
книги / Разрушение твердых тел
..pdf7. Хрупкости не наблюдается при испытаниях на сжатие.
8. Явление водородной хрупкости можно достаточно эффек тивно предупредить отжигом при 425—475° К в течение 24 ч.
В ранних работах было высказано предположение о том, что водородная хрупкость связана с образованием железо-водород ных соединений. В 1941 г. Цаппфе и Симс [155] предположили, что накопление водорода в «полостях» может привести к созданию высоких внутренних давлений, причем по достижении некоторого критического давления образуются трещины. Эта простая гипо теза не согласуется с некоторыми экспериментальными данными, но ее основные идеи использованы в ряде последующих теорий; при этом местами накопления водорода считают обычно микро трещины, создаваемые дислокациями. Бастьен и Азу [162] пред положили, что водород может проникать в пустоты или трещины под воздействием дислокаций, увлекающих за собой атомы водо рода, которые образуют вокруг этих дислокаций атмосферы Коттрелла. Однако при комнатной температуре водород не обна руживает сильного притяжения к дислокациям.
Петч и Стэйблз [111, 112] высказали предположение о том, что главной причиной водородной хрупкости железа является адсорбция водорода в вершинах трещин, образованных дислока циями. Авторы считают, что распространение трещины облегчает ся, если возникновение новых участков поверхности сопровож дается образованием адсорбционных слоев, так как в результате адсорбции поверхностная энергия снижается. Петч получил сле дующее уравнение для разрушающего напряжения:
|
o/ = °o + |
4 [3GY/7t(l — v)^ i]V*» |
(15) |
где |
сто — постоянная; |
поверхностная энергия у снижается в |
|
2Li — диаметр зерна; |
|||
|
в присутствии водорода до величины ун* |
|
|
|
YH = Y- |
2Ws m n [ l +(Л р)’/г]; |
(16) |
здесь |
Ns — удвоенное число адсорбированных молекул на |
||
|
единицу площади при насыщении [Ns = 6,106- |
||
|
• 1014 см~2 для плоскостей ( 100) |
в а-желе- |
|
|
зе] [39]; |
|
|
|
k — постоянная Больцмана; |
|
Т— абсолютная температура;
А^ 5 -104 мм~1— постоянная [39];
р— давление газа.
Уравнение (15) показывает, что величина (Of — Оо) пропор циональна ( 1/Li) ,/г; при этом коэффициент наклона прямой дол жен быть пропорциональным у или ун соответственно для ненаводороженного и наводороженного образцов. На рис. 25 показа
но такое соотношение для |
поликристаллической |
малоуглероди |
стой стали при 291° К при |
содержании водорода |
~ Ю см3 на |
388
100 г металла и для образцов |
без водорода. |
Полагая |
у |
|
я» 1200 мдж/м2, Петч [112] теоретически |
оценил |
величину |
at — |
|
— О0 = 147 М н/м2 (15 кГ/мм2) для |
( 2 |
= 5 м м ~ х>*, что оказа |
лось близко к экспериментальному значению а/ — ао = 169 М н/м2
(17,3 кГ/м м 2).
Однако Билби и Хьюитт [39] считают, что снижение поверх ностной энергии, сопровождающее адсорбцию водорода и не пре вышающее ~ 103 мдж/м2, не может быть достаточной причиной появления хрупкости в поликристаллической стали, так как энер гия разрушения (у0 + р) ненаводороженной стали имеет порядок
105 мдж/м2. Авторы полагают, что наиболее |
важным действием |
|||||
водорода в |
таких |
мате |
|
|
|
|
риалах должно быть сни |
|
|
|
|
||
жение величины р, |
проис |
|
|
|
|
|
ходящее, по всей вероят |
|
|
|
|
||
ности, вследствие осажде |
|
|
|
|
||
ния водорода на дефектах |
|
|
|
|
||
упаковки в о. ц .«. решет |
|
|
|
|
||
ке, что затрудняет |
попе |
|
|
|
|
|
речное скольжение, а сле |
|
|
|
|
||
довательно, |
и размноже |
Рис. 25. Влияние размера зерна на раз |
||||
ние дислокаций. |
|
|||||
Предполагалось |
так |
рушающее |
напряжение |
малоуглероди |
||
стой стали |
при |
291° К |
(Петч [112 ]): |
|||
же [163], что адиабатичес |
/ — без водорода; 2 — |
при содержании |
||||
кое расширение водорода |
водорода |
10 см? |
на 100 г |
|||
в микротрещинах |
при их^ |
|
|
|
|
росте дает дополнительный вклад в выражение для общей вели чины выделяющейся энергии. Тогда необходимая для распрост ранения трещины энергия деформации снижается, а это вызы вает и снижение разрушающего напряжения.
Морлет с сотрудниками [159] изучал влияние предварительной деформации ( 1,5—6,0 % при 77° К) и старения (различной про должительности при 300—400° К) на особенности разрушения наводороженных образцов при комнатной температуре. Пред варительная деформация ведет к повышению пластичности; старсниб первоначально также вызывает повышение пластичности, однако затем наступает ее характерное уменьшение (рис. 26).
В соответствии с моделями Петча и Цапффе, старение после предварительного деформирования способствует диффузии водо рода к полостям или микротрещинам, в результате чего давле ние водорода в них повышается. По этой причине пластичность должна снижаться с увеличением продолжительности старения. Чтобы объяснить это новое явление, Морлет с сотрудниками предложил механизм совместного действия полостей *, водорода
1 Под «полостью» понимается несовершенство решетки, размеры которого велики по сравнению с размерами элементарной ячейки.
