
книги / Резание материалов
..pdf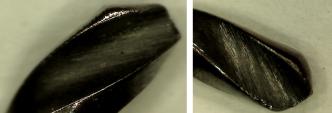
материала и высокой абразивностью углеродных волокон. На рис. 250 представлен износ сверл при сверлении композитов. Отчетливо видны следы истирания режущих кромок сверла от абразивного действия армирующих углеродных волокон.
Рис. 250. Износ сверл при сверлении композитов
Углеродное волокно получает все большее применение, поэтому возрастает необходимость автоматизации его производства для повышения производительности. Углеродное волокно может быть прочнее стали, легче алюминия и такое же жесткое, как титан. Углеродное волокно обычно применяется для уменьшения веса конструкции самолета, в результате чего снижается расход топлива, количество выбросов и повышается грузоподъемность.
Из углепластика, например, изготовляют такие конструкции самолета, как наружные створки, центральный отсек кессона крыла, панели кормовой части фюзеляжа и др.
Современные материалы становятся более труднообрабатываемыми. Это связано прежде всего с недостаточной стойкостью, производительностью и и эффективностью режущего инструмента. Кроме того, не обеспечивается требуемое качество обработки в процессе резания композиционных материалов.
На рис. 251 показаны примеры получения качества поверхностей при сверлении композиционных материалов. Видно, что плетенная структура композита разрушается режущими инструментами с вырывом волокон из матрицы. Внутри отверстий шероховатость также неудовлетворительная. В связи с этим растет трудоемкость по доводке этих отверстий на слесарных операциях вручную. Требуется проведение научно-исследовательских работ
452
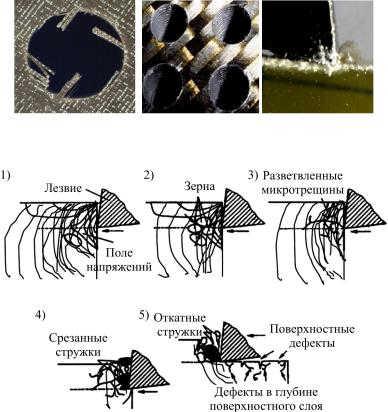
3.Расширение поля трещинообразования и трещин, сдвиг пучка волокон со срезанием, обрывом и вытягиванием волокон из матрицы.
4.Образование пылевидной стружки из срезанных сколотых частиц матрицы и срезанных разорванных и вытянутых частей армирующих волокон.
5.Образование дефектов поверхностного слоя – трещины
вобработанной поверхности из-за растягивающих напряжений и обрывки армирующих волокон.
Таким образом, основной причиной деламинации композиционного материала при резании лезвийным инструментом является периодическое сжатие армирующих волокон, затем срез, разрыв или вырыв волокон из разрушенной матрицы.
Из-за множества возможных комбинаций волокон и матрицы, а также специфических факторов отдельные аспекты, имеющие значение для обработки резанием, можно учитывать зачастую только применительно к какому-либо одному варианту композиционного материала. Реактопласты, напротив, остаются в твердом состоянии до достижения температуры разрушения; смягчение термопластов происходит начиная с 200 °C. Вследствие этого происходит снижение и без того низкой предельной допустимой температурной нагрузки на матрицу. Кроме того, расплавленная матрица может стать причиной налипаний материала на режущую кромку инструмента, что повышает его износ. В сравнении с волокнистыми тканями обработка ламинатов, армированных волокнистыми матами, заметно проще. В то время как у армированных матов следует преодолевать только прочность при изгибе и растяжении волокон, в случае тканей
вкачестве армирующегоэлемента добавляется тканевая структура.
Инструментальные материалы. Для резания композитов, ар-
мированных волокном, следует использовать инструментальные материалы, обладающие высокой устойчивостью к абразивному износу. К таким материалам наряду с твердыми сплавами (сорт K) относятся кубический нитрид бора (КНБ) и поликристаллические алмазы (PKD). Хотя твердые сплавы обладают высокой гибкостью геометрии режущей кромки инструмента и их изготовление на-
454

использование кондукторной втулки обеспечивает допуск на отверстие в пределах ±0,025 мм;
острая режущая кромка вставок из PCD с профильной впайкой обеспечивает оптимальное качество отверстий снижение риска расслоения и возникновения сколов;
геометрия сверла с двойной заточкой снижает расслоение;
универсальное сверло с четырехгранной геометрией режущей части гарантирует обработку различных углепластиков;
твердосплавные сверла с алмазным покрытием или с профильной впайкой вставок из PCD обеспечивают высокую стойкость и повышение качества обработки;
геометрия с двойной заточкой при вершине с алмазным покрытием обеспечивает стойкость и качество;
угол подъема стружечной канавки 40° улучшает эвакуацию стружки;
фрезы шевронной конструкции (режущая часть состоит из двух участков с разным направлением стружечных канавок) позволяют обрабатывать углепластик с большей толщиной; с небольшим углом винтовых канавок, уравнивающим осевые усилия
иснижающим радиальные силы резания. Угол наклона ленточки
ω1 = +5° – для обработки верхней кромки и ω2 = –5° – для обработки нижней кромки и снижения усилий резания;
сверла с лезвиями из поликристаллических алмазов имеют стойкость выше твердосплавных до 1500 раз.
