
Методическое пособие 747
.pdf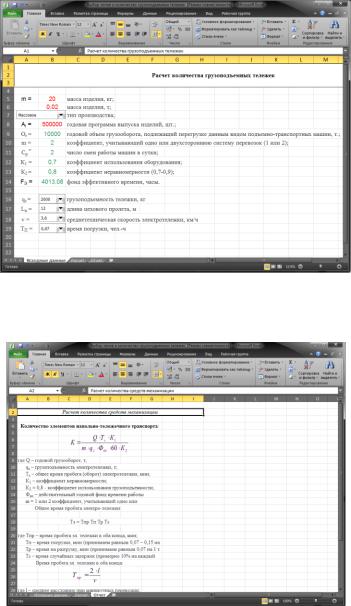
Рис. 69. Ввод исходных данных Результаты расчетов (рис. 70-71).
Рис. 70. Оформление отчета
140
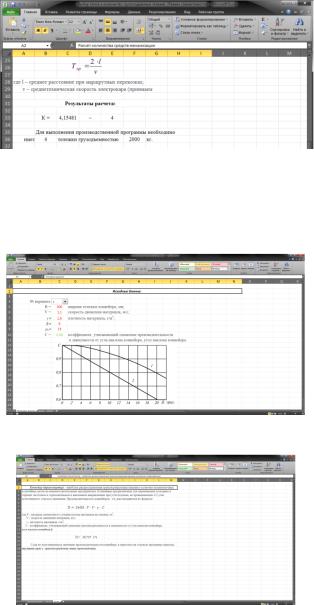
Рис. 71. Результат расчета
3. Производительность конвейера рассчитывается в специализированной программе при следующих исходных данных (рис. 72, 73).
Рис. 72. Исходные данные
Рис. 73. Оформление результатов
141
Лабораторная работа № 12. Оборудование сборочных цехов
(4 часа)
Цель работы: ознакомиться с производственными приспособлениями, средствами механизации и автоматизации современных сборочных производств.
Технические средства и программное обеспечение:
1.IBM-PC или совместимый компьютер;
2.Операционная система Microsoft Windows;
3.Пакет офисных программ Microsoft Office.
Средства для эскизирования:
1.Линейка инструментальная;
2.Штангенциркуль;
3.Карандаш.
Теоретические сведения:
Соединение деталей в сборочные единицы (механизмы, узлы, машины и т. д.) называется сборкой. Сборка предусматривает не только соединение деталей, но также и подгонку их перед сборкой, регулировку всей сборочной единицы. Технологический процесс сборки состоит из последовательно выполняемых операций. При этом деталь, с которой начинают сборку, присоединяя к ней последовательно остальные детали, называют базовой.
Операция сборки – это часть технологического, процесса сборки, выполняемая на одном рабочем месте (одним или несколькими исполнителями). Она, в свою очередь, разделяется на установки и переходы.
Установка при сборке – часть операции, которую выполняют при неизменном положении сборочной единицы.
142
Переход – часть сборочной операции, выполняемая одним и тем же инструментом при неизменном положении сборочной единицы.
Оборудование сборочных цехов условно может быть разделено на две группы: технологическое, предназначенное непосредственно для выполнения сборочных соединений, и вспомогательное, назначение которого – механизировать подъёмно-транспортные работы.
В состав технологического оборудования входят:
1)ручной слесарно-сборочный инструмент: ключи гаечные, рожковые, торцовые, разводные; отвёртки шлицевые, крестовые; молотки стальные, медные; напильники плоские, квадратные, трёхгранные, круглые; зубила; кернеры; кусачки торцовые; плоскогубцы комбинированные, круглогубцы;
2)ручные машины для слесарно-пригоночных и сборочных работ: сверлильные ручные машины (электрические, пневматические); шлифовальные машинки (электрические, пневматические); пневматические клепальные молотки; электрические и пневматические гайковерты и винтоверты;
3)приспособления: универсальные (винтовые или пневматические тиски, струбцины, съёмники, домкраты, захваты) и специальные (установочно-зажимные стенды, стапели, кондукторы);
4)прессы для запрессовки, напрессовки и клёпки: ручные винтовые и реечные, пневматические прямого и рычажного действия и гидравлические для больших усилий; переносные пресс-скобы;
5)оборудование для балансировки (статической, динамической);
6)оборудование для мойки, нагрева, клеймения и заправки смазками (промывочно-сушильные агрегаты, электропечи с масляными ваннами, индукционные печи, дозирующие машины);
143
7)оборудование для выполнения сварочных работ: сварочные трансформаторы, установки для лазерной сварки, агрегаты для газовой сварки);
8)оборудование для окраски изделий: пульверизаторы, окрасочные камеры, сушильные агрегаты.
