
|
|
|
|
|
|
500 |
|
62,689 |
|
0 |
|
|
|
|
|
|
600 |
|
62,924 |
|
0 |
|
|
|
|
|
|
0 |
|
64,206 |
|
0 |
|
|
|
|
|
|
100 |
|
63,547 |
|
–0,001 |
|
|
|
|
|
|
200 |
|
62,977 |
|
–0,002 |
161,494 |
|
29,727 |
|
– |
|
300 |
|
62,499 |
|
–0,001 |
2°13′48″ |
|
|||
|
400 |
|
62,113 |
|
0 |
|
|
|
|
|
|
500 |
|
61,820 |
|
0,001 |
|
|
|
|
|
|
600 |
|
61,620 |
|
0 |
|
|
|
|
|
|
0 |
|
65,443 |
|
0,004 |
|
|
|
|
|
|
100 |
|
64,377 |
|
–0,003 |
|
|
|
|
|
|
200 |
|
63,394 |
|
–0,005 |
158,399 |
|
47,775 |
|
– |
|
300 |
|
62,497 |
|
–0,003 |
2°9′59″ |
|
|||
|
400 |
|
61,684 |
|
0 |
|
|
|
|
|
|
500 |
|
60,959 |
|
0,002 |
|
|
|
|
|
|
600 |
|
60,322 |
|
0,003 |
|
|
|
|
|
|
|
|
|
|
|
|
|
|
|
|

156 .Стр
156
ru).pstu.(elib ПНИПУ ЭБ
Окончание табл. 5 . 6
Схема |
Вариант |
|
Профиль валка |
|
|
Параметры наладки |
|
|||
обработки |
профиля валка |
|
|
|
|
|
|
|
|
|
Zi, мм |
|
Ri, мм |
Ri – R1i, мм |
А, мм |
ψ |
Н, мм |
ν |
|||
|
|
0 |
|
64,207 |
|
0,001 |
|
|
|
|
|
мм |
100 |
|
63,545 |
|
–0,003 |
|
|
|
|
|
200 |
|
62,977 |
|
–0,002 |
161,541 |
3°13′40″ |
– |
2°19′41″ |
|
|
71,5 |
|
|
|||||||
|
|
300 |
|
62,500 |
|
0 |
||||
|
v = |
400 |
|
62,116 |
|
0,003 |
|
|
|
|
|
500 |
|
61,822 |
|
0,003 |
|
|
|
|
|
|
|
|
|
|
|
|
|
|||
б |
|
600 |
|
61,619 |
|
–0,001 |
|
|
|
|
|
0 |
|
65,442 |
|
0,003 |
|
|
|
|
|
|
|
|
|
|
|
|
|
|||
|
мм |
100 |
|
64,377 |
|
–0,003 |
|
|
|
|
|
200 |
|
63,396 |
|
–0,003 |
159,253 |
10°59′24″ |
– |
8°26′6″ |
|
|
68,5 |
|
|
|||||||
|
|
300 |
|
62,500 |
|
0 |
||||
|
v = |
400 |
|
61,689 |
|
0,005 |
|
|
|
|
|
500 |
|
60,962 |
|
0,005 |
|
|
|
|
|
|
|
|
|
|
|
|
|
|||
|
|
600 |
|
60,319 |
|
0 |
|
|
|
|
Погрешности наладки межосевого расстояния А практически полностью переходят на профиль валка, мало искажая его, но вызывая соответствующее изменение радиусов профиля. При изменении А на 0,01 мм для варианта v = 68,5 мм по схеме обработки б максимальная погрешность профиля валка составила 0,014 мм, что превысило начальную на 0,009 мм. Вертикальное смещение Н шлифовального круга активно влияет на профиль валка – для варианта v = 72,5 мм при отклонении Н на 0,01 мм максимальная погрешность профиля равна 0,006 мм.
Диаметр шлифовального круга при прочих равных условиях слабо влияет на точность обработки при обеих схемах формообразования. Его выбор в первую очередь обусловлен технологическими соображениями стойкости и экономичности. При износе круга коррекция его относительного положения только по межосевому расстоянию приводит к появлению существенных погрешностей обрабатываемого профиля. Так, при износе круга на 1 мм и внесении поправки в межосевое расстояние на 1 мм погрешности составили: для схемы а варианта v = 72,5 мм – 0,003 мм, для варианта v = 71,5 мм – 0,007 мм, для схемы б варианта v = 68,5 мм – 0,04 мм. Таким образом, при износе круга более 0,5…1,0 мм необходимо вновь рассчитать все оптимальные наладочные параметры ψ, ν, А, Н. С увеличением диаметра круга несколько уменьшается влияние ошибки вналадке наточностьобработки.
На основании проведенных экспериментов по шлифованию валков можно сделать следующие выводы.
Схемы шлифования а и б при прочих равных условиях обеспечивают приблизительно одинаковую точность изготовления профиля валка. Однако обработка симметричных валков по схеме б невозможна. Отклонения получаемого профиля валков при погрешности установки наладочных параметров ψ, ν – 10″ и
А, Н – 0,005 мм составляют от 0,001 до 0,005 мм.
