
ТРАНСВУЗ-2015.Часть 3
.pdf
Ремонт и динамика подвижного состава
3. Бисерикан, М. И. Совершенствование технологии обточки колес подвижного состава с усталостными дефектами [Текст] / М. И. Бисерикан, Ю. А. Иванова, В. В. Иванов // Омский научный вестник. Сер. Приборы, машины и технологии. – 2012. – № 2 (110). – С. 120 – 124.
УДК 629.1.027.115
А. В. Бородин, Д. Б. Гриц
О СОВЕРШЕНСТВОВАНИИ БУКСЫ ГРУЗОВОГО ВАГОНА
При планируемом увеличении скоростей движения и нагрузок на ось необходимы конструктивные решения буксы грузового вагона с целью повышения ее работоспособности. Предложена конструкция буксы грузового вагона и произведен расчет подшипников, входящих в состав буксы. Согласно расчетам, усовершенствованная конструкция буксы грузового вагона способна воспринимать повышенные нагрузки.
На восприятие нагрузки между двумя подшипниками или между двумя рядами тел качения существенное влияние оказывает изгиб шейки вагонной оси под нагрузкой, так как каждый тип подшипника эффективно работает при определенных значениях угла поворота оси. Взаимный перекос колец возникает при упругой деформации шейки оси от воздействия радиальных составляющих сил, действующих на колесную пару вагона.
На рис. 1 представлены значения деформации оси соответствующие заднему подшипнику при осевых нагрузках вагона 23,5; 25; 27; 30 тс [1].
Проведенные расчеты в работе [1], а так же планируемое увеличение осевой грузоподъемности вагонов до 27 – 30 тс и скоростей движения до 140 км/ч, согласно Стратегии развития железнодорожного транспорта Российской Федерации до 2030 г. [2] приводят к выводу о необходимости конструктивных решений буксы грузового вагона с целью повышения ее работоспособности.
Для решения поставленной цели предложена конструкция буксы грузового вагона со ступенчатой осью [3] (рис. 2).
40
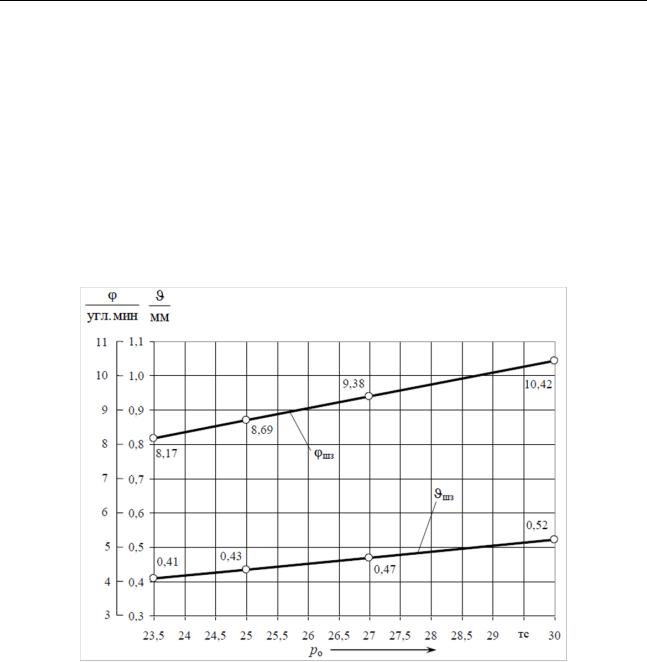
ТРАНСВУЗ – 2015
Долговечность и грузоподъемность подшипника, используемого в буксе, не должна быть меньше чем у типового подшипника.
В табл. 1 приведены параметры подшипников, используемые при расчетах.
При расчетах были приняты следующие допущения:
1.Рамная сила, действующая в кривых не учитывалась;
2.При расчете радиальной нагрузки считалось что 30% времени вагон в порожнем состоянии, 70% – в груженом.
3.Расчет проводился для скорости движения 60 км/ч, что соответствует частоте вращения равной 353,68 об/мин.
