
- •ВВЕДЕНИЕ
- •1. ЦЕЛЬ И ЗАДАЧИ КУРСОВОЙ РАБОТЫ
- •3. РАСЧЁТНАЯ ЧАСТЬ КУРСОВОЙ РАБОТЫ
- •3.1.1. Анализ исходных данных
- •3.1.3. Выбор технологических баз и схем установки заготовки
- •3.1.6. Расчет и назначение припусков и операционных размеров
- •3.1.7. Расчет режимов резания
- •3.1.8. Определение норм штучного времени
- •3.1.9. Расчет экономической эффективности ТП
- •3.1.10. Оформление технологических документов
- •3.2. Разработка технологии восстановления детали
- •3.2.4. Сопутствующая технологическая документация
- •3.2.6. Оформление технологической документации
- •3.3. Проектирование и расчёт приспособлений
- •3.3.2. Состав приспособления
- •3.3.4. Расчет составляющих силы резания
- •3.3.5. Расчет усилия зажима заготовки
- •3.3.6. Расчет рычажных зажимных механизмов
- •4. ТРЕБОВАНИЯ К ОФОРМЛЕНИЮ КУРСОВОЙ РАБОТЫ
- •4.1. Содержание пояснительной записки
- •4.2. Требования к оформлению пояснительной записки
- •4.2.1. Общие положения
- •4.2.2. Требования к текстовым документам
- •4.3.2. Требования к оформлению сборочного чертежа
- •Библиографический список
- •Приложение 1
- •Приложение 3
- •Приложение 6
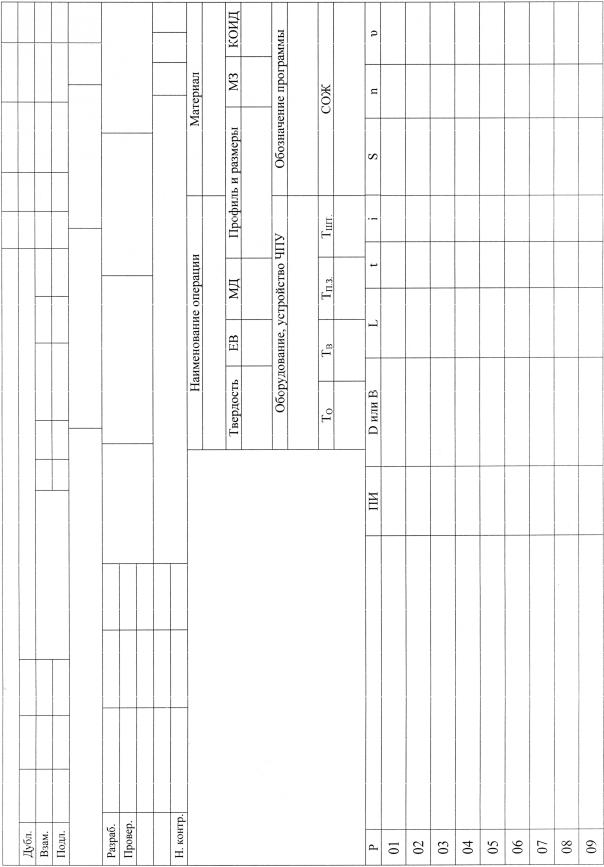
Приложение 3
105

Приложение 4
106

107
Министерство образования и науки РФ
Федеральное государственное бюджетное образовательное учреждение высшего профессионального образования «Сибирская государственная автомобильно-дорожная академия (СибАДИ)»
Кафедра “ Эксплуатация и сервис транспортно-технологических машин и комплексов в строительстве ”
Технологический процесс
к курсовой работе
Восстановление вала 161.54.001
Автор курсовой работы
Руководитель
Омск 20__
5 Приложение

Приложение 6
В качестве примера рассмотрим проектирование технологического процесса механической обработки вала приводного БШ.00.00.001.
Вал приводной предназначен для передачи крутящего момента с выходного вала редуктора привода непосредственно на буровой инструмент бурильно-крановой машины.
6.1 Исходные данные
рабочий чертеж детали;
технические требования, регламентирующие точность;
параметры шероховатости поверхности;
материал детали – сталь 40 Х.
Рабочий чертёж вала приводного БШ.00.00.001 представлен на рисунке П 6.1.
Рисунок П 6.1 – Рабочий чертеж приводного вала БШ.00.00.001
6.2 Выбор типа производства
Тип производства определяем в зависимости от годовой программы и массы заготовки.
Все заготовки делятся на 3 группы:
легкие (до 5 кг);
средние (до 20 кг);
тяжелые (более 20 кг).
