
ТРАНСВУЗ-2015.Часть 3
.pdf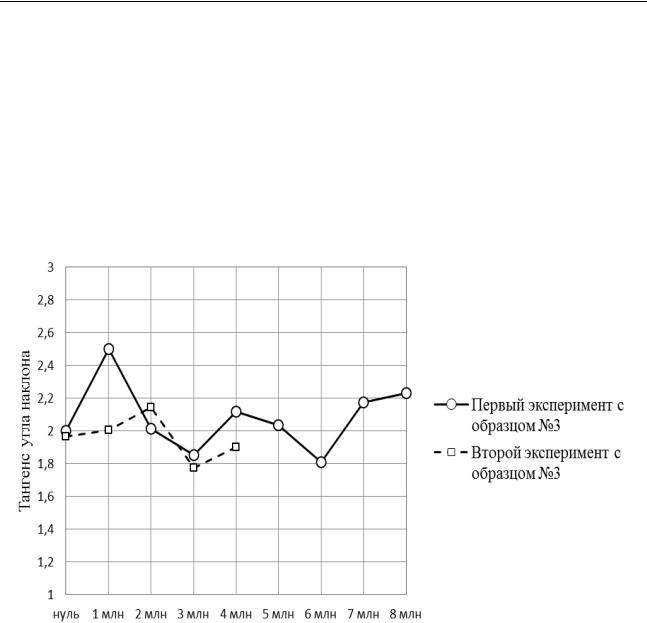
Ремонт и динамика подвижного состава
Склонность металлов к циклическому упрочнению или разупрочнению определяется отношением предела прочности σВ к условному пределу текучести σ0,2. Если отношение σВ / σ0,2 ≤ 1,2, то происходит разупрочнение, при σВ / σ0,2 ≥ 1,4 происходит упрочнение, при 1,2 ≤ σВ / σ0,2 ≤ 1,4 может происходить как упрочнение, так и разупрочнение. На первых двух стадиях хотя и происходят изменения в структурном состоянии механические свойства при этом практически не меняются. На стадии же циклического упрочнения или разупрочнения происходит интенсивное изменение механических свойств.
Результаты экспериментов приведены на рис. 2 – 4.
Рис. 2. Сравнение тангенса угла наклона для образца №3
Анализируя представленные графики, можно утверждать, что для образцов №3 и №6 наибольшие изменения тангенса угла наклона происходили в перовом эксперименте, в начале испытаний. Для образца №5 такие изменения находились в пределах погрешности.
Во втором эксперименте заметных изменений тангенса угла наклона во всех трех образцах зафиксировано не было.
С точки зрения физико-химических процессов, растворенные в феррите элементы, в исходном состоянии, приводят к тому, что образуется неравновесная термодинамическая система, которая постепенно стремится
50
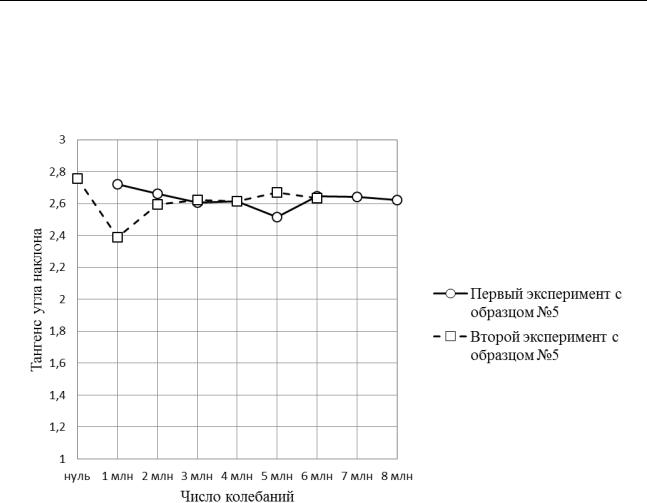
ТРАНСВУЗ – 2015
перейти в равновесное состояние. Основным механизмом такого перехода является диффузия легированных элементов. Скорость диффузии в этом случае будет существенно зависит от внешнего напряжения, понижающего потенциальный барьер и температуры.