В состав транспортного оборудования сборочных цехов входят различного рода устройства для перемещения собираемых изделий:
1)конвейеры подвесные грузонесущие и грузоведущие; для них не требуется дополнительной производственной площади, они обладают значительной протяжённостью (используются для транспортировки грузов между цехами);
2)напольные конвейеры: ленточные (для сборки лёгких
исредних изделий; резиновая лента;
3)грузоведущие напольные конвейеры: тележечные конвейеры наиболее распространены, на тележках устанавливаются собираемые изделия, скорость 0,25…6 м/мин, ширина 200…1600 мм, грузоподъёмность 10…8000 кг; рамные шагающие конвейеры для сборки станков; станки располагают в цехе на полу, на плитах; домкраты поднимают раму с изделием и толкают на следующую позицию (грузоподъёмность до
5 т);
4)мостовые краны применяют при массе изделия более 5 т, их грузоподъёмность от 5 до 50 т и больше (до 320 т); расстояние между подкрановыми путями 10,5…31,5 м; расстояние перемещения 50 м;
5)для перемещения изделий до 5 т часто используют мостовые опорные однобалочные краны, так называемые кран-балки, оснащённые электроталями грузоподъёмностью 0,5…5 т; расстояние перемещения груза 30…50 м;
6)консольно-поворотные краны устанавливают стационарно на рабочем месте при частых операциях подъёмаустановки; вылет стрелы – 3…6 м; грузоподъёмность –
0,25…3 т;
144
7) электротали применяются либо в виде самостоятельного грузоподъёмного устройства, перемещающегося на монорельсе, либо в составе кранов; их грузоподъёмность 0,25…5 т, высота подъёма 6…18 м.
Лако-красочные работы
Все поверхности готового изделия обычно покрывают специальными покрытиями, которые подразделяются по назначению: на защитные, защитно-декоративные и специальные.
Защитные покрытия предназначены для защиты деталей от коррозии; защитно-декоративные помимо защиты от коррозии придают изделиям приятный вид; специальные – предохраняют от воздействия каких-то специфических сред (кислоты, например).
На характер покрытия решающим образом влияют условия, в которых работает машина или отдельные её детали:
–лёгкие условия характеризуются работой изделия в закрытых помещениях при нормальных климатических условиях и влажности;
–средние условия: в окружающей среде небольшое количество газов, влажность воздуха периодически достигает 98 %; температура может меняться от -50 до +60 °С; эти условия характерны для машин, работающих в негерметизированной, но влагозащищённой обстановке (под крышей);
–жёсткие условия: среда загрязнена газами, возможен снег, дождь, влажность воздуха доходит до 98 %; температура может меняться от -70 до +70 °С. Условия работы таких машин – на открытом воздухе;
–морские условия: наружные детали машин и механизмов подвергаются воздействию морской воды, брызг, а внутренние находятся в атмосфере морских испарений;
–тропические условия: постоянное воздействие атмосферы влажного тропического климата, солнечных лучей,
145
осадков, повышенной температуры (до +60 °С), высокой влажности (до 90 %).
Воздействие внешней среды на детали машин проявляется в коррозии.
Коррозия – разрушение металлических деталей и изделий под влиянием химического и электрохимического взаимодействия с внешней средой. Интенсивность коррозии зависит от материала детали, окружающей среды, а также от шероховатости поверхности и остаточных напряжений.
Потери от коррозии во всём мире составляют до 1/3 всего количества добываемого металла. Существуют следующие способы борьбы с коррозией:
–изготовление изделий из инертных материалов (нержавеющие стали, алюминиевые бронзы, пластмассы);
–нанесение на поверхность металла лакокрасочных покрытий;
–нанесение на поверхность слоя жира, масла, тавота;
–создание на поверхности детали оксидных плёнок (воронение стали, чернение меди и т.п.);
–покрытие одного металла слоем другого, стойкого к коррозии.
Первый путь – самый эффективный, но часто и самый дорогой.