108
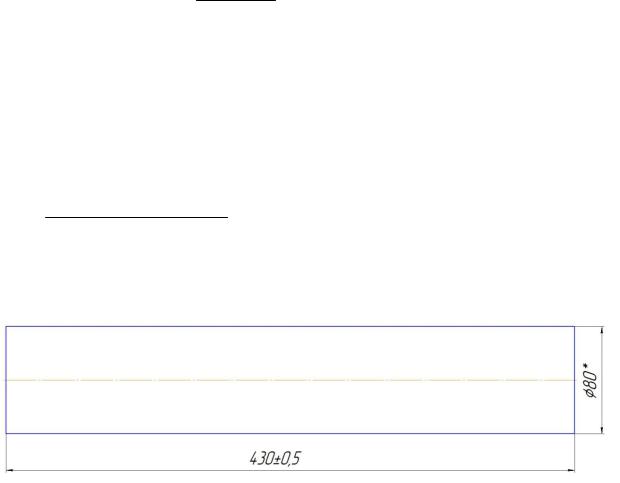
Массу заготовки mЗ, кг, определим по формуле
mЗ |
d |
2 |
l , |
|
|
|
|
|
(П 6.1) |
||
|
|
||||
|
4 |
|
|
|
где d – диаметр заготовки, d = 0,08 м; l – длина заготовки, l=0,43 м;
ρ – плотность стали, ρ = (7,7 – 7,9) ∙ 103 кг/м3.
mЗ 3,14 0,082 0,43 7,9 103 17,1кг. 4
Исходя из годовой программы и массы заготовки, выбираем единичный тип производства.
6.3 Выбор заготовки
Для единичного типа производства детали выбираем заготовку из сортового проката горячекатаной стали, сечением круг и диаметром 80 мм
80ГОСТ 2590 2006 Круг 40ХГТ ГОСТ4543 71 .
Эскиз заготовки детали представлен на рисунке П 6.2.
Рисунок П 6.2 – Эскиз заготовки детали
6.4 Расчет припусков на обработку
Заданные припуски на все обрабатываемые поверхности сведены в таблицу П 6.1.
109
Таблица П 6.1 – Промежуточные и общий припуски
В миллиметрах
Обозначение |
|
Обрабатываемые поверхности |
|
|
|||
припусков |
|
|
|
|
|
|
|
1 |
2 |
3 |
4 |
|
5 |
6 |
|
|
|
||||||
|
|
|
|
|
|
|
|
Zобщ |
10 |
4,2 |
12 |
5,2 |
|
4,1 |
3,2 |
|
|
|
|
|
|
|
|
Zчерн. точ |
8,8 |
4,1 |
10,8 |
5,1 |
|
2,9 |
3,2 |
|
|
|
|
|
|
|
|
Zчист. точ |
1 |
– |
1 |
– |
|
1 |
– |
|
|
|
|
|
|
|
|
Zшлифование |
0,2 |
0,1 |
0,2 |
0,1 |
|
0,2 |
– |
|
|
|
|
|
|
|
|
6.5 Назначение маршрута механической обработки
Исходя из анализа типового процесса изготовления ступенчатых шлицевых валов, назначаем следующий маршрут изготовления: /1/
отрезка заготовки из сортового круглого проката;
подрезка торцов;
черновое точение;
чистовое точение;
сверление сквозных отверстий;
фрезерование шлицов;
нарезание резьбы;
шлифование наружных шлицов и опорных шеек.
6.6 Проектирование операций чернового точения
Эскиз операции чернового точения представлен на рисунке П 6.3.
В операцию чернового точения включаем следующие технологические переходы:
подрезка торцов в размере 427h11 и зацентровки заготовки;
точение поверхности 1 до диаметра 62,4h11 мм, длиной l1 = 170 мм, односторонним припуском z1 = 8,8 мм, в 2 прохода с наибольшей глубиной
резания tmax = 4,4 мм;
точение поверхности 2 до диаметра 54,2h11 мм, длиной l2 = 130 мм, односторонним припуском z2 = 4,1 мм, в 2 прохода с наибольшей глубиной резания tmax = 2,05 мм;
точение поверхности 3 до диаметра 58,4h11 мм, длиной l3 = 242 мм, односторонним припуском z3 = 10,8 мм, в 3 прохода с наибольшей глуби-
ной резания tmax = 3,6 мм;
110
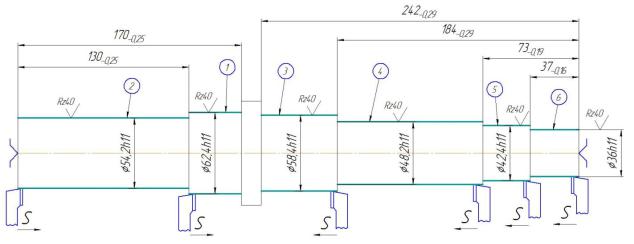
точение поверхности 4 до диаметра 48,2h11 мм, длиной l4 = 184 мм, односторонним припуском z4 = 5,1 мм, в 3 прохода с наибольшей глубиной резания tmax = 1,7 мм;
точение поверхности 5 до диаметра 42,4h11 мм, длиной l5 = 73 мм, односторонним припуском z5 = 2,9 мм, в 1 проход с наибольшей глубиной резания tmax = 2,9 мм;
точение поверхности 6 до диаметра 36h11 мм, l6 = 37 мм, односторонним припуском z6 = 3,2 мм, в 1 проход с наибольшей глубиной резания tmax = 3,2 мм.