и напряжений. Полости, содержащие водород, можно рассмат ривать как эквивалент тонкого внутреннего надреза; при дейст вии приложенного напряжения вокруг каждой полости возника ет трехосное напряженное состояние, которое оказывается наи более жестким на небольших расстояниях от нее. Морлет пред полагает, что степень хрупкости зависит от концентрации водо рода в области максимального проявления трехосного напря женного состояния: при накоплении достаточного количества водорода происходит зарождение трещины. Согласно этой гипо тезе, основное значение имеет концентрация водорода не в поло
стях, а © областях трехосного напряженного состояния вбли зи -полостей.
Верхнюю кривую на -рис. 26 можно тогда объяснить сле дующим образом. На стадии I концентрация водорода в об ластях, где максимально про является трехосное напряжен ное состояние, снижается вследствие диффузии водорода к полостям, размеры которых увеличились в результате пред варительной деформации. Ох рупчивание на стадии II связа но с последующим повышением содержания водорода в обла стях трехосного напряженного состояния вследствие диффу
зии водорода из объема образца при установлении нового рав новесного распределения водорода. Диффузия на последней ста дии может способствовать появлению градиентов концентрации водорода под действием напряжений [164, 165]. Увеличение пла стичности на стадии III наблюдается также в образцах, которые не были предварительно деформированы; его можно объяснить общей дегазацией образца при длительной выдержке при темпе ратуре старения.
В данной схеме развитие трещины рассматривается как пре рывистый процесс; это подтверждается наблюдениями Тетелмена и Робертсона [158]. По достижении критической концентрации водорода в области действия трехосных напряжений перед су ществующей трещиной возникают новые мелкие трещины, кото рые растут в наводороженных областях и соединяются с основ ной трещиной. Следовательно, скорость распространения тре щины зависит от скорости поступления водорода в опасные зоны, т. е. от скорости диффузии, температуры, времени и концентра ции водорода, как и в других схемах. Морлет с сотрудниками
390
считает, что данный механизм удовлетворительно объясняет статическую усталость, а также влияние предварительной дефор мации, скорости деформации и надрезов [165].
Коттерилл [20] обобщил предложенную Морлетом — Джонсо ном— Тройяно теорию осаждения водорода в областях трехос ных напряжений, полагая, что эта теория может объяснить на личие или отсутствие водородной хрупкости не только у сталей, Но и у других материалов. Склонность к водородной хрупкости зависит, в числе прочих факторов, от строения решетки и раз мерного фактора. Коттерилл считает, что у большинства о. ц. к. Металлов высокая локальная концентрация внедренных атомов
водорода должна вызывать значительные деформации, |
а при |
Приложении напряжений — зарождение трещин. Такого |
рода |
хрупкость не должна наблюдаться в металлах с плотноупакованной решеткой, так как атомарный водород может занимать в плотноупакованных решетках октаэдрические положения, не вызывая при этом деформаций. Однако у таких металлов воз можно появление хрупкости при образовании богатой водо родом второй фазы, поскольку она создает прочные препятствия для скольжения дислокаций, что приводит к образованию скоп лений дислокаций, их слиянию и образованию трещин. Таков, вероятно, механизм водородной хрупкости а-титана, «-циркония и «-урана.
Теория Морлета — Джонсона — Тройяно исходит из представ лений об относительно высокой концентрации внедренных атомов водорода, накапливающегося в зонах с трехосными напряжени ями и о возникновении при этом больших деформаций в о. ц. к. решетке. Эта теория встречает ряд возражений [166, 167]. Так, расчеты показывают [166], что максимально возможная концен трация водорода в области трехосных напряжений вблизи поло стей может лишь втрое превышать среднюю концентрацию его в решетке. При этом по данным Хилла [167] концентрация водо рода в «критических» областях в опытах, проведенных Морле том, была вероятно, не выше 0,0001%, и представляется очень мало вероятным, чтобы содержание водорода, отвечающее приб лизительно одному атому водорода на 4000 атомов железа, мог ло привести к наблюдаемым эффектам.
Хилл рассмотрел также возможную форму, в которой водо род содержится в железе — частично экранированные протоны, и закономерности их диффузии. На основе теории диффузии по междоузлиям, предложенной Вертом и Зинером [123], были рас считаны значения коэффициента диффузии D0 в предположении, что водород может занимать либо октаэдрические, либо тетраэд рические положения в решетке. Несколько неожиданным оказа лось, что для обеих моделей расчетные значения D0 оказались равными 1,6*10~3 см2/сек. Высокотемпературные измерения дают значения D0 = 1,4*10-3 см21сек\ хорошее совпадение теоретиче-
скйх и экспериментальных значений D0 указывает в соответствии с теорией Верта — Зинера на невозможность возникновения иска жений решетки при диффузионных перескоках атомов водорода, так как внедреные «частицы» водорода малы по сравнению с рас стояниями между узлами решетки. Было отмечено также [166], что концентрация водорода в микротрещинах в равновесных ус
ловиях превышает его |
концентрацию в решетке примерно в |
104 раз, следовательно, |
трещины являются значительно более |
эффективными накопителями водорода, чем напряженные обла сти решетки, окружающие их.
Тетелмен и Робертсон [158] впервые применили современные металлографические методы к изучению этой проблемы. Авторы использовали методику декорирования дислокаций для исследо вания деформации и разрушения в условиях осаждения водо рода в монокристаллах Fe — 3% Si. Образцы закаливали после нагрева в атмосфере водорода при 1000— 1500° К или проводили катодное насыщение водородом при комнатной температуре. Дислокации, возникшие при пластической деформации или при введении водорода, выявлялись после декорирования углеродом (старение при 430° К в течение 15 мин) по ямкам травления.
