
Методическое пособие 747
.pdf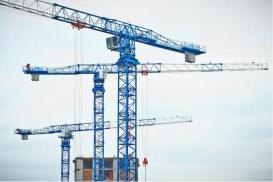
бования к диапазону регулирования скорости и плавности переходных процессов. Режим работы, как правило, не превышает 5К.
Перегрузочные краны, работающие в морских и речных портах. Такие краны являются универсальными, т.е. могут работать как в крюковом режиме, так и в грейферном. Для работы с грейфером такие краны имеют две грузовые лебедки, которые управляются раздельно. При работе в крюковом режиме лебедки синхронизируются. Для обеспечения высокой производительности такие краны имеют высокие рабочие скорости. Режим работы может доходить до 8К. Диапазон регулирования скорости механизма подъема в крюковом режиме может доходить до 8:1.
Портальные краны имеют также механизмы поворота, изменения вылета стрелы и передвижения. У перегрузочных портальных кранов передвижение является установочным (т.е. редко используемым) движением.
Башенные краны (рис. 58) применяются в промышленном и гражданском строительстве.
Рис. 58. Башенные краны с поворотной и неповоротной башнями
[http://avtokrany.kz/upload/iblock/44b/44b08830d8f9dec0a773a7 c37fcd4845.jpg]
120
На рис. 58 показаны два основных архитектурных типа башенных кранов – с поворотной и неповоротной башнями. Кроме того, изменение вылета может производиться подъемом и опусканием стрелы (краны с маневровой стрелой,) или передвижением по стреле грузовой тележки с подвешенной к ней крюковой подвеске (краны с балочной стрелой).
Особенностью башенного крана является также наличие больших упругих деформаций металлоконструкций, требующих учета при выборе механических характеристик электроприводов (прежде всего механизмов поворота) и режимов пуска и торможения.
Многие башенные краны имеют специальные механизмы и приспособления для самомонтажа.
Спецификой работы башенного крана является также питание его от временных электрических сетей малой мощности или автономных источников электроэнергии. Это предъявляет к его электрооборудованию дополнительные требования в части сохранения работоспособности при провалах напряжения.
Выбор подъемно-транспортного оборудования
Выбор того или иного подъемно-транспортного оборудования для механизации складских работ зависит от типа склада, ассортимента хранимых товаров, габаритов отдельных мест и используемого немеханического оборудования. Выбирать такое оборудование рекомендуется так, чтобы тип машин соответствовал:
•технологии обработки грузов с учетом их ассортимента и габаритов;
•объему погрузочно-разгрузочных и складских работ;
•характеру и типу выполняемых на складе операций по приему, складированию и выдаче грузов с учетом общей технологии складских работ,
121
•условиям проводимых работ (на открытых складских площадках или в закрытых складских помещениях);
•режиму работ складов;
•правилам техники безопасности;
•требованиям санитарных норм и противопожарной безопасности.
Кроме того, выбранное подъемно-транспортное оборудование должно обеспечивать повышение производительности труда и его облегчение и использоваться с высокой экономической эффективностью.
Так же имеет значение рабочая зона грузоподъемной машины. Она тоже оказывает существенное влияние на стоимость, а сама, в то же время, зависит от геометрических параметров машины. Поэтому, в частности, необходимо подбирать мостовой кран или тельфер с высотой подъема, лишь ненамного превышающей высоту размещения.
И, допустим, будет не совсем разумно приобретать стреловой подъемный кран с телескопической стрелой, если весь фронт работ предполагается в пределах минимального вылета.
Во многих случаях приобретение полноценного подъемного крана вовсе не целесообразно, так как достаточно установки обычного электротельфера, или, кран-балки, управляемой с пола.
В общем рекомендации по выбору грузоподъемной техники будут следующие:
1.Для закрытых цехов и мастерских подойдут мостовые краны, кран-балки и тельферы;
2.Для открытых грузовых площадок – козловые краны;
3.Для выездных работ в полевых условиях – стреловые (чаще всего автомобильные) краны;
4.Для речных и морских портов и доков – портальные
краны;
5.Для площадок многоэтажного строительства – башенные краны.
