
Суперфинишные станки для автомобильной промышленности
..pdfМинистерство образования и науки Российской Федерации
Федеральное государственное бюджетное образовательное учреждение высшего профессионального образования «Пермский национальный исследовательский политехнический университет»
Cаратовский государственный технический университет имени Ю.А. Гагарина
О.В. Захаров, А.В. Кочетков, Л.В. Янковский
СУПЕРФИНИШНЫЕ СТАНКИ ДЛЯ АВТОМОБИЛЬНОЙ ПРОМЫШЛЕННОСТИ
Монография
Издательство Пермского национального исследовательского
политехнического университета
2014
Стр. 1 |
ЭБ ПНИПУ (elib.pstu.ru) |
УДК 621.923 ББК 34.637 З-38
Рецензенты:
д-р техн. наук, проф. А.Ф. Денисенко (Самарский государственный технический университет);
д-р техн. наук, проф. П.Ю. Бочкарев (Саратовский государственный технический университет им. Ю.А. Гагарина)
Захаров, О.В.
З-38 Суперфинишные станки для автомобильной промышленности : монография / О.В. Захаров, А.В. Кочетков, Л.В. Янковский. – Пермь : Изд-во Перм. нац. исслед. поли-
техн. ун-та, 2014. – 265 с.
ISBN 978-5-398-01166-1
Рассмотрены физические основы, технология и конструкции станков для суперфиниширования. Приведены математические модели для расчета валковых систем бесцентровых суперфинишных станков, применяемых в автомобильной промышленности. Изложен авторский подход к оптимальной наладке оборудования, комплексно учитывающий геометрические, кинематические и силовые параметры формообразования. Приведены результаты экспериментов и практической реализации на примерах поршневого пальца, натяжного ролика, штока гидроцилиндра.
Предназначено для специалистов машиностроительных предприятий, научных работников, аспирантов и студентов машиностроительных специальностей.
УДК 621.923 ББК 34.637
ISBN 978-5-398-01166-1 |
© ПНИПУ, 2014 |
|
© СГТУ, 2014 |
Стр. 2 |
ЭБ ПНИПУ (elib.pstu.ru) |
ВВЕДЕНИЕ
Одна из современных тенденций мирового развития техники заключается в постоянном ужесточении требований к точности и качеству поверхностей деталей машин и механизмов. В первую очередь это относится к подвижным деталям автомобильного двигателя, подшипников качения и авиакосмической техники.
Заключительные этапы технологического процесса традиционно связаны с использованием абразивной обработки. Очевидно, что и в дальнейшем абразивная обработка будет занимать важное место в финишной технологии. Суперфиниширование служит окончательной операцией, на которой стремятся уменьшить отклонения формы, волнистость и шероховатость поверхности. Метод суперфиниширования получил широкое применение при изготовлении тел вращения благодаря высокой производительности и возможности полной автоматизации. Именно поэтому данный метод наиболее эффективно используется в массовом производстве деталей автомобильной техники.
Вместе с тем бесцентровое суперфиниширование имеют ряд особенностей, затрудняющих дальнейшее повышение точности обработки. Во-первых, осуществляется силовое замыкание контакта, и съем припуска зависит как от траектории перемещения заготовок, так и от стабильности их вращения и скорости продольной подачи. Во-вторых, характерно наследование геометрии заготовок с предшествующих операций. В-третьих, на детерминированные факторы процесса формообразования накладываются стохастические, которые при образовании отклонений формы заготовок проявляются наиболее значимо.
Известны фундаментальные труды в области обеспечения качества деталей машин [1–4] и работы, заложившие физические основы процессов абразивной обработки [5–10]. Значительное число монографий посвящено технологии абразивной обработки и отдельным ее аспектам [11–23]. Конструкции и особенности проек-
3
Стр. 3 |
ЭБ ПНИПУ (elib.pstu.ru) |
тирования технологического оборудования, в том числе суперфинишных станков, рассмотрены в работах [24–27]. За последние годы в отечественной промышленности получены новые результаты в исследовании динамики станков, проектировании абразивного инструмента, создании систем автоматизированного управления [28–33]. Однако до сих пор мало внимания уделено созданию комплексного подхода к обеспечению точности на этапах проектирования и эксплуатации технологического оборудования на основе детерминированных моделей, описывающих геометрические, кинематические и силовые параметры формообразования. Применение единого методологического подхода требует создания системы критериальных оценок качества процесса формообразования и обоснования в использовании формализованных методов оптимизации. Кроме того, детерминированные модели лишь в первом приближении отражают реальные процессы, а одно из направлений повышения степени их адекватности связано с учетом стохастических факторов.