Металлографические исследования показывают, что избыток водорода после дегазации осаждается и образует по плоскостям {100} трещины скола типа «гриффитсовых». Пример такой тре щины и связанной с ней дислокационной структуры приведен на рис. 27. Тетелмен и Робертсон установили следующее:
1. По мере насыщения металла водородом происходит разви тие трещин.
2.Размеры трещин зависят от начального содержания водо
рода.
3.Пластическая деформация, связанная с раскрывающимися под действием водорода трещинами, соответствует распределе нию напряжений, рассчитанному Снеддоном [74] для чечевицеоб разной трещины, внутри которой действует давление.
4. Длина наблюдавшихся трещин |
составляла — 2 -10~2 см, |
что вполне согласуется со значениями |
(0,8 * 10~2 см), рассчитан |
ными на основе измерений разрушающего напряжения и поверх ностной энергии, равной удвоенной истинной поверхности энер гии у0, в соответствии с подробным анализом механизма роста трещины.
5. В условиях растяжения при 77° К разрушающее напряже ние предварительно отожженных при 770° К кристаллов с тре щинами, возникшими при катодном насыщении водородом, сов падало с разрушающим напряжением не прошедших термиче ской обработки кристаллов в пределах ±15% . Следовательно, в случае монокристаллов давление газа в трещинах не оказывает заметного влияния на величину внешнего напряжения, необхо димого для их распространения. Однако и теоретические [39,
392
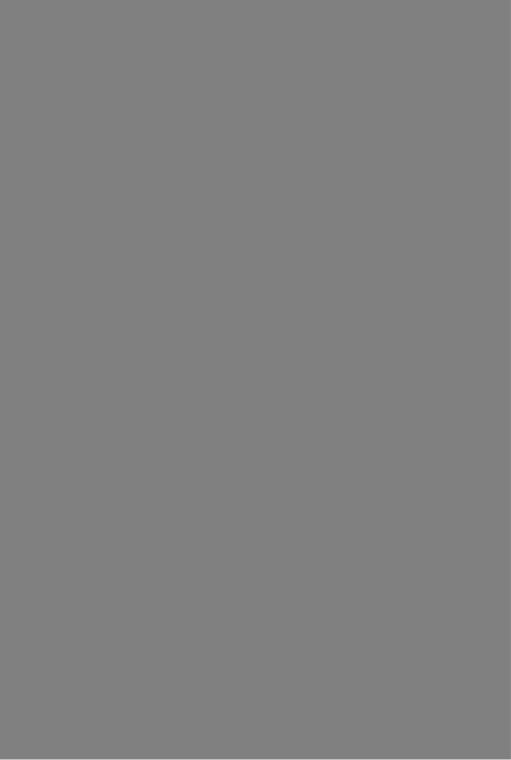
ния ху. Если т/ > 0,6%, то возникающая пластическая деформа ция приводит к притуплению вершины трещины и скола не про исходит. Кристаллы чистого железа не обнаруживают склонно
сти к водородной хрупкости, так как |
у них значение ху мало |
(ту (Fe) ~ 0,25% (Fe - з %si)) и критерий |
Тетелмена — Робертсона |
не выполняется. |
|
Многие вопросы, связанные с водородной хрупкостью, нужда ются в дальнейшем изучении. Особый интерес представляет оп ределение мест зарождения трещин, механизма их зарождения, а также особенностей механизма их роста.
8. ЗАКЛЮЧЕНИЕ
Нами изложено небольшое число примеров влияния среды на процессы разрушения и показано, что имеется много неясных и неисследованных вопросов. Между тем трудно переоценить то значение, которое имеет для техники более глубокое изучение рассмотренных явлений; в дальнейших экспериментальных ра ботах необходимо использовать: 1 ) образцы, имеющие простой состав и структуру; 2 ) среды известного и хорошо контролируе мого состава; 3 ) прямые экспериментальные методы, позволяю щие непосредственно трактовать получаемые данные.
