
Методическое пособие 747
.pdf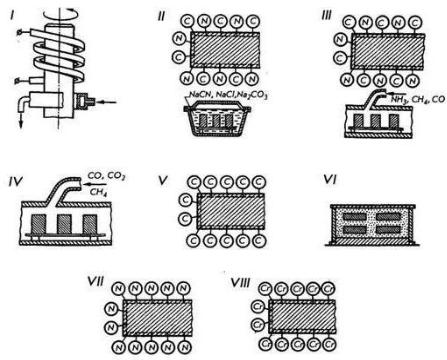
Наиболее распространенные виды химико-термической обработки стали — цементация, азотирование и цианирование. Некоторые методы упрочения поверхности металлических изделий приведены на рис.
I – индукционная закалка; II – цианирование;
III – нитроцементация; IV – газовая цементация; V – цементация;
VI – цементация в твердом карбюризаторе; VII – азотирование;
VIII – диффузное хромирование.
Рис. 16
40
Цементация – процесс поверхностного насыщения стальных деталей углеродом, с целью получения изделия с вязкой сердцевиной и твердой поверхностью. Цементации подвергают детали из углеродистой и легированных сталей с содержанием углерода 0,1 ... 0,3%. После цементации поверхностный слой должен содержать 0,8 ... 1,0% углерода. Цементации подвергаются детали, работающие обычно на истирание в условиях ударных нагрузок, например зубчатые колеса, шейки коленчатых валов, поршневые кольца и другие детали машин.
Азотирование – процесс насыщения поверхностных слоев стальных изделий азотом. Этот процесс обеспечивает повышение твердости и износостойкости деталей, увеличивает предел усталости, повышает коррозионную стойкость.
Твердость азотированного слоя обычно сохраняется при нагревании детали до 450 ... 500° С, а поверхностный слой детали после цементации начинает терять твердость уже при 200° С. Азотирование является одной из завершающих операций обработки изделий, так как после него изделия подвергают только шлифованию.
Чтобы придать сердцевине детали определенную прочность и вязкость, перед азотированием деталь подвергают закалке и отпуску.
Азотирование – дорогой процесс, так как проникновение азота в сталь протекает очень медленно (около 10 ч для получения слоя глубиной 0,1 мм). Чтобы сократить его в 1,5
... 2 раза, прибегают к двухступенчатому нагреву: сначала изделие выдерживают при температуре 510 ... 520° С, а затем несколько часов в зависимости от толщины слоя — при температуре 560 ... 600° С. Процесс азотирования ускоряется в 6
... 7 раз при нагреве изделий токами высокой частоты. Азотированию подвергаются в основном легированные
стали. Углеродистые стали азотируют в том случае, когда надо получить поверхностный слой толщиной 0,02 ... 0,04 мм
41
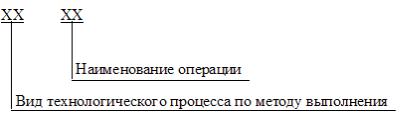
для защиты от коррозии. Такое азотирование называют антикоррозийным.
Цианирование – процесс, при котором происходит одновременное насыщение поверхностного слоя стали углеродом и азотом. Этот процесс происходит в ваннах с расплавленными цианистыми солями либо в газовой среде, содержащей метан, аммиак и закись углерода.
После ванны детали закаливаются в воде или масле. Цианированный слой толщиной 0,2 ... 0,3 мм имеет довольно высокую твердость и износостойкость. Цианированию подвергают режущие кромки сверл, резцов, метчиков, фрез, а также некоторые зубчатые колеса автомобилей и др.
Классификация технологических операций построена по методу иерархической 2 – ступенчатой классификации.
Вструктуре кода технологической операции каждая ступень классификации обозначена двумя цифровыми десятичными знаками. На каждой ступени классификации кодирование осуществляется цифрами от 01 до 99, причем на второй ступени группировки 10, 20, 30, и т.д. используют для кодирования обобщенных наименований операций.
Вклассификаторе установлена следующая структура кода технологической операции:
Рис. 17. Схема обозначения технологических операций
На первой ступени классификации основанием деления служит признак «вид технологического процесса по методу выполнения», характеризуемый определенным составом технологических операций.
