
- •ВВЕДЕНИЕ
- •1. ЦЕЛЬ И ЗАДАЧИ КУРСОВОЙ РАБОТЫ
- •3. РАСЧЁТНАЯ ЧАСТЬ КУРСОВОЙ РАБОТЫ
- •3.1.1. Анализ исходных данных
- •3.1.3. Выбор технологических баз и схем установки заготовки
- •3.1.6. Расчет и назначение припусков и операционных размеров
- •3.1.7. Расчет режимов резания
- •3.1.8. Определение норм штучного времени
- •3.1.9. Расчет экономической эффективности ТП
- •3.1.10. Оформление технологических документов
- •3.2. Разработка технологии восстановления детали
- •3.2.4. Сопутствующая технологическая документация
- •3.2.6. Оформление технологической документации
- •3.3. Проектирование и расчёт приспособлений
- •3.3.2. Состав приспособления
- •3.3.4. Расчет составляющих силы резания
- •3.3.5. Расчет усилия зажима заготовки
- •3.3.6. Расчет рычажных зажимных механизмов
- •4. ТРЕБОВАНИЯ К ОФОРМЛЕНИЮ КУРСОВОЙ РАБОТЫ
- •4.1. Содержание пояснительной записки
- •4.2. Требования к оформлению пояснительной записки
- •4.2.1. Общие положения
- •4.2.2. Требования к текстовым документам
- •4.3.2. Требования к оформлению сборочного чертежа
- •Библиографический список
- •Приложение 1
- •Приложение 3
- •Приложение 6
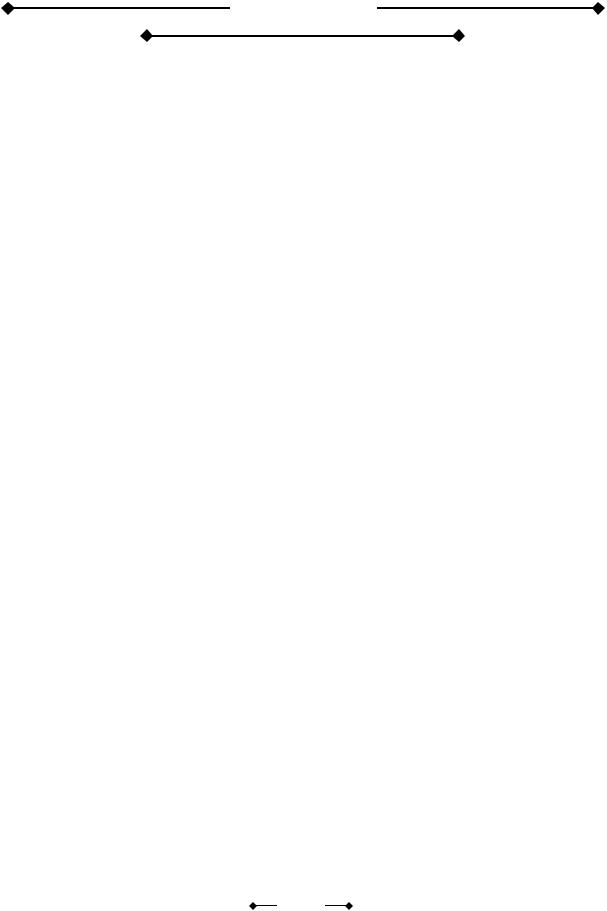
3. РАСЧЁТНАЯ ЧАСТЬ КУРСОВОЙ РАБОТЫ
3.1.Проектирование технологического процесса изготовления детали в курсовой работе
Последовательность разработки технологического процесса отражена в стандартах единой системы технологической подготовки производства
(ЕСТПП) ГОСТ Р 50995.3.1-96, ГОСТ Р 50995.0.1-96, ГОСТ Р 15.000-94 и
единой системытехнологическойдокументации(ЕСТД) поГОСТ3.1109-82. Проектирование технологического процесса содержит ряд взаимосвя-
занных и последовательных этапов:
1.Анализ исходных данных (подробное изучение чертежа детали и задания на курсовую работу).
2.Определение типа производства.
3.Выбор заготовки.
4.Выбор технологических баз.
5.Выбор методов обработки и разработка технологического маршрута обработки заготовки.
6.Разбивка технологических операций на составляющие их переходы с выбором режущего инструмента, металлообрабатывающего оборудования
иоснастки (приспособлений).
7.Расчет и назначение припусков и операционных размеров.
8.Расчет режимов резания.
9.Определение норм штучного времени.
10.Расчет экономической эффективности ТП.
11.Подготовка технологических документов [маршрутная карта (МК), операционная карта (ОК), карта технологического процесса (КТП), карта эскизов (КЭ)].
12.Оформление пояснительной записки.
Последовательность выполнения курсовой работы должна соответствовать данным требованиям.
3.1.1. Анализ исходных данных
Исходная информация для разработки технологического процесса подразделяется на базовую, руководящую и справочную (ГОСТ 14.301-83).
Базовая информация включает данные, содержащиеся в задании на
8

проектирование (задании на курсовую работу); как правило, это рабочий чертеж детали и годовая программа выпуска.
Руководящая информация включает данные стандартов ЕСКД и ЕСТД, классификаторов, инструкций и других нормативных материалов.
Справочная информация представляет собой данные заводской, отраслевой и ведомственной документации, справочной и учебно-методической литературы, периодических изданий, электронных средств.
Анализ следует начинать с чтения рабочего чертежа детали, установления размеров, требований к точности и шероховатости обработки отдельных поверхностей, требований к погрешности формы и взаимного расположения поверхностей, материала детали и ее термообработки. Следует выяснить служебное назначение детали в узле машины и определить степень ее важности для функционирования машины. Из описания назначения и конструкции детали должно быть ясно, какие поверхности и размеры имеют основное значение, а какие – второстепенное. Если назначение детали неизвестно, то следует описать ее назначение как типовой детали.