Рис. 3. Сравнение тангенса угла наклона для образца №5
Возможны два механизма выхода углерода: а) на границы зерен; б) рост карбидов.
Диффузия атомов углерода к дислокациям приводит к разупрочнению феррита, он как бы становится «мягче», сталь становится пластичнее. Рост карбидов, напротив, приводит к тому, что доля «жесткой» фазы в стали увеличивается, повышается суммарная твердость, происходит охрупчивание [5]. Именно это состояние является наиболее опасным и критическим. Вероятность хрупкого разрушения становится наибольшей.
Выводы:
1) Наибольшие изменения модуля Юнга происходят в начальный период нагружений, в интервале от 0 до 2 млн. колебаний, далее происходит стабилизация происходящих изменений в пределах погрешности.
51
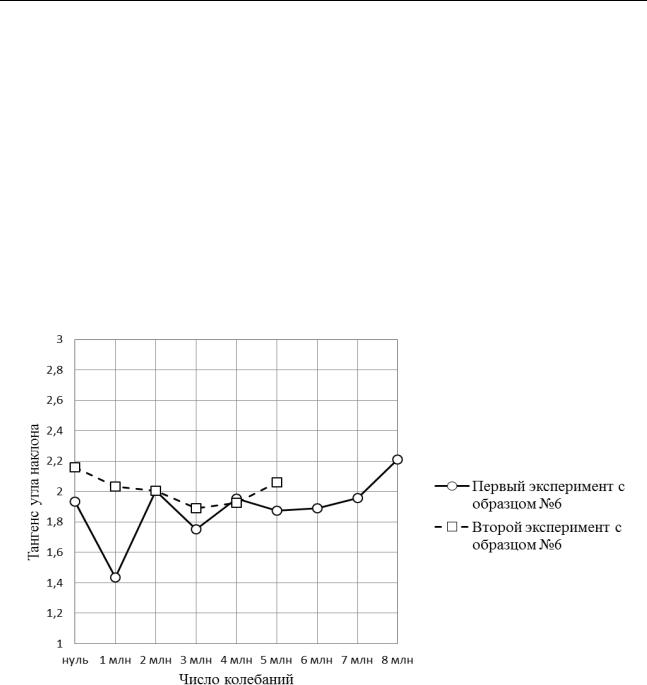
Ремонт и динамика подвижного состава
2) Значений модуля Юнга могут изменяться как в сторону увеличения, так и в сторону уменьшения. Выяснение причины направления изменений требует дополнительных исследований.
3) Согласно [6], увеличение значения модуля Юнга связано с изменением других характеристик кристаллических веществ: увеличением относительной и абсолютной твердости, уменьшением коэффициента теплового линейного расширения, увеличением скорости звука, увеличением теплопроводности и др.
4) Существует принципиальная возможность создания эффективного способа определения преддефектных критических состояний узлов и деталей грузовых вагонов железнодорожного транспорта.
Рис. 4. Сравнение тангенса угла наклона для образца№6
Авторы выражают искреннюю благодарность доценту кафедры «Технология транспортного машиностроения и ремонта подвижного состава» ОмГУПС, к.т.н. Ражковскому А. А. и заведующему лабораториями кафедры «Физика и химия» ОмГУПС Кондрикову Е. М. за помощь в проведении экспериментов.
52

ТРАНСВУЗ – 2015
Список литературы
1.Распоряжение Правительства РФ от 17.06.2008 № 877-р «О стратегии развития железнодорожного транспорта в Российской Федерации до 2030 года».
2.Левкович, Т. И. Прогнозирование вероятности опасных хрупких разрушений корпусов автосцепок вагонов: Автореф. дис. канд. техн. наук [Текст] / Т. И. Левкович / Брянский гос. техн. ун-т. – Брянск, 2000. – 22с.
3.Пат. 143895 Российская Федерация, МПК G 01 N 3/32. Устройство для ускоренного определения остаточного ресурса металлических ферромагнитных изделий [Текст] / Ю.И. Матяш, Ю.М. Сосновский, А.А. Ражковский, Е.М. Кондриков (Россия); заявитель и патентообладатель Омский гос. ун-т путей сообщения. – № 2014105761; заявл. 17. 02.2014; опубл.
02.07.2014.
4.Пат. 154462 Российская Федерация, МПК G 01 N 3/38. Лабораторная установка для ускоренного определения остаточного ресурса металлических ферромагнитных изделий с учётом комбинированной нагрузки [Текст] / Ю. И. Матяш, Ю. М. Сосновский, Е. М. Кондриков (Россия); заявитель и патентообладатель Омский гос. ун-т путей сообщения. – № 2014147715; заявл. 26.11.2014; опубл. 30.07.2015.
5.Матяш, Ю. И. Физико-химические основы оценки остаточного ресурса узлов и деталей грузовых вагонов железнодорожного транспорта [Текст] / Ю. И. Матяш, Ю. М. Сосновский, А. Г. Петракова // Известия Транссиба / Омский гос. ун-т путей сообщения. – Омск, –2015. №2(22). – С.
12 – 18.
6.Зуев, В. В. Кристаллоэнергетика как основа оценки свойств твердотельных материалов [Текст] / В. В. Зуев, Л. Н. Поцелуева, Ю. Д. Гончаров / Завод «Альфапол». – СПб, 2006. – 139 с.
53
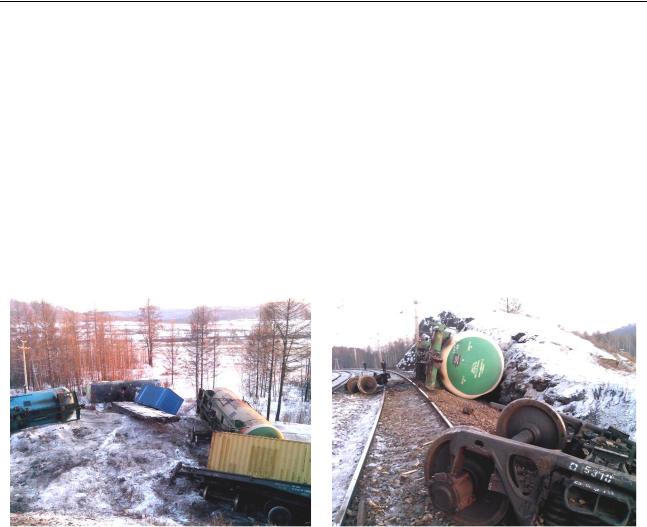
Ремонт и динамика подвижного состава
УДК. 629.4.027.2
Р. А. Ахмеджанов, А. О. Бельский
СОВЕРШЕНСТВОВАНИЕ КОНСТРУКЦИИ БОКОВОЙ РАМЫ ДВУХОСНОЙ ТРЕХЭЛЕМЕНТНОЙ ТЕЛЕЖКИ ГРУЗОВОГО ВАГОНА
В последние годы на сети железных дорог России участились изломы боковых рам двухосных трехэлементных тележек, которые вызвали сход подвижного состава и крушения (рис. 1 а, б) с человеческими жертвами.
