
Методическое пособие 747
.pdf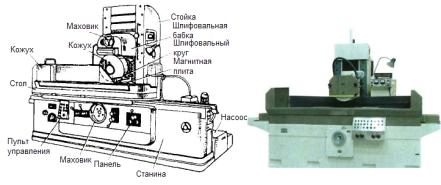
поддержания бортштанги, обеспечивающий необходимую жесткость в процессе резания,
–поворотный стол, расположенный между передней и задней стойками, перемещающийся по направляющим станины;
–электропривод, обеспечивающий главное движение и подачу; при расточке коротких отверстий подача сообщается шпинделю;
При обработке длинных и соосных отверстий с использованием бортштанги подача в продольном направлении сообщается столу, шпиндель может перемещаться в осевом направлении или вертикально вместе со шпиндельной бабкой по направляющим стойки.
Шлифовальные доводочные станки.
Шлифование – один из прогрессивных методов обработки металлов резанием. При шлифовании припуск на обработку срезают абразивными инструментами – шлифовальными кругами. Устройство и основные узлы шлифовального станка показаны на рис. 35.
Рис. 35. Основные узлы шлифовального станка
Шлифовальный круг представляет собой пористое тело, состоящее из большого числа абразивных зерен, скрепленных между собой связкой. Между зернами круга и связкой распо-
90
ложены поры. Материалы высокой твердости, из которых образованы зерна шлифовального круга, называют абразивными. Шлифование состоит в том, что шлифовальный круг, вращаясь вокруг своей оси, снимает тонкий слой металла (стружку) вершинами абразивных зерен, расположенных на режущих поверхностях шлифовального круга (периферия круга). Число абразивных зерен, расположенных на периферии круга, очень велико; у кругов средних размеров оно достигает десятков и сотен тысяч штук.
Таким образом, при шлифовании стружка снимается огромным числом беспорядочно расположенных режущих зерен неправильной формы, что приводит к очень сильному измельчению стружки и большому расходу энергии. Режущая поверхность шлифовального круга состоит из множества абразивных зерен, расположенных на его поверхности на некотором расстоянии друг от друга и выступающих на различную высоту.
Шлифовальные станки предназначены для затачивания различного инструмента, резания материалов, чернового шлифования и отделочных операций при обработке металлов. Обрабатывая камень, стекло, бетон, древесину, пластмассу, без них тоже не обойтись.
Шлифовальные материалы – это шлифовальные, полировальные и доводочные пасты, порошки, шлифовальные шкурки на бумажной и тканевой основе. Шлифовальные инструменты – это шлифовальные, полировочные и отрезные круги, сегменты, бруски.
Комбинированные станки – это многофункциональ-
ные агрегаты с возможностью одновременного выполнения нескольких функций обработки и отделки заготовки. Различают комбинированные станки для работы по дереву и для работы с металлом. Эксплуатация станков одного вида на заготовках из материалов, предназначенных для обработки на станках другого вида, строго запрещена.
Устройство и основные узлы станка показаны на рис. 36.
91
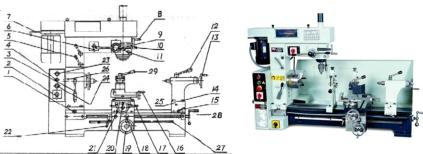
Рис. 36. Устройство комбинированных станков
1) |
Включающий рычаг про- |
16) |
Маховичок ручной пода- |
дольной подачи; |
чи резцовой каретки; |
||
2) |
Включатель токарного |
17) |
Замок поперечного суп- |
станка; |
порта; |
||
3) |
Рычаг передач; |
18) |
Включатель потолочной |
|
|
поперечной подачи; |
|
4) |
Кнопка «старт»; |
19) |
Маховичок ручной про- |
|
|
дольной подачи; |
|
5) |
Рукоятка стягивания |
20) |
Маховичок ручной попе- |
шпинделя фрезерного обору- |
речной подачи; |
||
дования; |
|
|
|
6) |
Включатель фрезерного |
21) |
Замок суппорта; |
оборудования |
|
|
|
7) |
Рычаг натяжения клино- |
22) |
Рычаг включения меха- |
видного ремня фрезерного |
нической подачи; |
||
оборудования; |
|
|
|
8) |
Рукоятка привода микро- |
23) |
Сигнальная контрольная |
подачи вертикального шпин- |
лампа напряжения; |
||
деля; |
|
|
|
9) |
Арретированный рычаг |
24) |
Кнопка аварийного вы- |
микроподачи вертикального |
ключения станка; |
||
шпинделя; |
|
|
|
10) |
Рычаг подачи вертикаль- |
25) |
Винт для несоосности |
ного шпинделя; |
задней бабки; |
92
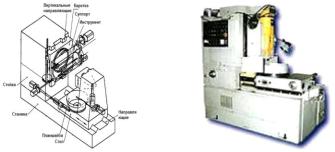
11) |
Замок рычага подачи вер- |
26) |
Замок натяжного ремен- |
тикального шпинделя; |
ного шкива горизонтального |
||
|
|
шпинделя; |
|
12) |
Замок пиноли; |
27) |
Гребенка токарного стан- |
|
|
ка; |
|
13) |
Маховичок ручной пода- |
28) |
Маховичок ручной про- |
чи пиноли; |
дольной подачи. |
14)4 шт. арретированных винтов несоосной задней бабки;
15)Замок задней бабки на станине;
Зубо- и резьбообрабатывающие станки. Зубонарезной станок - предназначен для нарезания и отделки зубьев колес различных передач. По виду обработки и инструмента различают следующие зубообрабатывающие станки: зубофрезерные, зубострогальные, зубопротяжные, зубошлифовальные и др. Устройство и основные узлы зубообрабатывающего станка показаны на рис. 37.