ЛИТЕРАТУРА
1. S a i n t - C l a i r e |
D e v i l l e |
Н. |
a. T r o o s t |
L. Compt. |
Rend., 56. |
р. 977; |
|||||||||||||
1861, 57, р. 965. |
|
|
|
|
|
|
|
|
|
|
|
|
|
|
|
|
|
||
2. |
C a i l l e t e t |
L. Compt. Rend., 1863, 58, 327, p. 1037. |
|
|
|
||||||||||||||
3. |
R e y n o l d s |
O. Manchester Lit. Phil. Soc., 1874, |
v. 13, p. |
93. |
|
||||||||||||||
4. R o b e r t s |
— |
A u s t e n W. C. Proc. Roy. Inst., |
1886, v. 11, p. 411 quoted |
||||||||||||||||
in R a s k S., Recent |
Advances |
in |
Stress Corrosion, Roy. Swedish Acad. Eng. |
||||||||||||||||
Sci., Stockholm, |
1961, |
p. 81. |
|
|
|
|
|
|
|
|
|
|
|
|
|
||||
5. |
C o b l e n t s |
W. W. Phys. Rev., 1903, v. 16, p. 389. |
|
|
|
||||||||||||||
6. S c h m i d |
E., B o a s |
W. |
Plasticy of |
Crystals. |
Hughes L., 1950, p. 258. |
||||||||||||||
(Ш м и д Э., Б о а с |
В. Пластичность кристаллов |
в особенности |
металлических, |
||||||||||||||||
ГОНТИ, |
1938). |
|
|
|
|
|
|
|
|
|
|
|
|
|
|
|
|
|
|
7. |
K l e i n h a n n s |
|
К. Z. Phvsik, |
1914, Bd. 15, |
S. 362. |
|
|
|
|||||||||||
8. |
J o f f е А. { И о ф ф е |
A.] |
u. a. Z. Physik, |
1924, |
Bd. 22, S. 286. |
|
|||||||||||||
9. И о ф ф е |
А. Ф. Физика кристаллов. Госиздат, 1929. |
|
|
|
|||||||||||||||
10. E w a l d |
W. |
u. P o l a n y i |
М. Z. Physik, |
1924, |
Bd. 28,S. |
29. |
|
||||||||||||
11. |
E w a l d |
W. |
u. P o l a n y i |
M. Z. Physik, |
1925,Bd. 31, |
S. |
746. |
|
|||||||||||
12. S m e k a l |
A. Naturwiss., 1928, v. 16, p. 743. |
|
|
|
|
|
|||||||||||||
13. S m e k a l |
A. Z. Physik, |
1931, v. 32, |
p. |
187. |
|
|
|
|
|
|
|||||||||
14. |
О r o w a n E. Z. Physik, |
1933, v. 86, |
p. |
195. |
|
|
|
|
|
|
|||||||||
15. |
H u n t i n g t o n |
A. K. J. Inst. Metals, |
1914, v. |
11, p. |
108. |
|
|||||||||||||
16 |
H e y n E. J. Inst. Metals, |
1914, v. 12, |
p. |
3. |
|
|
|
|
|
|
|||||||||
17. D e s c h |
С. H. J. Inst. Metals, 1919, v. 22, |
p. |
247. |
|
|
|
|||||||||||||
18. |
M o o r e |
H. |
a. B e c k i n s a l e |
S. J. Inst. Metals, 1920, v. 23, p . |
225. |
||||||||||||||
19. M o o r e |
H. |
a. o. J. Inst. Metals, 1921, |
v. 25, p. |
35. |
|
|
|
||||||||||||
20. |
C o t t e r i l l |
P. Progr. Mater. Sci., |
1961, |
v. 9, |
p. |
201. |
|
|
|
21.Hydrogen Embrittlement in Metal Finishing, Reinhold, N. Y., 1961.
22.Stress Corrosion Cracking and Embrittlement. Wiley, N. Y., 1956.
23. Physical |
Metallurgy |
of |
Stress |
|
Corrosion |
|
Fracture, |
Interscience, |
||||||||||||
N. Y. |
1959 |
|
|
° |
|
|
|
|
|
|
|
|
|
|
|
|
|
|
|
|
24. |
R о s t о к e r |
W |
a о |
Embrittlement by |
Liquid |
Metals, |
Reinhold, |
N. Y., |
||||||||||||
I960. |
[P о с т о к е р |
У. и'д р . Хрупкость |
под действием |
жидких |
металлов, |
|||||||||||||||
ИЛ, |
19621. |
|
|
|
|
|
|
|
|
|
|
|
|
|
|
|
|
|
|
|
25. С 1 a s s W. Н. а. о. Trans. А Ш Е , |
i961 |
v. 221, р. 769. |
|
v. 5, р. |
697 |
|
||||||||||||||
26. С 1 а г k е F. |
J. Р. a. S a m b е 11R. A. J. |
Phil. Mag |
1960 |
|
||||||||||||||||
27. A n d r a d e |
Е. N. da |
С. a. T s i e n |
L. |
С. Ргос. |
Roy. |
Soc., |
L.. |
1937, |
||||||||||||
A289'zPe n 4e6r C. Fracturing |
of |
Metals |
ASM, |
Cleveland. Ohio, |
1948, p. |
3. |
|
|||||||||||||
29. |
S t o k e s |
R. J. a. o. Phil. Mag., 1959, v. 4, p. 920. |
|
|
|
86, |
|
|
||||||||||||
|
30. |
B e l l R. L. |
a. C a h n |
R. W. J- Inst. Metals, |
1957-1958, v. |
p. 433. |
||||||||||||||
|
31. |
Q i 1 m a n J. J. Trans. AIME, 1954, v -200 p. 62 . |
|
|
|
|
|
|
|
|||||||||||
|
32. W e s t w о о d A. R. C. Phil. Mag., |
1961 |
v. 6 p 195. |
|
|
|
61 |
|
||||||||||||
|
33. |
J o h n s t o n |
T. L. a. o. Phil. Mag., |
1962, |
v. |
7 |
p',q2fi| |
v |
fi, |
n |
|
|||||||||
|
34. C l a r k e |
F. J. P. a. o. Trans. Brit. |
Ceram. Soc |
1962, v. 61, p. |
6 . |
|
||||||||||||||
|
35. W e s t w o o d |
A. R. С. P h i. M ag. |
196“ ' v - 5'P ;,981' |
|
|
|
|
|
|
|||||||||||
|
36. S t o k e s |
R. J. |
Trans. AIME, I960, v. 218, P- 655. |
|
|
|
|
|
|
|
||||||||||
|
38 |
G M i f i f i i |
A |
AdVp h ilPTryans. Roy. Soc’A . . |
1920-1921, v. A221, |
p. |
163. |
|||||||||||||
|
39 |
B i l b v |
R |
A |
a H e w i t t J. Acta Met., 1962, v. |
10, |
p. 587. |
|
|
|
||||||||||
|
40. L o w yj |
R |
Fractu” ? Wiley, N. Y„ |
1959, p. 68 [Л о у |
Д ж о н |
P. В |
сб. |
|||||||||||||
«А том нь^м етани^^р^руш ^ия^М ета^У Р гиздат,^ ^ |
|
^ |
|
5црр1 _ 195б. |
||||||||||||||||
V. 34, |
р. 570. |
|
|
|
|
|
|
|
|
|
|
|
|
|
|
|
|
|
v |
в |
|
|
|
|
|
“ " |
д |
а |
Е |
в' * |
44. |
T i p p e r |
С. F. Metallurgia |
l949, |
v. |
39 р |
133 |
|
дж.Дж. |
||
45. |
G i l m a n |
J. J. F |
a c |
t |
мёталлурРгиздат, |
1963, с. 220]. |
||||
В сб. «Атомный механизм разрушь™» |
|
OQQ |
|
|
||||||
« . R o s c o e |
R |
|
|
J Ргоег. М .1». |
Sci, 1961. v. 9, 133. |
|||||
( K p t » e pr r |
д |
Л £ Л |
|
среди |
> . механические c.efcxe . „e ,,.v |
|||||
лов. Изд-во |
«Металлургия», |
1964]. |
|
|
|
3 р. 971. |
|
S BE rv a n : ? ! I
p.889.
