
книги / Резание материалов
..pdf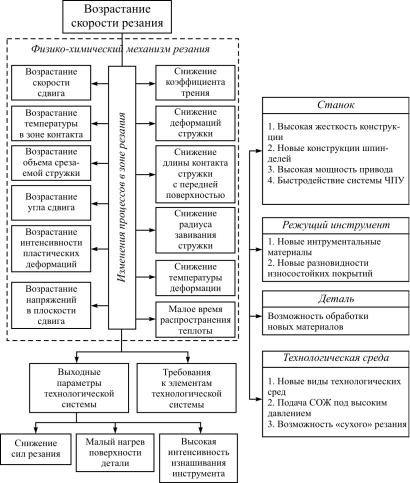
Рис. 258. Особенности изменения условий резания
ифизических процессов при высокоскоростном резании
Кнедостаткам применения высокоскоростного резания можно отнести возможное появление вибраций из-за неуравновешенности вращающихся масс деталей или инструмента. Для устранения этих недостатков высокоскоростного резания при внедрении
471
|
|
|
|
|
|
|
Таблица 3 7 |
|
Достоинства, условия и области использования HSC |
||||||||
|
|
|
|
|||||
Достоинства |
Условия применения |
|
Области использования |
|||||
Высокая |
произво- |
Обработка |
деталей из |
Изделия |
аэрокосмической |
|||
дительность |
сталей, чугунов, легких |
промышленности, производ- |
||||||
|
|
сплавов |
|
|
|
ство литейных форм и пресс- |
||
|
|
|
|
|
|
форм для объемной обработки |
||
Высокие качество и |
Прецизионнаяобработка |
Оптическая |
промышленность, |
|||||
точность |
обрабо- |
|
|
|
|
приборостроение, |
турбино- |
|
танной поверхности |
|
|
|
|
строение |
|
|
|
Малые силырезания |
Обработка тонкостенных |
Авиационная, |
космическая, |
|||||
|
|
(нежестких) деталей |
|
автомобильная |
промышлен- |
|||
|
|
|
|
|
|
ность, бытовое машинострое- |
||
|
|
|
|
|
|
ние (производство стиральных |
||
|
|
|
|
|
|
машин, пылесосов и т.д.) |
||
Высокие |
частоты |
Обработка |
труднооб- |
Приборостроение |
и оптиче- |
|||
возникающих в зоне |
рабатываемых |
мате- |
ская промышленность |
|||||
резания колебаний |
риалов без вибраций |
|
|
|
|
|||
Практически пол- |
Низкие температуры |
в |
Обработка деталей из магние- |
|||||
ный отвод |
теплоты |
зоне резания; отсутствие |
вых сплавов, прецизионное |
|||||
в стружку |
|
тепловыхдеформаций |
|
приборостроение |
|
в производство разработаны более жесткие станки, приспособления и инструменты и предусмотрена балансировка державок вращающегося инструмента.
7.3. Обработка резанием без применения СОЖ
Смазочно-охлаждающие жидкости (СОЖ) в последние годы все чаще рассматриваются как нежелательный фактор в производстве. Это обусловлено экономическими и экологическими причинами, в том числе более жесткими международными законами об охране окружающей среды.
Согласно имеющимся данным в крупносерийном производстве (автомобильная промышленность) на долю действий, связанных с применением СОЖ (доставка, использование, регенерация и т.д.), приходится от 7,5 до 17 % общих производственных затрат, тогда как расходы на режущий инструмент составляют только 4 %. Весьма значительны затраты на последующую утилизацию и регенера-
472

Известно, что резание всухую приводит к увеличению температуры в зоне резания и к ускоренному износу инструментов. При этом увеличиваются термические напряжения в поверхностном слое заготовки, возможна деформация деталей, изменение структуры и другие отрицательные последствия. Эти воздействия можно уменьшить следующим образом (рис. 259):
выбирать технологию обработки, не требующую применения СОЖ или с малым расходом – распыл в виде тумана;
изменять конструкцию и геометрию инструмента;
использовать теплозащитные и износостойкие покрытия;
подбирать марки инструментальных материалов с повышенной теплостойкостью и теплопроводностью; использовать твердые, газообразные вещества.
7.3.Новые принципы резания
вусловиях гибкого производства
На современных многоцелевых обрабатывающих центрах сегодня применяются новые методы резания и новые конструкции инструмента.
Современные многоцелевые обрабатывающие центры (рис. 260) представляют собой гибкие автоматизированные модули. Эти модули содержат в своем составе различные процессы резания. Например, на японских центрах, имеющих два шпинделя на одной оси (рис. 261), имеется возможность обработки детали с двух торцов методами точения, фрезерования, сверления, шлифования, зубонарезания последовательно с одной установки детали. Всем процессом резания управляет система ЧПУ. Поэтому станок может в течение смены обрабатывать деталь по всем поверхностям без вмешательства рабочего.
Подключение автоматизированных устройств или роботов к подаче заготовок и смене инструмента создает реальные условия безлюдной технологии. Такой центр может самостоятельно работать непрерывно в течение нескольких суток без перенастройки. Однако здесь необходима постоянная диагностика процесса резания по комплексу показателей – мощности, температу-
474

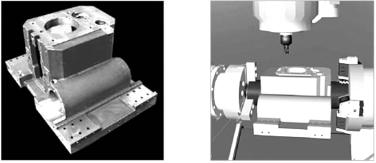
и сложные детали малыми партиями. Стало трудно прогнозировать загрузку производства, обострилась конкуренция по ценам. Все это обусловило следующие требования к оборудованию:
повышение производительности не на 20…30 % за счет увеличения скорости выполнения операций, а в 5…10 раз за счет кардинального изменения технологий и методов обработки;
переходот специального оборудования куниверсальному. Особо стоит отметить многофункциональные машины серии
Integrex, которые объединяют в себе возможности ОЦ и ТЦ и позволяют делать детали самой сложной конфигурации из цельного куска материала без переустановки (рис. 262). Integrex выполняет операции точения, растачивания, фрезерования (до пяти осей), сверления, закалки, шлифовки, зубонарезания и т.д. Заготовка загружается на Integrex один раз, снимается полностью обработанная деталь. При этом возможна обработка из цельного блока материала, следовательно, исключается оснастка. Эти станки привели к революции в механообработке, так как они позволяют эффективно изготавливать партию любого размера, сократить до минимума сроки от поступления заказа до изготовления детали. Они обеспечили переход от серийного производства к производству под заказ.
Рис. 262. Деталь, обрабатываемая |
Рис. 263. Обработка детали |
на станках серии Integrex |
на ОЦ серии Integrex |
Станки выпускаются как с горизонтальной (рис. 263), так и с вертикальной осью вращения заготовки. Широкий размерный
476

ются на японских заводах. Заводы Mazak представляют собой киберпроизводства. Цеха оборудованы ГПС, работающими в безлюдном режиме.
Рис. 264. Схема расположения |
Рис. 265. Схема расположения |
оборудования в гибкой |
оборудования в гибкой |
производственной системе |
производственной ячейке |
Конструкторские бюро (КБ), маркетинг, сбыт, отдел заказов, менеджмент – все эти службы завязаны в единую информационную среду. По мере того как изделие проектируется в КБ и отдельные его узлы уже готовы, начинается разработка управляющих программ, заказывается инструмент, заготовки и начинается обработка. Планирование процесса производства, анализ загрузки оборудования осуществляется с помощью компьютеров. Все это позволяет выпускать станки за 1–2 месяца с момента поступления заказа. При этом обеспечиваются конкурентоспособные цены. Цены на оборудование Mazak, конечно, не такие, как на оборудование более низкого качества, производимое в странах третьего мира, но они весьма приемлемы и не выше цен на качественное оборудование, поставляемоенароссийскийрынокевропейскимипроизводителями.
7.5. Электрофизические и физико-химические методы обработки
Эти способы обработки основаны на непосредственном использовании для технологических целей электрической, химической, звуковой, световой и других видов энергии. Они обладают рядом преимуществпо сравнению собработкой заготовокрезанием:
478
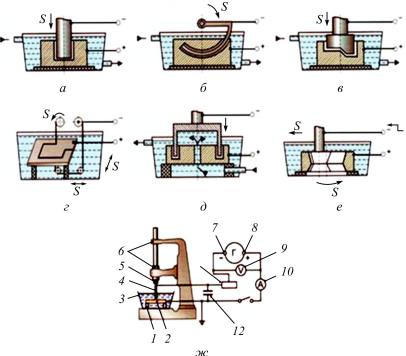
Недостатками электроискрового способа обработки являются относительно невысокая производительность труда и недостаточная точность формы и размеров обработанной детали.
Рис. 266. Схемы электроискровой обработки: а – прошивание отверстия; б – прошивание отверстия с криволинейной осью; в – обработка фасонной полости штампа; г – вырезание заготовки из листа; д – прошивание отверстия по способу трепанации; е – шлифование внутренней поверхности фильеры; ж – схема станка: 1 – стол; 2 – заготовка; 3 – ванна с жидкостью; 4 – электрод-инструмент; 5 – ползун; 6 – направляющие; 7, 8 – клеммы регулятора импульсов; 9 – вольтметр; 10 – амперметр;
11 – резистор; 12 – конденсатор
Электроимпульсная обработка (рис. 267) – разновидность электроэрозионной обработки. Процесс обработки проводят в ванне с диэлектрической жидкостью. Между инструментоманодом и заготовкой (катодом) происходят импульсные дуговые
480