а б Рис. 1. Последствия излома боковой рамы
В период с января 2002 г. по сентябрь 2015 г. произошло 166 изломов боковых рам (рис. 2). При этом число изломов до 2014 г. постоянно увеличивалось (см. рис. 2) и в 2013 г. достигло рекордных 34 случаев. Уменьшение количества изломов в 2014 г. и 2015 г. связано с увеличением отцепок грузовых вагонов в текущий ремонт по трещинам боковых рам, что в свою очередь связано с введением в действие новых критериев браковки литых деталей тележки [1]. Изломы боковых рам нанесли значительный экономический ущерб как для ОАО «РЖД», так для собственников подвижного состава: стоимость устранения их последствий, без учета затрат на восстановление поврежденного подвижного состава и груза, составляет десятки млн. рублей. Один из изломов боковых рам, произошедший на железных
54
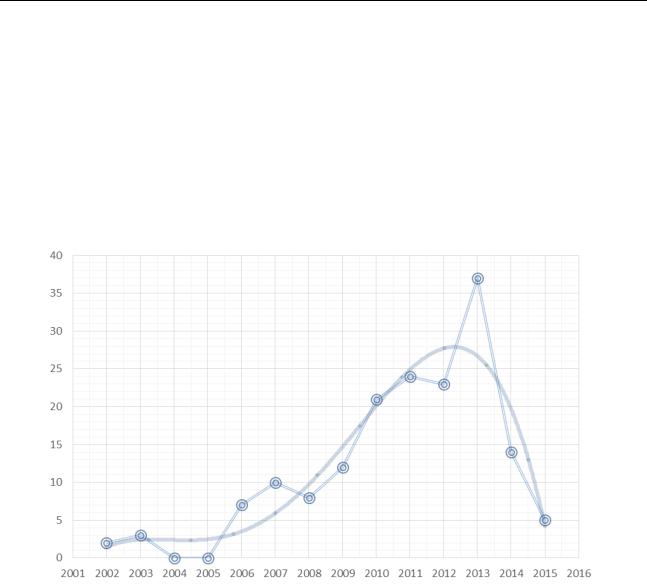
ТРАНСВУЗ – 2015
дорогах России в 2013 г., впервые привел к трагическим последствиям: в результате крушения поезда 12 января 2013 г. погибли машинист и помощник машиниста одиночного локомотива, проходящего по встречному пути. Анализ изломов боковых рам показывает, что 75 % от общего количества произошли в период 3 – 6 лет эксплуатации после изготовления. Предотвратить излом боковой рамы в эксплуатации практически невозможно, так как трещины зарождаются во внутреннем углу буксового проема, который недоступен для визуального осмотра.
Рис. 2. Распределение случаев излома боковых рам двухосных трёхэлементных тележек грузовых вагонов в период 2002 – 2015 гг.
Кроме того, на ПТО за период с 2006 г. по 2013 г. выявлено и подтверждено осмотрщиками-ремонтниками вагонов более 35 тысяч дефектов в боковых рамах тележек, и тем самым предотвращено более 35 тысяч случаев транспортных происшествий, которые могли повлечь за собой изломы боковых рам. За этот же период в среднем средствами неразрушающего контроля выявлено наличие дефектов в 11 тыс. боковых рамах, т. е. можно сделать вывод, что дефектообразование в боковых рамах имеет массовый характер.
Поиском причин и способов предотвращения неисправностей и изломов боковых рам в настоящее время занимаются ведущие предприятия-
55

Ремонт и динамика подвижного состава
изготовители и научные организации в России и в странах СНГ. Однако, что до сих пор нет однозначного ответа на вопрос: «по какой причине произошел излом боковины?». Одни считают, что решение проблемы заключается в недостаточном качестве изготовления боковых рам, другие – в плохом содержании железнодорожного пути, третьи – из-за нарушения правил эксплуатации и ремонта подвижного состава, четвертые – в несовершенстве конструкции подвижного состава.
По мнению авторов настоящей статьи, основной причиной изломов и является несовершенство как конструкции боковой рамы, так и конструкции тележки в целом. Следует отметить, что в настоящее время под грузовыми вагонами находятся тележки моделей 18-100, 18-100М, 18-578 и их аналоги, конструкции которых незначительно отличаются от внедренной в серийное производство в 1956 г. тележки ЦНИИ-Х3-О (теперь 18-100). Тележка ЦНИИ- Х3-О является ухудшенным вариантом американской тележки Barber, разработанной в 1926 г. в США.
В тележке ЦНИИ-Х3-О за более чем 55 лет эксплуатации были увеличены межремонтный пробег до 160 тыс. км и нагрузка на ось: в 1976 г. проектная нагрузка была увеличена с 21 до 22 тс, в 1977 г. – до 23, а позднее и до 23,5 тс. В боковой раме проведены следующие конструктивные улучшения: заменен двутавровый профиль концевой части (рис. 3, а) на коробчатый (рис. 3, б); изменена марка стали, из которой отливается рама; защищены пары трения износостойкими накладками. Введение коробчатого сечения в концевой части позволило увеличить прочность наружного угла буксового проема боковой рамы на 15 – 20 %, но это не привело к увеличению прочности внутреннего угла буксового проема. Можно сделать вывод о том, что увеличение осевой нагрузки и межремонтных пробегов стали возможным во многом благодаря заложенному конструкторскому запасу прочности еще при разработке тележки модели ЦНИИ-Х3-О.