Причем для валка симметричной формы возможна минимизация отклонений профиля до 0,001 мм. Приведенные данные справедливы для максимальной длины валков L = 800 мм. Для меньшей длины валков указанные отклонения существенно уменьшаются, что позволяет снизить точность наладки как ли-
157
Стр. 157 |
ЭБ ПНИПУ (elib.pstu.ru) |
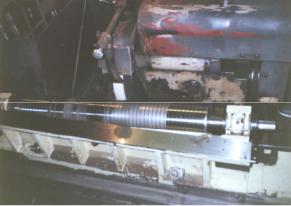
нейных, так и угловых параметров. Поэтому необходимую точность наладки круглошлифовального станка следует определять в каждом конкретном случае.
Приведенные выводы соответствуют результатам экспериментальных исследований и практической реализации рассмотренных схем формообразования при шлифовании валков для бесцентровых суперфинишных станков модели SZZ-3 на ОАО «Саратовский подшипниковый завод». Использовался модернизированный круглошлифовальный станок модели Olivetti (рис. 5.23). Применение разработки позволило шлифовать валки суперфинишных станков на универсальном круглошлифовальном станке с соблюдением всех требований рабочего чертежа валика поршневого пальца 6-1НР16115Е.62: непостоянство диаметра – не более 0,003 мм и отклонение профиля продольного сечения – не более 0,007 мм.
Рис. 5.23. Шлифование квазигиперболоидных валков суперфинишного станка
Формообразование валков суперфинишных станков для обработки конических поверхностей
Изготовление валков для обработки конических поверхностей с нелинейчатой винтовой поверхностью включает в себя получение заданного профиля, как рабочего, так и вспомогательного уча-
158
Стр. 158 |
ЭБ ПНИПУ (elib.pstu.ru) |
стков. При этом нецелесообразно добиваться полного соответствия профилю валка, полученного на этапе профилирования. Для рабочего участка валка, предназначенного для базирования, необходимо обеспечить угол профиля β и создать некоторое отклонение поверхности валка от теоретической за счет увеличенного значения стрелы прогиба f (в тело валка). Вспомогательный участок призван обеспечить контакт валка с деталью при суперфинишировании в некоторой заданной точке, что не налагает жестких требований на его форму. Кроме того, данная часть валка при изготовлении служит для выхода шлифовального круга. Таким образом, основное требование к вспомогательному участку валка – определенная ширинапереходныхкривых, заданная конструктором(см. рис. 5.4).
Рассмотрим профилирование шлифовального круга для формообразования винтовой поверхности валка. Данная задача заключается в нахождении осевого сечения производящей поверхности круга по исходным координатам профиля валка и наладочным параметрам станка. В качестве обрабатывающего оборудования, как правило, используют резьбошлифовальный станок соответствующего типоразмера.
Расчет профиля шлифовального круга для обработки винтовой поверхности может быть реализован различными методами. Например, в работе [44] для решения данной задачи был применен численный способ. Основное его достоинство заключается в гарантированном отсутствии подрезания профиля. Разработанная методика позволила спрофилировать круг для изготовления валков, имеющих нелинейчатую винтовую поверхность.
Однако при высоких требованиях к точности профиля круга его правка вызывает известные технологические трудности. В связи с этим предложено использовать упрощенную коническую форму шлифовального круга, а задачу формообразования решать на основе оптимизации параметров наладки.
Введем в рассмотрение следующие координатные системы (рис. 5.24): S0(X0 О0 Y0 Z0) – система конического шлифовального круга; S1(X1 О1 Y1 Z1) – вспомогательная условно неподвижная система; S2(X2 О2 Y2 Z2) – система валка. Система координат S1
159
Стр. 159 |
ЭБ ПНИПУ (elib.pstu.ru) |

по отношению к системе S0 повернута вокруг оси Х по часовой стрелке на угол λ и смещена на величину А. Винтовое движение в системе S2 задано параметрами р и ϕ. Данная схема формообразования может быть реализована, например, на резьбошлифовальном станке.
Рис. 5.24. Координатная схема формообразования валка
По аналогии с выводом формул в п. 5.3 получим выражения для семейства поверхностей валка:
X2 |
= (X0 |
+ A)cosϕ + (Y0 cosλ − Z0 sin λ)sin ϕ; |
|
|
Y2 = −(X0 |
|
|
(5.44) |
|
+ A)sin ϕ + (Y0 cosλ − Z0 sin λ)cosϕ; |
||||
Z2 |
= Y0 sin λ + Z0 cosλ − pϕ, |
|
|
|
|
|
где р – шаг винтовой линии; ϕ – угловой параметр винтового движения валка; А – кратчайшее межосевое расстояние; λ – угол перекрещивания осей валка и шлифовального круга.
160
Стр. 160 |
ЭБ ПНИПУ (elib.pstu.ru) |