Некоторые виды режущих инструментов для высококачественного фрезерования композиционных материалов приведены на рис. 253.
Рис. 253. Виды режущих инструментов для высококачественного фрезерования композиционных материалов
456
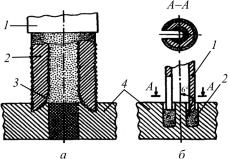
Рис. 254. Применение кольцевых алмазных сверл при сверлении композиционных материалов: а – со сферической внутренней поверхностью, б – разрезными трубками (1 – трубчатая оправка, 2 – алмазная коронка, 3 – сферическая поверхность, 4 – деталь)
Для сверления отверстий в деталях из композиционных материалов используются спиральные твердосплавные сверла с покрытиями из поликристаллических алмазов или кубического нитрида бора. Однако более эффективны кольцевые алмазные сверла, обрабатывающие отверстия диаметром свыше 1 мм
(рис. 254).
6.2. Выбор и назначение оптимальных параметров режущего инструмента
Определение оптимальных режимов работы инструмента является важной технико-экономической задачей в области машиностроения. Значение этой задачи особенно возрастает в связи с широкой автоматизацией машиностроительного производства, применением станков с числовым программным управлением, автоматических станочных линий и многооперационных станков, а также широким использованием новых материалов, как правило, обладающих низкой обрабатываемостью резанием. Оптимизация процессов резанием охватывает вопросы производительности, экономичности и точности обработки, качества поверхностного слоя и эксплутационной надежности и долговечности деталей машин. Оптимизация процессов обработки на
457
металлорежущих станках может быть осуществлена только на основе изучения физической сущности явлений, сопровождающих процесс резания, и основных закономерностей износа инструмента как главного фактора, влияющего на точность обработки.
В связи с этим весьма важно правильно назначать геометрию режущего инструмента. Порядок назначения может быть следующий:
1.Выбор режущего инструмента. Проводится согласно виду обработки. Например, токарный проходной отогнутый резец. Такой резец позволяет проводить обработку как цилиндрических, так и торцовых поверхностей со свободным выходом резца.
2.Выбор инструментального материала. Зависит главным образом от химсостава и механических свойств обрабатываемого материала. Например, для легких цветных сплавов выгоднее применять инструменты из быстрорежущих сталей, для чугунов, титановых сплавов и при прерывистом резании наиболее рациональны твердые сплавы группы ВК, для пластичных сталей – группа ТК.
3.Выбор типоразмера инструмента. Зависит от применяемого оборудования и параметров обрабатываемой заготовки. Например, токарные резцы выбираются по размерам сечения державки резца для конкретного токарного станка.
4.Выбор геометрических параметров резца. Зависит от условий обработки. Геометрические параметры выбираются по справочникам и по рекомендациям с учетом влияния рассмотренных выше физических явлений процесса резания на износ и стойкость инструмента.
6.3. Назначение оптимальных режимов резания различными методами
Под оптимальными режимами резания понимают такое наивыгоднейшее сочетание глубины резания t, подачи S и скорости резания V, при котором в данных условиях производства обеспечивается максимальная производительность, наименьшая себестоимость и требуемое качество обработки.
458
дится так же, как и при назначении режимов резания, – табличным методом.
Далее производится выбор подачи из следующих ограничивающих факторов:
1.Величина шероховатости обработанной поверхности (подача выбирается табличным способом S1).
2.Прочность пластины твердого сплава (табличным спосо-
бом S2).
3.Прочностьмеханизмаподачистанка(табличнымспособомS3).
4.Жесткостьдетали (выбирается сучетом способакрепления).
5.Прочность державки резца. Резец можно считать балкой, защемленной одним концом и нагруженной на другом тремя сила-
ми – Рz, