
Методическое пособие 483
.pdf1)с автоматической передачей деталей (изделий);
2)с механизированной передачей изделий;
3)с немеханизированной передачей изделий.
4.По способу поддержания и характеру ритма по-
точные линии бывают:
1) с регламентированным, или принудительным, ритмом. Передача осуществляется с помощью конвейера или жесткой связью оборудования. Деталь перемещается с заранее заданной скоростью;
2) со свободным ритмом. Ритм поддерживается рабочими. Чтобы рабочие не простаивали, требуются заделы.
5.По степени непрерывности поточные линии делятся
на:
1) непрерывно-поточные;
2) прерывно-поточные (прямоточные).
На непрерывно-поточной линии все операции синхронизированы (равны или кратны ритму). Все операции имеют равную производительность. Они могут иметь регламентированный или свободный ритм. Эти линии характерны для сборочных цехов, так как сборочный процесс легко расчленить на операции по времени, равные или кратные ритму, особенно при их слабой механизации.
На прямоточной поточной линии не все операции синхронизированы. Есть операции со значительными отклонениями от среднего ритма поточной линии. Загрузка оборудования и рабочих на таких линиях недостаточно равномерна. На операциях, длительность которых меньше такта, процесс производства прерывается и рабочие и оборудование могут
151
Этот вид поточных линий используется в обрабатывающих цехах, в которых из-за разнохарактерности оборудования и технологической оснастки синхронизация ограничена.
Непрерывные и прерывные поточные линии могут
|
быть одно- и многономенклатурными. |
|
6. Поточные линии бывают с конвейерами, находящи- |
|
мися в непрерывном движении и пульсирующими. Это деле- |
|
ние принято для линий конвейерного типа и определяется спо- |
|
собом движения конвейера. Причем, местом выполнения опе- |
|
рации на поточной линии может быть конвейерная лента или |
|
рабочее место. В первом случае поточная линия носит назва- |
|
ние линии с рабочим конвейером, во втором – с распредели- |
|
тельным конвейером. |
|
7. В зависимости от размещения рабочих мест и кон- |
|
фигурации поточные линии бывают: односторонние, двусто- |
|
ронние, замкнутые, незамкнутые, прямолинейные, Г-образные, |
|
П-образные, кольцевые, зигзагообразные. |
|
Одним из условий непрерывной и ритмичной работы |
|
поточных линий является организация межоперационного |
|
транспорта. В поточном производстве транспорт не только |
|
средство перемещения сырья, материалов, полуфабрикатов, но |
|
и условие организации процесса производства и регулирования |
|
темпов работы. |
|
На поточных линиях применяются разнообразные |
|
средства транспорта. |
|
Все виды поточного транспорта подразделяются на |
|
конвейерные и неконвейерные транспортные средства. |
|
Неконвейерные транспортные средства – это склизы |
|
(желоба), ручные и механизированные тележки, электрокары, |
простаивать. На операциях, длительность которых больше так- |
транспортные роторы в поточных линиях роторного типа. |
та, образуются заделы. |
В полупроводниковом производстве их применение |
|
возможно на поточных линиях, объединяющих ряд последова- |
|
тельных операций. В сборочных цехах обычно средством |
152
транспортировки является транспортерная лента, организующая работу поточной линии. В этом случае она называется конвейером.
Конвейеры бывают рабочие и распределительные.
На рабочем конвейере все операции по изготовлению изделия выполняются на конвейере без снятия. Рабочие конвейеры бывают непрерывные и пульсирующие.
Распределительные конвейеры доставляют изделие на последующие рабочие места линии с заданной скоростью.
Прежде чем формой организации производственного процесса выбрать поток, необходимо произвести анализ изделия, которое хотят перевести на поток. Это изделие должно удовлетворять следующим требованиям:
1)достаточным объемом выпуска;
2)номенклатура должна быть постоянной (устойчи-
вой);
3)конструкция должна быть отработана;
4)устойчива перспектива производства (сбыта);
5)конструкция блочная;
6)широко применена унификация и стандартизация ее
деталей;
7)конструкция технологична.
Выбор типа линии зависит в основном от следующих коэффициентов, представляющих собой отношение:
количества детале-операций к общему числу потребного количества рабочих мест на линии;
средней нормы времени операции к ритму выпуска. Чем ближе значения коэффициентов к единице, тем
больше возможности организовать поток в виде однономенклатурной линии.
Предварительно необходимо рассчитать потребное количество рабочих мест. Здесь учитывают не только технологи-
153