Рис. 1. График зависимости прогиба и угла поворота сечения оси φ от осевой нагрузки po
Статическая грузоподъемность радиальных подшипников с короткими цилиндрическими роликами, Н:
|
|
C0 2,2 i z leff |
D cos , |
(1) |
где i |
– число рядов роликов; |
|
|
|
z |
– число роликов в одном ряду; |
|
|
|
leff |
–эффективная длина зоны контакта ролика с кольцом, мм; |
|
||
D |
– диаметр тела качения, мм; |
|
|
|
|
|
41 |
|
|
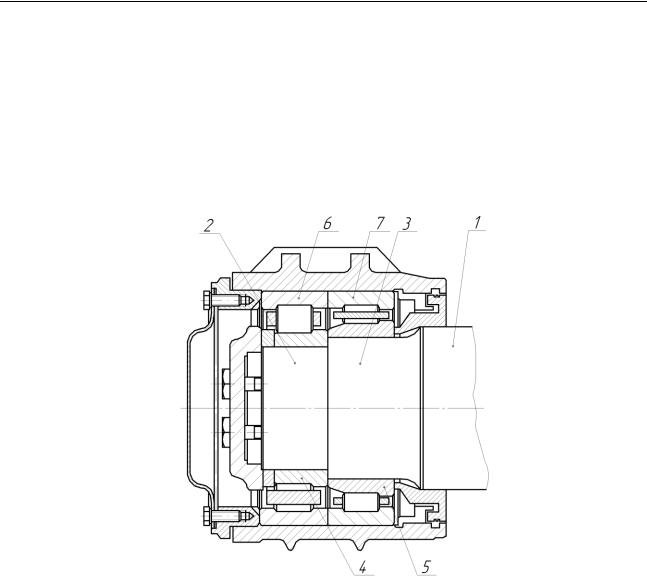
Ремонт и динамика подвижного состава
– номинальный угол контакта, град.
Динамическая грузоподъемность радиальных подшипников с короткими цилиндрическими роликами, Н:
|
Ñ f |
c |
(i l |
cos )7 / 9 z3 / 4 D29/ 27 |
, |
(2) |
|
|
eff |
|
|
|
|
где |
fc – коэффициент, зависящий |
от геометрии деталей |
подшипников, |
точности их изготовления и материала.
Рис. 2. Букса грузового вагона: 1 – ось; 2 – первая ступень оси; 3 – вторая ступень оси; 4 – внутреннее кольцо подшипника;
5 – внутреннее кольцо подшипника; 6 – наружное кольцо подшипника; 7 – наружное кольцо подшипника
Значение коэффициента fc |
для радиальных роликоподшипников, |
выполненных из закаленной стали ШХ15, или иной, той же твердости, выбирается из табл. 2 [4] по отношению:
D cos |
, |
(3) |
|
dm |
|||
|
|
где dm – диаметр окружности, проходящей через центры роликов, мм.
42

|
|
|
ТРАНСВУЗ – 2015 |
|
|
|
|
|
|
|
Таблица 1 |
|
Параметры подшипников |
|
|
|
|
|
|
|
Параметр |
Типовой |
Модернизированный |
|
подшипник |
подшипник |
|
|
|
||
|
|
|
|
|
Количество тел качения |
15 |
22 |
|
|
|
|
|
Диаметр тела качения, мм |
32 |
25 |
|
|
|
|
|
Эффективная длина зоны контакта |
50 |
50 |
|
ролика с кольцом, мм |
||
|
|
|
|
|
|
|
|
|
Диаметр окружности, проходящей |
190 |
200 |
|
через центры роликов, мм |
||
|
|
|
|
|
|
|
|
|
Диаметр дорожки качения наружного |
206 |
225 |
|
кольца, мм |
||
|
|
|
|
|
|
|
|
|
Наружный диаметр подшипника, мм |
250 |
250 |
|
|
|
|
|
Посадочный диаметр подшипника, мм |
130 |
150 |
|
|
|
|
Используя линейную интерполяцию можно более точно определить значение коэффициента fc .
