
- •ВВЕДЕНИЕ
- •1. ЦЕЛЬ И ЗАДАЧИ КУРСОВОЙ РАБОТЫ
- •3. РАСЧЁТНАЯ ЧАСТЬ КУРСОВОЙ РАБОТЫ
- •3.1.1. Анализ исходных данных
- •3.1.3. Выбор технологических баз и схем установки заготовки
- •3.1.6. Расчет и назначение припусков и операционных размеров
- •3.1.7. Расчет режимов резания
- •3.1.8. Определение норм штучного времени
- •3.1.9. Расчет экономической эффективности ТП
- •3.1.10. Оформление технологических документов
- •3.2. Разработка технологии восстановления детали
- •3.2.4. Сопутствующая технологическая документация
- •3.2.6. Оформление технологической документации
- •3.3. Проектирование и расчёт приспособлений
- •3.3.2. Состав приспособления
- •3.3.4. Расчет составляющих силы резания
- •3.3.5. Расчет усилия зажима заготовки
- •3.3.6. Расчет рычажных зажимных механизмов
- •4. ТРЕБОВАНИЯ К ОФОРМЛЕНИЮ КУРСОВОЙ РАБОТЫ
- •4.1. Содержание пояснительной записки
- •4.2. Требования к оформлению пояснительной записки
- •4.2.1. Общие положения
- •4.2.2. Требования к текстовым документам
- •4.3.2. Требования к оформлению сборочного чертежа
- •Библиографический список
- •Приложение 1
- •Приложение 3
- •Приложение 6

технологического процесса может определяться путем сравнения следующих показателей:
а) себестоимости ремонта или изготовления детали со стоимостью детали по прейскуранту;
б) себестоимости ремонта детали разными способами; в) себестоимости механической обработки детали разными методами.
Эффективность ремонта детали выражается коэффициентом эффективности (коэффициентом экономической целесообразности ремонта) Кэ, который определяется по формуле
Kэ |
|
СнКд |
1, |
(16) |
|
||||
|
|
Св |
|
где Сн – стоимость новой детали по прейскуранту, руб.; Св – себестоимость восстановления детали, руб.; Кд – коэффициент долговечности детали, восстановленной принятым способом.
Оптимальный вариант механической обработки детали определяется путем сравнения себестоимости обработки ее различными методами. Наиболее эффективным способом восстановления детали является такой, у которого отношение себестоимости восстановления к коэффициенту долго-
вечности детали, восстановленной этим способом, будет меньше: |
|
||||
|
Св1 |
|
Св2 |
|
(17) |
|
Кд1 или |
Кд2 и т.д. |
|||
|
|
3.2.4. Сопутствующая технологическая документация
Установив рациональный способ устранения дефектов (групп дефектов) и мер, повышающих механические свойства детали, необходимо выполнить ремонтный чертеж детали (рис. 3).
Ремонтные чертежи выполняют в соответствии с правилами, предусмотренными ГОСТ 2.604-68 «Чертежи ремонтные» и ОСТ 70.0009.006-85 «Чертежи ремонтные. Порядок разработки, согласования и утверждения».
Карты технологического процесса восстановления детали.
Оформление карт технологических процессов производится в соответствии с требованиями ГОСТ 3.1118-82, ГОСТ 3.1404-86 и др.
Планы операций технологических процессов восстановления детали по маршрутам. План операций технологического процесса разрабатывается для каждого в отдельности маршрута на основании изучения ремонтного чертежа детали.
54
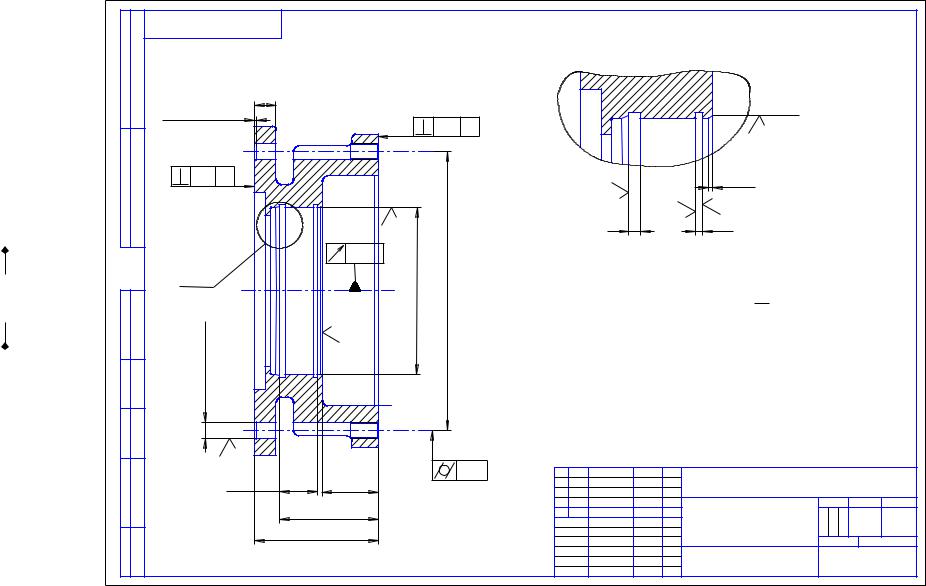
|
|
|
ЭО-3322.03.02.015 |
|
|
|
|
|
|
|
|
|
|
|
|
|
|
. |
|
|
|
|
|
Б (2:1) |
|
|
|
|
|
|
|
|
|
Перв. примен |
|
17 |
|
|
|
|
|
|
|
|
|
|
|
|
|
|
|
|
|
|
|
|
|
|
|
|
|
|
|
|
|
|
2 фаски 1,3•45 |
|
|
|
|
|
|
|
|
|
|
|
|
|
|
|
|
|
|
|
0,8 |
В |
|
|
|
Rz 40 |
|
|
|
|
|
|
|
|
|
|
|
|
|
|
|
|
|
|
|
|
|
. № |
0,1 |
В |
|
|
|
|
|
|
2•45 |
|
|
|
|
|
Рис |
прав |
|
|
|
|
|
2,5 |
|
|
2.5 |
|
|
|
|
|
С |
|
|
|
2,5 |
|
5 |
|
2.5 |
2,8 |
|
|
|
|
|
|
. |
|
|
|
|
|
|
|
|
|
|
|
|
|
|
|
.3 |
|
|
|
0,045 |
) |
|
|
|
|
|
|
|
|
|
|
2.сиР |
|
Б |
|
|
+0,010 -0,025 |
|
1.HB 131...157. |
|
|
|
|
|
|
|
|
|
|
|
|
2.*Размеры для справок. |
|
|
|
|
|
|
||||
|
|
|
|
|
|
|
|
IT14 |
|
|
|
||||
|
|
|
|
|
|
|
|
|
|
|
|
|
|||
55 |
Ремонтный |
одп. и дата |
|
|
Rz80 |
93,15K7( |
147,42 |
3.Неуказанныепредельныеотклонения H14,h14,± |
2 . |
|
|
|
|||
|
|
4.Несоосность поверхностей Б,В,Г не более 0.06мм. |
|
|
|
||||||||||
0,035 |
|
5.Допускается неустранять дефекты, величина которых не выходит за пределы |
|||||||||||||
|
детали чертёж |
зам. инв. № Инв. № дубл. П |
+ |
|
|
|
|
допустимых значений, указанных в таблицедефектов. |
|
|
|
||||
|
2отв.11,37 |
|
|
|
|
|
|
|
|||||||
|
|
|
|
|
6.На обработанных поверхностях допускают рассредоточениераковин (на расстоянии |
||||||||||
|
|
|
|
|
неменее 15мм друг от друга) диаметром не более 3мм и глубиной 2мм. |
|
|
||||||||
|
|
|
|
|
7.Осталные технические требования по ГОСТ 70.0009.003-84. |
|
|
|
|||||||
|
2,5 |
|
|
|
|
|
|
|
|
|
|
|
|||
|
|
В |
|
|
|
|
|
|
|
|
|
|
|
|
|
|
|
|
|
|
|
|
0,01 |
|
|
|
|
|
|
|
|
|
|
дата |
|
22,5 +0,052 |
28,35 |
|
|
|
|
ЭО-3322.03.02.015 |
|
||||
|
|
|
|
|
|
|
|
|
|||||||
|
|
. и |
|
|
|
|
|
|
|
|
|
|
Лит. |
Масса Масштаб |
|
|
|
Подп |
|
|
63,8 |
|
|
Изм. Лист № докум. |
Подп. |
Дата |
Корпусмуфты |
||||
|
|
|
|
|
|
|
|
1:1 |
|||||||
|
|
. |
|
|
87* |
|
|
Разраб. |
|
|
ремонтный чертеж |
|
|
||
|
|
|
|
|
|
Пров. |
|
|
|
|
|
||||
|
|
подл |
|
|
|
|
|
|
Лист |
Листов |
|||||
|
|
|
|
|
|
|
Т.контр. |
|
|
Сталь 30 ХГС |
|||||
|
|
№ |
|
|
|
|
|
Н.контр. |
|
|
|
|
|
||
|
|
Инв. |
|
|
|
|
|
|
|
|
|
|
|||
|
|
|
|
|
|
|
|
|
ГОСТ 5632-72 |
|
|
|
|||
|
|
|
|
|
|
|
Утв. |
|
|
|
|
|
|||
|
|
|
|
|
|
|
|
|
|
|
Копировал |
|
Формат |
A3 |