ческий процесс, но и размеры помещения и удобство размещения в нем линии и др. Производят технико-экономическое обоснование (сравнение) нескольких возможных вариантов типа линии, главным образом, по показателям себестоимости
продукции, размеру единовременных затрат и сроку окупаемости затрат.
3. Основные расчеты потока
Рассмотрим их на примере однономенклатурной не- прерывно-поточной линии.
Проектирование поточного процесса начинается с расчета такта. Величина такта кладется в основу разработки технологического режима операций.
Исходными данными для этого расчета являются производственное задание (план) в штуках (на смену, месяц, год) и фонд рабочего времени (в часах или минутах за тот же период). Такт определяется отношением рабочего времени к количеству подлежащих изготовлению изделий за принятый период по формуле
T |
|
ФП |
, |
П |
|
||
|
N |
||
|
|
где ТП – такт поточной линии, мин; ФП – полезный фонд рабочего времени за определенный одинаковый с планом период, мин;
N – объем выпуска продукции за определенный плановый период времени, шт.
Если в течение смены или другого планируемого периода предусматриваются регламентируемые перерывы, то
Т |
|
ФП |
П |
, |
П |
N |
|||
|
|
|
|
где П – перерыв в течение планируемого периода, мин. Лучше при расчете такта поточной линии исходить из
сменного задания и продолжительности смены:
154

Т П |
Фсм Псм |
. |
|
||
|
Nсм |
Значит, под тактом понимается промежуток времени между выпуском, или запуском двух смежных изделий (деталей) с последней или первой операции поточной линии.
Такт по запуску в минутах определяется в том случае, если на операциях планируются технологические потери
Т |
|
Фсм Псм |
, |
П |
|
||
|
N зап.см |
||
|
|
Пример расчета объемов запуска изделий, исходя из суточного планового задания выпуска приборов, дан в таблице
17.
Таблица 17 Расчет суточного (сменного) запуска приборов на поточную линию
Наименова- |
Брак |
Коэффициент выхода |
Коэффи- |
Запуск по |
|
ние опера- |
на |
|
годных |
циент за- |
операциям, шт. |
ций по ходу |
опера- |
|
|
пуска, |
|
по |
по цеху |
|
|||
технологи- |
циях, |
обеспечи- |
|
||
опе |
|
|
|||
ческого |
% |
|
вающий |
|
|
ра- |
|
|
|||
процесса |
|
|
выпуск |
|
|
|
ции |
|
|
||
|
|
|
годных |
|
|
|
|
|
|
|
|
|
|
|
|
приборов |
|
|
|
|
|
по плану |
|
27. Привар- |
– |
1,0 |
0,59*1=0,59 |
1/0,59=1,7 |
1000*1,7=1700 |
ка гибкого |
|
|
|
|
|
вывода |
|
|
|
|
|
28. Циклро- |
– |
1,0 |
0,59*1=0,59 |
1/0,59=1,7 |
1000*1,7=1700 |
вание |
|
|
|
|
|
29. Класси- |
20 |
0,8 |
0,74*0,8=0,59 |
1/0,59=1,7 |
1000*1,7=1700 |
фикация |
|
|
|
|
|
30. Измере- |
5 |
0,95 |
0,78*0,95=0,74 |
1/0,74=1,3 |
1000*1,35=135 |
ние на ст. |
|
|
|
5 |
0 |
31. Провер- |
3 |
0,97 |
0,8*0,97=0,78 |
1/0,78=1,2 |
1000*1,28=128 |
ка на им- |
|
|
|
8 |
0 |
пульс |
|
|
|
|
|
155
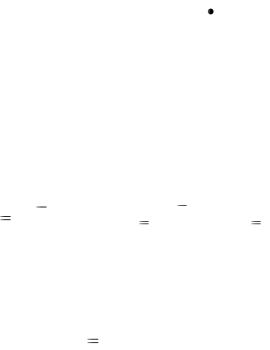
Окончание таблицы 17
32. Испыта- |
– |
1,0 |
0,8*1=0,8 |
1/0,8=1,25 |
1000*1,25=125 |
ние в камере |
|
|
|
|
0 |
влаги |
|
|
|
|
|
33. Класси- |
20 |
0,8 |
0,8 |
1/0,8=1,25 |
1000*1,25=125 |
фикация и |
|
|
|
|
0 |
т.д. |
|
|
|
|
|
План, шт. |
|
|
|
|
1000 |
При передаче на поточной линии изделий транспортными партиями рассчитывается ее ритм
ч=ТП р.
Ритм (ч) равен произведению такта поточной линии на число деталей (изделий) в транспортной партии (ритм характерен для полупроводникового производства).
Такт поточной линии имеет обратную величину –
темп.
Темп поточной линии характеризует ее производительность и представляет собой количество приборов, выданных линией в единицу времени (час, мин, смену и т.д.)
|
|
|
|
|
|
|
|
20 |
|
||
|
|
Ф П |
|
|
60 |
|
|
мин |
|
||
ТТ |
|
, |
Т |
|
8 |
30 шт. за 1 час. |
|||||
|
|
|
|
|
|||||||
|
|
Т |
|
|
|
||||||
|
|
Т П |
|
2 мин |
|
||||||
|
|
|
|
|
|
|
|||||
|
Далее рассчитывается количество рабочих на поточ- |
||||||||||
ной линии (Ср) |
|
|
|
|
|
|
|
|
|||
|
|
СР |
t |
|
|
|
- (на одной операции), |
||||
|
|
|
|
|
|
||||||
|
|
Т П |
|
|
|
||||||
|
|
|
|
|
|
|
|
|
|
|
156