Впроцессе анализа проверяют, содержит ли рабочий чертеж все сведения о детали: необходимые проекции, разрезы и сечения, размеры с допусками, требования к точности формы и взаимному расположению поверхностей, требования к качеству поверхности.
При этом необходимо произвести оценку технологичности конструкции детали по правилам, установленным ГОСТ 14.201 - 83. Конструкция детали считается технологичной, если она обеспечивает простое и экономически эффективное изготовление и удовлетворяет следующим основным требованиям: конфигурация и материал позволяют применять наиболее прогрессивные заготовки; в детали используются простые геометрические формы; обоснованы требования к точности размеров и формы; использованы стандартизация и унификация детали и ее элементов; предусмотрены допуски только на размеры посадочных поверхностей; деталь имеет достаточную жесткость; имеется возможность подвода инструмента
кзоне обработки детали; обеспечены свободные вход и выход инструмента из зоны обработки; учтена возможность одновременной обработки нескольких деталей.
По результатам анализа исходных данных допускается вносить корректирующие изменения в рабочий чертеж детали (по согласованию с преподавателем). Все изменения и предложения обосновываются и отражаются в пояснительной записке.
Впояснительной записке следует привести описание детали и ее служебное назначение, технические требования к точности и шероховатости, а также данные о материале. Например: «Сталь 20Х ГОСТ 4543 - 71 легированная конструкционная применяется для деталей средних размеров с износоустойчивой поверхностью при достаточно прочной и вязкой серд-
9

цевине». Желательно указать химический состав и основные механические свойства материала.
На основе анализа исходных данных необходимо сформулировать основные технологические задачи, которые необходимо решать при изготовлении данной детали: обеспечение требований к точности и шероховатости основных поверхностей, к технологическому оборудованию и оснастке, к квалификации исполнителей и др. В задании на курсовую работу указывается годовая программы выпуска изделий, которая в значительной степени определяет тип машиностроительного производства.
Тип производства – это классификационная категория производства (единичное, серийное, массовое), определяемая по признакам широты номенклатуры, регулярности и объема выпуска изделий (ГОСТ 14.004 - 83). Тип производства ориентировочно может быть определен в зависимости от массы детали годовой программы выпуска (табл. 1).
Таблица 1
Зависимость типа производства от массы и объема выпуска деталей
Масса |
Годовая программа выпуска деталей, шт. |
|
||||
детали, |
|
|
|
|
|
|
|
Тип производства |
|
||||
|
кг |
|
|
|||
|
|
|
|
|
|
|
|
|
Единичное |
Мелкосерийное |
Среднесерийное |
|
Массовое |
|
|
|
|
|
|
|
Менее 1,0 |
Менее 10 |
10 - 2 000 |
1 500 - 10 0000 |
|
200 000 |
|
1,0 |
- 2,5 |
Менее 10 |
10 - 1 000 |
1 000 - 50 000 |
|
100 000 |
|
|
|
|
|
|
|
2,5 |
- 5,0 |
Менее 10 |
10 - 500 |
500 - 35 000 |
|
75 000 |
5,0 |
- 10,0 |
Менее 10 |
10 - 300 |
300 - 25 000 |
|
50 000 |
Более 10 |
Менее 10 |
10 - 200 |
200 - 10 000 |
|
25 000 |
|
|
|
|
|
|
|
|
Разрабатываемый в курсовой работе технологический процесс ориентирован на единичный или мелкосерийный тип производства.
Согласно ГОСТ 14.312 -74 форма организации производства может быть поточной или групповой. Для единичного или мелкосерийного типа производства характерна групповая форма организации производства, характеризующаяся периодическим запуском производства деталей партиями.
Количество деталей в партии (n, шт.) определяется по формуле
n N ,
12
где N – годовая программа выпуска деталей, шт.
10

3.1.2. Выбор заготовки
Выбор заготовки для дальнейшей механической обработки является одним из важнейших этапов проектирования технологического процесса изготовления детали.
На выбор заготовки влияют следующие показатели: назначение детали; материал; технические условия; объем выпуска и тип производства; тип и конструкция детали; размеры детали и оборудования, на котором она изготовляется; экономичность изготовления заготовки, выбранной по предыдущим показателям. Все эти показатели должны учитываться одновременно, так как они тесно связаны.
Наиболее часто в курсовых проектах применяют заготовки из проката, штампованные заготовки и отливки.
Заготовки из проката. Для изготовления деталей методами резания может применятся сортовой и специальный прокат. Сортовой прокат следует использовать в тех случаях, когда профиль детали приближен к профилю проката.
Простые сортовые профили общего назначения - круглые и квадратные (ГОСТ 2590-71), шестигранные (ГОСТ 2879-69) и полосовые (ГОСТ 103-76)
–используют для изготовления гладких ступенчатых валов с небольшим перепадом диаметров ступеней, стаканов диаметром до 50 мм, втулок диаметром до 25 мм, рычагов, клиньев, фланцев (табл. 2, 3, 4, 5).
Фасонные профили общего назначения – сталь угловую равнополочную и неравнополочную (ГОСТ 8509-72 и ГОСТ 8510-72), балки двутавровые (ГОСТ 8239-72) и швеллеры (ГОСТ 8240-72) – применяют при изготовлении металлоконструкций (рам, плит, подставок, кронштейнов).
Трубный прокат – стальной бесшовный холодный, горячекатаный, холоднотянутый (ГОСТ 8732-78; ГОСТ 8734-75) – служит для изготовления цилиндров, втулок, гильз, шпинделей, стаканов, барабанов, роликов, пустотелых валов (табл. 6).
Профили продольной прокатки (ГОСТ 8319.0-75; ГОСТ 8319.13-75 и ГОСТ 8531-78) служат для изготовления балок передних осей автомобилей, лопаток, осей; поперечно-винтовой (ГОСТ 8320.0-83; ГОСТ 8320.13-83)
–для изготовления валов электродвигателей, шпинделей машин, осей рычагов; поперечно-клиновой прокатки – для изготовления валов коробки передач автомобилей, валиков и других деталей типа тел вращения крупносерийного и массового производства; поперечной прокатки (ГОСТ 7524-83)
–для изготовления шариков подшипников качения, профилированных трубчатых деталей (втулки).