Результативность решения приведенных задач на практике существенным образом зависит от технических возможностей того или иного предприятия и квалификации специалистов, занимающихся данными вопросами. В современных российских условиях опыт, накопленный на предприятиях космического или оборонно-промышленного комплекса, не всегда находит применение в других отраслях промышленности. Зарубежные производители не публикуют подробную информацию об особенностях технологии суперфиниширования и наладке станков. Указанные трудности в настоящее время сдерживают повышение точности суперфиниширования и ограничивают область обработки только достаточно простыми поверхностями.
Исторически процесс суперфиниширования возник в связи с повышением требований к точности формы и снижению шероховатости тел качения подшипников. В 1935 г. в США было установлено, что при транспортировании по железной дороге новых автомобилей за счет толчков и тряски на недостаточно точно обработанных дорожках подшипников качения возникали
4
Стр. 4 |
ЭБ ПНИПУ (elib.pstu.ru) |
вмятины или углубления [34]. Причиной их появления были сами тела качения. Фирма «Крайслер» (США) первой правильно распознала причину этих дефектов и устранила их путем введения суперфинишной обработки. Слово «суперфиниш», которое было использовано для названия этого метода, буквально означает «самая последняя» ступень обработки. В 1940 г. в своих первых публикациях Уаллис сообщил о данном методе обработки. Фирма «Крайслер» уже тогда для удовлетворения собственных потребностей изготовила суперфинишные станки по современному принципу движений. Позднее разработками в этой области занялись и в других странах.
Теоретические основы бесцентрового суперфиниширования были заложены отечественными исследованиями в 60–70-е гг. ХХ в. Однако сложность физических и геометро-кинемати- ческих аспектов бесцентрового суперфиниширования не позволяет говорить о достаточной изученности этого процесса даже в настоящее время. За последние десятилетия благодаря гибкости процесса суперфиниширования значительно расширился диапазон обработки деталей различных форм и размеров. Кроме того, изменились представления о возможностях исправления погрешностей формы обрабатываемых поверхностей. Все это дает основания утверждать о необходимости дальнейших исследований, как фундаментального характера, так и в интересах отдельных отраслей техники, например автомобильной промышленности, чему и посвящена настоящая монография.
Стр. 5 |
ЭБ ПНИПУ (elib.pstu.ru) |
1. ФИЗИЧЕСКИЕ ОСНОВЫ СУПЕРФИНИШИРОВАНИЯ
1.1. Влияние суперфиниширования на эксплуатационные свойства деталей машин
Эксплуатационные свойства деталей машин (износостойкость, усталостная прочность, контактная жесткость, коррозионная стойкость и др.) существенным образом зависят от качества их сопрягаемых поверхностей и поверхностного слоя, которые определены геометрическими параметрами (номинальная геометрия, отклонения формы и расположения поверхностей, волнистость, шероховатость) и физико-механическими свойствами поверхностных слоев (микротвердость, остаточные напряжения, структура). Все эти параметры неразрывно связаны с технологией изготовления. Чтобы получить то или иное эксплуатационное свойство детали или узла, необходимо обеспечить требуемые характеристики качества рабочих поверхностей деталей. Для решения этой задачи следует знать зависимости, связывающие характеристики качества обрабатываемых поверхностей с условиями обработки (режимы, геометрия инструмента и т.д.), причем эти зависимости должны отражать влияние технологической наследственности.