Рисунок П 6.3 – Эскиз операции чернового точения
Для чернового точения выбираем токарный станок 16К20 с наибольшей длиной обрабатываемой заготовки 1 000 мм. Инструмент – резец проходной упорный, прямой с пластикой из твердого сплава Т15К6 по ГОСТ 18879-73. Параметры сведены в таблицу П 6.2.
Таблица П 6.2 – Параметры резца
Главный угол в плане |
45º |
|
|
Передний угол |
0º |
|
|
Угол наклона главного лезвия |
5º |
Радиус при вершине резца r |
0,5 мм |
Стойкость резца |
60 мин |
Величину подачи для всех поверхностей принимаем S = 0,6 мм/об /1/. Скорость резания Vp, м/мин, определим по формуле
111

Vр |
CV |
kV , |
(П 6.2) |
Tm tx S y |
где CV – постоянная резания, CV = 350 /1/;
Т – период стойкости резца, принимаем Т = 60 мин; t – глубина резания, t = 4,4 мм;
S – подача инструмента, мм/об;
m, x, y – показатели степени, m = 0,2; x = 0,15; y =0,35 /1/;
kV – общий поправочный коэффициент, определяется из следующего условия:
kV kMV kNV kUV , |
(П 6.3) |
здесь kMV – поправочный коэффициент, учитывающий материал заготовки, принимаем для материала Сталь 40 ХГТ kMV = 0,7;
kNV – поправочный коэффициент, учитывающий материал, состояние поверхности заготовки, принимаем kNV = 0,9;
kUV – поправочный коэффициент, учитывающий состояние инструмента, принимаем kUV = 1,0.
Следовательно, скорость резания при S = 0,6 мм/об будет следующей:
350 0,7 0,9 1,0
Vр 600,2 4,40,15 0,60,35 93,1 м/мин.
По аналогии определим Vp для остальных поверхностей, результаты сводим в таблицу П 6.3.
Таблица П 6.3 – Скорости резания поверхностей
Поверхность |
1 |
2 |
3 |
|
4 |
5 |
6 |
|
t, мм |
4,4 |
2,05 |
3,6 |
|
1,7 |
2,9 |
3,2 |
|
Vp, м/мин |
93,1 |
104,39 |
95,94 |
|
107,36 |
99,1 |
97,65 |
|
Частоту вращения n, мин–1, заготовки определяем по формуле |
|
|||||||
|
|
n |
1000 Vp |
, |
|
|
(П 6.4) |
|
|
|
|
|
|
|
D
где D – диаметр ступени заготовки, мм.
n 1000 93,1 370,62 мин–1. 3,14 80
112

По аналогии определим частоты вращения для обработки остальных поверхностей, результаты сводим в таблицу П 6.4.
Таблица П 6.4 – Расчетная частота вращения шпинделя станка
Поверхность |
1 |
2 |
3 |
4 |
5 |
6 |
Vp, м/мин |
93,1 |
104,39 |
95,94 |
107,36 |
99,1 |
97,65 |
n, мин–1 |
370,62 |
415,57 |
381,93 |
427,39 |
394,51 |
388,74 |
Принимаем ближайшее паспортное значение частоты вращения шпинделя станка n = 315 мин–1.
Определим основное время на обработку поверхности 1 tо1, мин, по формуле
tо1 |
l i |
, |
(П 6.5) |
|
|||
|
S n |
|
где l – длина обрабатываемой поверхности, мм; i – число проходов.
170 2
tо1 0,6 315 1,80 мин.
По аналогии определим to для остальных поверхностей, результаты сводим в таблицу П 6.5.
Таблица П 6.5 – Время, затраченное на обработку поверхности
Поверхность |
1 |
2 |
3 |
4 |
5 |
6 |
to, мин |
1,80 |
1,38 |
3,84 |
2,92 |
0,39 |
0,20 |
Определим основное временя на операцию tо, мин, по формуле |
|
|||||
|
|
|
6 |
|
|
|
|
|
tо tоi . |
|
|
(П 6.6) |
|
|
|
|
i 1 |
|
|
|
tо 1,80 1,38 3,84 2,92 0,39 0,2 10,44 мин.