Точность горячекатаного проката ориентировочно соответствует 12– 14-му квалитетам, холоднотянутого – 9–12-му квалитетам (табл. 7).
11
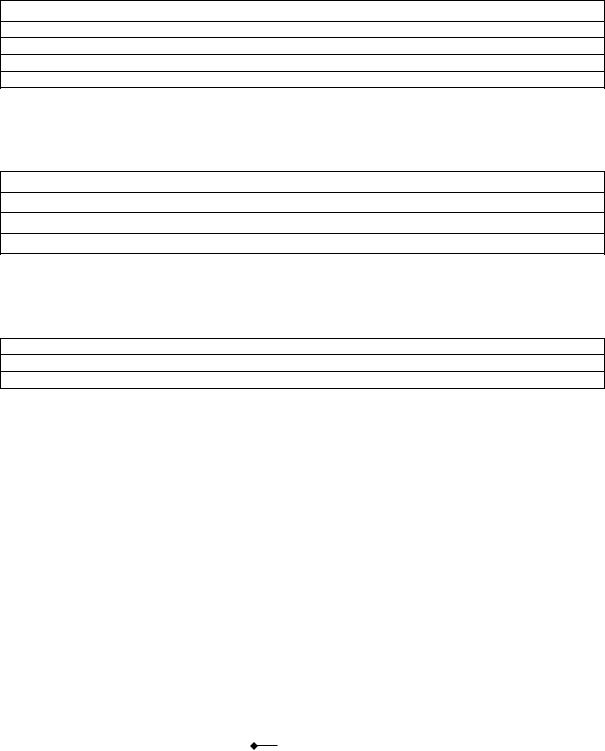
Для получения заготовок для деталей из проката пруток разрезают на мерные части. Выбор диаметра заготовки для деталей, изготавливаемых из круглого сортового проката производят по ГОСТ 2590-88 (табл. 8) в зависимости от номинального диаметра детали и соотношения ее длины и диаметра. Обработка давлением обеспечивает получение заготовок с помощью ковки, штамповки и других специальных процессов.
Таблица 2
Сталь горячекатаная круглая обычной точности
(из ГОСТ 2590-88)
Диаметр, мм
5; 5,5; 6; 7; 8; 9; 10; 11; 12; 13; 14; 15; 16; 17; 18; 19; 20
21; 22; 23; 24; 25; 26; 27; 28; 29; 30; 31; 32; 33; 34; 35; 36; 37; 38; 39; 40
42; 44; 48; 50; 52; 54; 55; 56; 58; 60; 62; 65; 68; 70; 72; 75; 78; 80
85; 90; 95; 100; 110; 115; 120; 125; 130; 140; 150; 160; 170; 180; 190; 200
Таблица 3
Сталь горячекатаная квадратная
(из ГОСТ 2591-88)
Сторона квадрата, мм
5; 6; 7; 8; 9; 10; 11; 12; 13; 14; 15; 16; 17; 18; 19; 20; 22; 24; 25;
26; 28; 30; 32; 34; 36; 38; 40; 42; 45; 48; 50; 53; 56; 60; 63; 65; 70; 75;80;
85; 90; 95; 100; 105; 110; 120; 125; 130; 140; 150; 160; 170; 180; 190; 200
Таблица 4
Сталь горячекатаная шестигранная
(из ГОСТ 2879-88)
Диаметр вписанного круга, мм
8; 9; 10; 11; 12; 13; 14; 15; 16; 17; 18; 19; 20; 21; 22; 24; 25; 26; 27; 28; 30; 32;
34; 36; 38; 40; 42; 45; 48; 50; 53; 56; 60; 63; 65; 70; 75; 80; 85; 90; 95; 100
|
|
Сталь прокатная толстолистовая |
|
Таблица 5 |
|
|
|
|
|
|
|
(из ГОСТ 19903-74) |
|
|
|
|
|
|
|
Толщиналистов,мм |
|
Ширина листов, мм |
|
Длина листов, мм |
4,0; 4,5 |
600; 710; 1 000; 1 250; 1 400; 1 500; |
2 |
000; 2 500; 2 800; |
|
1 600 |
3 500 |
|||
5,0; 5,5 |
1 |
250; 1 400; 1 500; 1 600 |
2 |
500; 2 800; 3 500 |
6,0; 7,0 |
1 |
250; 1 400; 1 500; 1 600; 1 800 |
2 |
800; 3 500; 4 500; |
5 000 |
||||
8,0; 9,0; 10,0; 11,0 |
1 |
250; 1 400; 1 500; 1 600; 1 800; 2 000 |
4 |
500; 5 000; 5 500; |
6 000 |
||||
12,0; 13,0 |
1 |
400; 1 500; 1 600; 1 800; 2 000 |
5 |
000; 5 500; 6 000; |
7 000 |
||||
16; 18; 20; 22; 25; |
1 |
400; 1 500; 1 600; 1 800; 2 000; 2 200; |
5 |
000; 5 500; 6 000; |
28; 30; 32 |
2 |
400 |
7 000; 8 000 |
|
36; 40; 45; 50; 56; |
1 |
500; 1 600; 1 800; 2 000; 2 200; 2 500 |
5 |
000; 5 500; 6 000; |
60 |
7 000; 8 000 |
12

Кованые и штампованные заготовки. Кузнечно-штамповочное про-
изводство уступает литейному в возможной сложности конфигурации получаемых деталей, но имеет преимущества в прочности и надежности выпускаемой продукции.