42
В табл. 1 приведены виды технологических процессов по методу выполнения и их коды.
Если процесс состоит менее чем из ста операций и имеет достаточный резерв кодов, то для кодирования отведена одна группировка. Например: «Порошковая металлургия» – код 65, «Фотохимико-физическая обработка» – код 55.
Назначение припусков на механическую обработку и разработка технологического процесса начинается с анализа технологичности изготавливаемой детали.
Пример анализа технологичности детали
Деталь - крышка. Служит для осевой фиксации подшипника качения, поддерживающего червячный вал редуктора.
Состоит из посадочного цилиндра О 52е9. Параметр шероховатости которого Ra 1,6.
Для крепления крышки болтами к корпусу редуктора, её фланец О 80 имеет четыре отверстия О 8.
Торец О 52е9 упирающийся в наружное кольцо подшипника и привальные торец фланца имеет параметры шероховатости так же Ra 1,6.
Эти торцы связаны размером 14 четырнадцатого квалитета, однако параллельность этих поверхностей ограничена величиной 0,05мм. Поверхности полости О 42 мм и глубиной 14 мм не обрабатывается. Размеры крышки маленькие (до 500 мм). Материал крышки - серый чугун с пределом прочности на растяжение 15кг/мм.
Структура СЧ15: перлит, феррит, графит пластинчатый средней величины.
Химический состав:
Углерод – 3,5% - 3,7%
Кремний – 2% - 2,4% Марганца –......
43
Технологичность детали:
Подсчитать кол-во основных металлообрабатывающих технологических операций.
Размеры детали соответствуют нормальному ряду чисел, допустимые отклонения размеров соответствуют СТ.
СЭВ 144 – 75.
Деталь жесткая, имеет поверхности, удовлетворяющие требованиям достаточной точности установки.
Простановка размеров технологична, т. к. их легко можно измерить на обрабатывающих и контрольных операциях.
При изготовлении детали используют нормализованные измерительные и режущие инструменты.
Назначение технологических операций
Если технологический процесс насчитывает более ста технологический операций, то для его кодирования выделяется несколько классификационных группировок. Например: «Термообработка» – коды 50 и 51, «Испытания» – коды 06 и 07. На второй ступени классификации основание деления является признак «наименование операции».
При необходимости отрасли промышленности могут проводить дальнейшую детализацию признаков классификации технологических операций и их кодов, которые следует записывать после кода операции по „Классификатору технологических операций машиностроения и приборостроения”.
Примерный перечень технологических операций, необходимых для изготовления детали может выглядеть следующим образом:
000 – Заготовительная
005 – Термообработка
010 – Токарная
015 – Токарная
020 – Токарная
44
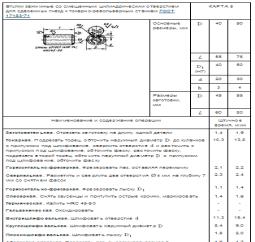
025 – Сверлильная
030 – Фрезерная
035 – Плоскошлифовальная
040 – Токарная
045 – Круглошлифовальная
050 – Резьбонарезная
055 – Внутришлифовальная
060 – Контрольная
Перечень операций оформить в виде технологической карты (рис. 18).
Рис. 18. Технологическая карта
Выполнение работы:
1.По выданному преподавателем чертежу изделия и выбранной серийности производственной программы сделать анализ технологичности изделия;
2.Определить размеры заготовки, согласно требованиям чертежа, предварительно рассчитав величины припусков на механическую обработку;
3.Определить количество и состав технологических операций.
45
РАЗДЕЛ 2. ОСНОВНОЕ ТЕХНОЛОГИЧЕСКОЕ ОБОРУДОВАНИЕ МЕХАНООБРАБАТЫВАЮЩЕГО ПРОИЗВОДСТВА
Лабораторная работа № 5.
Определение потребного количества технологического оборудования
(4 часа)
Цель работы: ознакомиться с технологическим оборудованием металлообрабатывающего участка машиностроительного завода. Определить состав и количество металлообрабатывающего оборудования.