Намечая план операций для каждого маршрута, необходимо исходить из условий правильного базирования детали, чтобы обеспечить необходимую точность обработки, удобство, простоту и надежность закрепления детали.
При выборе базовых поверхностей необходимо учитывать следующие положения:
1)рекомендуется принимать основные поверхности, при помощи которых определяется положение детали в изделии;
2)базирование детали по поверхности с износами повышает погрешности базирования и снижает точность обработки;
3)базирующая поверхность должна обеспечивать наибольшую жесткость детали при установке ее на станке или в приспособление;
4)в качестве установочной базы может быть принята вспомогательная база. Она может быть использована для исправления основных базовых поверхностей;
5)за черновые базы необходимо принимать поверхности, которые не обрабатываются или обрабатываются с минимальной точностью;
6)за черновую базу рекомендуется принимать основные базирующие поверхности;
7)необходимо соблюдать принцип постоянства баз, целесообразно использовать те же базы, что и при изготовлении детали.
При составлении плана операций для каждого маршрута первоначально необходимо выделить наиболее ответственные (точные) поверхности, а также дефекты, требующие многократной обработки для их устранения. Затем для устранения каждого дефекта, входящего в маршрут, намечают состав и последовательность выполнения технологических операций.
На основании последовательности выполнения операций по устранению каждого в отдельности дефекта составляется план операций для отдельного маршрута (сочетание дефектов) путем выявления операций, которые можно совместить, и поверхностей, которые можно обработать совместно.
Технологические операции каждого маршрута располагают одна за другой в наиболее рациональной последовательности из условий выполнения требований ремонтного чертежа наиболее экономичным способом.
При составлении плана технологических операций маршрута можно исходить из таких основных положений:
1)тепловые операции (кузнечные, сварочные, наплавочные и т.д.) выполняются в первую очередь, т.к. при этом вследствие остаточных внутренних напряжений возникает деформация деталей;
2)операции, при выполнении которых производится съем металла большой толщины, также планируются в числе первых, т.к. при этом
56

