
Методическое пособие 483
.pdf
Если tпосл < tпред, то возможно лишь частичное совмещение по времени. Максимально совмещенные в этом случае
операции разнятся на время изготовления последней детали или последней транспортной партии на последующей операции (рисунок 21).
Рисунок 21. Операционный цикл при параллельнопоследовательном виде движения партии изделий
Tц.п-п равна разности между Tц при последовательном движении и суммарной величиной межоперационных перекрытий (r):
141

|
m 1 |
Tц.п п Tц.посл |
ri , |
|
1 |
где m-1 – количество пар смежных операций;
ri – время параллельной работы или период одновременной работы на двух смежных операциях (перекрываемое время).
Чтобы определить для каждой пары смежных операций перекрываемое время (совмещение времени), сравним графики работы операций 1 и 2, 2 и 3, 3 и 4:
r1,2=(3-1) t2,
где t2 – время выполнения более короткой операции
(tкор), т.к. t1=2, t2=1;
r2,3=(3-1) t2,
где t2 – время выполнения более короткой операции,
т.к. t2=1, t3=4;
r3,4=(3-1) t4,
где t4 – время выполнения более короткой операции,
т.к. t3=4, t4=1,5.
Отсюда,
|
m 1 |
Tц.пар. посл. Tц.посл |
(n 1) tкор . |
|
1 |
При выполнении операций на нескольких параллельных рабочих местах
m |
ti |
m 1 |
|
t |
кор |
|
Tц.пар посл n |
|
|
(n 1) |
|
|
. |
ci |
|
cкор |
||||
1 |
1 |
|
|
При передаче изделий транспортными (обработочными, передаточными) партиями
m |
ti |
m 1 |
|
t |
кор |
|
Tц.пар посл n |
|
|
(n p) |
|
|
. |
ci |
|
cкор |
||||
1 |
1 |
|
|
Вернемся к формуле длительности производственного
цикла
142

Тц= Тт(о)+ Тк+ Ттр+ Те+ Тп.
Выше была рассмотрена методика определения длительности технологического (основного) производственного процесса. Время контрольных и транспортных процессов не рассчитывается, т.к. процессы должны осуществляться параллельно технологическим, т.е. время считается перекрываемым. Если часть времени Тк не является перекрываемым, его рассчитывают по методике технологического цикла (Тц. посл., Тц.
пар., Тц. пар.-посл.).
Время перерывов складывается из времени межоперационного ожидания, или пролеживания (Тм.о.), и потерь времени, вызванных режимом работы предприятия (Тсм.р.). Длительность производственного цикла, выраженная в календарных днях, рассчитывается по формуле
Т |
ц. |
|
1,45 |
|
(ТТ (О) |
(m 1) t |
м.о. ) |
Т е |
, |
Т р.дн. |
Sсм Кв.н. 60 |
24 |
|
||||||
|
|
|
|
|
|
||||
где |
Тц – длительность производственного цикла при |
последовательном (параллельном, параллельно-
143

Те – время естественных процессов, которое включается в формулу по фактическим данным завода, ч; 24 – продолжительность суток.
Для определения длительности производственного цикла прибора, как правило, используется формула
Тц. изд.= Тц.вед.д.+ Тц. вед.сб.ед.+ Тц. сб.и.,
где Тц.вед.д – производственный цикл изготовления ведущей детали, календарные дни;
Тц. вед.сб.ед – то же сборочной единицы, календарные дни; Тц. сб.и. – то же сборки изделия, календарные дни.
Длительность производственного цикла можно определить по построенному сетевому графику процессов изготовления прибора, а также построением циклового графика. Цикловой график строится на основе рассчитанных заранее длительностей производственного цикла деталей, сборочных единиц, сборки изделия. График продолжительности времени строится в порядке, обратном ходу технологического процесса изготовления, исходя из даты отгрузки партии изделий покупателю согласно “Договору о поставке”. Пример графика дан
-последовательном) видах движения предметов труда по опена рисунке 22. рациям, календарные дни;
Тм.о.=(m-1) tм.о. ,
где m – количество операций;
tм.о. – пролеживание между парой смежных операций, мин; Тр. дн. – продолжительность рабочего дня, ч;
Sсм. – количество смен работы предприятия, цеха;
Кв.н. – планируемый коэффициент выполнения установленных норм выработки или времени на операциях;
60 – перевод Тр. дн. в минуты; 1,45 – коэффициент перевода рабочих дней в календарные;
144
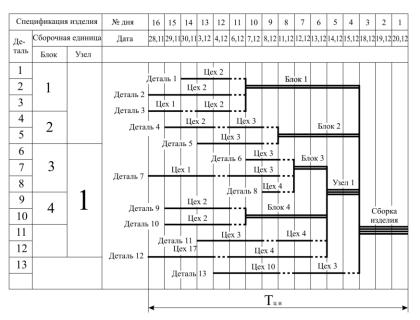
Рисунок 22. Цикловой график производственного цикла изделия.
На рисунке штриховой линией отмечено резервное (страховое) время деталей.
6. Пути сокращения длительности производственного цикла
При изучении в курсе “Экономика предприятия” оборотных средств и их оборачиваемости мы отмечали, что производственный цикл включается в показатель оборачиваемости
145