aScEhVwaanrSZTenPbhu r g e gr ’ D. R. Phil. Mag., 1959. v. 4,
ЛЛQO
50. |
H e a d |
A. |
K. PhilMa^ |
p ^ c |
• |
Vphys.PSoc.; L., 1950, v. A63, p. 616. |
||||||||||||
51. V a n d e г |
M e r w e J. H. |
|
|
|
jg i |
|
|
\ \ № . |
|
|
||||||||
2 |
i l m a n |
J. J. J ra^ - A| / % |
e r D. A. J |
|
Inst. Metals, 1955-1956, v. 84, |
|||||||||||||
53. |
G r e e n o u g h G. Ь. а. ку |
|
|
|
|
|
|
|
|
|
|
|||||||
P- 467. |
|
|
|
|
|
|
Г о л . а т е г |
M. J. Inst. Metals, 1957, v. 85, p. 441. |
||||||||||
54. W e i n e r |
L. C. a. G en . ME |
|
1958i v |
212, p. 253. |
|
|
||||||||||||
. W |
i n e r |
|
L. C. Trans. AI- |
’ |
|
|
h Q |
B |
|
J |
Inst. Metals, |
1955—1956, |
||||||
56. D er u y t t er |
A. a. GreenouB |
|
|
|
|
|
|
|
||||||||||
v. 84, p. 337. |
|
|
J. |
|
hi. |
м а |
е . , |
1951, |
v. 42, |
p. 351. |
|
|
||||||
57. |
E s h e l b y |
D. а. о P |
• |
^ |
|
^ |
1954> v |
|
A223i p. 494.*260958 |
|
|
|||||||
58. |
S t r o h |
A- |
N• |
Pr^ anRs°yA iM E, |
|
1958, v. 212, p. 342. |
|
|
||||||||||
59. W e i n e r |
|
L. C. |
l r ®“ s- " |
,959 |
|
v |
30, p. 791; |
1959, v . 30, p . |
|
|||||||||
60. W e i k |
H. J. ApplPhys., |
l;«y, |
|
A plp phys |
1471. |
|||||||||||||
61 |
W e b b |
W. W, |
a. S t e m |
Л. У |
^ |
|
У |
’1962, v . 14, p. 87. |
||||||||||
62. |
В |
11 e 1 1 0 |
|
J. С |
a. C a d o n |
|
|
|
|
1958i v 41j p. i |
6 I. |
|
||||||
64 |
P a r k ™ |
AF ER 3Mechanical |
Properties |
of |
Engineering |
Ceramics. Inter- |
||||||||||||
“ '“ IS ' Й |
|
|
|
|
|
M .U |
1* |
|
8, v. 6, p |
610. |
|
|
|
|
66. |
Л и х т м а н |
|
Вц и., Р е б и н д е р |
П. |
А., |
К а р п е н к о |
Г |
В. |
Влияние |
||||||||||||||||||
поверхностно |
активной |
среды |
на |
|
процессы |
деформации |
металлов. |
|
Изд-во |
|||||||||||||||||||
АН |
СССР |
1954 |
|
|
|
Н е к л ю д о в а |
М. В. }КЭТФ, |
1936, |
т. 6, с. |
584. |
|
|
||||||||||||||||
|
67. |
К л а с с е н |
|
|
|
|||||||||||||||||||||||
|
68. |
S u z u k i |
Т. |
Dislocations |
|
and Mechanical |
|
|
Properties |
of |
Crystals, |
|||||||||||||||||
Wiley, N. Y., 1957, p. 217. |
[ С у з у к и T. В сб. «Дислокации |
и |
механические |
|||||||||||||||||||||||||
свойства кристаллов», ИЛ, 1960, с. 120]. |
|
|
|
|
|
|
|
|
|
|
|
|
|
|
|
|||||||||||||
|
69. |
K r a m e r |
I. R. a. D erne г |
L. J. Trans. AIME, |
|
1961, v. 221, р. |
129. |
|||||||||||||||||||||
|
70. |
К л а с с е н - Н е к л ю д о в а |
М. В. ДТФ , |
1938, |
т. 5, |
с. |
827. |
|
|
|||||||||||||||||||
|
71. |
B r e i d t |
Р. а. о. J. Appl. Phys., 1958, |
v. 29, |
р. |
|
226. |
|
|
|
|
|
|
|||||||||||||||
|
72. |
J о h n s t о n Т. L. а. о. Acta Met., |
1958, v. 6, |
р. 713. |
|
|
|
|
|
|
||||||||||||||||||
|
73. |
S t o k e s |
iR. J. |
a. o. Phil. Mag., 1961, |
v. 6, |
p. |
9. |
|
|
|
|
|
|
|
||||||||||||||
|
74. |
S n e d d o n |
|
L. N. Proc. Roy. Soc., 1946, v. 187, p. 229. |
|
|
|
|
||||||||||||||||||||
|
75. |
S t o k e s |
R. J. Trans. AIME, 1962, v. 224, p. |
|
1227. |
|
|
|
|
|
|
|||||||||||||||||
|
76. |
K o e h l e r |
J. S. Phys. Rev., 1952, v. 86, p. 52. |
|
|
|
|
|
|
|
|
|
|
|||||||||||||||
|
77. |
О r o w a n |