Определим штучно-калькуляционное время Тшт.к, мин, по формуле
Т |
шт.к |
t |
o |
t |
в |
t |
д |
|
tпз |
, |
(П 6.7) |
|
n |
||||||||||||
|
|
|
|
|
|
|
где tв – вспомогательное время на установку и снятие детали со станка, пуск и остановку детали, подвод и отвод режущего инструмента, измерение размерови т.п.,дляданногостанка принимаемtв =0,87мин; tд – дополнительное время при точении, мин, определяется по формуле
113
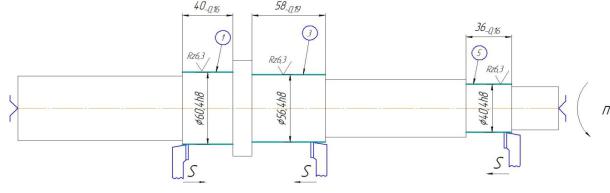
tд = 3%(tв + tо); |
(П 6.8) |
||
tд = 0,03 ∙ (0,87 + 10,44) = 0,34 мин; |
|
||
tпз – подготовительно-заключительное время при партии |
деталей |
||
n = 7–22 можно принять 13–16 мин. |
|
||
Тшт.к 10,44 0,87 0,34 |
15 |
15,06 мин. |
|
|
|
||
4 |
|
|
|
6.7 Проектирование операции чистового точения |
|
Эскиз операции чистового точения представлен на рисунке П 6.4.
Рисунок П 6.4 – Эскиз операции чистового точения
Для чистового точения выбираем станок 16К20. Инструмент – резец проходной упорный, прямой с пластикой из твердого сплава Т15К6 по ГОСТ 18879-73.
В операцию чистового точения включаем следующие технологические переходы:
точение поверхности 1 до диаметра 60,4h8 мм, длиной l1 = 40 мм, односторонним припуском z1 = 1 мм, в 2 прохода с наибольшей глубиной резания tmax = 0,5 мм;
точение поверхности 3 до диаметра 56,4h8 мм, длиной l3 = 58 мм, односторонним припуском z3 = 1 мм, в 2 прохода с наибольшей глубиной резания tmax = 0,5 мм;
точение поверхности 5 до диаметра 40,4h8 мм, длиной l5 = 36 мм, односторонним припуском z5 = 1 мм, в 2 прохода с наибольшей глубиной резания tmax = 0,5 мм.
114
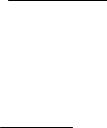
Исходя из требований к точности и шероховатости поверхности принимаем величину подачи S = 0,15 мм/об.
По формуле (П 6.2) определим скорости резания при S = 0,15 мм/об и t = 0,5 мм.
Vр1 Vр3 Vр5 |
350 0,7 0,9 1,0 |
209,56 м/мин. |
600,2 0,50,15 0,150,35 |
По формуле (П 6.4) определим частоту вращения заготовки.
n1 n3 n5 1000 209,56 834,24 мин–1. 3,14 80
Принимаем n = 800 мин–1.
По формуле (П 6.5) определим основное время на обработку поверхности 1.
40 2
tо1 0,15 800 0,67 мин.
По аналогии определим to для остальных поверхностей, результаты сводим в таблицу П 6.6.
Таблица П 6.6 – Время, затраченное на обработку поверхности
Поверхность |
1 |
3 |
5 |
to, мин |
0,67 |
0,97 |
0,6 |
Определим основное время на операцию по формуле (П 6.6).
tо 0,67 0,97 0,6 2,24 мин.
Определим для штучно-калькуляционного времени дополнительное время по формуле (П 6.8).
tд = 0,03 ∙ (0,87 + 2,24) = 0,09 мин.
Подсчитаем штучно-калькуляционное время по формуле (П 6.7).
Тшт.к |
2,24 0,87 0,09 |
15 |
6,95 мин. |
|
|||
|
4 |
|
115
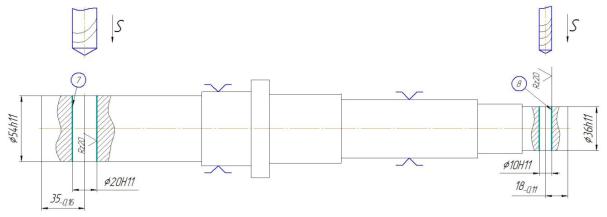
6.8 Проектирование операции сверления
Эскиз операции сверления представлен на рисунке П 6.5.
Рисунок П 6.5 – Эскиз операции сверления
В операцию сверления включаем следующие технологические переходы:сверление отверстия радиального диаметром 20 мм, глубиной l1 = 54 мм;сверление отверстия радиального диаметра 10 мм, глубиной
l2 = 26 мм.
Для радиального сверления выбираем станок вертикально-сверлильный 2Н125. Инструмент – сверло спиральное с цилиндрическим хвостом по ГОСТ 886-77, материал режущей части сверла – сталь быстрорежущая Р6М5.