Расчет долговечности роликовых подшипников с короткими цилиндрическими роликами можно произвести по формуле, млн. км:
|
|
C p |
|
||||
|
L |
|
|
, |
(4) |
||
|
|
||||||
|
|
|
P |
|
|||
где P – эквивалентная нагрузка, Н; |
|
|
|
|
|
||
p |
– степенной показатель равный |
10 |
|
для роликоподшипника. |
|||
|
|||||||
|
|
|
3 |
|
|
||
В общем виде эквивалентная нагрузка определяется как: |
|||||||
P X V Fr Y Fa ká kò , |
(5) |
|
|
|
|||
где X – коэффициент радиальной нагрузки; |
|||||||
V |
– коэффициент вращения; |
|
|
|
|
|
|
Fr |
– радиальная нагрузка, действующая на подшипник, Н; |
||||||
Y |
– коэффициент рамной силы; |
|
|
|
|
|
|
Fa |
– рамная сила, Н; |
|
|
|
|
|
|
ká |
– коэффициент безопасности; |
|
|
|
|
|
|
kò |
– температурный коэффициент. |
|
|||||
|
|
|
43 |
|
|

Ремонт и динамика подвижного состава
С учетом допущений, принятых при расчетах формулу (5) можно записать в виде:
P X V Fr ká kò . |
(6) |
Помимо грузоподъемности и долговечности подшипников необходимо учесть допустимую осевую нагрузку. При пластичной смазке, используемой в буксах грузовых вагонов, осевая нагрузка, которую может воспринимать подшипник, рассчитывается по формуле, Н:
|
|
|
2 |
|
|
|
n D1 |
|
|
||
|
Fa |
fa fb D1 |
2 |
|
|
|
|
, |
(7) |
||
|
100000 |
|
|||||||||
|
|
|
|
|
|
|
|
|
|||
где fa |
– коэффициент, зависящий от условий нагружения; |
|
|||||||||
fb |
– коэффициент, зависящий от типа и серии подшипника; |
|
|||||||||
D1 |
– диаметр дорожки качения наружного кольца, мм; |
|
|||||||||
n – частота вращения, об/мин. |
|
|
|
|
|
|
|
|
|||
Коэффициенты fa и fb |
выбираются из табл. 27 и 28 [5] соответственно. |
|
|||||||||
Результаты расчетов грузоподъемности и долговечности для обоих типов |
|||||||||||
подшипников приведены в табл. 2. |
|
|
|
|
|
|
|
|
|||
|
|
|
|
|
|
|
|
|
|
Таблица 2 |
|
|
|
|
Результаты расчета |
|
|||||||
|
|
|
|
|
|
|
|
|
|
|
|
|
|
|
Типовой подшипник |
|
Модернизированный |
|
|||||
|
|
|
|
подшипник |
|
||||||
|
|
|
|
|
|
|
|
|
|
|
|
|
|
|
|
|
|
|
|
|
|
|
|
Статическая |
|
517791 |
|
|
|
|
593302 |
|
|||
грузоподъемность, Н. |
|
|
|
|
|
|
|||||
|
|
|
|
|
|
|
|
|
|
||
|
|
|
|
|
|
|
|
|
|
|
|
Динамическая |
|
514945 |
|
|
|
|
515998 |
|
|||
грузоподъемность, Н. |
|
|
|
|
|
|
|||||
|
|
|
|
|
|
|
|
|
|
||
|
|
|
|
|
|
|
|
|
|||
Долговечность, млн. об. |
|
321,94 |
|
|
|
|
324,14 |
|
|||
|
|
|
|
|
|
|
|
|
|
|
|
Увеличение долговечности на 2,2 млн. об. позволит производить плановый ремонт подшипников в одно время, не прибегая к дополнительному обслуживанию буксового узла. Помимо этого, ступенчатая конструкция оси позволяет при монтаже внутренних колец подшипников не нарушать посадочные размеры, обеспечивая гарантированный натяг, в свою очередь, это дает возможность исключить проворот внутреннего кольца.