выявляются возможные внутренние дефекты и происходит перераспределение внутренних напряжений, что сопровождается деформациями деталей;
3)механическую обработку необходимо начинать с исправления базовых поверхностей, а при использовании в качестве установочных баз работавших поверхностей необходимо ориентироваться на изношенные участки;
4)в первую очередь необходимо обработать ту поверхность, относительно которой на чертеже координировано большее количество других поверхностей;
5)в числе последующих операций назначают механические (слесарные) и окончательные обработки сначала менее точных поверхностей, а затем более точных;
6)если при восстановлении детали применяется термическая обработка, то операции выполняются в такой последовательности: черновая механическая, термическая, чистовая механическая;
7)не рекомендуется совмещать черновые и чистовые операции, т.к. они выполняются с различной точностью;
8)в последнюю очередь выполняются чистовые операции;
9)заканчивают обработку детали обработкой наиболее точной поверхности;
10)последними в маршруте часто назначают обработку легко повреждаемых поверхностей (резьба и т.п.).
Вкачестве примера в табл. 34 приведен примерный план технологического процесса восстановления гильзы двигателя СМД-14.
Выбор средств технологического оснащения. Средства технологиче-
ского оснащения включают:
– технологическое оборудование (в том числе контрольное и испытательное);
– технологическую оснастку (в том числе инструменты и средства контроля);
– средства механизации и автоматизации производственных процессов. Выбор технологического оборудования производится исходя из сле-
дующих основных условий:
1)возможности формирования требуемых поверхностей деталей, возможности выполнения технических требований, которые предъявляются к детали;
2)соответствия основных размеров оборудования габаритным размерам детали;
3)обеспечения наиболее эффективных методов обработки поверхностей (выполнения работы).
57

Таблица 34
Примерный план технического процесса восстановления гильзы двигателя СМД-14
Номер |
Наименование и содержание операции |
|
операции |
||
|
||
1 |
Токарно-винторезная. Зачистить наружные посадочные пояски, |
|
|
расточить фаски |
|
2 |
Внутришлифовальная. Шлифовать внутреннюю поверхность |
|
|
гильзы |
|
3 |
Токарно-винторезная. Подрезать внутренний бурт гильзы |
|
4 |
Хонинговальная. Предварительно хонинговать внутреннюю |
|
|
поверхность гильзы |
|
5 |
Хонинговальная. Окончательно хонинговать внутреннюю по- |
|
|
верхность гильзы |
|
6 |
Виброобработочная. Обработать вибрационно-механическим |
|
|
методом внутреннюю поверхность гильзы |
|
7 |
Контрольная. Заключительный контроль |
|
|
|
Выбор технологической оснастки производится на основе анализа возможности реализации технологического процесса при выполнении технических требований к детали, технических возможностей, а также конструктивных характеристик детали (габаритные размеры, материал, точность, конструктивные характеристики поверхностей и т.д.) и организаци- онно-технологических условий ее ремонта (схема базирования и фиксации, вид технологической операции, организационная форма процесса ремонта).
Выбранные средства технологического оснащения заносят в сводную ведомость оборудования и оснастки.
3.2.5. Расчет режимов выполнения основных технологических операций и техническое нормирование
Автоматическая наплавка под слоем флюса. Скорость наплавки Vн,
м/ч:
V |
|
ан I |
. |
(18) |
|
||||
н |
|
h S |
|
Частота вращения детали nД , мин-1 :
58

|
|
nД |
1000 Vн |
. |
(19) |
|||||
|
|
|
|
|||||||
|
|
|
|
60 d |
Таблица 35 |
|||||
|
|
|
|
|
|
|
|
|||
Зависимость силы тока от диаметра детали |
||||||||||
|
|
|
|
|
|
|
||||
|
|
Сила тока, А, при диаметре электродной |
|
|||||||
Диаметр детали, мм |
|
|
|
проволоки, мм |
|
|
||||
|
|
|
|
|
|
|
|
|
||
|
|
1,2-1,6 |
|
|
|
2-2,5 |
|
|||
|
|
|
|
|
|
|
|
|
||
50-60 |
|
120-140 |
|
|
|
140-160 |
|
|||
|
|
|
|
|
|
|
|
|
||
65-75 |
|
150-170 |
|
|
|
180-220 |
|
|||
|
|
|
|
|
|
|
|
|
||
80-100 |
|
180-200 |
|
|
|
230-280 |
|
|||
|
|
|
|
|
|
|
|
|
||
150-200 |
|
230-250 |
|
|
|
300-350 |
|
|||
|
|
|
|
|
|
|
|
|
||
250-300 |
|
270-300 |
|
|
|
350-380 |
|
|||
|
|
|
|
|
|
|
||||
Скорость подачи проволоки VПР , м/ч : |
|
|
||||||||
|
|
VПР |
4 ан I |
|
|
|||||
|
|
|
. |
(20) |
||||||
Шаг наплавки S , мм/об : |
dПР2 |
|||||||||
S (2 2,5) dПР . |
(21) |
|||||||||
Вылет электрода , мм : |
||||||||||
|
|
|
|
|
|
|
|
|||
|
|
(10 12) dПР . |
(22) |
|||||||
Смещение электрода l , мм : |
|
|
||||||||
|
|
l (0,05 0,07) d , |
(23) |
где ан – коэффициент наплавки, г/А·ч (при наплавке постоянным током обратной полярности ан=11–14); – плотность электродной проволоки, г/см3 , =7,85; dПР – диаметр электродной проволоки, мм; I – сила тока, А (табл. 35); d – диметр детали, мм.
Параметры режима наплавки следует подставлять в формулы без изменения размерностей.
Толщина слоя наплавки h, мм, наносимого на наружные цилиндрические поверхности, определяется по следующей формуле:
h |
И |
z |
z |
|
, |
(24) |
|
|
|||||
2 |
1 |
|
2 |
|
|
где И – износ детали, мм; z1 – припуск на обработку перед слоем наплав-
ки, мм (на сторону), ориентировочно z1=0,1…0,3 мм;z2 – припуск на ме-
59