Суперфиниширование выполняют после шлифования, а для заготовок, не подвергающихся термической обработке, – после чистового и тонкого точения на специальных суперфинишных станках или универсальных токарных и шлифовальных станках с суперфинишными головками. Суперфиниширование применяют в качестве финишной операции, в основном при обработке наружных поверхностей. Широкое распространение суперфиниширование получило в подшипниковой промышленности для доводки колец, роликов, иголок, шаров. В автомобильной промышленности суперфинишированием обрабатывают шейки коленчатых и распределительных валов, поршни и поршневые
6
Стр. 6 |
ЭБ ПНИПУ (elib.pstu.ru) |
пальцы, тормозные диски и барабаны, клапаны, валы коробок передач, штоки амортизаторов. В станкостроении суперфинишируют шпиндели и пиноли, роторы электродвигателей, в других отраслях машиностроения – гладкие и ступенчатые валы, круглые калибры, плунжеры, золотники, валы для холодной прокатки листового материала и другие детали.
Поверхности заготовок, полученные суперфинишированием, обладают значительно большей площадью фактического контакта по сравнению с поверхностями, полученными другими методами обработки. По литературным данным, высота микронеровностей, достигаемая при разных способах обработки, составляет: при тонком точении Rz = 10…40 мкм, при шлифовании Rz = 4…10 мкм, притонкомшлифованииRz = 1…4 мкм, присуперфинишировании Rz = 0,1…0,5 мкм. Несущая часть поверхности (опорная поверхность) в зависимости от высоты шероховатости при Rz = 10 мкм равна 4 %, при Rz = 5 мкм – 12 %, при Rz = 2 мкм – 30 %, при
Rz = 0,1 мкм – 95 % [5]. В результате опорная поверхность после шлифования составляет примерно 30 %, в результате суперфиниширования она увеличивается до 95 %. Данный факт имеет большое значение для повышения износостойкости деталей, сокращения времени их приработки и сохранения заданных посадок в узлах машин. Известно, что значение периода приработки деталей особенно велико для ответственных узлов, лимитирующих точность и надежность работы машин. От результатов приработки зависит время наступления усиленного износа, вызываемого изменением зазоров в трущихся парах, а следовательно, долговечность механизмови машин.
При шлифовании в результате высокой температуры в зоне резания (1100–1200 °С) и больших давлений разрушается кристаллическая структура поверхностного слоя заготовок. Путем суперфиниширования деформированный слой может быть частично или полностью удален и создана высококачественная износостойкая поверхность. Новый деформированный слой при суперфинишировании не создается, так как небольшие давления, применяемые при обработке, повышают температуру по-
7
Стр. 7 |
ЭБ ПНИПУ (elib.pstu.ru) |
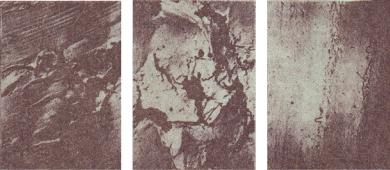
верхности незначительно (не более 50–80 °С). После суперфиниширования поверхностный слой имеет структуру, по которой равномерно проходят тонкие канавки, в то время как после обработки другими методами на поверхности видны разрывы, трещины и стыковки (рис. 1.1).
а |
б |
в |
Рис. 1.1. Поверхности (×12000), полученные шлифованием (а), абразивной доводкой (б) и суперфинишированием (в) [24]
Направление следов механической обработки на несущей поверхности также оказывает немаловажное влияние на эксплуатационные свойства деталей. Так, взаимно пересекающиеся риски на суперфинишированной поверхности образуют замкнутые резервуары, в которых надежно удерживается смазка. Исследования влияния процесса суперфиниширования на состояние поверхностного слоя показали, что в поверхностном слое металла возникают напряжения сжатия от 250 до 800 МПа, распространяющиеся на глубину 7–10 мкм. Микротвердость поверхности термически необработанных заготовок после суперфиниширования повышается на 30–40 %, а закаленных – на 10–15 %. Причина упрочнения заключается в интенсивном измельчении кристаллических блоков и увеличенииплотностидислокаций.
