
Методическое пособие 747
.pdf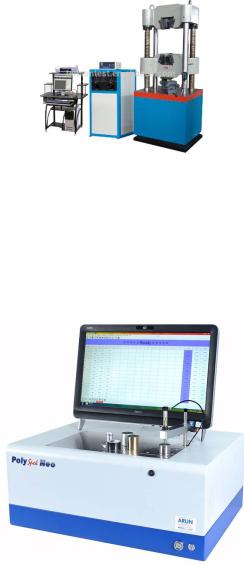
Универсальная гидравлическая разрывная машина
Рис. 7. Гидравлическая разрывная машина
[https://sc01.alicdn.com/kf/HTB1duwUIXXXXXXpXFXXq6xXFXX Xl/Tenson-WAW-Series-Computerized-Electro-hydraulic- Servo.jpg]
Компактный стационарный многоосновный оптикоэмиссионный анализатор химического состава металлов и сплавов
Рис. 8. Анализатор химического состава металлов и сплавов [http://nesarainstruments.in/assets/gallery/e1.jpg]
20
5.Изготовление стержней.
6.Выбивка.
7.Очистка.
Показатели использования оборотных фондов на предприятии
Эффективность производственных процессов, в частности литья, может быть определена с помощью следующих основных показателей: коэффициент использования, коэффициент раскроя, выход продукта (полуфабриката), коэффициент извлечения продукта из исходного сырья.
Коэффициент использования характеризует степень использования сырья и материалов и определяется отношением полезного расхода (массы, теоретического расхода) к норме расхода материалов, установленной на изготовление единицы продукции (работы).
Коэффициент раскроя – показатель, характеризующий степень полезного использования листовых, полосных, рулонных материалов главным образом в заготовительном производстве; определяется отношением массы (площади, длины, объема) производственных заготовок к массе (площади, длине, объему) исходной заготовки раскраиваемого материала.
Расходный коэффициент – показатель, обратный ко-
эффициенту использования и коэффициенту раскроя. Он определяется как отношение нормы расхода материальных ресурсов, установленной на производство единицы продукции (работы), к полезному их расходу.
Выход продукта (полуфабриката) выражает отноше-
ние количества произведенного продукта (полуфабриката) к количеству фактически израсходованного сырья. Например, выход ткани из пряжи, сахара из сахарной свеклы, растительного масла из маслосемян, пиломатериалов из древесины и др.
21
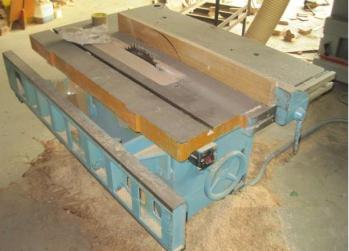
Коэффициент извлечения продукта из исходного сы-
рья характеризует степень использования полезного вещества, содержащегося в соответствующем виде исходного сырья. Он определяется отношением количества извлеченного полезного вещества из исходного сырья к общему его количеству, содержащемуся в этом сырье.
Важнейшим обобщающим показателем уровня использования всех материальных ресурсов на предприятии являет-
ся материалоемкость продукции; обратный показатель ма-
териалоемкости продукции – материалоотдача.
Пример
На машиностроительном заводе выпускались станки мощностью 200 кВт, а их чистый вес составлял 4,5 т (чистый вес базовых элементов конструкции, например станины рис. 9). Черновой вес металла на изготовление одного станка —
6,0 т.
Рис. 9. Литая станина (основание) станка
[http://drovosek2008.ru/assets/images/part_old/a21c14f6d061176 178b5966a2993cf12.jpg]
22
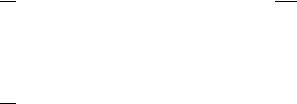
После совершенствования конструкции станка и внедрения новой техники в производство его мощность увеличилась до 250 кВт при сохранении прежнего чистого веса, а черновой расход металла на один станок составил 5 т.
Определите показатели использования металла до и после совершенствования конструкции и внедрения новой техники.
Решение
1. Определяем показатели использования металла до совершенствования конструкции станка и внедрения новой техники:
; |
|
;КИМТ |
|
кг кВт
2. Определяем показатели использования металла после совершенствования конструкции станка и внедрения новой техники:
; |
|
;КИМТ |
|
кг кВт |
|
|
Таким образом, общая экономия металла на 1 кВт со-
ставила 9,3 кг (29,3-20).
Выполнение работы:
1.Ознакомиться с видами машиностроительных предприятий и основным технологическим оборудованием литейных цехов.