ханическую обработку после нанесения слоя наплавки, мм (на сторону,
табл. 36).
Таблица 36
Припуск на механическую обработку при восстановлении деталей различными способами
Способ восстановления |
Минимальный односторонний |
|
припуск z2, мм |
||
|
||
Ручная электродуговая наплавка |
1,4…1,7 |
|
|
|
|
Наплавка под слоем флюса |
0,8…1,1 |
|
|
|
|
Вибродуговая наплавка |
0,6…0,8 |
|
|
|
|
Наплавка в среде углекислого газа |
0,6…0,8 |
|
|
|
|
Плазменная наплавка |
0,4…0,6 |
|
|
|
|
Аргонно-дуговая наплавка |
0,4…0,6 |
|
|
|
|
Электроконтактная наплавка |
0,2…0,5 |
|
|
|
|
Газотермическое напыление |
0,2…0,5 |
|
|
|
|
Осталивание |
0,1…0,20 |
|
|
|
|
Хромирование |
0,05…0,1 |
|
|
|
В зависимости от необходимой твердости наплавленного слоя применяют следующие марки проволок и флюсов.
Наплавка проволоками Св-08А, НВ-30, НП-40, НП-60, НП-30ХГСА под слоем плавленых флюсов (АН-348А, ОСЦ-45) обеспечивает твердость НВ 187-300. Использование керамических флюсов (АНК-18, ШСН) с указанными проволоками позволяет повысить твердость до HRC 40-55 (без термообработки).
Норма времени на выполнение наплавочных работ под слоем флюса и другими механизированными способами наплавки Тн складывается из следующих элементов затрат времени:
Тн То Твс Тдоп |
Тпз |
, |
(25) |
|
|||
|
n |
|
где То– основное время, определяется по следующей формуле:
То |
d l |
|
, |
(26) |
1000 V |
S |
|||
|
н |
|
|
|
здесь l – длина направляемой поверхности детали, мм; n – количество наплавляемых деталей в партии, шт.; Твс – вспомогательное время наплавки (в учебных целях для механизированных способов наплавки принимается
60

равным 2–4 мин); Тдоп – дополнительное время, определяется по следующей формуле:
Тдоп |
(То Твс ) К |
, |
(27) |
|
|||
100 |
|
|
где К = 10–14% – коэффициент, учитывающий долю дополнительного
времени от основного и вспомогательного; Тпз |
– принимается (в учебных |
|||
целях) равным 16–20 мин. |
|
|
|
|
Вибродуговая наплавка. Сила тока: |
2 |
|
|
|
d |
|
|
||
I (60...75) |
|
ПР |
. |
(28) |
|
|
|||
4 |
|
|
|
Скорость подачи электродной проволоки может быть подсчитана по
формуле |
|
0,1 I U |
|
|
|
VПР |
|
, |
(29) |
||
dПР2 |
|||||
|
|
|
|
где VПР – скорость подачи проволоки, м/ч; I – сила тока, А; U – напряжение, U =14 – 20 В; dПР – диаметр электродной проволоки, мм (табл. 37).
Скорость наплавки рассчитывается по формуле
|
|
0,785 d |
2 |
V |
ПР |
|
|
|
VН |
|
|
ПР |
|
|
, |
(30) |
|
h S a |
|
|
||||||
|
|
|
|
|
|
где VН – скорость наплавки, м/ч; – коэффициент перехода электродного материала в наплавленный металл, принимают равным 0,8–0,9; h – заданная толщина наплавленного слоя (без механической обработки), мм; S – шаг наплавки, мм/об; a – коэффициент, учитывающий отклонения фактической площади сечения наплавленного слоя от площади четырехугольника с высотой h, a = 0,8.
Между скоростью подачи электродной проволоки и скоростью наплавки существует оптимальное соотношение, при котором обеспечивается хорошее качество наплавки. Обычно VН (0,4 0,8)VПР . Частота вращения детали определяется по формуле (19).
Шаг наплавки:
S (1,6 2,2) dПР . |
|
(31) |
||||||
Амплитуда колебаний: |
|
|
|
|
|
|
|
|
A (0,75 1,0) dПР . |
|
(32) |
||||||
Индуктивность L, Гн: |
|
2 |
|
|
|
|
|
|
|
51 d |
|
V |
ПР |
|
|
|
|
L |
|
ПР |
|
|
, |
(33) |
||
|
|
|
|
|
||||
|
Imax |
2 f |
|
|
|
|
61