Таблица 6
Трубы стальные бесшовные холоднотянутые и холоднокатаные
(из ГОСТ 8734-75)
Наружный |
Толщина стенки, мм |
|
диаметр, мм |
|
|
|
0,25; 0,3; 0,4; 0,5; 0,6; 0,8; 1,0; 1,2; 1,4; 1,6; 1,8; 2,0; 2,2; 2,5; 2,8; 3,0; |
|
10,0; 11,0 |
3,2; 3,5 |
|
|
0,25; 0,3; 0,4; 0,5; 0,6; 0,8; 1,0; 1,2; 1,4; 1,6; 1,8; 2,0; 2,2; 2,5; 2,8; 3,0; |
|
12,0; 14,0 |
3,2; 3,5; 4,0 |
|
|
0,25; 0,3; 0,4; 0,5; 0,6; 0,8; 1,0; 1,2; 1,4; 1,6; 1,8; 2,0; 2,2; 2,5; 2,8; 3,0; |
|
16,0; 18,0 |
3,2; 3,5; 4,0; 4,5; 5,0 |
|
19; 20 |
0,25; 0,3; 0,4; 0,5; 0,6; 0,8; 1,0; 1,2; 1,4; 1,6; 1,8; 2,0; 2,2; 2,5; 2,8; 3,0; |
|
|
3,2; 3,5; 4,0; 4,5; 5,0; 5,5; 6,0 |
|
22; 25; 28 |
0,4; 0,5; 0,6; 0,8; 1,0; 1,2; 1,4; 1,6; 1,8; 2,0; 2,2; 2,5; 2,8; 3,0; 3,2; 3,5; |
|
|
4,0; 4,5; 5,0; 5,5; 6,0; 6,5; 7,0 |
|
30; 32; 34; |
0,4; 0,5; 0,6; 0,8; 1,0; 1,2; 1,4; 1,6; 1,8; 2,0; 2,2; 2,5; 2,8; 3,0; 3,2; 3,5; |
|
36 |
4,0; 4,5; 5,0; 5,5; 6,0; 6,5; 7,0; 7,5; 8,0 |
|
38; 40 |
0,4; 0,5; 0,6; 0,8; 1,0; 1,2; 1,4; 1,6; 1,8; 2,0; 2,2; 2,5; 2,8; 3,0; 3,2; 3,5; |
|
|
4,0; 4,5; 5,0; 5,5; 6,0; 6,5; 7,0; 7,5; 8,0; 8,5; 9,0 |
|
42; 45; 48 |
1,0; 1,2; 1,4; 1,6; 1,8; 2,0; 2,2; 2,5; 2,8; 3,0; 3,2; 3,5; 4,0; 4,5; 5,0; 5,5; |
|
|
6,0; 6,5; 7,0; 7,5; 8,0; 8,5; 9,0; 9,5; 10,0 |
|
50; 53; 56; |
|
|
60; 63; 65; |
1,0; 1,2; 1,4; 1,6; 1,8; 2,0; 2,2; 2,5; 2,8; 3,0; 3,2; 3,5; 4,0; 4,5; 5,0; 5,5; |
|
70; 75 |
6,0; 6,5; 7,0; 7,5; 8,0; 8,5; 9,0; 9,5; 10,0; 11; 12 |
|
80; 85; 90; |
|
|
95; 100; |
1,4; 1,6; 1,8; 2,0; 2,2; 2,5; 2,8; 3,0; 3,2; 3,5; 4,0; 4,5; 5,0; 5,5; 6,0; 6,5; |
|
110 |
7,0; 7,5; 8,0; 8,5; 9,0; 9,5; 10,0; 11; 12 |
|
120 |
1,6; 1,8; 2,0; 2,2; 2,5; 2,8; 3,0; 3,2; 3,5; 4,0; 4,5; 5,0; 5,5; 6,0; 6,5; 7,0; |
|
7,5; 8,0; 8,5; 9,0; 9,5; 10,0; 11; 12 |
||
|
||
125 |
1,8; 2,0; 2,2; 2,5; 2,8; 3,0; 3,2; 3,5; 4,0; 4,5; 5,0; 5,5; 6,0; 6,5; 7,0; 7,5; |
|
|
8,0; 8,5; 9,0; 9,5; 10,0; 11; 12 |
|
130 |
2,5; 2,8; 3,0; 3,2; 3,5; 4,0; 4,5; 5,0; 5,5; 6,0; 6,5; 7,0; 7,5; 8,0; 8,5; 9,0; |
|
9,5; 10,0; 11; 12 |
||
|
3,0; 3,2; 3,5; 4,0; 4,5; 5,0; 5,5; 6,0; 6,5; 7,0; 7,5; 8,0; 8,5; 9,0; 9,5; 10,0; |
|
140;150 |
11; 12 |
|
160; 170; |
|
|
180 |
3,5; 4,0; 4,5; 5,0; 5,5; 6,0; 6,5; 7,0; 7,5; 8,0; 8,5; 9,0; 9,5; 10,0; 11; 12 |
|
190; 200 |
4,0; 4,5; 5,0; 5,5; 6,0; 6,5; 7,0; 7,5; 8,0; 8,5; 9,0; 9,5; 10,0; 11; 12 |
13

Таблица 7
Предельные отклонения по диаметру сортового круглого проката, мм
Диаметр проката, мм |
|
|
Точность прокатки |
|
|||
высокая |
|
обычная |
повышенная |
||||
|
|
|
|
|
|
|
|
|
+ |
|
|
+ |
|
+ |
|
5; 5,5; 6; 6,5; 7...9 |
0,1 |
0,2 |
|
0,2 |
0,5 |
0,3 |
0,5 |
|
|
|
|
|
|
|
|
10... 19 |
0,1 |
0,3 |
|
0,2 |
0,5 |
0,3 |
0,5 |
|
|
|
|
|
|
|
|
20...25 |
0,2 |
0,3 |
|
0,2 |
0,5 |
0,4 |
0,5 |
|
|
|
|
|
|
|
|
26...48 |
0,2 |
0,5 |
|
0,2 |
0,7 |
0,4 |
0,7 |
|
|
|
|
|
|
|
|
50; 52...58 |
0,2 |
0,8 |
|
0,2 |
1,0 |
0,4 |
1,0 |
|
|
|
|
|
|
|
|
60; 62; 63; 65; 67; 68 |
0,3 |
0,9 |
|
0,3 |
1,1 |
0,5 |
1,1 |
|
|
|
|
|
|
|
|
70; 72; 75; 78; 80; 82; 85; 90; 95 |
0,3 |
1,1 |
|
0,3 |
1,3 |
0,5 |
1,3 |
|
|
|
|
|
|
|
|
100;105; 110; 115 |
|
|
|
0,4 |
1,37 |
0,6 |
1,7 |
|
|
|
|
|
|
|
|
120; 125; 130; 135 |
|
|
|
0,6 |
2,0 |
0,8 |
2,0 |
|
|
|
|
|
|
|
|
140; 150; 160; 170; 180; 190; 200 |
|
|
|
|
|
0,9 |
2,5 |
210; 220; 230; 240; 250 |
|
|
|
|
|
1,2 |
3,0 |
|
|
|
|
|
|
|
|
Наиболее ответственные детали машин изготавливают из кованых и штампованных заготовок, так как механические свойства металла выше, чем у литых материалов. Технологический процесс получения заготовок обработкой давлением отличается также и высокой производительностью.
Ковкой получают поковки простой формы до 350 кг с большими припусками в единичном и мелкосерийном производствах.
Поковки массой до 500 1 000 кг получают на паровоздушных молотах, а более крупные на гидравлических прессах. Припуски и допуски на поковки из углеродистой и легированной стали при ковке на молотах определяют по ГОСТ 7829-79, а для поковок, изготовляемых ковкой на прессах, по ГОСТ 7062-90.
Штамповка на кривошипных прессах в 2 3 раза производительнее по сравнению со штамповкой на молотах, при этом припуски и допуски уменьшаются на 20 35%, расход металла снижается на 10 15%. Припуски и допуски на поковки, получаемые горячей объёмной штамповкой, определяют по ГОСТ 7505-89 в зависимости от массы поковки (не более 250 кг с линейным габаритным размером не более 2 500 мм), группы материала, степени сложности, класса точности и шероховатости поверхности детали.
14

Таблица 8
Выбор диаметра заготовки для деталей, изготавливаемых из круглого сортового проката по ГОСТ 2590-88 (размеры, мм)
Номи- |
Отношение длины |
Номи- |
|
|
Отношение длины |
||||||
нальный |
детали к ее диаметру |
нальный |
|
детали к ее диаметру |
|||||||
диаметр |
|
|
L/D |
|
диаметр |
|
|
|
L/D |
|
|
вала, мм |
<4 |
<8 |
|
<12 |
<20 |
вала, мм |
<4 |
|
<8 |
<12 |
<20 |
5 |
7 |
7 |
|
7 |
8 |
46 |
50 |
|
50 |
52 |
52 |
6 |
8 |
8 |
|
8 |
8 |
48 |
52 |
|
52 |
54 |
54 |
7 |
9 |
9 |
|
9 |
9 |
50 |
54 |
|
54 |
55 |
55 |
8 |
10 |
10 |
|
10 |
11 |
52 |
55 |
|
55 |
56 |
56 |
9 |
11 |
11 |
|
11 |
11 |
54 |
58 |
|
60 |
60 |
62 |
10 |
12 |
12 |
|
13 |
13 |
55 |
60 |
|
60 |
62 |
65 |
11 |
13 |
13 |
|
13 |
13 |
58 |
62 |
|
62 |
65 |
68 |
12 |
14 |
14 |
|
15 |
15 |
60 |
65 |
|
65 |
68 |
70 |
13 |
15 |
15 |
|
16 |
16 |
62 |
68 |
|
68 |
70 |
72 |
14 |
16 |
16 |
|
17 |
17 |
65 |
70 |
|
70 |
72 |
75 |
15 |
17 |
17 |
|
18 |
18 |
68 |
72 |
|
72 |
76 |
78 |
16 |
18 |
18 |
|
18 |
19 |
70 |
75 |
|
75 |
78 |
80 |
17 |
19 |
19 |
|
20 |
20 |
72 |
78 |
|
78 |
80 |
85 |
18 |
20 |
20 |
|
21 |
21 |
75 |
80 |
|
80 |
80 |
90 |
19 |
21 |
21 |
|
22 |
22 |
78 |
85 |
|
85 |
90 |
90 |
20 |
22 |
22 |
|
23 |
24 |
80 |
85 |
|
90 |
95 |
95 |
21 |
24 |
24 |
|
24 |
25 |
82 |
90 |
|
95 |
95 |
95 |
23 |
26 |
26 |
|
26 |
27 |
85 |
90 |
|
95 |
95 |
100 |
24 |
27 |
27 |
|
27 |
28 |
88 |
95 |
|
100 |
100 |
100 |
25 |
28 |
28 |
|
28 |
30 |
90 |
95 |
|
100 |
105 |
105 |
26 |
30 |
30 |
|
30 |
30 |
92 |
100 |
|
100 |
105 |
110 |
27 |
30 |
30 |
|
32 |
32 |
95 |
100 |
|
105 |
110 |
110 |
28 |
32 |
32 |
|
32 |
32 |
98 |
105 |
|
110 |
110 |
115 |
30 |
33 |
33 |
|
34 |
34 |
100 |
105 |
|
110 |
115 |
115 |
32 |
35 |
35 |
|
36 |
36 |
105 |
110 |
|
115 |
120 |
120 |
34 |
38 |
38 |
|
38 |
38 |
110 |
115 |
|
120 |
125 |
125 |
35 |
38 |
38 |
|
39 |
39 |
115 |
120 |
|
125 |
130 |
130 |
36 |
39 |
40 |
|
40 |
40 |
120 |
125 |
|
130 |
135 |
135 |
38 |
42 |
42 |
|
42 |
43 |
125 |
130 |
|
130 |
135 |
140 |
40 |
43 |
45 |
|
45 |
45 |
130 |
135 |
|
140 |
140 |
150 |
42 |
45 |
45 |
|
48 |
48 |
135 |
140 |
|
140 |
150 |
150 |
44 |
48 |
48 |
|
50 |
50 |
140 |
150 |
|
150 |
160 |
160 |
15

Стандартом предусмотрено 5 классов точности поковок: T1, Т2, Т3, Т4 и Т5 (наиболее точный класс Т1). Класс точности выбирают в зависимости
от применяемого оборудования (табл. 9).