Широкое применение суперфиниширование получило в подшипниковой промышленности. Известно, что наибольшее влияние на долговечность подшипников качения оказывают: от-
8
Стр. 8 |
ЭБ ПНИПУ (elib.pstu.ru) |
клонение от круглости, волнистость, шероховатость, наличие шлифовочных или доводочных рисок. Повышение точности изготовления тел качения увеличивает долговечность подшипников на 30 %, снижение огранки с 4 до 1 мкм подшипника 307 повышает долговечность в 2 раза, а уменьшение волнистости с 2,5 до 1 мкм увеличивает контактную выносливость более чем в 3 раза. При этом наличие волнистости вызывает неравномерное распределение шероховатости и твердости, что создает дополнительный источник концентрации напряжений, особенно при циклических нагрузках. Снижение шероховатости рабочих поверхностей подшипников в интервале Ra = 0,25 мкм – Ra = = 0,08…0,04 мкм в несколько раз увеличивает долговечность. Наличие отдельных рисок на рабочих поверхностях деталей подшипников, выходящих за пределы общего фона шероховатости поверхности, может вызывать резкое снижение долговечности. Возникновение отдельных доводочных рисок обусловлено разной высотой расположения зерен и степенью их затупления в конце рабочего цикла. Глубина рисок при суперфинишировании может примерно на 25–50 % превышать высоту микронеровностей основной шероховатости.
Важным комплексным показателем качества подшипника является шумность его работы. По данным литературных источников, уровень вибраций подшипника качения зависит от огранки и волнистости дорожки и тел качения. Разноразмерность тел качения и шероховатость, не выходящие за пределы допустимых значений, не оказывают существенного влияния на шумность подшипников. Наибольший вклад вносят геометрические отклонения поверхностей шариков или роликов. Например, с увеличением величины огранки роликов подшипников 42204, 32205, 32206, 32306 с 0,3 мкм до 3,4 мкм уровень вибрации подшипника при n = 3000 мин–1 повысился на 16,5 дБ. Наиболее интенсивное возрастание вибраций происходит с увеличением огранки от 0,3 до 1 мкм, а отклонение от круглости приводит к увеличению высокочастотных составляющих спектра.
9
Стр. 9 |
ЭБ ПНИПУ (elib.pstu.ru) |
Точность обработки суперфинишированием зависит от жесткости технологической системы, основными элементами которой являются устройство для передачи давления на брусок, базирующие элементы и заготовка. Лучшие результаты достигаются при передаче давления на брусок непосредственно от штока гидроили пневмоцилиндра суперфинишной головки. Наличие в этой системе пружин значительно (в 4–6 раз) замедляет исправление отклонения от круглости. Современные суперфинишные станки оснащены гидравлической системой прижима бруска с обратным клапаном [8].
При бесцентровом суперфинишировании роликов подшипников достигается уменьшение овальности от 0,8–1,2 мкм до 0,2– 0,6 мкм иотклоненияот круглостиот1,2–2,5 мкм до 0,4–1,0 мкмза один проход. При последующих проходах исправление некруглости значительно замедляется. При наличии достаточного припуска отклонение от круглости после суперфиниширования составляет 0,3–0,07 мкм (рис. 1.2). Бесцентровое суперфиниширование способствует резкому уменьшению разноразмерности обрабатываемых заготовок. Так, исходная разноразмерность роликов, равная 7–10 мкм, уменьшается после одного прохода до 2–4 мкм, а после двух-трех проходов– до 1–2 мкм.
Точность формы заготовки в продольном сечении зависит от соотношения длины бруска и обрабатываемой поверхности, а также от величины перебега бруска. При обработке с продольной подачей величина перебега должна составлять 0,33– 0,25 длины бруска. В этом случае отклонения от прямолинейности не превышают 1,0–1,5 мкм.
За последнее время разработаны новые способы размерного суперфиниширования с жестким прижимом брусков (односторонним и в обхват) подобно тому, как происходит при хонинговании. Такое суперфиниширование позволяет во многом уменьшать отклонения от правильной геометрической формы обрабатываемых поверхностей.
10
Стр. 10 |
ЭБ ПНИПУ (elib.pstu.ru) |