где Imax – максимальная сила тока в цепи, А (ее берут в два раза больше силы тока по амперметру); f – частота колебаний, Гц.
Таблица 37
Сварочная проволока, выпускаемая для механизированной сварки и наплавки
по ГОСТ 2246-70, ГОСТ 10543-82
Марка проволоки |
Диаметр сварочной |
Краткая |
и краткая характеристика |
проволоки, мм |
характеристика поверх- |
|
|
ностного слоя после на- |
|
|
плавки |
Св 08; |
0,8; 1,0; 1,2; 1,4; 1,6; |
Твердость НRC20 |
низкоуглеродистая, для дета- |
2,0; 2,5; 3,0; 3,2; 3,5 |
|
лей из низкоуглеродистых |
|
|
сталей |
|
|
Св 08 Г2С; |
|
Твердость HRC20 |
низкоуглеродистая, кремне- |
-//- |
|
марганцовистая |
|
|
Нп 30; |
|
Твердость HRC30 |
среднеуглеродистая, содер- |
-//- |
|
жание С 0,3 %, для осей, |
|
|
валов |
|
|
Нп 80; |
-//- |
Твердость HRC 40 |
высокоуглеродистая, С 0,8 |
|
|
%, для коленчатых валов, |
|
|
крестовин, деталей ходовой |
|
|
части |
|
|
ПП-АН 1; |
|
Твердость HRC50, |
порошковая, низкоуглероди- |
-//- |
повышенная износостой- |
стая, с порошком ферромар- |
|
кость |
ганца |
|
|
ПП-АН 122; |
|
Твердость HRC50, по- |
порошковая, легирующие |
-//- |
вышенная износостой- |
элементы: Mn – 08 %, Cr – |
|
кость |
4,5 % и др. для валов, осей, |
|
|
коленчатых валов |
|
|
Применяются следующие марки электродных проволок: Нп-65, Нп-80, Нп-30ХГСА и др.
Твердость наплавленного слоя зависит от химического состава электродной проволоки и количества охлаждающей жидкости (среды). При наплавке проволокой Нп-60, Нп-80 и др. с охлаждением обеспечивается
62

твердость 35 – 55 HRC. Расчет нормы времени для вибродуговой наплавки следует выполнять по формулам (25), (26), (27).
Наплавка в среде углекислого газа. Сила тока выбирается в зависи-
мости от диаметра электрода и диаметра детали (см. табл. 35).
Скорость наплавки VН , частота вращения n, скорость подачи электродной проволоки VПР , шаг наплавки S, смещение электрода l определяются по тем же формулам, что и при наплавке под слоем флюса. При определении режимов наплавки следует учитывать практические рекомендации
(табл. 38).
|
Режимы наплавки в углекислом газе |
Таблица 38 |
||||
|
|
|
||||
|
|
|
|
|
|
|
Диаметр |
Диаметр |
|
I, А |
|
U, В |
|
проволоки, мм |
детали, мм |
|
|
|
||
|
|
|
|
|
||
|
|
|
|
|
|
|
До 0,8 |
10…20 |
|
70…95 |
|
18…19 |
|
|
|
|
|
|
|
|
0,8…1 |
20…30 |
|
90…120 |
|
18…19 |
|
|
|
|
|
|
|
|
1,0 |
30…40 |
|
110…140 |
|
18…19 |
|
|
|
|
|
|
|
|
1…1,2 |
40…50 |
|
130…160 |
|
18…20 |
|
|
|
|
|
|
|
|
1,2…1,4 |
50…70 |
|
140…175 |
|
19…20 |
|
|
|
|
|
|
|
|
1,4…1,6 |
70…90 |
|
170…195 |
|
20…21 |
|
|
|
|
|
|
|
|
1,6…2 |
90…120 |
|
195…225 |
|
20…22 |
|
|
|
|
|
|
|
|
Коэффициент |
наплавки при |
наплавке на обратной |
полярности |
аН = 10...12 г/А ч. Вылет электрода равен 8…15 мм. Расход углекислого газа составляет 8…20 л/мин. Наплавка осуществляется проволоками Нп-30ХГСА, Св-18ХГСА, Св-08Г2С, в состав которых должны обязательно входить раскислители – кремний, марганец.
Твердость слоя, наплавленного низкоуглеродистыми проволоками марок Св-08Г2С, Св-12ГС, составляет HB 200-250, а проволоками с содержа-
нием углерода более 0,3% (30ХГСА и |
др.) после закалки |
достигает |
50 HRC. Норму времени следует рассчитывать по формулам(25),(26),(27). |
||
Гальванические покрытия. Сила тока |
|
|
I Dk Fk |
, |
(34) |
где Dk – катодная плотность тока, А/дм2 (определяется условиями работы детали, видом покрытия, температурой и концентрацией электролита). При хромировании принимают Dk = 50 – 75 А/дм2, при осталивании –
20…30 А/дм2 ; Fk – площадь покрываемой поверхности, дм2. Норма времени Тн определяется выражением
63

Тн |
|
(Тo Т1) Кпз |
, |
(35) |
|
||||
|
|
nД И |
|
где Тo – продолжительность электролитического осаждения металлов в ванне, ч; Т1 – время на загрузку и выгрузку деталей, Т1 = 0,1 – 0,2 ч; Кпз – коэффициент, учитывающий дополнительное и подготовительнозаключительное время (при работе в одну смену Кпз =1,1 – 1,2; в две смены Кпз =1,03 – 1,05); nД – число деталей, одновременно наращиваемых в ванне (для учебных целей можно принять 10 – 40); И – коэффициент использования ванны, И =0,8 – 0,95.
Время выдержки деталей в ванне определяется по формуле
Т0 |
1000 h |
, |
(36) |
||
C D |
|
В |
|||
|
Н |
|
|
|
где h – толщина наращивания, мм (выбирается согласно заданию с учетом износа и припуска на обработку); – плотность осажденного металла, г/см3 (хромирование – =6,9; осталивание – =7,8); C – электрохимический эквивалент металла, г/А∙ч (хромирование – C = 0,323; осталивание – C = 1,042); В – выход металла по току (для хромирования – 12 – 15%; для осталивания – 80 – 95%).
Отношение площади анода к площади катода FВ / Fк при осталивании и хромировании можно принять 2:1.
Механическая обработка покрытий. Механическая обработка по-
крытий, наносимых на изношенные поверхности, является завершающей операцией в технологии восстановления деталей.
Механическую обработку наплавленных слоев при твердости до HRC 40 рекомендуется выполнять резанием резцами с пластинами из сплава ВК6. При твердости свыше HRC 40 следует применять шлифование.
При восстановлении изношенной поверхности железнением и хромированием шлифование рекомендуется выполнять кругами на керамической связке зернистостью 20 – 25 среднемягкой или мягкой твердости (от М1-М3 до СМ1-СМ2) при скорости круга 25 – 30 м/с.
Шлифование наплавленных слоев с высокой твердостью рекомендуется производить кругами из электрокорунда хромистого при твердости СМ1-СМ2 и скорости 30 – 335 м/с.
К основным элементам режима резания относятся: глубина резания t,
мм; подача S, мм/об; скорость резания V, м/мин или частота вращения n, мин-1.
64

