
книги / Резание материалов
..pdf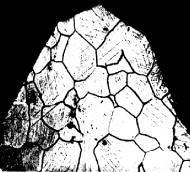
Анализ этих графиков показал, что применение упрочняющих методов обработки – обдувки песком и дробеструйной обработки – формируют в поверхностном слое шестерен благоприятные сжимающие напряжения на большой глубине слоя, что обеспечивает повышение сопротивление усталости и долговечности работы деталей.
5.2.4.Микроструктура поверхностного слоя деталей
Впроцессе резания под воздействием силы и температуры резания, влияния пластической деформации микроструктура поверхностного слоя может существенно измениться. Это может
привести к нежелательным дефектам в поверхностном слое и снижению сопротивления усталости и долговечности работы деталей машин. Микроструктура поверхностного слоя оценивается: размером зерна; плотностью и распределением дислокаций; концентрацией вакансий; размером блоков; углом разориентации блоков; размером областей когерентного рассеяния; среднеквадратическим смещением атомов, вызванным статическими искажениями решетки; среднеквадратическим смещением атомов,
вызванным их тепловыми ко- |
|
|
лебаниями. |
Микроструктура |
|
поверхностного слоя исследу- |
|
|
ется с помощью микроскопов |
|
|
на специально подготовлен- |
|
|
ных шлифах после травления |
|
|
поверхности с увеличением не |
|
|
менее 100 раз. На рис. 188 |
|
|
представлена |
фотография |
|
микрошлифа образца, выре- |
|
|
занного из диска турбины по- |
|
|
сле обработки методом протя- |
Рис. 188. Микроструктура шлифа |
|
гивания на |
повышенной до |
образца из диска турбины из спла- |
14 м/мин скорости резания. |
ва ЭП742-ПД после протягивания |
|
На шлифе можно ясно разли- |
на скорости резания 14 м/мин |
|
чить вид и направление линий |
(выступ «елочного» замка) ×100 |
341
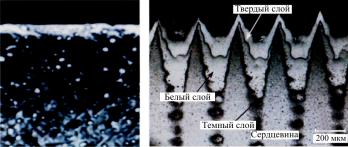
скольжения в поверхностном слое елочного профиля диска турбины из жаропрочного сплава на никелевой основе ЭП742-ПД. Сравнивая микроструктуру шлифов образцов деталей, обработанных при различных условиях резания, можно определить закономерности формирования микроструктуры и выбрать наиболее рациональные условия резания.
Анализ микроструктуры поверхностного слоя деталей из закаленных сталей после обработки шлифованием позволяет выявить наличие так называемого «белого слоя» на поверхности деталей (рис. 189). Белый слой является дефектом поверхности и представляет собой неотпущенный мартенсит и остаточный аустенит. Этот слой обладает весьма высокой твердостью и неблагоприятными растягивающими напряжениями.
Рис. 189. Микроструктура поверхностного слоя закаленной стали после обработки шлифованием с наличием на поверхности «белого слоя»
В качестве меры воздействия для ликвидации данного дефекта применяют дополнительный термический отпуск для снятия напряжений после механической обработки.
5.3. Зависимость параметров качества поверхностного слоя от условий обработки
5.3.1.Влияние условий обработки на шероховатость поверхности. Четвертый закон резания
Влияние способа обработки резанием на шероховатость.
Шероховатость обработанной резанием поверхности в первую очередь определяется видом, методом и способом обработки.
342
Существуют черновые обдирочные грубые методы резания, предназначенные для снятия предварительно большого слоя металла. В то же время имеются методы чистовой окончательной обработки резанием, обеспечивающие получение высокой точности и весьма низкой шероховатости особо ответственных деталей аэрокосмической техники и приборостроения. В табл. 21 приведены данные экспериментальных исследований влияния способов обработки резанием на формирование шероховатости обработанной поверхности от обдирки до сверхтонкой доводки.
Таблица 2 1
Влияние способа обработки на шероховатость обработанной поверхности
Cпособ обработки |
Ra, мкм |
Rz, мкм |
Литье, ковка, штамповка |
ГОСТ 2789–83 |
320 |
Обдирка |
|
160 |
Черновое точение, фрезерование |
|
80 |
Получистовое точение, фрезерование, |
|
|
сверление |
|
30 |
Чистовоеточение, фрезерование, сверление |
2,5; 2,0; 1,6 |
|
Протягивание, твердое точение, зенкеро- |
1,25; 1,00; 0,80 |
|
вание, предварительное шлифование |
|
|
Чистовое шлифование, развертывание, |
0,63; 0,50; 0,40 |
|
хонингование |
|
|
Притирка, доводка, полировка |
0,32; 0,25; 0,20 |
|
Суперфиниш, доводка |
0,160; 0,125; 0,100 |
|
Тонкая доводка пастами |
0,080; 0,063; 0,050 |
|
Сверхтонкая доводка пастами |
0,040; 0,032; 0,025 |
|
Влияние скорости резания на шероховатость. Известно,
что при работе на низких скоростях резания (первая зона скоростей), при которых нарост не образуется, получается (образуется) довольно хорошая чистота поверхности, т.е. меньшая шероховатость обработанной поверхности (рис. 190).