|
E. Dislocations in Metals, AIME, |
N. Y., |
1954, p. |
103. |
|||||||||||||||||||||
|
78. |
J о h n s t о n W. G. a. G i 1m a n J. J. J. Appl. |
|
Phys., |
|
1960, |
v. 31, |
p. 632. |
||||||||||||||||||||
|
79. |
W a s h b u r n |
J. a. o. Phil. Mag., i960, v 5, |
p. |
991. |
|
|
|
|
|
|
|||||||||||||||||
|
80. |
G i 1ш a n |
J. J. J. Appl. Phys., 1959, v. 30, p. 1584. |
|
|
|
|
|
|
|||||||||||||||||||
|
81. |
G u r n e y |
C. Proc. Phys. Soc. L., 1947, v. 59, p. 169. |
|
|
|
|
|
||||||||||||||||||||
|
82. |
P u l l i a m |
G. R. J. Am. Ceram. Soc., 1959, v. 42, p. 477. |
|
|
|
||||||||||||||||||||||
|
83. |
O b r e i m o v |
|
J. W. Proc. Roy. Soc. L., 1930, v. A127, p. 290. |
|
|
||||||||||||||||||||||
|
84. |
G i l m a n |
J. J. J. Appl. Phys., 1960, v. 31, p. |
208. |
|
|
|
|
|
|
|
|||||||||||||||||
|
85. |
S h u t t l e w o r t h |
R. Proc. |
Phys. |
Soc., |
1949, |
v. A62, |
p. |
167. |
|
|
|||||||||||||||||
|
86. |
W a s s e r m a n |
G. Z. Metallk., 1942, |
v. 34, C. |
|
297. |
|
|
|
|
|
|
||||||||||||||||
|
87. |
E d m u n d s |
|
G. Symposium on the Stress Corrosion Cracking of Me |
||||||||||||||||||||||||
tals, |
ASTM— AIME, |
|
Philadelphia, |
1944, p. |
70. |
|
|
|
|
|
|
|
|
|
|
|
|
|
|
|||||||||
|
88. |
D e n h a r d |
E. E., |
T h e s i s |
M. S. Johns Hopkins |
Univ., |
1957. |
|
|
|||||||||||||||||||
|
89. |
E d e l e a n u |
|
C. a. F o r t y |
A. J. Phil. Mag., |
1960, |
v. 5, p. |
1029. |
|
|
||||||||||||||||||
|
90. |
B a k i s h |
|
R. a. R o b e r t s o n W. D. Acta |
Met., 1955, |
v. 3, |
p. 513; 1956, |
|||||||||||||||||||||
v. 4, |
p. |
342. |
|
|
|
|
|
|
|
|
|
|
|
|
|
|
|
|
|
|
|
|
|
|
|
|
|
|
|
91. |
R o b e r t s o n W. |
D. a. T e t e l m a n |
A. S. Strengthening |
Mechanisms |
|||||||||||||||||||||||
in Solids. ASM, |
Cleveland, |
Ohio, |
1962, p. |
217. |
( Р о б е р т с о н |
В. |
Д., |
Т е т е л - |
||||||||||||||||||||
м а н А. Б. «Сб. «Механизмы |
упрочнения |
твердых |
тел». Изд-во |
«Металлур |
||||||||||||||||||||||||
гия», 1965, |
с. 220]. |
|
|
|
|
|
|
|
|
|
|
|
|
|
|
|
|
|
|
|
|
|
|
|||||
|
92. |
P a x t o n |
Н. W. а. о. Physical Metallurgy of Stress Corrosion Fractu |
|||||||||||||||||||||||||
re, Interscence. N. Y., 1959, |
p. |
181. |
|
|
|
|
|
|
|
|
|
|
|
|
|
|
|
|
||||||||||
|
93. |
U h 1i g |
H. H. Physical Metallurgy |
of |
Stress |
Corrosion |
Fracture, |
Inter |
||||||||||||||||||||
science, N. Y., p. 1. |
|
|
|
|
|
|
|
|
|
|
|
|
|
|
|
|
|
|
|
|
|
|
||||||
|
94. T h o m p s o n |
D. H. a. T r a c y A. W. Trans. AIME, |
1949, v. 185, |
p. 100. |
||||||||||||||||||||||||
|
95. |
C o l e m a n |
E. G. a. o. Acta Met., |
1961, v. 9, |
|
p. |
491. |
|
|
|
|
|
||||||||||||||||
|
96. L i d u i a г d E. A. G., Toughness and Brittleness |
in |
Metals, |
Interscience, |
||||||||||||||||||||||||
N Y., 1961, |
p. |
41. |
|
|
|
|
|
|
|
|
|
|
|
|
|
|
|
|
|
|
|
|
|
|
|
|||
1956^ |
*48Г 3 * |
^ |
|
stress |
Corrosion |
Cracking |
and |
Embrittlement, Wiley, |
N. Y., |
|||||||||||||||||||
|
98. |
H i n e s |
J. |
G. Corrosion Sci., 1961, v. |
1, p. |
21. |
|
|
|
|
|
|
|
|
|
|
||||||||||||
|
99. |