Выбор режима резания при токарной обработке. Частота вращения
n |
1000 V |
. |
(37) |
|
|||
|
d |
|
Глубина резания t определяется исходя из возможностей оборудования и требований к качеству детали.
Подача для черновых точений выбирается по табл. 39 и 40 (для учебных целей). Требуемая шероховатость обработанной поверхности является основным фактором, определяющим подачи при чистовом точении (табл. 41).
|
Подача при обтачивании деталей из стали |
|
|
Таблица 39 |
|||||||||||||||||
|
|
|
|
|
|
||||||||||||||||
|
|
|
|
|
|
|
|
|
|
|
|
|
|
|
|
|
|
|
|
|
|
Глубина резания ,tмм |
|
|
|
|
|
|
Диаметр детали, мм |
|
|
|
|
|
|
|
|
||||||
18 |
|
30 |
|
50 |
|
80 |
|
|
120 |
180 |
|
260 |
|
Св. 260 |
|||||||
|
|
|
|
|
|
|
|
||||||||||||||
|
|
|
|
|
|
|
|
|
|
|
|
|
|
|
|
|
|
|
|
|
|
|
|
|
|
|
|
|
|
Подача S, мм/об |
|
|
|
|
|
|
|
|
|||||
До 5 |
До 0,25 |
|
0,2-0,5 |
0,4-0,8 |
|
0,6-1,2 |
|
1,0-1,4 |
1,4 |
|
1,4 |
|
|
1,4 |
|
||||||
|
|
|
|
Подача при растачивании |
|
|
|
|
|
Таблица 40 |
|||||||||||
|
|
|
|
|
|
|
|
|
|
|
|
||||||||||
|
|
|
|
|
|
|
|
|
|
|
|
|
|
||||||||
Глубинарезания ,tмм |
|
|
|
Диаметр круглого сечения державки резца, мм |
|
|
|
||||||||||||||
|
|
|
|
|
|
|
|
|
|
|
|
|
|
|
|
|
|
||||
10 |
|
|
15 |
|
|
|
Подача |
S, мм/об |
|
30 |
|
|
40 |
|
|||||||
|
|
|
|
|
|
20 |
|
25 |
|
|
|
|
|||||||||
|
50 |
|
|
80 |
|
|
|
100 |
|
125 |
|
150 |
|
|
200 |
|
|||||
|
|
|
|
|
|
|
|
|
|
|
|
|
|
|
|
|
|
|
|
|
|
|
|
|
|
|
|
|
|
|
|
|
|
|
|
|
|
|
|
|
|
|
|
Сталь |
0,05-0,08 |
|
0,08-0,20 |
|
0,15-0,40 |
|
0,25-0,70 |
|
0,50-1,0 |
|
|
|
|
||||||||
t=2 |
|
|
|
|
|
|
|
||||||||||||||
|
|
|
|
|
|
|
|
|
|
|
|
|
|
|
|
|
|
|
|
|
|
t=3 |
|
|
0,08-0,12 |
|
0,10-0,25 |
|
0,15-0,40 |
|
0,20-0,50 |
|
0,25-0,60 |
|
|||||||||
|
|
|
|
|
|
|
|
|
|
|
|
|
|
|
|
|
|
|
|
|
|
Чугун |
0,08-0,12 |
|
0,25-0,40 |
|
0,50-0,80 |
|
0,90-1,50 |
|
|
|
|
|
|
|
|||||||
t=2 |
|
|
|
|
|
|
|
|
|
||||||||||||
|
|
|
|
|
|
|
|
|
|
|
|
|
|
|
|
|
|
|
|
|
|
t=3 |
0,05-0,08 |
|
0,15-0,25 |
0,30-0,50 |
0,50-0,90 |
|
0,90-1,20 |
|
|
|
|
||||||||||
|
|
|
|
|
|
||||||||||||||||
|
|
|
|
|
|
|
|
|
|
|
|
|
|
|
|
|
|
|
|||
Скорость резания |
|
|
|
C |
|
|
|
|
|
|
|
|
|
|
|
||||||
|
|
|
|
|
|
V |
|
|
|
, |
|
|
|
|
|
(38) |
|||||
|
|
|
|
|
|
tx S y Tm |
|
|
|
|
|
где t – глубина резания, мм; S – подача, мм/об; T – стойкость инструмента, мин (выбирается согласно табл. 42); C – постоянная резания (табл. 43); m – показатель степени (табл. 44).
65