Технические средства и программное обеспечение:
1.IBM-PC или совместимый компьютер;
2.Операционная система Microsoft Windows;
3.Пакет офисных программ Microsoft Office;
Средства для эскизирования:
1.Линейка инструментальная;
2.Штангенциркуль;
3.Карандаш.
Теоретические сведения:
Подсчет количества оборудования
Количество оборудования на механическом участке рассчитывается по трудоемкости (по видам работ с учетом годовой программы выпуска):
|
, |
(2) |
Э КВ |
46
где: Т – годовая трудоемкость по видам работ (операци-
ям).
Fэ – годовой эффективный фонд времени работы одного станка в часах.
Кв – коэффициент выполнения норм. Кв =1,1; Ср – расчетное количество станков по операциям. Fэ = ((Дк-Дв-Дпр)·Тs-Тсокр)·С·(1-a/100),
Здесь:
Дк – количество календарных дней в году (365). Дв – количество выходных дней в году (104). Дпр – количество праздничных дней в году (8). Тs – продолжительность рабочей смены (8,2).
Тсокр – количество часов сокращения рабочей смены в предпраздничные дни (6).
С – количество смен (2).
a – процент потерь времени работы на ремонт и регламентированные перерывы (3%).
Fэ = ((365-104-8)·8,2-6)·2·(1-3/100) = 4013 часов.
Количество станков для токарной операции:
принимаем 5 Количество станков для фрезерной операции:
принимаем 5 Количество станков для шлифовальной операции:
принимаем 3 Количество станков для сверлильной операции:
принимаем 3 Количество станков для строгальной операции:
принимаем 2 Количество станков для зубонарезной операции:
47
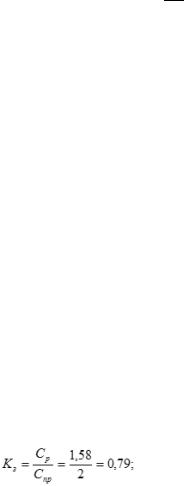
принимаем 2 Количество станков для долбёжной операции:
принимаем 2 Коэффициент загрузки будет равен:
КЗ , (3)
ПР
где Спр – принятое количество оборудования.
Ср – расчетное количество станков по операциям. Коэффициент загрузки оборудования для токарной опе-
рации: Коэффициент загрузки оборудования для фрезерной
операции: Коэффициент загрузки оборудования для шлифоваль-
ной операции: Коэффициент загрузки оборудования для сверлильной
операции: Коэффициент загрузки оборудования для строгальной
операции: Коэффициент загрузки оборудования для зубонарезной
операции: Коэффициент загрузки оборудования для долбёжной
операции:
Общий коэффициент загрузки оборудования:
48
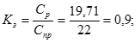
Под нормированием технологических процессов понимают назначение технически обоснованных норм времени на продолжительность выполнения операций.
Технически обоснованной нормой времени называют время выполнения технологической операции в определённых организационно-технических условиях, наиболее благоприятных для данного типа производства.
На основе технически обоснованных норм времени устанавливают расценки, определяют производительность труда, осуществляют планирование производства и т. п.
|
|
, |
(4) |
|
|||
где L – длина обработки, мм; |
|
||
S – подача, мм/об; |
|
||
n – частота вращения шпинделя, мин-1; |
|
||
i – число рабочих ходов (проходов). |
|
||
, |
(5) |
где l0 – длина обрабатываемой поверхности в направлении обработки, мм;
l1 – длина врезания, мм;
l2 – перебег режущего инструмента, мм.
Расчеты необходимого количества оборудования на участке сводим в табл. 5.
Необходимые для выполнения лабораторной работы расчеты можно выполнить как вручную, так и с помощью специализированной программы, написанной в табличном процессоре Microsoft Excel (рис. 19).
Студенты направления подготовки «Конструкторско-
технологическая подготовка кузнечно-штамповочного производства» выполняют расчеты в настоящей работе применительно к условиям кузнечно-штамповочного производства. Подбор кузнечно-штамповочного оборудования тесно
49