К настоящему времени разработаны следующие конструкции боковых рам: с модернизированными усиливающими ребрами внутреннего угла буксового проема (рис. 4, а, б); с усиливающими ребрами в зоне радиуса R55 или дополнительными внутренними ребрами; рамы, имеющие измененную
56
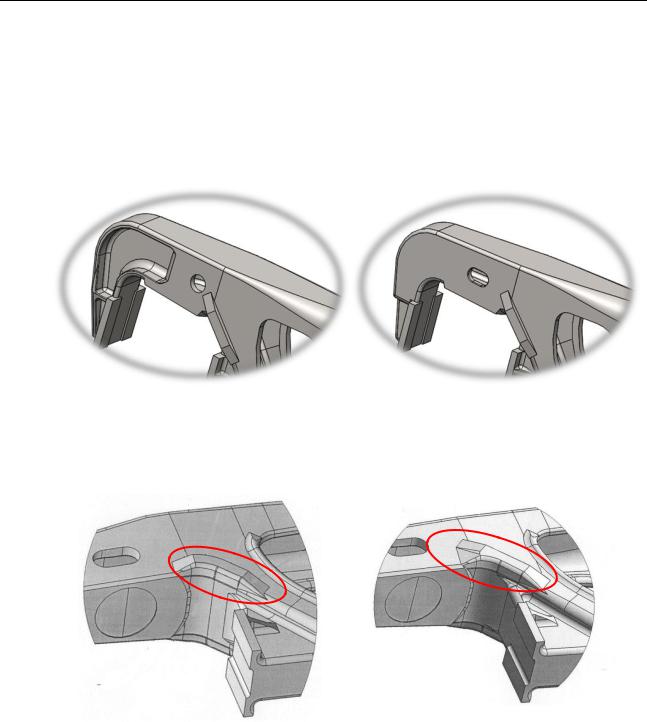
ТРАНСВУЗ – 2015
форму сечений в местах радиусных переходов нижнего и наклонного поясов и опорных поверхностей для корпусов буксы; рамы с буксовыми проемами, выполненными в виде замкнутой в горизонтальной плоскости усеченной сверху многогранной пирамиды с открытым основанием; с наклонной надбуксовой поверхностью; с измененной нижней частью опорной поверхности буксового проема и др.
а б Рис. 3. Профили концевых частей боковых рам тележки модели 18-100:
а – двутавровый, б – коробчатый
а б Рис. 4. Боковая рама с усиливающими наклонными ребрами
Как показала практика, введение наружных или внутренних подкрепляющих ребер, утолщение и изменение формы нижних стенок или верхних поясов не повышают прочности элементов боковой рамы до желаемой,
57
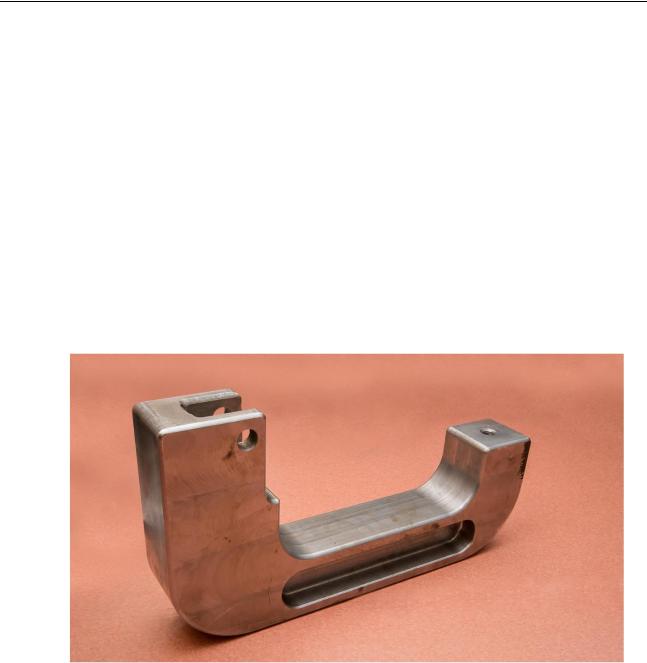
Ремонт и динамика подвижного состава
но увеличивают ее массу и повышают вероятность возникновения в этих местах литейных дефектов.