122
Все производители грузоподъемной техники поставляют свою продукцию по опросным листам, в которых, кроме основных характеристик оборудования, указывается и характер условий работы техники.
В частности, указывается необходимость наличия специального грузозахватного приспособления для проведения специальных работ.
Для своевременного обеспечения цехов материалами, заготовками, деталями и узлами необходимо определять потребное количество подъемно транспортных средств. Для точного определения следует учитывать массу грузов, путь перемещения, время, затрачиваемое на подъем грузов и многие другие условия.
Количество подъемно-транспортных машин, необхо-
димое для выполнения соответствующего объема погрузоч- но-разгрузочных и складских работ, определяется по формуле:
|
|
|
Г К |
|
, |
(7) |
|
|
ПЭ СР |
Д |
|
||
|
|
Р |
|
|||
где М – потребное количество машин для выполнения |
||||||
работ, единиц; |
|
|
|
|
||
Ог – годовой объем грузооборота, подлежащий пере- |
||||||
грузке данным видом подъемно-транспортных машин, т.; |
|
|||||
ПЭ – эксплуатационная производительность машин, т/ч; |
||||||
Ср – |
число смен работы машин в сутки; |
|
||||
Днр – |
число нерабочих дней машины в году; |
|
Кн – коэффициент неравномерности грузооборота (грузопотока).
Количество кранов можно определить по следующей
формуле: |
|
|
|
КР |
|
, |
(8) |
|
|||
|
ФЭ |
|
где NJ – количество j-х изделий, подлежащих транспортировке за год:
i – количество транспортных операций; tp – время одного рейса, мин;
123

ФЭ – годовой действительный расчетный фонд времени работы крана, ч.
Для определения производительности машины подсчитывают ее фактическую среднюю производительность за расчетный период, исходя из средних нагрузок, средних расстояний перемещения грузов и средних скоростей ее движения.
Эксплуатационная часовая производительность подъем- но-транспортной машины может быть определена по формуле:
ПЭ ПТ КЗ КВ, |
(9) |
где Пэ – эксплуатационная производительность машин периодического действия, т/ч;
Пт – техническая (конструктивная) производительность машин, т/ч;
Кз – коэффициент использования машины по загрузке (грузоподъемности, мощности);
Кв – коэффициент использования машины по времени. Коэффициент использования машины по загрузке (гру-
зоподъемности) определяют по формуле: |
|
|
КЗ |
, |
(10) |
ГМ
где ОСР – средняя масса транспортируемого груза за один цикл работы, т;
Гм – номинальная грузоподъемность машины, т. Коэффициент использования машины во времени рас-
считывают по формуле: |
|
|
|
|
К |
|
ТР |
, |
(11) |
В |
|
|||
|
Т |
|
||
|
|
|
где ТР – фактическая продолжительность работы машины за смену за вычетом простоев машины на профилактику, заправку, техническое обслуживание, перерывы в работе, предусмотренные для водителя, ч;
ТН – нормативная продолжительность рабочей смены, ч.
124
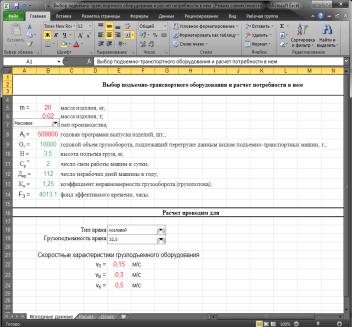
Выполнение работы:
1.По выданному преподавателем заданию выполнить расчет количества грузоподъемного оборудования с учетом заданной годовой программы выпуска изделия.
2.Расчет проводится при помощи специализированного ПО в следующем порядке:
– вводятся исходные данные (рис. 59);
Рис. 59. Ввод исходных данных
– результаты расчета представлены на листе «Отчет», по которым наглядно видно, какой тип грузоподъемного оборудования подойдет для данного типа производства (рис. 60).
125
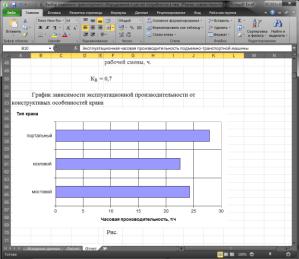
Рис. 60. График загрузки грузоподъемного оборудования
3. В отчете представить краткий конспект по теоретической части и результаты расчетов количества грузоподъемного оборудования.