Таблица 9
Выбор класса точности поковок
Основное технологическое оборудование, |
|
Класс точности |
|
||
технологические процессы |
Т1 |
Т2 |
Т3 |
Т4 |
Т5 |
Кривошипные горячештамповочные прессы, |
|
|
|
+ |
+ |
открытая штамповка, закрытая штамповка |
|
+ |
+ |
||
|
|
|
|||
Горизонтально-ковочные машины |
|
|
|
+ |
+ |
Штамповочные молоты |
|
|
|
+ |
+ |
Калибровка |
+ |
+ |
|
|
|
Стандарт делит штампуемые стали на три группы: Ml, М2 и М3: Ml с содержанием углерода до 0,35% включительно и суммарным содержанием легирующих элементов до 2% включительно; М2 с содержанием углерода свыше 0,35 до 0,65% включительно или суммарным содержанием легирующих элементов свыше 2,0 до 5,0% включительно; М3 с содержанием углерода свыше 0,65% или суммарным содержанием легирующих элементов свыше 5%.
Стандартом предусмотрено 4 степени сложности штамповок: С1, С2, СЗ и С4. Степень сложности определяют путем вычисления отношения массы (объема) поковки GП к массе (объему) геометрической фигуры Gф, в которую вписывается форма поковки. Геометрическая фигура может быть шаром, параллелепипедом, цилиндром с перпендикулярными к его оси торцами или правильной призмой. Степеням сложности соответствуют следующие числовые значения отношения GП /Gф :
С1 св. 0,63; С2 св. 0,32; до 63 вкл.;
С3 св. 0,16; до 0,32 вкл.; С4 до 0,16.
Расчетная масса поковки определяется исходя из размеров детали по формуле
GП Gg Kр,
где Gg масса детали, кг; Kр расчетный коэффициент, устанавливаемый по ГОСТ 7505-89 (табл. 10).
Расчетная масса геометрической фигуры Gф, в которую вписывается форма поковки, определяется произведением объема фигуры на плотность материала (плотность стали составляет 7,8 г/см3).
16

Объем фигуры простейших профилей заготовок можно рассчитать по следующимформулам:
круглое сечение V 0,78 d2 l;
квадратное сечение V а2 l;
прямоугольное сечение V b а l;
шестигранное сечение V 0,87 c2 l;
кольцевое сечение V 0,78 D2 d l,
где d – диаметр круглого сечения; l – длина; а – сторона квадрата или прямоугольника; b – сторона прямоугольника; с – диаметр вписанного в шестигранник круга; D, d – диаметры внешней и внутренней окружностей кольца.
Коэффициент Кр для определения |
Таблица 10 |
|
|
||
ориентировочной расчетной массы поковки |
|
|
|
|
|
Характеристика детали |
Типовые представители |
Кр |
|
(виды, типы деталей) |
|
|
Удлиненной формы |
|
С прямой осью |
Валы, оси, цапфы, шатуны |
1,3-1,6 |
С изогнутой осью |
Рычаги,сошки рулевого управле- |
1,1-1,4 |
|
ния |
|
Круглые и многогранные в плане |
|
|
Круглые |
Шестерни, ступицы, фланцы |
1,5-1,8 |
Квадратные, прямоугольные, |
Фланцы, ступицы, гайки |
1,3-1,7 |
многогранные |
|
|
С отростками |
Крестовины, вилки |
1,4-1,6 |
Комбинированной |
Кулаки поворотные, коленчатые |
1,3-1,8 |
конфигурации |
валы |
|
С большим объемом |
Балки передних осей, рычаги пе- |
1,1-1,3 |
необработанных поверхно- |
реключения коробок передач, |
|
стей |
буксирные крюки |
|
С отверстиями, углубления- |
Полые валы, фланцы, блоки шес- |
1,8-2,2 |
ми, не оформляемыми в по- |
терен |
|
ковке |
|
|
По стандарту, при определении припусков и допусков штампованной поковки используют исходный индекс, который определяют в зависимости от массы, группы стали, степени сложности и класса точности поковки (прил. 2). Стандартом предусмотрено 23 исходных индекса (1 23).
Согласно стандарту имеются два вида припусков на механическую обработку: основной и дополнительный (учитывает отклонение формы по-
17
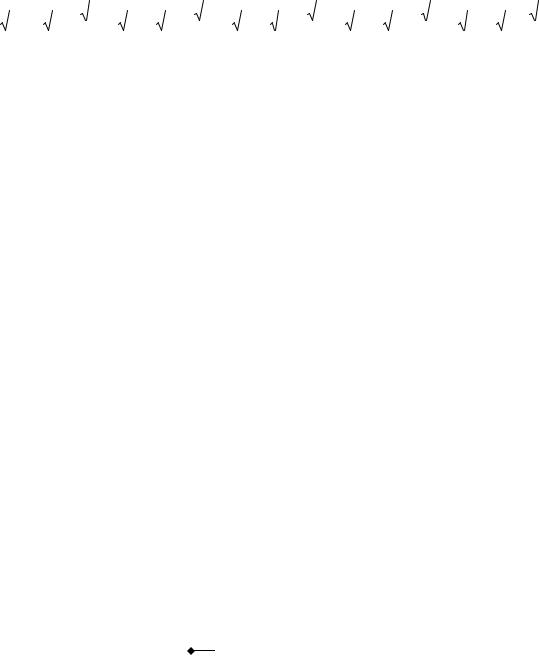
ковки). Основные припуски на механическую обработку поковок определяют по ГОСТ 7505-89 (табл. 11) в зависимости от исходного индекса, линейных размеров и шероховатости поверхности детали.