Авторы настоящей статьи видят совершенствование конструкции боковой рамы в снижении и перераспределения нагрузок, действующих на буксовые проемы боковой рамы, как наиболее подверженных изломам. Для этого в конструкцию буксовых проемов боковой рамы предложено ввести устройство (рис. 5), обеспечивающее соединение концевых частей наружной и внутренней челюстей в каждом буксовом проеме и выполненное в виде специальной скобы. Соединения скоб осуществляется соответствующим болтовым комплектом к наружной челюсти и опорному приливу внутренней челюсти.
Рис. 5. Подбуксовая скоба
Согласно теоретическим исследованиям по «Нормам…» [2], проведенными авторами настоящей статьи на кафедре «Вагоны и вагонного хозяйства» ОмГУПС с использованием уточненной математической модели [3, 4] методом конечных элементов, напряжения в опасных сечениях (рис. 6.) снижаются до значений (табл. 1), позволяющих повысить срок службы боковых рам в эксплуатации (табл. 2). Выводы о работоспособности боковой рамы в
58
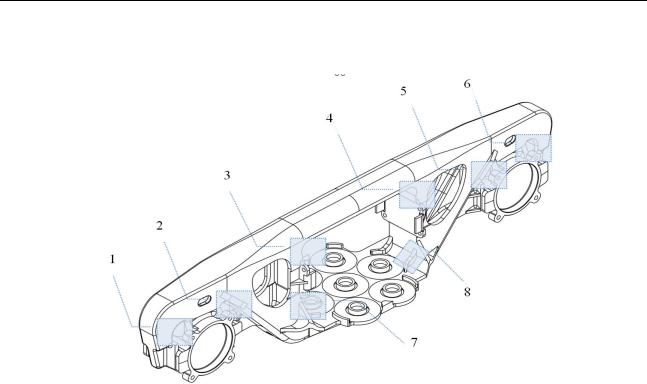
ТРАНСВУЗ – 2015
течении срока служба выполнены так же на основе метода конечных элементов и рекомендаций «Норм...».
Рис. 6. Опасные сечения боковой рамы:
1 – наружный угол буксового проема, 2 – внутренний угол буксового проема, 3 – верхний угол рессорного проема, 4 – верхний угол рессорного проема,
5 – внутренний угол буксового проема, 6 – наружный угол буксового проема, 7 – нижний угол рессорного проема, 8 – нижний угол рессорного проема
Исследования показали, что разработанное устройство позволяет значительно улучшить прочностные характеристики буксового проема боковой рамы двухосных трехэлементных тележек. Так напряжения в наружном углу 1 при I расчетном режиме уменьшились в 3 раза, при III расчетном режиме – уменьшились в 1,58 раз; во внутреннем углу 2 буксового проема при I расчетном режиме уменьшились в 2 раза, при III расчетном режиме – уменьшились в 1,3 раза. Стоит отметить, что применение предложенного технического решения оказывает положительный эффект на верхние углы рессорного проема боковой рамы (зоны 3 и 4). Так при I расчетном режиме напряжения в зоне 3 уменьшились в 2,57 раза, а в зоне 4 – в 1,47 раза. При III расчетном режиме напряжения в зоне 3 уменьшились в 1,6 раза, а в зоне 4 – осталось на прежнем уровне. В остальных зонах модернизированной боковой рамы напряжения остались на прежних уровнях по сравнению с серийно выпускаемой. Единственной зоной в модернизированной боковой раме, где
произошло увеличение напряжений, |
а не |
их уменьшение, является зона |
6. Увеличение напряжений в этой |
зоне |
связано с появлением усилия, |
|
59 |
|