m
|
|
|
ti |
|
С |
|
i 1 |
- (на линии), |
|
Р |
Т |
|
||
|
|
П |
|
где t – норма времени на операцию, мин; ТП – такт поточной линии.
Аналогично считается количество рабочих мест. Выше речь шла о явочном количестве рабочих. Явоч-
ное количество рабочих равно количеству рабочих мест на линии. Списочное количество учитывает количество рабочих смен и возможные потери рабочего времени каждым рабочим, закрепленным за линией,
С р.спис (1 |
|
в |
) |
|
100 |
||||
|
|
m
С р. яв SСМ ,
1
где в – добавочный процент числа рабочих на случай невыходов (очередные отпуска, выполнение гособязанностей, болезни и др.);
Sсм – количество рабочих смен;
– явочная численность рабочих.
Потребное количество оборудования рассчитывается аналогично явочному количеству рабочих, таким образом определяют расчетное количество оборудования, рабочих, рабочих мест с точностью до десятых долей единицы. Принятое количество единиц оборудования и т.д. – это округленное до целого число.
При определении потребного количества оборудования, людей, мест допускается их перегрузка на 10%. Коэффициент загрузки рассчитывается как
К загр |
Соб. расч |
. |
|
Соб.прин |
|||
|
|
157

Особо рассчитывается потребность оборудования с аппаратурными процессами (стенды, сушильные шкафы, термическое оборудование для диффузии, окисления, напыления, эпитаксии и др.)
Соб |
N зап.см. |
|
Тцикл. |
, |
q |
Т |
см |
где Nзап.см – сменное здание по запуску, шт.;
Тцикл – продолжительность одного рабочего цикла оборудования, мин;
Тсм – продолжительность смены, мин; q – емкость оборудования, шт.;
Тцикл = q tвсп tо tподг;
где q tвсп – вспомогательное нормированное время на загрузку и выгрузку приборов, q;
t0 – основное (технологическое) время на операцию,
мин;
tподг – время подготовительное на приведение рабочей зоны в состояние готовности к приему очередной партии приборов, мин.
Рабочая длина поточной линии (Lр) рассчитывается следующим образом
|
m |
Lp |
Cобi li , |
|
i 1 |
где l – расстояние по оси потока между центром соседних рабочих мест, м (1; 1,2; 1,5):
158

Lр Cоб l – при равных расстояниях между рабочими местами на всех операциях.
Это рабочая длина линии при одностороннем (последовательном) расположении рабочих мест.
В целях более компактной планировки применяется 2- стороннее расположение: шахматное и параллельное.
m
Cоб.i li
Lр |
i 1 |
|
|
|
(параллельное расположение); |
|
|
|
|
2 |
|||
|
|
|
|
|
||
|
m |
l |
i |
|
|
|
Lр |
|
(Cоб.i |
1) (“шахматное” расположение). |
|||
2 |
||||||
|
i 1 |
|
|
Скорость движения потока (V) определяется следующим образом
l
V – при непрерывном движении транспорт-
Т п
ной ленты;
V |
l |
– при пульсирующем движении, |
|
||
tтр |
|
|
|
|
где tтр – время транспортировки изделий на один интервал, мин.
Скорость движения конвейера имеет ограничения.
Для рабочих конвейеров с равномерным движением ленты допустимая скорость – 2,25 м в минуту, до 6 м в минуту может быть увеличена скорость в остальных случаях.
На поточной линии имеются заделы (изделия в незавершенном производстве) следующих видов: технологический,
159

транспортный, резервный (страховой). Сумма этих заделов в рублях составляет незавершенное производство поточных линий.
Технологический задел – это изделия, находящиеся в каждый данный момент непосредственно в изготовлении на всех рабочих местах линии
|
m |
Z тех |
Собi p - при передаче транспортными |
i |
1 |
партиями;
Zтех=Соб - при поштучной передаче,
где р – число предметов, одновременно находящихся в работе или на контроле на данном рабочем месте (транспортная партия в полупроводниковом производстве).
Транспортный задел – это изделия, находящиеся в движении на конвейере в каждый данный момент. При штучной передаче с предыдущей операции на последующую он равен
|
m |
Zтр |
Собi 1. |
|
i 1 |
Резервный (страховой) задел – это изделия, предна-
значенные для обеспечения бесперебойного питания последующей операции. Он предотвращает общий простой линии. Хранится на рабочем месте со степенью готовности изделия по данную операцию включительно. Резервный задел обычно восстанавливается каждую смену, при этом он может быть в течение смены разным по величине. Рассчитывается обычно средний размер:
160