Рис. 37. Основные узлы зубо- и резьбообрабатывающих станков
По назначению станки бывают: для обработки цилиндрических колес с прямыми и косыми зубьями, червячных колес, шевронных колес, зубчатых реек, конических прямозубых колес, с криволинейными зубьями.
93
По степени шероховатости обработанной поверхности выделяют станки: для предварительного нарезания зубьев, для чистовой обработки, для отделочной обработки поверхности зубьев.
Существуют два метода нарезания зубчатых колес, метод обката и метод следа (копирования).
При методе копирования используется инструмент, режущая кромка которого совпадает по форме с профилем впадины зубчатого венца. Модульная фреза 7 перемещается вдоль впадины цилиндрического колеса 2, в каждый момент времени оставляя отпечаток своей формы.
После обработки одной впадины заготовку поворачивают на окружной шаг (движение деления) и обрабатывают следующую впадину.
Данный метод имеет свои недостатки: профиль зуба зависит от модуля и числа зубьев колеса. Для точной обработки каждого колеса нужна своя фреза. Поэтому необходим большой набор сложных фрез. Практически ограничиваются набором из 8 или 15 фрез для каждого модуля.
При этом одной фрезой нарезают колеса с различным числом зубьев (в некотором интервале). Наименьшее из колес интервала получается с правильным профилем, другие — не точно. Достоинство метода копирования — простота оборудования.
Фрезерный станок – станок, предназначенный для обработки металлов при помощи фрезы. Фрезерные станки способны обрабатывать как внутренние, так и внешние плоские и фасонные поверхности, пазы и переходы, а так же тела вращения и зубчатые колеса. Устройство и основные узлы фрезерного станка показаны на рис. 38.
94
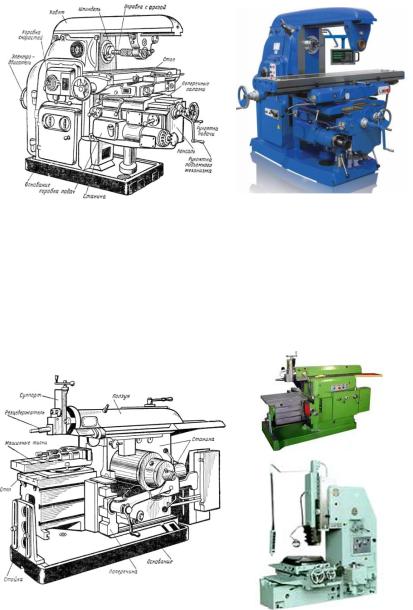
Рис. 38. Основные узлы фрезерного станка
Строгальные, долбежные и протяжные станки.
На строгальном станке по металлу проводится один из этапов обработки заготовки, как правило, следующий после фуговального станка.
Устройство и основные узлы строгального станка показаны на рис. 39.
Рис. 39. Основные узлы строгального и долбежного станков
95
Металлорежущие и металлообрабатывающие станки различных видов используются на многих производственных линиях. Их основная функция заключается в придании необходимой формы конкретной детали. И возможности данного оборудования достаточно разнообразны, что значительно расширяет сферу применения строгальных станков в производстве.
Они отличаются между собой по характеру обрабатывающего движения. Основному резцу поперечно-строгаль- ного станка, который закрепляется в суппорте, сообщается прямолинейное возвратно-поступательное движение. У продольно строгального станка по металлу движется сам стол, на котором закрепляется изделие. Фактически процесс резания можно разделить на два шага – рабочий и холостой ход. Сначала резец продвигается вперёд, а затем возвращается в исходное положение.
Скорость движения остаётся постоянной, если используется гидравлический привод. На тех моделях, где установлен кулисно-кривошипный привод скорость резца меняется от нуля до максимальной.
Строгальный станок по металлу является одним из наиболее распространённых видов оборудование в своей области. Он применяется при обработке фасонных и плоских поверхностей. Продольно-строгальные станки предназначаются для обработки небольших заготовок.