44
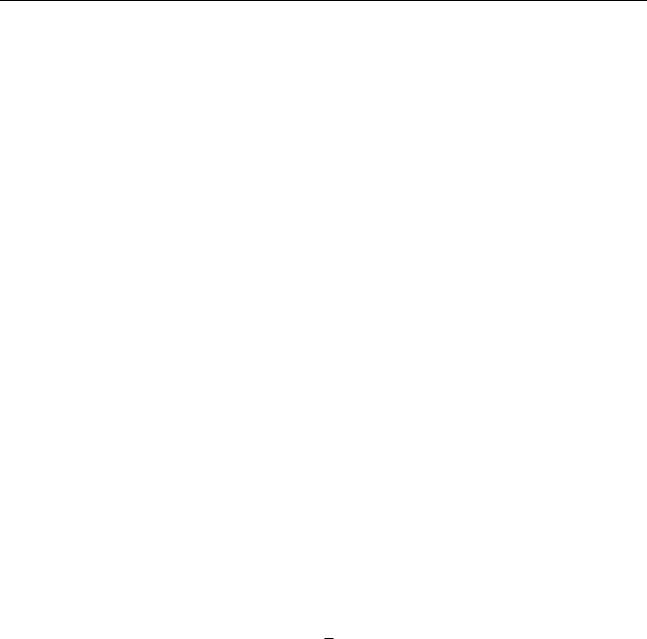
ТРАНСВУЗ – 2015
В табл. 3 приведены результаты расчета допустимой осевой нагрузки при различных условиях действия осевой нагрузки, типах и сериях подшипников.
Таблица 3
Допустимая осевая нагрузка
Условия |
Тип и серия |
Типовой |
Модернизированный |
|
нагружения |
подшипника |
подшипник |
подшипник |
|
|
|
|
|
|
|
2 и 5 |
25897,99 |
29262,67 |
|
|
|
|
|
|
Постоянное |
3 и 6 |
32372,49 |
36578,34 |
|
|
|
|
|
|
|
4 |
35609,74 |
40236,18 |
|
|
|
|
|
|
Периодическое |
2 и 5 |
51795,99 |
58525,35 |
|
|
|
|
||
3 и 6 |
64744,98 |
73156,69 |
||
и прерывное |
||||
|
|
|
||
4 |
71219,48 |
80472,35 |
||
|
||||
|
|
|
|
|
|
2 и 5 |
77693,98 |
87788,02 |
|
|
|
|
|
|
Ударное |
3 и 6 |
97117,47 |
109735,03 |
|
|
|
|
|
|
|
4 |
106829,22 |
120708,53 |
|
|
|
|
|
Поскольку в буксе устанавливается два подшипника, то необходимо рассматривать их как опору из системы подшипников и определить срок службы до первого выхода одного из подшипников из строя:
1 |
|
1 |
|
1 |
... |
1 |
, |
(8) |
e |
e |
e |
e |
|||||
L |
L |
L |
L |
|
||||
|
|
1 |
|
2 |
|
n |
|
где L1e , Le2 ,..., Len – долговечность каждого подшипника, входящего в систему;
e – степенной показатель равный 9 для роликовых подшипников [5].
8
Долговечность системы подшипников будет всегда меньше чем долговечность каждого подшипника в отдельности. Таким образом, для буксы с двумя типовыми подшипниками долговечность системы подшипников составит 173,86 млн. об., а для модернизированной буксы – 174,45 млн. об.
Сравнивая результаты расчетов, можно сделать вывод о том, что модернизированная букса грузового вагона в условиях планируемого повышения осевой нагрузки и скоростей движения за счет увеличения жесткости оси и уменьшения перекоса колец подшипников способна воспринимать повышенные нагрузки.
45

Ремонт и динамика подвижного состава
Список литературы
1.Бородин, А. В. Пути повышения работоспособности букс грузовых вагонов [Текст] / А. В. Бородин, Ю. А. Иванова, Д. Б. Гриц // Материалы научно-практической конференции, посвященной Дню Российской науки. – Омск: изд-во Омского гос. ун-та путей сообщения, 2014. – С. 170-175.
2.Гапанович, В. А. Белая книга ОАО «РЖД»: Стратегические направления научно-технического развития компании [Текст] / В. А. Гапанович
//Железнодорожный транспорт. 2007. №8. С. 2-6.