Исходя из диаметра и глубины отверстия определяем величину подачи:
S = 0,3 мм/об /1/.
Скорость резания Vp, м/мин, определим по формуле
|
|
|
C Dq |
|
|
|
V |
|
|
V |
k |
, |
(П 6.9) |
|
Tm S y |
|||||
|
р |
|
V |
|
где CV – постоянная резания, CV = 9,8 /1/;
Т – период стойкости резца, принимаем Т = 45 мин; D – диаметр отверстия, мм;
S – подача инструмента, мм/об;
m, y, q – показатели степени, m=0,2; y=0,5; q=0,4 /1/;
kV – общий поправочный коэффициент,определяется по формуле (П 6.3).
Vр7 |
|
9,8 200,4 |
0,63 |
17,45 |
м/мин; |
||
450,2 0,30,5 |
|
||||||
|
|
|
|
Vр8 |
|
9,8 100,4 |
0,63 |
13,23 |
м/мин. |
||
450,2 0,30,5 |
|
||||||
|
|
|
|
116
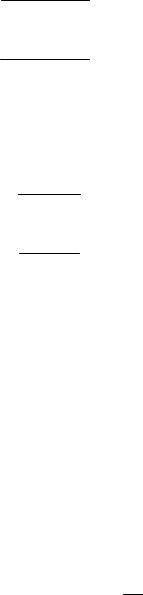
По формуле (П 6.4) определим частоту вращения инструмента.
n7 1000 17,45 278 мин–1; 3,14 20
n8 1000 13,23 422 мин–1. 3,14 10
Примем n7 и n8 равными соответственно 270 мин–1 и 384 мин–1.
Поформуле (П6.5)определим основное времянасверлениеотверстий7 и8.
54 1
tо7 0,3 270 0,67 мин;
36 1
tо8 0,3 384 0,32 мин.
Определим вспомогательное и подготовительно-заключительное вре-
мя: tв = 1,2 мин; tпз = 14 мин /2/.
Определим основное временя на операцию по формуле (П 6.6). tо 0,32 0,67 0,99 мин.
Определим для штучно-калькуляционного времени дополнительное время по формуле (П 6.8).
tд = 0,03 ∙ (1,2 + 0,99) = 0,07 мин.
Подсчитаем штучно-калькуляционное время по формуле (П 6.7).
Тшт.к 0,99 1,2 0,07 14 5,76 мин. 4
6.9 Проектирование операции фрезерования шлицов Эскиз операции сверления представлен на рисунке П 6.6.
117
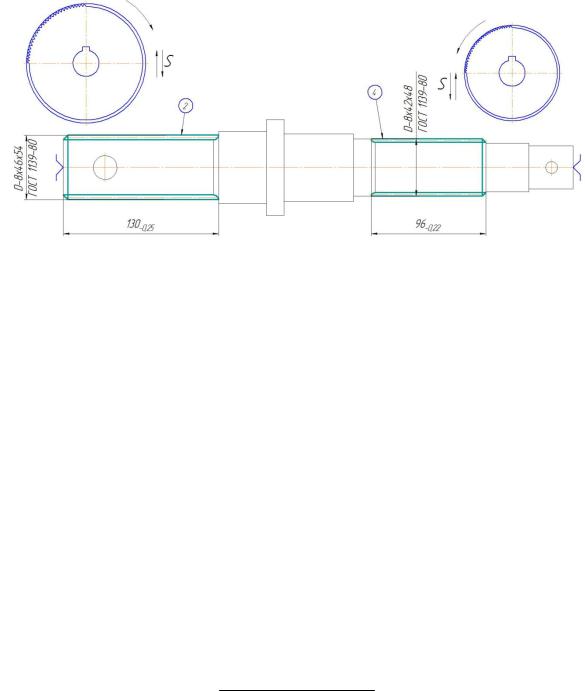
Рисунок П 6.6 – Эскиз операции фрезерования шлицов
В шлицефрезерную операцию включаем следующие технологические переходы:
фрезерование дисковой пазовой фрезой шлицевых пазов поверхности 2 D-8×46×54h7, кол-во пазов 8, ширина пазов B2 = 9 мм, глубина – h2 = 4 мм, длина l2 = 130 мм, i = 1;
фрезерование дисковой пазовой фрезой шлицевых пазов поверхности 4 D-8×42×48h7, кол-во пазов 8, ширина пазов B4 = 8 мм, глубина – h4 = 3 мм, длина l4 = 96 мм, i = 1.
Определим предварительно параметры инструмента: фреза шлицевая по ГОСТ 2679-73, стойкость инструмента Т = 90 мин, диаметры фрезы D1 = 100 мм, D2 = 80 мм, число зубьев соответственно Z1 = 20; Z2 = 18, материал режущей части – сталь быстрорежущая 6РМ5.