Лакокрасочные покрытия предохраняют металл от контакта с окружающей средой. Чаще всего применяют масляные краски – смесь олифы с минеральными красками. Первый слой краски называется грунтовкой, поверх которого наносится второй слой, называемый декоративным.
Число слоёв краски может быть 3-4. Достоинство лакокрасочных покрытий заключается в дешевизне и лёгкости их восстановления; недостатки – малая стойкость, прочность и некоторая пористость.
Жировые покрытия хорошо защищают поверхности металла от воздействия влажных и газообразных сред, но они
146
легко нарушаются, а потому чаще всего применяются для сохранения неработающих машин (консервация).
Оксидные покрытия представляют собой искусственно создаваемую плёнку окисла металла, надёжно изолирующую основной металл от окружающей среды.
На некоторых металлах (например, алюминий) эта плёнка образуется естественным путём, на других она недостаточно плотная и прочная. Путём интенсивного окисления создают прочные плёнки (воронение стали, чернение меди). Нанесение жира и технических масел повышает коррозионную стойкость, особенно пористых покрытий.
Гальванопокрытия бывают двух типов: анодное, защищающее металл не только механически, но и электрохимически (при образовании микрогальванических пар разрушающимся элементом – катодом будет металл покрытия); и катодное, предохраняющее металл лишь механически. Это такие известные способы, как никелирование, хромирование, анодирование и др.
Существует несколько способов нанесения металлопокрытий. При способе горячего металлопокрытия листы основного металла погружаются в ванну с расплавленным ме- таллом–покрытием, в результате чего расплавленный металл тонкой плёнкой осаждается на поверхности изделия. Основное преимущество этого метода – быстрота процесса. Недостаток – большой расход металлического покрытия.
Наибольшее распространение получил метод гальванопокрытия путём электролитического осаждения металла в гальванических ваннах.
Пример определения последовательности сборочных операций
Даны сборочные чертежи изделий (рис. 74, 75).
147
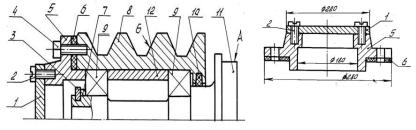
|
Рис. 75. Изделие фланец |
|
1 – Крышка; 2 – Винт; |
Рис. 74. Сборочная единица |
3 – Фланец; |
«Ступица» |
4 – Прокладка |
Для данной сборочной единицы последовательность технологических операций будет следующей (табл. 17).
|
|
|
Таблица 17 |
№ |
Наименование |
|
Содержание операции и |
операции |
операции |
|
переходов |
005 |
Сборка фланца |
1. |
Закрепить фланец 5 в |
|
|
приспособлении |
|
|
|
2. |
Установить крышку |
|
|
3. |
Закрепить крышку |
|
|
винтами 2 |
|
|
|
4. |
Установить прокладку 6 |
010 |
Установка |
5. |
Установить фланец |
|
фланца |
6. |
Закрепить фланец винтами |
015 |
Контрольная |
7. |
Проверить легкость |
|
|
вращения шкива |
|
|
|
8. |
Проповерить биение |
|
|
поверхности А относительно |
|
|
|
поверхности Б |
|
|
Выполнение работы: |
По выданному преподавателем варианту определить последовательность сборочных операций в соответствии с производственной программой.
148
РАЗДЕЛ 4. ОСНОВЫ ПРОЕКТИРОВАНИЯ ЭНЕРГЕТИЧЕСКОГО ХОЗЯЙСТВА МАШИНОСТРОИТЕЛЬНОГО ПРЕДПРИЯТИЯ
Лабораторная работа № 13.
Расчет годового потребления электроэнергии
(4 часа)
Цель работы: ознакомиться с методикой расчета количества годового потребления электроэнергии на механообрабатывающем участке.
Технические средства и программное обеспечение:
1.IBM-PC или совместимый компьютер;
2.Операционная система Microsoft Windows;
3.Пакет офисных программ Microsoft Office;
Средства для эскизирования:
1.Линейка инструментальная;
2.Штангенциркуль;
3.Карандаш.
Теоретические сведения:
Все ресурсы современного машиностроительного предприятия подразделяются на: трудовые, финансовые, природные, материальные, энергетические и производственные.
Трудовые ресурсы – это часть населения страны, участвующая в создании валового национального продукта (ВНП) в соответствии со своим образовательным и профессиональным уровнем.
149