Значение x при обработке стали 0,18, при обработке чугуна – 0,15. Значение y при обработке стали 0,27, при обработке чугуна – 0,30.
Таблица 41
Подача в зависимости от заданной шероховатости поверхности для токарного резца со значениями главного и вспомогательного углов в плане φ´ = φ = 45
Диапазонскорезаниярости, |
мин/м |
мкм, |
|
|
|
|
|
|
|
|
|
|
|
|
|
|
|
|
- Шерохова - поверх тость ности R |
|
|
|
|
|
Радиус при вершине резца r, мм |
|
|
||||||||||
|
|
|
|
|
|
|
|
|
|
|||||||||
|
|
a |
|
0,5 |
|
|
1,0 |
1,5 |
|
2,0 |
|
3,0 |
|
4,0 |
|
|||
|
|
|
|
|
|
|
|
|
|
|||||||||
|
|
|
|
|
|
|
|
|
|
|
|
|
|
|
|
|
|
|
|
|
|
|
|
|
|
|
|
|
ПодачаS, мм/об |
|
|
|
|
||||
|
|
|
|
|
|
|
|
|
|
|
|
|
|
|
|
|
|
|
|
|
80-40 |
|
– |
|
|
– |
– |
|
– |
2,8 |
|
3,2 |
|
||||
|
|
|
|
|
|
|
|
|
|
|
|
|
|
|
|
|
|
|
диапазон |
|
40-20 |
|
– |
|
|
– |
1,45 |
|
1,60 |
|
1,90 |
|
2,10 |
|
|||
|
|
|
|
|
|
|
|
|
|
|
|
|
|
|
|
|
|
|
|
20-10 |
|
0,46 |
|
0,58-0,89 |
0,67-1,05 |
|
0,73-1,15 |
0,85-1,30 |
0,93-1,45 |
||||||||
|
|
|
|
|
||||||||||||||
Весь |
|
|
|
|
|
|
|
|
|
|
|
|
|
|
|
|
|
|
|
10-5,0 |
|
0,20-0,35 |
0,25-0,44 |
0,29-0,51 |
|
0,32-0,57 |
0,37-0,65 |
0,41-0,71 |
|||||||||
|
|
|
|
|||||||||||||||
|
|
|
|
|
|
|
|
|
|
|
|
|
|
|
|
|
|
|
|
|
5,0-2,5 |
|
0,13 |
|
0,12-0,17 |
0,14-0,20 |
|
0,16-0,22 |
0,13-0,26 |
0,15-0,30 |
|||||||
|
|
|
|
|
|
|
|
|
|
|
|
|
|
|
|
|
|
|
|
|
|
|
|
|
Стойкость инструмента |
Таблица 42 |
|||||||||||
|
|
|
|
|
|
|
|
|
|
|||||||||
|
|
|
|
|
|
|
|
|
|
|
|
|
|
|
|
|
||
|
|
|
|
|
|
|
|
|
|
Сечение резца, мм |
|
|
|
|
||||
|
|
|
|
|
|
|
|
|
|
|
|
|
|
|||||
Материал резца |
|
|
16х25 |
|
20х30 |
|
25х40 |
|
40х60 |
|
60х90 |
|
||||||
|
|
|
|
|
|
|
|
|
|
|
|
|
|
|
|
|||
|
|
|
|
|
|
|
|
|
|
Стойкость резца Т, мин |
|
|
||||||
|
|
|
|
|
|
|
|
|
|
|
|
|
||||||
Быстрорежущая сталь |
|
60 |
|
|
60 |
|
90 |
|
120 |
|
150 |
|
||||||
|
|
|
|
|
|
|
|
|
|
|
|
|
|
|
||||
Металлокерамический |
|
90 |
|
|
90 |
|
120 |
|
150 |
|
180 |
|
||||||
твердый сплав |
|
|
|
|
|
|
|
|
||||||||||
|
|
|
|
|
|
|
|
|
|
|
|
|
|
|
||||
|
|
|
|
|
|
|
|
|
|
|
|
|
|
|
Таблица 43 |
|||
|
|
Безразмерное значение постоянной резания С |
|
|
||||||||||||||
|
|
|
|
|
|
|
|
|
|
|
|
|
||||||
|
Обрабатываемый материал |
|
|
|
|
|
|
С |
|
|
|
|
||||||
Сталь, стальное литье |
|
|
|
|
|
|
41,7 |
|
|
|
||||||||
Серый чугун и медные сплавы |
|
|
|
|
24,0 |
|
|
|
||||||||||
|
|
|
|
|
|
|
|
|
|
|
|
|
|
|
|
|
|
|
66

|
|
Значение m |
|
|
Таблица 44 |
||
|
|
|
|
|
|
|
|
|
|
|
|
|
|
|
|
Обрабаты- |
|
Условия |
|
m |
|
|
|
|
|
|
|
|
|
||
|
Быстроре- |
|
|
|
|
||
ваемый |
Тип резцов |
Сплав |
|
Сплав |
|
||
обработки |
|
|
|||||
материал |
|
жущая |
ТК |
|
ВК |
|
|
|
|
сталь |
|
|
|||
|
|
|
|
|
|
|
|
Сталь, |
Проходные, |
С охлаждением |
0,125 |
0,125 |
|
0,150 |
|
стальное |
подрезные, |
Без охлаждения |
0,100 |
0,125 |
|
0,150 |
|
литье, ков- |
расточные, |
|
|
|
|
|
|
Без охлаждения |
0,200 |
– |
|
0,150 |
|
||
кий чугун |
отрезные |
|
|
||||
|
|
|
|||||
|
|
|
|
|
|
|
|
|
Проходные, |
Без охлаждения |
0,100 |
0,125 |
|
0,200 |
|
Серый |
подрезные, |
|
|
|
|
|
|
Без охлаждения |
|
|
|
|
|
||
чугун |
расточные, |
0,150 |
– |
|
0,200 |
|
|
|
|
|
|||||
|
отрезные |
|
|
|
|
|
|
Норма времени на обработку данной детали Тн |
выражается следующей |
|||||
формулой: |
|
|
Тпз |
|
|
|
Тн То Твс Тдоп |
, |
(39) |
||||
n |
||||||
|
|
|
|
|
||
где То– основное (технологическое) время при точении, мин, |
|
|||||
То |
L |
i , |
|
(40) |
||
|
|
|||||
|
n S |
|
|
|||
здесь L – расчетная длина обработки в направлении подачи, мм, |
|
|||||
L l l1 l2 l3 , |
|
(41) |
где l – длина обрабатываемой поверхности, мм; l1– длина врезания инструмента, мм; l2– длина подхода и перебега инструмента, мм (2 – 5 мм); l3 – длина проходов при взятии пробных стружек, мм (5 – 8 мм); i – число проходов.
При точении l1 t ctg , при расчетах φ главный угол в плане можно принять равным 45 , тогда
l1 t.
Твс – вспомогательное время на установку и снятие детали со станка, пуск и остановку станка, подвод и отвод режущего инструмента, измерение размеров и т.п. Твс при точении выбирается из табл. 45.
Основное То и вспомогательное Твс время (см. табл. 45) в сумме составляют оперативное время Топ.
67