При повышении скорости резания (II зона) до V = 20...30 м/мин создаются условия для развитого и устойчивого нароста, который, выступая впереди лезвия и ниже линии среза, ухудшает шероховатость поверхности. Дальнейшее увеличение скорости резания
343
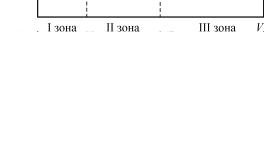
(III зона) приводит к уменьшению наростообразования и высоты неровностей обработанной поверхности. За пределами наростообразования высотанеровностей принимает наименьшее значение.
Рис. 190. Влияние скорости резания на усадку стружки и шероховатость поверхности
Вместе с тем экспериментальные данные многих исследователей показывают, что кривые Rz = f(V), выражающие зависимость высоты неровностей от скорости резания при обработке различных материалов инструментами, оснащенными различными марками твердого сплава, во многих случаях имеют характерные точки минимума. Например, при протягивании различных материалов есть две зоны скоростей резания (рис. 191): зона неблагоприятных скоростей от 0,5 до 12 м/мин и зона благоприятных скоростей резания от 25 м/мин и выше.
Характерным является то, что точки минимума шероховатости совпадают с минимальной интенсивностью износа инструмента. Это показывает, что между интенсивностью износа инструмента, трением и шероховатостью существует тесная взаимосвязь.
Дальнейшее увеличение скорости резания, по данным многих исследователей, не оказывает существенного влияния на шероховатость. В связи с этим введено понятие «граничной» скорости резания Vгран и понятие скорости зеркальной Vзерк, после которой поверхность приобретает зеркальный блеск.
344
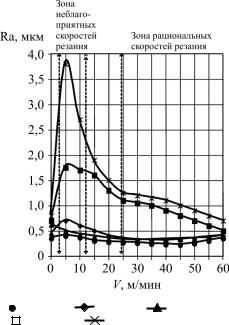
|
|
|
|
ВЖЛ-14 |
|
ВТ3-1 |
ЭИ787-ВД |
|
|
|
|
|
|
||||
|
|
|
|
|
ЭП517Ш |
|
ЭП517Ш (0,1 мм/зуб) |
|
|
|
|
|
|
Рис. 191. Влияние скорости резания V на шероховатость протянутой поверхности Ra различных сталей и сплавов с подачей 0,02 и 0,1 мм/зуб
Установлено, что скорости Vгран и Vзерк совпадают с оптимальными скоростями Vo как по интенсивности износа, так и по
шероховатости. Наименьшая шероховатость обнаружена при существующем на предприятии ОДК-ПМ процессе протягивания протяжками из Р18 на весьма низкой скорости резания
0,5…1,5 м/мин.
При скорости 6…8 м/мин наблюдалось интенсивное наростообразование и шероховатость поверхности ухудшилась. При дальнейшем увеличении скорости резания до 25…30 м/мин высота микронеровностей снизилась до требуемой величины Ra = = 0,63…1,25 мкм. В настоящее время эти высокие скорости резания внедрены впервые в мировой практике на предприятии ОДК-ПМ (Пермь) при протягивании замков лопаток компрессоров современных газотурбинных двигателей.
345
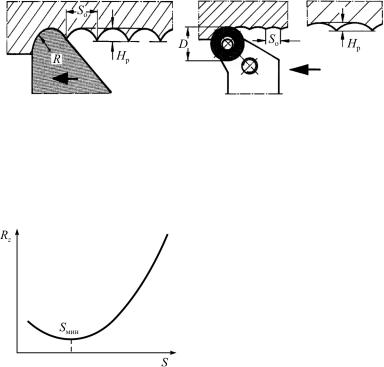
Влияние подачи на шероховатость обработанной поверх-
ности. Подача является важным элементом режима резания, влияющим на производительность процесса обработки. На характер зависимости Rz = f(S) будет влиять сумма факторов. При чистовой обработке повышение подачи ограничивается требуемой низкой шероховатостью обработанной поверхности. Чаще всего подача влияет на высоту микронеровностей как фактор геометрии остаточного сечения среза режущим инструментом (рис. 192).
Рис. 192. Влияние радиуса при вершине резца R(D) и подачи So на высоту микронеровностей Hp
Известно, что с увеличением подачи S при радиусе R, не равном нулю, растет и высота микронеровностей согласно зависимости
Нр = S2/8R.