G i 1m a n |
J. J. Trans. AIME, 1958, |
v. |
212, |
p. |
783. |
|
|
|
|
|
|
|
||||||||||||||
|
100 |
F o r t y |
A. J. Physical Metallurgy |
of |
Stress |
Corrosion |
Fracture, |
Inter- |
||||||||||||||||||||
science, |
N. Y., 1959, p. 99. |
|
|
|
|
|
|
|
|
|
|
|
|
|
|
|
|
|
|
|
||||||||
|
101. |
F u j i t a |
F. E. Acta Met., 1958, v. 6, |
p. 543. |
|
|
|
|
|
|
|
|
|
|
|
|||||||||||||
|
102. G r a f |
L. u. B u d k e |
J. Z. Metallk., |
1955, |
Bd. 46, |
S |
|
378. |
|
|
|
|||||||||||||||||
|
103. |
L o m e r W |
|
M. Phil. Mag., 1951, v. 42, p. 1327 |
|
|
|
|
|
|
|
|
||||||||||||||||
|
104. |
C o t t r e l l |
|
A. H. Phil. Mag., 1952, v. 43, p. |
645. |
|
|
|
|
|
|
|
||||||||||||||||
|
105. |
G a r a f a l o |
|
F. Acta |
Met., |
1960, v. 8, |
p. |
504. |
|
|
|
|
|
|
|
|
|
|||||||||||
|
106. |
D ix |
E. Trans. AIME, |
1940, v. 137, p. |
11. |
|
|
|
|
|
|
|
|
|
|
|
|
|||||||||||
|
107. |
M e a r s |
|
R. a. o. Symposium on the Stress Corrosion Cracking of Me- |
||||||||||||||||||||||||
tals, ASTM—AIME, Philadelphia, |
1944. |
|
|
|
|
|
|
|
|
|
|
|
|
|
|
|
||||||||||||
|
108. |
U h l i g |
H. |
|
H. |
Relation |
of |
Properties |
to |
Microstructure, |
ASM, |
Cleve- |
||||||||||||||||
land, 1954, |
p. |
199. |
|
|
|
|
|
|
|
|
|
|
|
|
|
|
|
|
|
|
|
|
|
|
|
396
|
ии. |
|
|
|
|
|
|
|
|
|
|
|
|
|
|
|
|
|
|
|
|
|
|
|
|
|
111. |
P e t c h |
N. J. |
|
a. S t a b l e s |
P. Nature, |
|
1952, v. 169, |
p. |
842. |
|
|
|||||||||||||
|
112. |
P e t c h |
N. J. Phil. Mag., 1956, |
v. |
1, p. |
331. |
|
|
|
|
|
|
|
||||||||||||
|
113. |
S t r o h |
|
|
|
|
|
|
D ~ |
, |
w. ж, |
|
|
|
|
|
|
|
|
|
|||||
|
A. N. Proc. Rov. Snr |
т a |
las. |
|
|
|
p. |
548. |
|
|
|
||||||||||||||
|
j j л |
D , |
ь |
м |
т |
|
т |
т |
Kc°y-,s oc., |
La., 1955, v. A232, |
|
|
|
||||||||||||
|
!.= ' |
|
|
N„ J; |
|
r |
' r |
l ? . l |
nst-. 1953. V. 174, p. 25 |
Corrosion |
Cracking |
||||||||||||||
|
|
|
|
|
|
|
|
|
|
|
|
|
|
|
|
|
|
Stress |
|||||||
|
|
|
|
|
|
|
|
|
|
|
|
|
|
|
|
|
Interscience, |
N. Y., 1959, p. 97. |
|||||||
|
|
|
|
|
|
|
|
|
Relation of Properties to Microstructure, ASM. Cle- |
||||||||||||||||
veland, Ohio, 1954, p. 131. |
|
|
|
|
|
|
|
|
|
|
|
|
|
|
|
|
|||||||||
|
118. |
B r o o m |
T., |
|
a. B i g g s W. D. Phil. Mag., |
1954, v. 45, |
p. |
246. |
|
|
|||||||||||||||
|
119. |
G i l m a n |
J. J. a. o. J. Appl. Phys., 1958, v. 29, p. 601. |
|
|
|
|
||||||||||||||||||
|
120. |
G i l m a n |
J. J. Plasticity, Pergamon, N. Y., 1960, p. 92. |
|
|
|
|||||||||||||||||||
|
121. |
G r e e n w o o d |
J. N. J. Inst. Metals, 1953, v. 81, p. |
177. |
|
|
|
||||||||||||||||||
|
122. |
T i n e r |
N. A. Trans. AIME, 1961, v. 221, |
p. 261. |
|
|
|
|
|
|
|||||||||||||||
|
123. W e r t |
C. |
a. Z e n e r C. Phys. Rev., |
1949, v. 76, p. 1169. |
|
|
|
||||||||||||||||||
|
124. |
R o b e r t s o n |
W. D. Trans. AIME, |
1951, v. 191, p. 1190. |
|
|
|
||||||||||||||||||
|
125. Р о ж а н с к и й В . |
H., П е р ц о в |
H |
|
В., |
Щ у к и н |
E. |
Д., |
Р е б и н - |
||||||||||||||||
Aep П. А. ДАН СССР, |
1957, т. 116, с. 769-771. |
Б р ю х а н о в а |
Л. С. ДАН |