Д Т |
Сп |
...П... Т Д , |
|
Рс |
|||
|
|
где П – длительность производственного цикла.
Каждый оборот оборотных средств приносит предприятию прибыль, чем короче цикл, тем больше оборотов и масса прибыли. Изделия в период производства (П) являются его незавершенным производством (элементом оборотных средств). Мероприятия по сокращению производственного цикла вытекают из принципов построения производственного процесса: специализации, пропорциональности, параллельности и др. Более полная реализация принципов на практике приводит к сокращению длительности производственного цикла. Факторы его сокращения целесообразно рассмотреть по элементам производственного цикла.
Тц= Тт(о)+ Тк+ Ттр+ Те+ Тп..
Сокращение длительности рабочего периода достигается за счет совершенствования технологий, повышения технологичности конструкции, совершенствования организации производства.
В свою очередь, совершенствование технологических процессов сводится к их автоматизации, интенсификации процессов, внедрению скоростных режимов работы оборудования, прогрессивных технологических процессов, групповой обработки. Эффективной является концентрация нескольких операций в одной единице оборудования.
Направлениями совершенствования организации производства выступают внедрение параллельного и параллельнопоследовательного видов движения изделий, параллельных рабочих мест, поточных принципов производства, бригадных форм организации труда; сокращения транспортировок - автоматизация, унификация тары, прогрессивные технологические планировки производственных участков и цехов; сокращения времени контрольных операций (а они в полупроводниковом производстве занимают до 30 % времени рабочего периода производственного цикла) – автоматизация, внедрение статистических методов контроля (методы будут изучены в одной
146
из последующих тем курса), совмещение времени технологических и контрольных операций.
Последнее исследование фактического времени перерывов в производственном цикле изделий машиностроительного комплекса, включая предприятия радио- и электронной промышленности, было проведено по Центральному Черно- земно-Экономическому району (ЦЧЭР) в конце 50-х - начале 60-х годов прошлого столетия. Тогда оно составило 70 % времени, оно и сейчас более 50 %. Сократить его долю можно за счет замены последовательно вида движения элементов изделия в производственном процессе параллельным (поточным производством) и параллельно-последовательным; введением предметной специализации цехов и участков вместо технологической; увеличением количества рабочих смен; уплотнением рабочего дня за счет ликвидации простоев.
2.2 Организация поточного производства
Рекомендуемая литература
1.Организация, планирование и управление предприятиями электронной промышленности /Под ред. П.М. Сту-
колова, 1986. С. 124-145
2.Организация и планирование машиностроительного производства /Под ред. М.И. Ипатова и др. 1988. М.: Высш. шк. С. 179-196
3.Орлов В.И. Гибкие производственные системы. Организация и оборудование. Обзоры по электронной технике. Серия 7. Технология, организация производства и оборудование. – М.: ЦНИИ “Электроника”, 1985. 43с.
4.Организация производства /Под ред. О.Г. Туровца, М.: Экономика и финансы, 2002. 452 с.
147
|
Поточное производство организовано на основе па- |
|
раллельного движения предметов труда по операциям. |
|
Сущность поточного метода заключается в том, что |
|
параллельный вид движения предметов труда по ходу техноло- |
|
гического процесса осуществляется по жестко и четко уста- |
|
новленному маршруту и в заранее рассчитанных темпах. |
|
Наиболее общими принципами организации поточного |
|
производства являются: |
|
1) расчленение процесса производства на простые по |
|
содержанию операции (1-3 перехода); |
|
2) расчленение процесса производства на равные или |
|
кратные по трудоемкости операции и установление целесооб- |
|
разной их последовательности, что служит предпосылкой не- |
|
прерывности производства; |
|
3) закрепление одной детале-операции за одним рабо- |
|
чим местом; |
|
4) прямоточное с наименьшими разрывами расположе- |
|
ние рабочих мест по ходу технологического процесса; |
|
5) поштучная передача деталей (изделий) или неболь- |
|
шими транспортными партиями с одного рабочего места на |
|
другое сразу после обработки на предыдущей операции с по- |
|
мощью специальных транспортных средств; |
|
6) одновременное параллельное выполнение операций |
|
на всех или большинстве рабочих мест; |
|
7) преимущественно механизированное передвижение |
|
обрабатываемых предметов с операции на операцию; |
|
8) замкнутый характер производства и непрерывность |
|
движения предметов труда в процессе производства. |
|
Только совокупность этих признаков дает поток. |
|
Впервые поток был создан в СССР в 1938г. на Воронежском |
|
заводе “Электросигнал”. |
|
Поточный метод является наиболее прогрессивной |
1. Сущность и принципы организации поточного |
формой организации производственных процессов, наиболее |
производства |
эффективной. Поточное производство, как видно из вышеска- |
|
занного, обладает характерными чертами передовой организа- |
148

ции производственных процессов: специализацией рабочих мест, параллельным выполнением операций, пропорциональностью мощностей, ритмичностью и непрерывностью протекания процессов.
Поточное производство представлено поточными линиями. Поточная линия (ПЛ) – группа рабочих мест, организованная на основе принципов поточного производства.
2. Организация поточных линий
Поточные линии, применяемые в производстве, весьма разнообразны и делятся на несколько групп.
1. По степени механизации и автоматизации процесса
различают немеханизированные, механизированные и автоматизированные поточные линии.
Механизированная поточная линия характеризуется тем, что в ней механизированы технологические, транспортные и контрольные операции.
Уровень механизации линии можно определить следующим образом:
|
К |
|
|
|
С р |
1; |
|
||
|
А,М |
|
Соб |
|
|||||
|
|
|
|
|
|
|
|
||
К |
|
|
Т МА |
Т МР |
1, |
||||
А,М |
|
|
Т |
|
|
|
|||
|
|
|
|
шт |
|
|
|
где Соб – общее количество рабочих мест (оборудования) на линии; Ср – общее количество рабочих на линии;
149
– суммарное время соответственно машинноавтоматическое, машинно-ручное и штучное время по всем операциям, в том числе и транспортным.
2. По количеству закрепленных за линией изделий и по порядку их чередования поточные линии делятся на однономенклатурные, многономенклатурные и групповые.
Однономенклатурные поточные линии, за которыми закреплено одно изделие, применяются в массовом производстве, обеспечивающем достаточную специализацию и полную загрузку рабочих мест.
Многономенклатурные поточные линии, на которых изготавливается по унифицированному технологическому процессу несколько наименований конструктивно сходных изделий, позволяет внедрить поточные методы работы в серийное производство. Эти линии могут быть с последовательным, параллельным и смешанным чередованием изделий.
Многономенклатурные поточные линии с последовательным чередованием изделий характеризуются тем, что одновременно на линии изготавливается одно изделие, путем переналадки оборудования изделия по очереди изготавливаются в течение года, квартала.
На многономенклатурных поточных линиях с параллельным изготовлением изделий одновременно изготавливают все наименования изделий, которые планируются на один год.
Например, поточная линия по одновременному изготовлению жгутов трех видов (№ 1,2,3) для телевизоров на Воронежском заводе «Электросигнал».
На смешанных многономенклатурных поточных линиях одновременно сочетаются и последовательный, и параллельный принципы.
Разновидностью последнего типа поточных линий являются групповые поточные линии. На них закрепляется и изготавливается несколько изделий различных по конструкции, технологии изготовления и сборке. Применяются они в единичном и мелкосерийном производстве.
3. В зависимости от способа транспортировки изделия поточные линии бывают:
150