Выбираем горизонтально-фрезерный универсальный станок 6Р80.
С учетом обрабатываемого материала определим величину подачи на зуб фрезы: SZ = 0,1 мм/зуб /1/.
Скорость резания Vp, м/мин, определим по формуле
|
C Dq |
|
|
Vр |
V |
kV , |
(П 6.10) |
Tm tx Szy Bu Z p |
где CV – постоянная резания, CV = 68,5 /1/; В – ширина фрезы, мм;
D – диаметр фрезы, мм;
Z – подача инструмента, мм/об;
m, y, q, x, u, p – показатели степени, m = 0,2; y = 0,2; q = 0,25; x = 0,3; u = 0,1; p = 0,1 /1/;
kV – общий поправочный коэффициент,определяется по формуле (П 6.3).
118

Vр2 |
|
|
68,5 1000,25 0,63 |
24,7 |
м/мин; |
||
|
80,3 0,10,2 |
100,1 |
200,1 |
||||
|
900,2 |
|
|
Vр4 |
|
68,5 800,25 |
0,63 |
27,8 |
м/мин. |
||
900,2 50,3 0,10,2 |
80,1 |
180,1 |
|||||
|
|
|
|
По формуле (П 6.4) определим частоту вращения фрезы для фрезерова-
ния поверхностей 2 и 4. |
|
|
|
|
|
n2 |
|
1000 24,7 |
78,4 мин–1; |
||
|
|
||||
|
|
|
3,14 100 |
||
n4 |
|
1000 27,8 |
110,3 мин–1; |
||
|
|||||
|
|
|
3,14 80 |
Определим основное время на фрезерование шлицов поверхности 2 и 4 tо, мин, по формуле
tо |
l i |
, |
(П 6.11) |
|
|||
|
SМ |
|
где SM – минутная подача инструмента, мм/мин, определяется по формуле
SM n Z SZ . |
(П 6.12) |
SM 2 78 20 0,1 156 мм/мин;
SM4 110,3 18 0,1 198,54 мм/мин.
150 8
tо2 156 7,7 мин;
87 10
tо4 198,54 4,4 мин.
Определим вспомогательное и подготовительно-заключительное время tв = 4,1 мин; tпз = 23,0 мин /2/.
Определим основное временя на операцию по формуле (П 6.6).
tо 7,7 4,4 12,1 мин.
Определим для штучно-калькуляционного времени дополнительное время по формуле (П 6.8).
tд = 0,03 ∙ (4,1 + 12,1) = 0,5 мин.
Подсчитаем штучно-калькуляционное время по формуле (П 6.7).
Тшт.к |
12,1 4,1 0,5 |
23 |
22,45 мин. |
|
|||
|
4 |
|
119
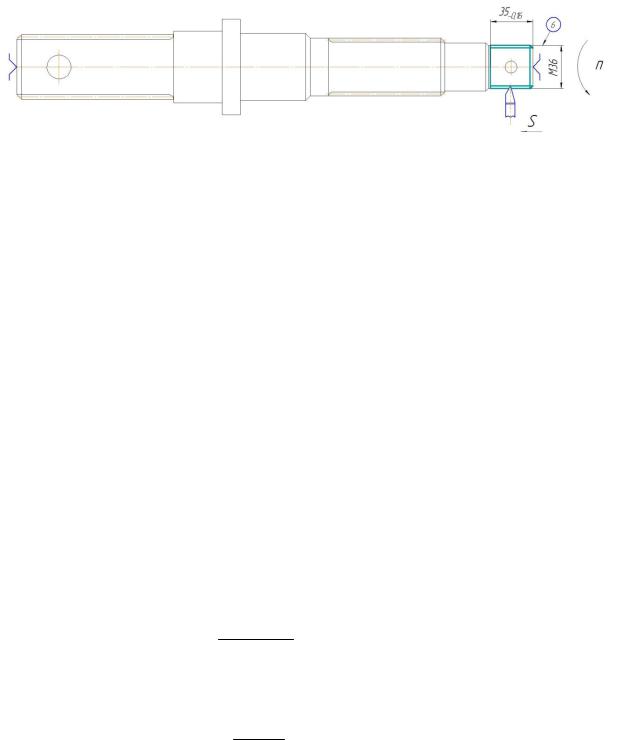
6.10 Проектирование операции резьбонарезания
Эскиз операции резьбонарезания представлен на рисунке П 6.7.
Рисунке П 6.7 – Эскиз операции резьбонарезания
Операция резьбонарезания состоит из одного основного технологического перехода – нарезания резьбы М36 с крупным шагом 4 мм.
Нарезание резьбы произведем резьбовым резцом на токарном станке
16К20.