2.По выданному преподавателем варианту и данным таблицы №1 рассчитать показатели эффективности использования металла в конструкции станка до и после модернизации;
3.Сделать вывод об эффективности проведенной модернизации базовых деталей станка.
23
Таблица 1
Исходные данные для расчета
|
|
до модернизации |
после модернизации |
|||||
|
Модель |
мощ- |
чис- |
чер- |
мощ |
чис- |
чер- |
|
№ |
тый |
ност |
тый |
новой |
||||
станка |
ность, |
новой |
||||||
|
вес, |
ь, |
вес, |
вес, |
||||
|
|
кВт |
вес, кг |
|||||
|
|
кг |
кВт |
кг |
кг |
|||
|
|
|
|
|||||
1 |
7Д430 |
11 |
51495 |
60050 |
15 |
60000 |
65555 |
|
2 |
53А50 |
12 |
9650 |
11000 |
20 |
9000 |
10350 |
|
3 |
2А55 |
8,5 |
4100 |
5000 |
15 |
4700 |
5600 |
|
4 |
2К52 |
1,5 |
1250 |
1800 |
5 |
2300 |
2850 |
|
5 |
2Н55 |
8,5 |
4100 |
5000 |
15 |
4700 |
5600 |
|
6 |
НС16 |
0,75 |
100 |
150 |
1,5 |
150 |
200 |
|
7 |
1Б140 |
7,25 |
2300 |
2700 |
8 |
2350 |
2900 |
|
8 |
1Б240Б |
24,9 |
12000 |
14000 |
30 |
12200 |
14200 |
|
9 |
1К62 |
11,2 |
2140 |
2550 |
20 |
2410 |
2850 |
|
10 |
1Н65 |
23,62 |
12800 |
15000 |
30 |
14700 |
17000 |
|
11 |
1616П |
8,5 |
2000 |
3000 |
15 |
3000 |
3300 |
|
12 |
Korvet400 |
0,4 |
37 |
60 |
0,75 |
50 |
70 |
|
13 |
Korvet402 |
0,75 |
105 |
130 |
1 |
120 |
150 |
|
14 |
Korvet403 |
0,75 |
120 |
170 |
1 |
140 |
200 |
|
15 |
Korvet407 |
0,75 |
160 |
230 |
1 |
185 |
250 |
|
16 |
ИЖ250 |
3 |
1180 |
1350 |
3 |
1280 |
1450 |
|
17 |
МК6046 |
11 |
3005 |
3800 |
15 |
3680 |
4500 |
|
18 |
ТВ-320 |
2,8 |
980 |
1350 |
5 |
1350 |
1700 |
|
19 |
5К32 |
7,5 |
7200 |
8500 |
9 |
7800 |
9300 |
|
20 |
6Е63 |
3,75 |
1340 |
1670 |
5 |
1430 |
1800 |
|
21 |
6А23 |
13 |
10500 |
12500 |
17 |
11500 |
14000 |
|
22 |
6В75 |
1,7 |
855 |
1250 |
3 |
1100 |
1500 |
|
23 |
6Е80Ш |
2,2 |
950 |
1400 |
5 |
1100 |
1600 |
24
Лабораторная работа № 3. Машиностроительные предприятия. Кузнечный цех
(4 часа)
Цель работы: ознакомиться с основным технологическим оборудованием кузнечного цеха. Подобрать вид кузнеч- но-прессовой машины для осуществления технологической операции.
Технические средства и программное обеспечение:
1.IBM-PC или совместимый компьютер;
2.Операционная система Microsoft Windows;
3.Пакет офисных программ Microsoft Office.
Средства для эскизирования:
1. Линейка инструментальная;
3.Штангенциркуль;
4.Карандаш.
Теоретические сведения:
Кузнечные цехи (рис. 11) служат для изготовления крупных и мелких поковок, термические – для термообработки деталей и инструментов. Оборудование кузнечных цехов – молоты, прессы, ковочные машины, нагревательные печи, горны для ручной ковки. Только разогретый металл становится пластичным и легко поддается деформации. Для нагрева металла издавна пользуют специальное нагревательное оборудование – кузнечный горн (рис. 10).
Оборудование термических цехов – нагревательные печи и закалочные ванны.