||||||||||||||||||||||
_ |
126. |
Л и х т м а н |
|
В. И., |
К о ч а н о в а |
Л. А., |
|||||||||||||||||||
СССР, 1958, т. 120, с. 757—760. |
|
|
|
|
|
|
|
|
|
|
|
|
|
|
|
||||||||||
|
127. |
Л и х т м а н |
|
|
В. И., |
Щ у к и н |
Е. Д. Успехи |
физических |
наук, |
1958, |
|||||||||||||||
т- 66, с. 213. |
|
|
|
|
|
|
|
|
|
|
|
|
|
|
|
|
|
|
|
|
|
|
|
||
|
!on' |
M o r g a n |
W, A., Thesis Ph. D. Univ. Cambridge, 1954, v. 24, p. 72. |
||||||||||||||||||||||
|
129. |
R h i n e s |
F. N. a. o. Trans. ASM, |
Quart., 1962, v. 55, p. |
22. |
|
|
||||||||||||||||||
|
30. |
Г о р ю н о в |
|
У. В и др.. ДАН |
СССР, |
|
1959, 127, с. 1070—1073. |
|
|||||||||||||||||
|
131. Щ у к и н |
Е. Д., |
П е р ц о в |
Н. В., |
Г о р ю н о в |
У. В. Кристаллография, |
|||||||||||||||||||
т- 4, 1959, с. 887. |
|
|
|
|
|
|
|
|
|
|
|
|
|
|
|
|
|
|
|
|
|
||||
|
,132- |
Р е б и н д е р |
|
П. А. и др. ДАН СССР, |
1956, т. III. с. |
1284. |
т. |
124, |
|||||||||||||||||
|
133. Щ у к и н |
Е. Д., Л и х т м а н |
В. |
И. |
|
ДАН |
СССР, |
1959, |
|||||||||||||||||
е. 307—310. |
|
|
|
|
|
|
|
|
|
|
|
|
|
|
|
|
|
|
|
|
|
|
|
||
|
134. |
S t r o h |
А. N. Phil. Mag., |
1958 |
v |
3, |
р. |
598. |
|
|
|
|
|
|
|
||||||||||
V |
2 135 |
T2ierS |
|
|
A' a’ N e i g h b o u r s |
J- |
R- |
Bul1- |
Am- |
|
РЬУ5- |
Soc- |
1957- |
||||||||||||
|
136. |
Р о ж а |
н е к и й |
В. H. Физика |
твердого |
тела, |
1960, т. 2, |
с. 978. |
|
||||||||||||||||
|
137. |
П е р ц о в |
Н. В. и др. ДАН СССР, 1959, т. 128, с. 1003. |
504. |
|
||||||||||||||||||||
|
138. |
N i c h o l s |
Н. a. R o s t o k e r W . Acta |
|
Met., 1961, v. 9, p. |
|
|||||||||||||||||||
|
139. |
C o t t r e l l |
A. H. Trans. AIME, |
1958, v. 212, p. 192. |
|
|
|
|
|||||||||||||||||
|
140. |
M o t t |
N. F. Phil. Mag., 1952- |
v |
43, |
p. |
1151. |
|
|
|
|
|
|
|
|||||||||||
|
141. |
S t r o h |
A. N. Proc. Roy. Soc., |
L„ |
1953, v. A128, p. 391. |
|
|
|
|||||||||||||||||
|
142. Ф р и д е л ь |
|
Дж. Дислокации. ИЛ, |
1966. |
|
|
|
|
|
|
|
|
|||||||||||||
|
143. Р о ж а |
н е к и й |
В. Н. ДАН СССР, |
1958, т. 123, с. 648—651. |
|
|
|||||||||||||||||||
|
144. |
О го w a n |
Е. Nature, L., |
1944, v. |
154, |
р. 341. |
|
|
|
|
|
|
|||||||||||||
|
145. Р о ж а и с к и й В. Н., Р е б и н д е р |
П. А. ДАН СССР, 1953, 91, с. 129. |
|||||||||||||||||||||||
|
146. |
E l l i o t |
Н. A. Proc. Phys. Soc. L„ |
1947, v. B59, p. 208. |
|
|
|
||||||||||||||||||
|
147. |
B a i l e y |
A. 1. J. Appl. Phys., 1961, |
v. 32, p. |
1407. |
|
|
|
|
|
|||||||||||||||
|
148. |
М е ц и к |
M. С. Физика твердого тела, 1959, т. 1, с. 1084. |
Гостехиз- |
|||||||||||||||||||||
|
149. |
К у з н е ц о в |
В. Д. Поверхностная |
|
энергия |
твердых тел. |
|||||||||||||||||||
дат, 1954. |
|
|
|
|
|
|
|
|
|
|
|
|
|
|
|
|
|
|
|
|
|
|
|
||
|
150. |
Д е р я г и н |
|
|
Б. В., |
М е ц и к М. С. Физика твердого |
тела, |
1959, |
т. 1, |
с.1521.
151. |
R o b e r t s o n |
W. |
D., a. U h l i g |
Н. Н. J. Appl. Phys., 1948, |
v. 19, |
р. 814. |
R o b e r t s o n |
W. |
D. a. U h l i g |
H. H. Trans. Electrochem. Soc., |
1949, |
152. |
|||||
v. 96, p. |
27. |
|
|
|
|