3.Пат. 149000 Российская Федерация, МПК B 61 F 5/52. Букса грузового вагона [Текст] / А. В. Бородин, Д. Б. Гриц; заявитель и патентообладатель Омский гос. ун-т путей сообщения. — № 2014129461/11; заявл. 17.07.2014; опубл. 20.12.2014, Бюл. № 35. — 4 с.: ил.
4.Расчет и выбор подшипников качения [Текст]: справочник / Н. А. Спицын [и др.]. – М.: «Машиностроение», 1974. – 57с.
5.Перель, А. Я. Подшипники качения: Расчет, проектирование и обслуживание опор [Текст]: справочник / А. Я. Перель. – М.: «Машиностроение», 1983. – 543 с.
УДК 629.46
Ю. И. Матяш, Ю. М. Сосновский, Д. В. Колосов
ЭКСПЕРИМЕНТАЛЬНОЕ ОПРЕДЕЛЕНИЕ КРИТИЧЕСКИХ СОСТОЯНИЙ УЗЛОВ И ДЕТАЛЕЙ ГРУЗОВЫХ
ВАГОНОВ ЖЕЛЕЗНОДОРОЖНОГО ТРАНСПОРТА
Разработана оригинальная экспериментальная установка. Представлены экспериментальные результаты лабораторных исследований изменения механических свойств стали при упругом нагружении. Показано, что в начале эксперимента изменения упругих свойств стали наиболее выражены. На основе связи модуля Юнга с физическими характеристиками стали высказано предположение о возможности диагностирования этих изменений в узлах и деталях грузовых вагонов железнодорожного транспорта.
Одним из стратегических направлений инновационного развития ОАО
46

ТРАНСВУЗ – 2015
«РЖД» является совершенствование системы управления и обеспечения безопасности движения поездов, снижение рисков чрезвычайных ситуаций [1]. В связи с этим, вопросы, связанные с, достоверным определением остаточного ресурса узлов и деталей подвижного состава (боковая рама, надрессорная балка и др.), работающие в условиях постоянно повышенных нагрузок является актуальным.
К наиболее распространенным практическим методам выявления дефектов относятся: визуальный осмотр, ультразвуковой и магнитопорошковый методы. При этом оценка механических свойств металла на ремонтных предприятиях ОАО РЖД не производится. Это связано с отсутствием оборудования, позволяющего обнаружить изменение структуры металла, механических свойств и возможности прогнозирования поведения детали в процессе эксплуатации. При этом, в научной литературе встречаются данные подтверждающие факт структурных изменений узлов и деталей грузовых вагонов в процессе эксплуатации [2].
Цель нашего эксперимента заключалась в определении механических изменений свойств конструкционной стали 45 в процессе усталостного знакопеременного нагружения и установления возможности диагностирования этих изменений в условиях производства.
Выбор данной марки стали был обусловлен, тем, что количество углерода в ней составляет примерно промежуточное значение между количеством углерода в сталях марки 20 ГФЛ, 20 ФЛ-У, 20 Л, используемых для изготовления боковых рам, надрессорных балок, корпусов автосцепок (доля углерода 0,17% – 0,25%) и рельсовых сталях (доля углерода 0,83% – 0,90%).
В качестве исследуемого объекта были изготовлены стальные образцы в форме прямоугольного параллелепипеда (рис. 1). Материал испытуемых образцов – сталь 45. Физические и геометрические параметры исследуемых образцов указаны в табл. 1, а их химический состав указан в табл. 2.
Для проведения экспериментальных исследований была разработана оригинальная лабораторная установка работа которой и её возможности подробно описаны в [3, 4].
