
книги / Резание материалов
..pdf5.Назовите методы улучшения обрабатываемости.
6.Назовите особенности обрабатываемости резанием различных материалов – сталей, чугунов, цветных сплавов, жаропрочных и титановых сплавов, композиционных материалов.
7.Каков порядок выбора и каково назначение оптимальных геометрических параметров режущего инструмента?
8.Каков порядок назначения оптимальных режимов резания различными методами?
9.В чем особенности табличного метода?
10.В чем особенности аналитического расчета оптимальных режимов резания?
462
ва и применению экологически опасных СОТС и внедрению обработки резанием всухую без СОТС.
5.Возрастание мощности компьютеров систем ЧПУ на металлорежущих станках, благодаря чему можно эффективно решать задачи адаптивного управления и мониторинга работы систем станка в режиме текущего времени работы. По мере увеличения износа режущих инструментов проводится корректировка режимов резания без съема инструментов. Возросла и способность компьютеров к самообучению при обработке резанием.
6.Совершенствование проектирования и производства новых инструментальных материалов и конструкций режущих инструментов на основе создания тонких мелкозернистых структур
иприменение преимущественного сборного инструмента с новыми видами износостойких и теплостойких покрытий создает.
7.Применение нового метода резания – твердого точения, твердого фрезерования закаленных и твердых сталей и сплавов вместо обработки шлифованием. Такая возможность появилась в связи сразработкой сменных режущих пластин из сверхтвердых материалов и керамики вместо твердосплавных пластин той же формы. При этом обеспечивается высокая производительность, качество и точностьобработки, возможностьсбораипереработкистружки.
8.Компьютерное моделирование процесса резания благода-
ря разработке новых инженерных программ расчета «Деформ», «Ансис», «Третья волна». Это позволяет довольно точно прогнозировать параметры производительности и качества обработки, не прибегая к дорогостоящим экспериментальным исследованиям; изучать процессы образования стружки, движения ее по передней поверхности, стружкозавивания и ломания на скоростях резания до 1800 м/мин. Появилась возможность рассчитывать силы и температуру резания, контакные нагрузки и распределение напряжений в зоне сдвига, на контактных поверхностях инструмента и заготовки при точении, фрезеровании, сверлении, строгании и протягивании.
9.Применение комбинированых методов резания за счет введения в зону резания дополнительной энергии – тепловой,
464

завод», ОАО «Инкар», ОАО «Редуктор» и др. Стоимость новых станков достаточно велика – достигает 2–3 млн евро за станок. Значительно (в десятки раз) выросла и стоимость режущих сборных инструментов.
Непредвиденный выход из строя этого оборудования и инструмента по различным причинам приводит к большим издержкам производства на машиностроительных заводах. Поэтому резко вырос уровень активности исследований в области контроля и управления процессами механической обработки и инструмента в нашей стране и за рубежом. Одна из этих систем – система АСМ.
ACM – это система адаптивного регулирования и мониторинга. Она включает следующие направления:
1.Автоматическое изменение подачи в реальном времени.
2.Защита инструмента, детали и станка от перегрузки и по-
ломки.
3.Контроль износа инструмента.
4.Увеличение времени жизни инструмента.
5.Обнаружение поломки инструмента.
6.Статистические отчеты о работе станка, деталях и инструментах.
7.Графическое отображение процесса резания.
Основная деятельность разработчиков систем управления направлена на контроль износа инструмента или интенсивности его износа в любой текущий момент времени процесса обработки резанием. Способ механической обработки, обеспечивающий оптимизацию процесса резания за счет условий обработки, режимов резания, в зависимости от конкретных условий резания в каждой точке заготовки называют адаптивным резанием.
Адаптивные системы перерабатывают информацию о принятом для регулирования критерии, например, силе или температуре резания и обепечивают нестационарное резание. Они позволяют значительно повышать точность и качество обработанной поверхности. Основной фактор, влияющий на эти показатели обработки, – колебание силы резания, вызывающее изменение упругих перемещений в технологической системе. Для каждой технологической
466
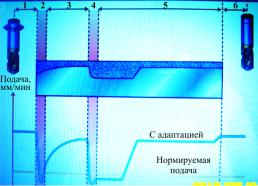
3.Постоянное регулирование подачи в соответствии с нагрузкой на шпинделе.
4.Снижениеподачиприперегрузкедля защитыинструмента.
5.Постоянное регулирование подачи в соответствии с нагрузкой на шпинделе.
6.Увеличение подачи во время движения в воздухе.
ACM непрерывно сравнивает нагрузку на шпинделе с предварительно записанной максимальной величиной для данной операции. Контролируются два уровня: уровень предупреждения и уровень аварии. ACM автоматически снижает подачу до безопасного уровня, предотвращающего поломку инструмента. Автоматическое изменение подачи в реальном времени до ее оптимального уровня для каждого отдельного инструмента и материала обеспечивает до 30 % экономии времени при черновой обработке.
При фрезеровании турбинных лопаток с применением системы адаптивного управления экономия времени составила 31,2 %; при фрезеровании профиля штампов – 24,7 %. Адаптивные системы управления могут использоваться для стабилизации величины шероховатости или наклепа. Управляя скоростью резания
иподачей, можно обеспечить постоянную шероховатость поверхности, несмотря на изменение припуска, конфигурации детали. Изменяя силовой и температурный режимы, можно управлять показателями наклепа поверхностного слоя и величиной остаточных напряжений.
Известно, что износ инструмента вызывает рост температуры, силы резания, увеличение шума и вибраций в зоне резания. Установленная взаимосвязь этих параметров с износом инструмента позволила разработать ряд устройств адаптивного слежения и управления режимами обработки. Например, увеличение силы резания по мере износа инструмента вызывает увеличение мощности резания, что отслеживается системой ЧПУ. Система ЧПУ выдает команду на снижение режимов резания – скорости
иподачи на определенную величину. При увеличении силы резания сверх допустимого значения подается мгновенная команда на остановку процесса резания и смену инструмента. Аналогичным
468
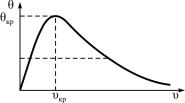

На рис. 257 представлены уровни скоростей резания при обработке различных материалов.
Рис. 257. Уровни скоростей резания при обработке различных материалов: – зона традиционных скоростей;
– переходная зона;
– зона сверхвысоких скоростей
Впроцессе исследования высокоскоростного резания установлены новые физические явления в зоне резания. Эти явления потребовали изменить все составляющие системы резания
(рис. 258).
Высокоскоростное резание имеет ряд существенных преимуществ перед традиционным резанием. В табл. 37 приведены основные преимущества метода высокоскоростного резания.
Всвязи с резким возрастанием скоростей резания реальная производительность увеличивается в 1,5–4 раза. Сегодня применяются станки, обеспечивающие съем металла до 4000 см3/мин или 25…30 кг/мин. Сверхскоростное резание позволяет повысить съем металла до 100 000 см3/мин и более.
470