Однако при уменьшении подачи S уменьшается и толщина среза. В результате радиус округления режущей кромки оказывается соизмеримым с толщиной среза. В этом случае при малых подачах процесс стружкообразования становится неустойчивым, сила трения на задней поверхности возрастает и высота микронеровностей Rz увеличивается (рис. 193).
С повышением подачи S при сохранении постоянства оптимальной температуры То усадка стружки снижается, также сни-
346
жается величина оптимального поверхностного износа hо.п.о и скорость размерного износа Vи.
Понижение (уменьшение) величин hо.п.о и Vи при увеличении подачи может уменьшить высоту микронеровностей до минимальной величины Sмин. При дальнейшем увеличении подачи превалирует геометрический фактор остаточного сечения среза
ивысота микронеровностей резко увеличивается согласно зависимости Нр = S2/8R.
Влияние глубины резания на шероховатость. Глубина ре-
зания как геометрический фактор не может изменить профиль
ивысоту неровностей обработанной поверхности. Глубина резания влияет на высоту неровностей при изменении температуры резания, условий наростообразования, деформации срезаемого слоя и т.д. Но так как глубина резания слабо влияет на температуру резания, усадку стружки и геометрические параметры нароста, то высота неровностей изменяется незначительно. Указанное заключение справедливо при работе резцами с углом при
вершине > 90°.
При работе же резцом с < 90° изменение глубины может существенно влиять на высоту неровностей Нр, что связано с изменением отношения ширины срезаемого слоя к его толщине.
Как правило, глубина резания, оптимальная по шероховатости, оптимальна и по интенсивности износа инструмента. Здесь можно вывести четвертый закон резания: снижение шероховатости обработанной поверхности при неизменном сечении среза можно достичь путем снижения подачи и пропорционального увеличения глубины резания.
Влияние геометрии режущего инструмента на шерохо-
ватость. На образование регулярного профиля микронеровностей влияет геометрия режущего инструмента, в частности главный и вспомогательный угол в плане, радиус при вершине, передний и задний углы, угол наклона режущей кромки.
Исходя из геометрических соотношений расчетная высота неровностей для резца с нулевым радиусом закругления будет
347

Hp Rzp S sin sin 1 . sin( 1 )
Для резца с радиусом закругления R (при S R) используются эмпирические зависимости Нр = S2/8R.
Таким образом, с увеличением углов в плане и 1, уменьшением радиуса при вершине и увеличением подачи высота микронеровностей значительно возрастает, и наоборот. Эту закономерность сегодня используют, применяя зачистную пластину с геометрией Wiper c дополнительным большим радиусом закругления при вершине токарного резца (рис. 194).
Рис. 194. Схема эффективности снижения шероховатости Ra
сприменением зачистной пластины Wiper: а – стандартная пластина;
б– зачистная пластина Wiper
348

Увеличенный зачистной радиус при вершине резца сглаживает и снижает высоту микронеровностей на обработанной поверхности при одной и той же подаче. В результате появляется возможность увеличивать подачу токарного резца в 1,5…2 раза, сохранив одинаковую высоту микронеровностей. Это подтверждено экспериментальными исследованиями влияния подачи и радиуса закругления на высоту микронеровностей (рис. 195).
Рис. 195. Результаты сравнительного исследования влияния подачи So, радиуса закругления R и зачистной геометрии Wiper на высоту микронеровностей Ra
В результате исследований установлено, что требуемая шероховатость 1,6 мкм может быть обеспечена при одной и той же скорости резания при подаче 0,15 мм/об (0,8); 0,2 мм/об (1,2); 0,25 (1,6) и при подаче 0,4 мм/об с использованием зачистной геометрии Wiper. В результате использования зачистной геометрии Wiper производительность процесса точения увеличилась в 1,5…2 раза.
Влияние переднего угла проявляется в снижении пластической деформации при увеличении переднего угла, что приводит к снижению деформационной составляющей шероховатости.
349

Угол наклона главной режущей кромки изменяет направление схода стружки. При отрицательном значении стружка сходит в сторону поверхности резания и не портит обработанную поверхность.
Влияние износа режущего инструмента. При затуплении режущего инструмента шероховатость обработанной поверхности возрастает: при точении – на 50…60 %; при фрезеровании на 35…45 %; при сверлении – на 30…40 %, что связано с увеличением силы трения и пластической деформации поверхностного слоя.
На рис. 196 представлены сравнительные результаты измерения шероховатости в виде профиллограмм после точения острыми резцами и резцами с износом 0,1 и 0,2 мм.
Рис. 196. Сравнительные профиллограммы обработанной поверхности при точении резцами без износа (а),
с износом 0,1 мм (б) и с износом 0,2 мм (в)
Анализ этих осциллограмм показал, что при токарной обработке заготовок из стали ШХ 15 (НРС61,5), пластина DNGA 150612, инструментальный материал PCBN, связка TiC на режим
350