Испытуемый образец одним концом жестко закреплялся в фиксирующем устройстве, а незакрепленный конец помещался в область разрезанного сердечника силового трансформатора. Под действием переменного магнитного
47
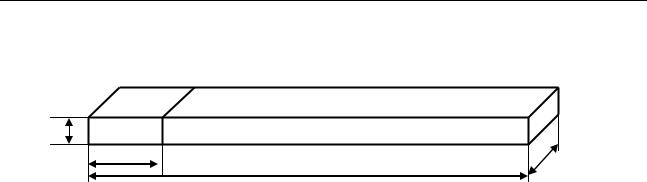
Ремонт и динамика подвижного состава
поля свободный конец образца начинал вибрировать с частотой равной частоте переменного магнитного поля 50 Гц.
c
d
b
а
Рис. 1. Форма и маркировка образца
Таблица 1 Физические и геометрические параметры исследуемых образцов
№ |
a, мм |
b, мм |
c, мм |
m, гр |
d, мм |
|
|
|
|
|
|
3 |
88,0 |
5,7 |
3,6 |
13,40 |
10 |
|
|
|
|
|
|
5 |
85,6 |
5,7 |
3,6 |
13,05 |
10 |
|
|
|
|
|
|
6 |
87,6 |
5,7 |
3,6 |
13,35 |
10 |
|
|
|
|
|
|
Таблица 2
Химический состав конструкционной стали 45
Химический элемент |
Содержание элементов (вес. %) |
|
|
Железо (Fe) |
≈97 |
|
|
Углерод (C) |
0,42-0,50 |
|
|
Кремний (Si) |
0,17-0,37 |
|
|
Медь (Cu), не более |
0,25 |
|
|
Мышьяк (As), не более |
0,08 |
|
|
Марганец (Mn) |
0,50-0,80 |
|
|
Никель (Ni), не более |
0,25 |
|
|
Фосфор (P), не более |
0,035 |
|
|
Хром (Cr), не более |
0,25 |
|
|
Сера (S), не более |
0,04 |
|
|
Через интервал, примерно 1 миллион колебаний, к свободному концу образца подвешивались грузы массами от 0,1 кг, до 0,6 кг. Под воздействием веса этих грузов, свободный конец начинал прогибаться. Стрела прогиба измерялась микрометром с ценой деления 10 мкм. По результатам этих
48

ТРАНСВУЗ – 2015
измерений строился график зависимости подвешиваемой массы от прогиба. Полученная зависимость аппроксимировалась линейной функцией, по которой определялся тангенс угла наклона прямой.
Эксперимент проходил в два этапа: первый раз весной 2015 года, второй раз осенью 2015 года в лаборатории кафедры физики и химии ОмГУПС.
Следует заметить, что тангенс угла наклона прямой являлся косвенным подтверждением изменения модуля Юнга. Суммарная относительная погрешность измерений не превышала 10%.
Моделируя, таким образом, процесс усталостного нагружения мы исходили из следующих закономерностей:
1.Циклическая нагрузка может вызывать разрушение металла при напряжении не только меньшем предела прочности, но и меньшем предела текучести и предела упругости. Чем ниже напряжение, тем больше нужно приложить смен (циклов) напряжений, чтобы вызвать разрушение образца. Зависимость между напряжением и числом циклов, вызывающим разрушение образца называется кривой Вёлера.
2.Разрушение металла под действием циклической нагрузки носит локальный характер. Чаще всего очаги разрушения образуются на поверхности. Если же поверхность подвергнута упрочнению, то очаги усталостного разрушения могут образовываться и под поверхностью.
3.Способность металла сопротивляться повторным знакопеременным нагрузкам характеризуется циклической вязкостью металла. Она характеризует способность металлов поглощать энергию в необратимой форме. Кривые деформации при нагружении и разгружении не совпадают между собой, а образуют петлю гистерезиса. Площадь петли гистерезиса характеризует ту энергию, которую металл способен поглотить за один цикл.
4.Согласно теории кинетической прочности процесс разрушения на начальной стадии следует рассматривать как процесс, в котором вследствие тепловых флуктуаций преодолевается энергетический барьер U0, величина которого может быть уменьшена в результате действия внешних напряжений σ. Внешняя нагрузка σ и повышение температуры приводит к повышению вероятности флуктуационного перехода.
5.Период зарождения усталостных трещин, согласно можно разделить на три основные стадии: стадия циклической микротекучести, стадия циклической текучести и стадия циклического упрочнения (разупрочнения).
49