|
|
|
|
|
|
|
|
|
|
|
|
|
|
|
|
|
|
|
|
|
|
|
|
|
|
|
|
|
|
|
|
|
|
|
|
|
|
|
|
Таблица 11 |
||||||||
|
|
Основные припуски на механическую обработку поковок |
|
|
|
|
|
|
||||||||||||||||||||||||||||||||||||||||
|
|
|
|
|
|
|
|
|
|
|
|
|
|
|
|
|
|
|
|
|
|
|
|
|
|
|
|
|
|
|
|
|
|
|
|
|
|
|
|
|
|
|
|
|
|
|
|
|
Ис- |
|
|
|
|
|
|
|
|
|
|
|
|
|
|
|
|
|
|
Толщина детали |
|
|
|
|
|
|
|
|
|
|
|
|
|
|
|
|
|
|
|||||||||||
ход- |
|
|
|
до 25 |
|
|
|
|
|
|
25-40 |
|
|
|
|
|
|
40-63 |
|
|
|
63 - 100 |
|
|
100-160 |
|
|
|||||||||||||||||||||
ный |
|
|
|
|
|
|
|
Длина, ширина, диаметр, глубина и высота детали |
|
|
|
|
|
|
||||||||||||||||||||||||||||||||||
ин- |
|
|
|
|
|
|
|
|
|
|
|
|
|
|
|
|
|
|
|
|
|
|
|
|
|
|
|
|
|
|
|
|
|
|
|
|
|
|
|
|
|
|
|
|
|
|
||
|
|
|
до 40 |
|
|
|
400-100 |
|
|
100-160 |
|
|
160-250 |
|
|
250-400 |
|
|
||||||||||||||||||||||||||||||
декс |
|
|
|
|
|
|
|
|
|
|
|
|
|
|
|
|
|
|
|
|
|
|
|
|
|
|
|
|
|
|
|
|
|
|
|
|
|
|
|
|
|
|
|
|
|
|
|
|
|
|
|
|
|
|
|
|
|
|
|
|
|
|
|
|
|
Шероховатость, мкм |
|
|
|
|
|
|
|
|
|
|
|
|
|
|
|
||||||||||||||||
|
100 |
|
10 |
1,25 |
100 |
|
10 |
1,25 |
100 |
|
10 |
1,25 |
100 |
10 |
1,25 |
100 |
10 |
1,25 |
||||||||||||||||||||||||||||||
|
12,5 |
|
1,6 |
12,5 |
|
1,6 |
12,5 |
|
1,6 |
12,5 |
1,6 |
12,5 |
1,6 |
|||||||||||||||||||||||||||||||||||
|
|
|
|
|
|
|
|
|
|
|
|
|
|
|
|
|||||||||||||||||||||||||||||||||
|
|
|
|
|
|
|
|
|
|
|
|
|
|
|
|
|
|
|
|
|
|
|
|
|
|
|
|
|
|
|
|
|
|
|
|
|
|
|
||||||||||
1 |
0,4 |
|
0,6 |
0,7 |
0,4 |
|
0,6 |
0,7 |
0,5 |
|
0,6 |
0,7 |
0,6 |
0,8 |
0,8 |
0,6 |
0,8 |
0,8 |
||||||||||||||||||||||||||||||
2 |
0,4 |
|
0,6 |
0,7 |
0,5 |
|
0,6 |
0,7 |
0,6 |
|
0,8 |
0,9 |
0,6 |
0,8 |
0,8 |
0,7 |
0,9 |
0,9 |
||||||||||||||||||||||||||||||
3 |
0,5 |
|
0,6 |
0,7 |
0,6 |
|
0,8 |
0,9 |
0,6 |
|
0,8 |
0,9 |
0,7 |
0,9 |
0,9 |
0,8 |
1,0 |
1,0 |
||||||||||||||||||||||||||||||
4 |
0,6 |
|
0,8 |
0,9 |
0,6 |
|
0,8 |
0,9 |
0,7 |
|
0,9 |
1,0 |
0,8 |
1,0 |
1,0 |
0,9 |
1,1 |
1,1 |
||||||||||||||||||||||||||||||
5 |
0,6 |
|
0,8 |
0,9 |
0,7 |
|
0,9 |
1,0 |
0,8 |
|
1,0 |
1,1 |
0,9 |
1,1 |
1,1 |
1,0 |
1,2 |
1,2 |
||||||||||||||||||||||||||||||
6 |
0,7 |
|
0,9 |
1,0 |
0,8 |
|
1,0 |
1,1 |
0,9 |
|
1,1 |
1,2 |
1,0 |
1,2 |
1,2 |
1,1 |
1,4 |
1,4 |
||||||||||||||||||||||||||||||
7 |
0,8 |
|
1,0 |
1,1 |
0,9 |
|
1,1 |
1,2 |
1,0 |
|
1,2 |
1,4 |
1,1 |
1,4 |
1,4 |
1,2 |
1,5 |
1,5 |
||||||||||||||||||||||||||||||
8 |
0,9 |
|
1,1 |
1,2 |
1,0 |
|
1,2 |
1,4 |
1,1 |
|
1,4 |
1,5 |
1,2 |
1,5 |
1,5 |
1,3 |
1,6 |
1,6 |
||||||||||||||||||||||||||||||
9 |
1,0 |
|
1,2 |
1,4 |
1,1 |
|
1,4 |
1,5 |
1,2 |
|
1,5 |
1,6 |
1,3 |
1,6 |
1,6 |
1,4 |
1,8 |
1,8 |
||||||||||||||||||||||||||||||
10 |
1,1 |
|
1,4 |
1,5 |
1,2 |
|
1,5 |
1,6 |
1,3 |
|
1,6 |
1,8 |
1,4 |
1,8 |
1,8 |
1,5 |
1,9 |
1,9 |
||||||||||||||||||||||||||||||
11 |
1,2 |
|
1,5 |
1,6 |
1,3 |
|
1,6 |
1,8 |
1,4 |
|
1,8 |
1,9 |
1,5 |
1,9 |
1,9 |
1,7 |
2,0 |
2,0 |
||||||||||||||||||||||||||||||
12 |
1,3 |
|
1,6 |
1,8 |
1,4 |
|
1,8 |
1,9 |
1,5 |
|
1,9 |
2,0 |
1,7 |
2,0 |
2,0 |
1,9 |
2,3 |
2,3 |
||||||||||||||||||||||||||||||
13 |
1,4 |
|
1,8 |
1,9 |
1,5 |
|
1,9 |
2,0 |
1,7 |
|
2,0 |
2,2 |
1,9 |
2,3 |
2,3 |
2,0 |
2,5 |
2,5 |
||||||||||||||||||||||||||||||
14 |
1,5 |
|
1,9 |
2,0 |
1,7 |
|
2,0 |
2,2 |
1,9 |
|
2,3 |
2,5 |
2,0 |
2,5 |
2,5 |
2,2 |
2,7 |
2,7 |
||||||||||||||||||||||||||||||
15 |
1,6 |
|
2,0 |
2,2 |
1,9 |
|
2,3 |
2,5 |
2,0 |
|
2,5 |
2,7 |
2,2 |
2,7 |
2,7 |
2,4 |
3,0 |
3,0 |
||||||||||||||||||||||||||||||