Особенность его конструкции заключается в обеспечении максимального удобства при работе. Поперечнострогальные станки в свою очередь активно используются работы с деталями средних размеров. Другими их функциями являются прорезание отверстий, пазов, каналов и выемок.
Строгальные станки по металлу применяются для обработки мелких и относительно крупных заготовок, также они подходят для работы с длинными и широкими поверхностями.
96
Как правило, подобное оборудование больше востребовано для небольшого производства. На крупных предприятиях, где налажено крупносерийное производство, используются профессиональные фрезерные, протяжные и шлифовальные станки.
Долбежный станок по металлу позволяет обрабатывать цилиндрические и конические поверхности для выполнения шлицев, канавок, шпоночных пазов, поднутрений и т.д. При этом конструкция станка позволяет обрабатывать как наклонные, так и прямые, внутренние и наружные поверхностей, тип профиля канавки или реза может быть любым.
Устройство и основные узлы долбежного станка показаны на рис. 39.
Такое оборудование незаменимо на мелкосерийном и единичном производстве мебели, окон, деталей судов вагонов, лыж и прочей продукции. Использование станка для долбления на производстве позволяет получить следующие преимущества.
Включив его в перечень парка оборудования, предприятие экономит финансовые средства на услугах сторонних организаций. Процесс эксплуатации станка достаточно удобен даже при обработке наклонных плоскостей.
Что касается особенностей устройства долбежного станка по металлу, то в перечень его элементов входят станина, привод рабочий стол, долбяк и кулисный механизм. Также в конструкции присутствует коробка скоростей, коробка подач
иэлектрооборудование и коробка подач.
Входе работы оператор регулирует угол наклона долбяка, а также такие параметры как круговая, поперечная и продольная подача стола. Рабочая зона должная быть оптимальным образом освещена, а потому в перечень элементов такого оборудования часто входит источник света.
Долбежный станок должен иметь высокую степень устойчивости. Этот вопрос решается установкой массивного чугунного основания, которое обладает приличными габари-
97
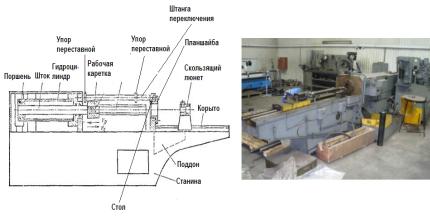
тами, а значит, имеет большой вес. Этот элемент механизма обеспечивает точность обработки деталей.
В зависимости от требуемой производительности станок может быть рассчитан на обработку как одной, так и нескольких деталей одновременно. Это позволяет при необходимости гарантировать высокую производительность без особенного увеличения парка оборудования на предприятии. Как показывает практика, долбежный станок незаменим в судостроении, строительстве вертолетов, тяжелой боевой техники, тракторов, а также в сервисных мастерских и мелкосерийном производстве.
Станок протяжной – это устройство, предназначенное для обработки металлических поверхностей с разными видами профиля. Существует два вида станков: стандартные и специальные (обрабатывающие наружные и внутренние поверхности металлоконструкций).
Устройство и основные узлы протяжного станка показаны на рис. 40.
Рис. 40. Основные узлы протяжного станка
Данный вид станков чаще всего используется для крупномасштабного производства изделий из металла. Качество
98
изделий «на выходе» зависит от точности и мощности оборудования, так как протяжка металла проходит в условиях жестких нагрузок (изгибы, растяжение и сжатие металла). Прежде, чем использовать станок, металл обрабатывают, развертывают, сверлят, создавая максимально точные заготовки.
Станок протяжной используется для выполнения следующих операций:
–калибровка отверстия (фигурного, многогранного, цилиндрического и пр.);
–коррекция наружного профиля сложной конструкции;
–нарезка канавки шпоночной и шлица;
–обработка посадочной поверхности лопатки для турбины авиационного двигателя;
–обработка и корректировка отверстия для огнестрельного оружия нарезного типа (ствол пушки, пулемета, пистолетный ствол).
В мелкомасштабном производстве оборудование используется для создания отверстий в шестеренках и втулках, шпоночных и шлицевых канавок. Основными характеристиками протяжных станков являются:
–тяговая сила (максимальный показатель – 1 МН);
–скорость протягивания (от 1,5 до 15 м/мин., в зависимости от назначения станка);
–длина хода каретки (максимальный показатель – 2
метра);
–конструкция привода (гидравлическая или электромеханическая);
–точность работы (от 1 до 10 класса).
Тяговая сила станка зависит от каретки. Для станков общего назначения характерна скорость протягивания от 15 до 20 м/мин. и привод, основанный на гидравлике, а для станков непрерывного действия скорость протягивания от 1,5 до 15 м/мин. и электромеханический привод.
В массовом производстве используются станки 1-2 класса, не допускающие погрешностей.
99