Для метрической резьбы с крупным шагом 4 мм определяем число рабочих ходов при нарезании резьбы резьбовым резцом с пластинами из твердого сплава Т15К6 с количеством проходов i = 7 (5 черновых и 2 чистовых) /1/.
Определим скорость резания Vp, м/мин, по формуле /1/
Vр |
D f |
, |
(П 6.13) |
|
|||
|
1000 P |
|
где D – номинальный диаметр резьбы, D = 36 мм;
f – ширина виточка для резца, принимаем f = 1,5 мм;– время на отвод резца, = 0,04 мин; Р – шаг резьбы, Р = 4 мм.
Vр |
3,14 36 1,5 |
1,06 м/мин. |
|
1000 0,04 4 |
|||
|
|
Определим по формуле (П 6.4) частоту вращения заготовки.
n 1000 1,06 9,38 мин–1. 3,14 36
Окончательно принимаем n = 12,5 мин–1.
По формуле (П 6.5) определим основное время резьбонарезания.
35 7
tо 4 12,5 4,9 мин.
Определим вспомогательное и подготовительно-заключительное вре-
мя: tв = 1,9 мин; tпз = 10,0 мин /2/.
120
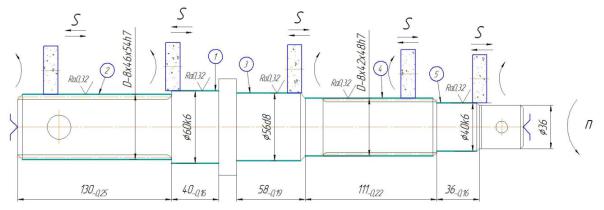
Определим для штучно-калькуляционного времени дополнительное время по формуле (П 6.8).
tд = 0,03 ∙ (1,9 + 4,9) = 0,2 мин.
Подсчитаем штучно-калькуляционное время по формуле (П 6.7).
Тшт.к |
4,9 1,9 0,2 |
10 |
9,5 мин. |
|
|||
|
4 |
|
6.11 Проектирование операции шлифования
Эскиз операции шлифования представлен на рисунке П 6.8.
Воперациюшлифования включаем следующие технологическиепереходы:круглое шлифование поверхности 1 диаметром 60k6 мм с односторонним припуском z2 = 0,2 мм, в 8 проходов с наибольшей глубиной резания
tmax = 0,025 мм, длиной поверхности l1 = 40 мм, шероховатость Ra 0,32;
крупное шлифование поверхности 2 выступов шлицов D-8×46×54h7
содносторонним припуском z2 = 0,1 мм, в 4 прохода с наибольшей глуби-
ной резания tmax = 0,025 мм, длина поверхности l2 = 130 мм, диаметр поверхности 54h7 мм, шероховатость Ra 0,32;
круглое шлифование поверхности 2 диаметром 56d8 мм с односторонним припуском z2 = 0,2 мм, в 8 проходов с наибольшей глубиной резания tmax = 0,025 мм, длиной поверхности l3 = 58 мм, шероховатость Ra 0,32;круглое шлифование поверхности 4 выступов шлицов D-8×42×48h7 с односторонним припуском z2 = 0,1 мм, в 4 прохода с наибольшей глубиной резания tmax = 0,025 мм, длиной поверхности l4 = 111 мм, диаметр поверх-
ности 48h7 мм, шероховатость Ra 0,32;
круглое шлифование поверхности 5 диаметром 40k6 мм с односторонним припуском z2 = 0,2 мм, в 8 проходов с наибольшей глубиной резания tmax = 0,025 мм, длиной поверхности l5 = 36 мм, шероховатость Ra 0,32.
Рисунок П 6.8 – Эскиз операции шлифования
121

Для круглого наружного шлифования требуемой шероховатости выбираем шлифовальный круг на керамической связке, тип круга ПП (прямой профиль), зернистость 50-М28, диаметр круга 100 мм, ширина круга 32 мм, диаметр отверстия 20 мм (ГОСТ 2424-83).
Для операции шлифования выбираем станок круглошлифовальный
3М151Ф2.
Определим основные режимы круглого наружного шлифования /1/:
продольная подача S1 = S2 = S3 = S4 = S5 = 24 мм/об;
скорость заготовки V1 = V2 = V3 = V4 = V5 = 20 м/мин;
частота заготовки n = 64 об/мин;
скорость круга VK = 30 м/с.
По формуле (П 6.5) определим основное время на шлифование поверхности.
40 8
tо 24 64 0,21 мин.
По аналогии определим to для остальных поверхностей, результаты сводим в таблицу П 6.7.
Таблица П 6.7 – Время, затраченное на обработку поверхности
Поверхность |
1 |
2 |
3 |
4 |
5 |
to, мин |
0,21 |
0,34 |
0,3 |
0,29 |
0,19 |
Определим вспомогательное и подготовительно-заключительное вре-
мя: tв = 10,1 мин; tпз = 9,0 мин /2/.