25
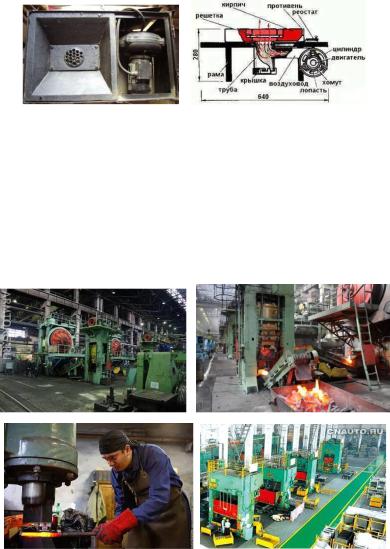
Рис. 10. Кузнечный горн
[https://a.d-cd.net/a1b0ee6s-960.jpg]
Кузнечный цех состоит из следующих отделений: молотового, прессового, болто-гаечного, рессорного и пружинного, заготовительного и из складов для железа и штампов. Большинство кузниц оборудовано паровыми молотами в 2 - 3 т, и лишь отдельные кузницы имеют молоты с большим тоннажем.
Рис. 11. Цех кузнечный
[http://paotmz.ru/content/files/ext_catalog2/production_big_1455 706522/Kuznechnopressovyj_cex_sm_880x390__0_0_d41d8cd98f 00b204e9800998ecf8427e_25.jpg]
26
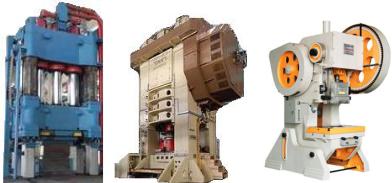
Кроме молотов имеются ковочные машины Аякс, Газенклевер, прессы Венсана, гайкоделительные станки. В среднем кузница выпускает ок. Из всей поковки в среднем 50% проходит через молоты и прессы, 15% – через ковочные машины, 15% – через бульдозеры и 20% изготовляется вручную.
Разновидности кузнечного оборудования
Наиболее часто в качестве основного технологического оборудования применяются следующие виды кузнечнопрессового оборудования:
1. Гидравлические и кривошипные прессы - предназначены для ковки, штамповки, гибки, резки и формовки как фасонного в горячем состоянии, так и листового материала как индивидуально, так и в составе автоматических линий;
а |
б |
в |
Рис. 12. Основное технологическое оборудование кузнечных цехов: а) пресс гидравлический; б) КГШП; в) пресс кривошипный
[http://www.tmp-press.ru/images/857.jpg]
27
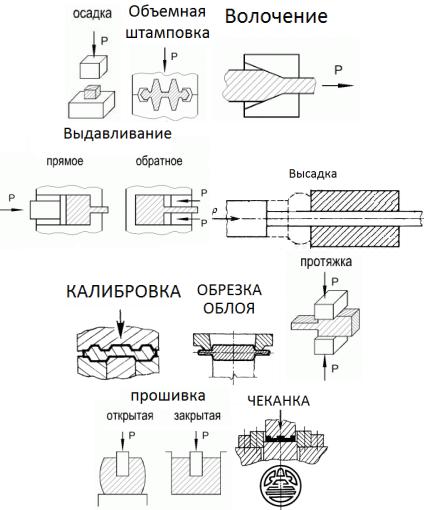
Многообразие основного технологического оборудования кузнечных цехов вызвано широким спектром технологических операций обработки металлов давлением (рис. 13).
Рис. 13. Основные технологические операции обработки металлов давлением [https://im0-tub-ru.yandex.net/i? id=91274d873d9500978d6fa7900597552a&n=13&exp=1]
28
Далее рассмотрим назначение основных технологических операций.
Осадкой называют формоизменяющую технологическую операцию, при помощи которой уменьшают высоту исходной заготовки с одновременным увеличением площади ее поперечного сечения.
Калибровка – повышение точности размеров штампованной заготовки и уменьшении шероховатости ее поверхности.
Выдавливание – штамповка заготовки вытеснением металла исходной заготовки в полость и отверстие ручья.
Редуцирование – уменьшение площади поперечного сечения заготовки при протягивании ее через калибрующую матрицу усилием, направленным вдоль оси заготовки.
Чеканка – образование на поверхности заготовки рельефных изображений за счет перераспределения металла.
Штамповка в открытых штампах характеризуется переменным зазором между подвижной и неподвижной частями штампа.
Штамповка в закрытых штампах характеризуется тем, что полость штампа в процессе деформирования остается закрытой.
2. Оборудование для формирования проката – ковочные вальцы (рис. 14) – предназначено для получения из прута фигур или заготовок нестандартной формы методом прокатки между несколькими вальцами.
29