Лабораторная работа № 11.
Средства механизации технологических процессов машиностроительных производств
(4 часа)
Цель работы: изучить состав, назначение и конструкцию основных устройств, позволяющие упростить перемещение заготовки по позициям технологического процесса.
Технические средства и программное обеспечение:
1.IBM-PC или совместимый компьютер;
2.Операционная система Microsoft Windows;
126
3. Пакет офисных программ Microsoft Office.
Средства для эскизирования:
1.Линейка инструментальная;
2.Штангенциркуль;
3.Карандаш.
Теоретические сведения:
В качестве транспортных средств (рис. 61) в условиях современных машиностроительных предприятий применяют:
1.Автоматизированные тележки;
2.Штабелеры;
3.Конвейеры;
4.Кантователи;
5.Поворотные столы;
6.Роботы;
7.Конвейеры для удаления стружки и т.д.
Горизонтально-замкнутые (напольные) конвейеры
применяют для транспортирования грузов в условиях серийного и массового поточного производства.
Конвейер (рис. 62) имеет большое количество соединенных между собой тележек 1, движущихся по рельсам 2 при помощи тяговой замкнутой цепи. Пуск конвейера осуществляется от электродвигателя приводной станции 10. Изготовленные на машинах формы 6 со сборочных рольгангов 7 передаются в заливочное отделение. Заливка форм расплавом производится со специального движущегося вертикальнозамкнутого конвейера – платформы 3 разливочным ковшом 4, который доставляется из плавильного отделения на подвижной тележке по монорельсу 5.
127
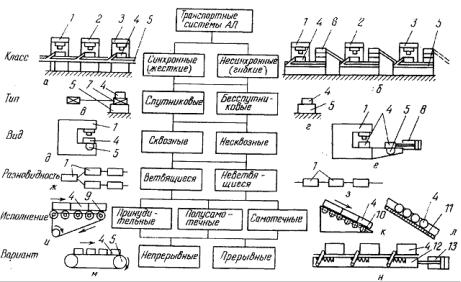
Рис. 61. Классификация транспортных систем
[https://im0-tub-ru.yandex.net/i?id=88e95e1ecab 01dda9806b86c6c14e3e8-sr&n=13&exp=1]
Залитые расплавом формы поступают под охладительный кожух 9, а после остывания в них отливок – в выбивное отделение. После выбивки форм на механической решетке 8 отливки транспортируются в очистное отделение, выбитая из опок смесь – в смесеприготовительное отделение, а пустые опоки – на участок формовки.
Таким образом, конвейер дает возможность создать в литейном цехе единый последовательный процесс получения отливок. Скорость конвейеров колеблется в пределах от 1 да
7,5 м/мин.
128
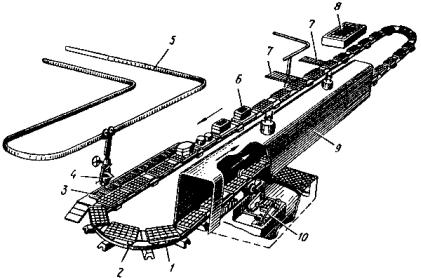
Рис. 62. Напольный конвейер:
1 – тележки, 2 – рельсовый путь, 3 – заливочная подвижная платформа, 4 – разливочный ковш, 5 – монорельс,
6 – литейные формы, 7 – рольганги формовочного участка, 8 – механическая выбивная решетка, 9 – охладительный кожух, 10 – приводная станция конвейера
[http://www.stroitelstvo-new.ru/formovka/img/105.png]
Шагающие конвейеры применяют для транспортировки форм с участка формовки на заливку и выбивку вместо напольных горизонтально-замкнутых конвейеров, занимающих много места. Линия шагающего конвейера (рис. 63) состоит из двух неподвижных наружных швеллеров 1, закрепленных на чугунных тумбах 7, и двух внутренних подвижных швеллеров, связанных в единую раму 2. Последняя опирается на ролики механизма подъема и направляется боковыми роликами. С помощью рычажно-эксцентрикового механизма 6 и пневматических цилиндров 5 рама может подниматься или опускаться на высоту, равную 20 мм.
129