|
|
Топ То Твс . |
|
|
|
|
(42) |
||||
Дополнительное время Тдоп |
при точении можно принять 3% от Топ |
||||||||||
(в учебных целях). |
|
|
|
|
Тпз при |
|
|
|
|
||
Подготовительно-заключительное время |
партии |
деталей |
|||||||||
n = 7–22 можно принять 13–16 мин (в учебных целях). |
|
|
|
|
|||||||
|
|
|
|
|
|
|
|
|
Таблица 45 |
||
|
Вспомогательное время при точении, мин |
|
|
||||||||
|
|
|
|
|
|
|
|
|
|
|
|
Способ уста- |
|
|
|
Масса заготовки, кг |
|
|
|
|
|||
новки обраба- |
|
|
|
|
|
|
|
|
|
|
|
|
|
|
|
|
|
|
|
|
|
|
|
тываемой за- |
до 1 |
до 3 |
|
до 5 |
|
до 8 |
|
до 12 |
|
до 20 |
|
готовки |
|
|
|
|
|
|
|
|
|
|
|
В центрах: |
0,35 |
0,44 |
|
0,54 |
|
0,64 |
|
0,72 |
|
0,87 |
|
с хомутиком |
|
|
|
|
|
||||||
с люнетом |
0,44 |
0,5 |
|
0,64 |
|
0,78 |
|
0,91 |
|
1,12 |
|
|
|
|
|
|
|
|
|
|
|
|
|
На гладкой |
0,42 |
0,53 |
|
0,67 |
|
0,79 |
|
0,91 |
|
1,1 |
|
оправке |
|
|
|
|
|
||||||
|
|
|
|
|
|
|
|
|
|
|
|
На оправке |
0,53 |
0,61 |
|
0,7 |
|
0,75 |
|
0,8 |
|
0,86 |
|
с гайкой |
|
|
|
|
|
||||||
|
|
|
|
|
|
|
|
|
|
|
|
В патроне: |
0,2 |
0,22 |
|
0,27 |
|
0,33 |
|
0,38 |
|
0,39 |
|
без выверки |
|
|
|
|
|
||||||
|
|
|
|
|
|
|
|
|
|
|
|
|
|
|
|
|
|
|
|
|
|
|
|
с выверкой |
0,4 |
0,47 |
|
0,56 |
|
0,63 |
|
0,7 |
|
0,84 |
|
с люнетом |
|
|
|
|
|
|
|
|
|
|
|
0,4 |
0,41 |
|
0,53 |
|
0,6 |
|
0,67 |
|
0,78 |
|
|
|
|
|
|
|
|
|
|
|
|
|
|
Выбор режимов резания при шлифовании: 1. Шлифование с продольной подачей.
Глубина шлифования: t = (0,005–0,015) мм/проход – при круглом чистовом шлифовании; t = (0,010–0,025) – при черновом шлифовании.
Число проходов
i |
z2 |
, |
(43) |
|
|||
|
t |
|
|
где z2 – припуск на шлифование (на сторону), мм. |
|
||
Продольная подача S, мм/об: |
|
||
S SД BК , |
(44) |
где SД – продольная подача в долях ширины круга на один оборот детали;
BК – ширина шлифовального круга, мм, BК =20–60 мм. При круглом шлифовании S зависит от вида шлифования:
68

1) S = (0,3 – 0,5) ·BК – при черновом шлифовании деталей, изготовленных из любых материалов диаметром меньше 20 мм;
2) S = (0,6 – 0,7) ·BК – при черновом шлифовании деталей, изготовленных из любых материалов диаметром больше 20 мм;
3)S = (0,75 – 0,85) ·BК – для деталей из чугуна;
4)S = (0,2 – 0,3) ·BК – при чистовом шлифовании независимо от мате-
риала и диаметра детали.
Окружная скорость детали VД : VД = 20–80 м/мин (для черного шлифо-
вания); VД = 2–5 м/мин (для чистого шлифования).
Число оборотов детали (частота вращения) определяется по формуле
(37).
Скорость продольного перемещения стола VСТ , м/мин,
VСТ S nД .
1000
Основное время при шлифовании
L i
To nД S K ,
где L – длина продольного хода стола. При шлифовании на проход, мм,
L = l + (0,2 – 0,4) ·BК .
При шлифовании в упор, мм,
L = l – (0,4 – 0,6) ·BК ,
(45)
(46)
(47)
(48)
где l – длина шлифуемой поверхности, мм; K – коэффициент точности (коэффициент выхаживания, равный при черновом шлифовании 1,1; при чис-
товом – 1,4).
2. Шлифование с поперечной подачей (методом врезания).
Врезное шлифование является производительным методом обработки. Оно осуществляется с поперечной подачей до достижения необходимого размера поверхности (продольная подача отсутствует). Шлифовальный круг перекрывает всю ширину (длину) обрабатываемой поверхности детали.
Основное время при поперечном шлифовании
То |
z2 |
, |
(49) |
|
nД Sпоп |
||||
|
|
|
||
где Sпоп – поперечная подача при |
обработке детали, |
Sпоп = 0,0025– |
||
0,02 мм/об. |
|
|
|
69