Определим основное временя на операцию по формуле (П 6.6).
tо 0,21 0,34 0,3 0,29 0,19 1,33 мин.
Определим для штучно-калькуляционного времени дополнительное время по формуле (П 6.8).
tд = 0,03 ∙ (10,1 + 1,33) = 0,34 мин.
Подсчитаем штучно-калькуляционное время по формуле (П 6.7).
Тшт.к 1,33 10,1 0,34 |
9 |
14,02 мин. |
|
||
4 |
|
6.12 Расчет себестоимости изготовления вала приводного
Себестоимость является экономическими критерием и представляет сумму затрат, приходящихся на единицу продукции. Себестоимость восстановления детали, С, руб., определяется по формуле
i |
|
|
1 |
1 2 |
, |
|
|
C M З K |
Д |
|
(П 6.14) |
||||
|
|||||||
о |
|
|
100 |
|
|||
1 |
|
|
|
|
|
122
где М – стоимость материала заготовки, руб.;
Зо – основная заработная плата рабочего на i-й операции, руб.; i – число операций данного технологического процесса;
α1 – процент накладных расходов (цеховые и общезаводские расходы), α1 = 200 – 250 % и может достигать 600 %;
α2 – процент начислений на социальные расходы, α2 = 36 – 38 %;
KД – коэффициент дополнительной заработной платы, в учебных целях можно принять KД = 1,15.
Затраты на материал заготовки определяются ориентировочно произведением массы заготовки на стоимость единицы массы сортового проката (штампованной или литой заготовки), которая составляет 49,0 руб. за килограмм для стали 40Х.
Основная заработная плата Зо, руб., определяется по формуле
Зо Тшт.к t k, |
(П 6.15) |
где Тшт.к – штучно-калькуляционное время операции, ч;
t – часовая тарифная ставка рабочего первого разряда, определяется отношением минимального уровня оплаты труда к среднемесячному фонду рабочего времени, например: t = 5554/170 = 32,67 руб.;
k – тарифный коэффициент соответствующего разряда.
Для определения основной заработной платы составляем расчетную таблицу П 6.8.
Таблица П 6.8 – Расчет основной заработной платы рабочих
|
Тшт.к |
|
|
|
|
Тарифный |
Основная |
||
Наименование опе- |
|
Разряд |
|
|
заработная |
||||
|
|
|
коэффициент |
||||||
рации |
|
|
|
|
|
|
плата Зо, |
||
|
|
|
|
|
|
k |
|
||
мин |
ч |
|
|
|
|
|
|||
|
|
|
|
|
|
|
руб. |
||
Черновое точение |
15,06 |
0,25 |
|
3 |
|
|
1,69 |
|
13,8 |
Чистовое точение |
6,95 |
0,12 |
|
4 |
|
|
1,91 |
|
7,5 |
Сверление |
5,76 |
0,10 |
|
3 |
|
|
1,69 |
|
5,5 |
|
|
|
|
|
|
|
|
|
|
Фрезерование |
24,71 |
0,41 |
|
4 |
|
|
1,91 |
|
25,6 |
|
|
|
|
|
|
|
|
|
|
Резьбонарезание |
11,19 |
0,20 |
|
3 |
|
|
1,69 |
|
11,0 |
Шлифование |
14,02 |
0,24 |
|
4 |
|
|
1,91 |
|
15,0 |
|
|
|
|
|
|
|
|
|
6 |
|
|
|
|
|
|
|
|
|
Зо 78,4 |
|
|
|
|
|
|
|
|
|
1 |
По формуле (П 6.14) определим себестоимость изготовления вала. |
|||||||||
|
|
|
300 36 |
|
|
|
|
||
C 837,9 78,4 1,15 1 |
|
|
1231,0 |
руб. |
|
||||
100 |
|
||||||||
|
|
|
|
|
|
|
123

Учебное издание
ТЕХНОЛОГИЯ
ПРОИЗВОДСТВА И РЕМОНТА
ПТСДМ И ИХ ЭЛЕМЕНТОВ
Методические рекомендации для выполнения курсовой работы
Составители:
Сергей Владимирович Мельник, Александр Иванович Злобин, Людмила Анатольевна Шапошникова
***
Редактор И.Г. Кузнецова
***
Подписано к печати 29.09.2014 Формат 60 90 1/16. Бумага писчая Оперативный способ печати Гарнитура Times New Roman Усл. п. л. 7,75
Тираж 100 экз. Заказ № Цена договорная
***
Редакционный отдел ИПЦ СибАДИ 644080, г. Омск, ул. 2-я Поселковая, 1
______________________________________________
Отпечатано в отделе ОП ИПЦ СибАДИ 644080, г. Омск, пр. Мира, 5
124