16 |
1,7 |
|
2,3 |
2,5 |
2,0 |
|
2,5 |
2,7 |
2,2 |
|
2,7 |
3,0 |
2,4 |
3,0 |
3,0 |
2,6 |
3,2 |
3,5 |
||||||||||||||||||||||||||||||
17 |
1,8 |
|
2,5 |
2,7 |
2,2 |
|
2,7 |
3,0 |
2,4 |
|
3,0 |
3,3 |
2,6 |
3,2 |
3,5 |
2,8 |
3,5 |
3,8 |
||||||||||||||||||||||||||||||
18 |
1,9 |
|
2,7 |
3,0 |
2,4 |
|
3,0 |
3,3 |
2,6 |
|
3,2 |
3,5 |
2,8 |
3,5 |
3,8 |
3,0 |
3,8 |
4,1 |
||||||||||||||||||||||||||||||
19 |
2,0 |
|
3,0 |
3,3 |
2,6 |
|
3,2 |
3,5 |
2,8 |
|
3,5 |
3,8 |
3,0 |
3,8 |
4,1 |
3,4 |
4,3 |
4,7 |
||||||||||||||||||||||||||||||
20 |
2,1 |
|
3,2 |
3,5 |
2,8 |
|
3,5 |
3,8 |
3,0 |
|
3,8 |
4,1 |
3,4 |
4,3 |
4,7 |
3,7 |
4,7 |
5,1 |
||||||||||||||||||||||||||||||
21 |
2,8 |
|
3,5 |
3,8 |
3,0 |
|
3,8 |
4,1 |
3,4 |
|
4,3 |
4,7 |
3,7 |
4,7 |
5,1 |
4,1 |
5,1 |
5,6 |
||||||||||||||||||||||||||||||
22 |
3,0 |
|
3,8 |
4,1 |
3,4 |
|
4,3 |
4,7 |
3,7 |
|
4,7 |
5,1 |
4,1 |
5,1 |
5,6 |
4,5 |
5,7 |
6,2 |
||||||||||||||||||||||||||||||
23 |
3,4 |
|
4,3 |
4,7 |
3,7 |
|
4,7 |
5,1 |
4,1 |
|
5,1 |
5,6 |
4,5 |
5,7 |
6,2 |
4,9 |
6,2 |
6,8 |
Отливки. Одним из методов получения заготовок в машиностроении является литье. Преимущество литых заготовок заключается в том, что их можно изготовить максимально приближенными к заданной форме и размерам и практически любой конфигурации.
18

Отливки применяют для изготовления корпусных и других деталей сложной формы (корпусов, кронштейнов, стоек, фланцев и т.п.). Для получения отливок наиболее широко применяется литье:
-в песчаные формы;
-в кокиль;
-по выплавляемым моделям;
-под давлением;
-в оболочковые формы.
Выбор того или иного метода литья зависит от материала детали, точности размеров и шероховатости поверхностей, от конфигурации, размеров и массы детали, а также от типа производства.
Литьё в песчаные формы является наиболее универсальным методом. Однако изготовление формы требует больших затрат времени.
Литьём в землю по металлическим моделям при машинной формовке получают отливки массой до 10 15 т при наименьшей толщине стенок 3 8 мм. Параметр шероховатости Ra 20 5.
Литьё в оболочковые формы применяют главным образом при получении ответственных фасонных алюминиевых и стальных отливок массой до 100 кг. Параметр шероховатости Ra 20 2,5.
Литьё в кокиль экономически целесообразно при величине партии менее 300 500 шт. для мелких отливок и 30 50 шт. для крупных отливок. Этим способом можно получать отливки массой 0,25 7 т. Параметр шероховатости Ra 20 2,5.
Литьё по выплавляемым моделям экономически целесообразно для литых деталей сложной конфигурации из любых сплавов и массой 50 100 кг при партии свыше 1 000 шт. Параметр шероховатости Ra 10 2,5.
Литьё под давлением применяется в основном для получения фасонных отливок из цинковых, алюминиевых, магниевых и латунных сплавов. Способ считается целесообразным при величине партии в 1 000 и более деталей и массе отливки до 100 кг. Параметр шероховатости не более Ra 5.
Центробежное литьё может применяться при выполнении заготовок, имеющих форму тел вращения и массу 0,01 3 т. Параметр шероховатости не более Ra 40 10.
Припуски и допускаемые отклонения на литые заготовки, припуски на механическую обработку отливок из чугуна, стали, цветных металлов и сплавов, а также допускаемые отклонения от номинальных размеров устанавливают по ГОСТ 26645-85.
Согласно ГОСТ 26645-85 точность отливки характеризуется четырьмя показателями:
классом размерной точности (22 класса);
степенью коробления (11 степеней);
19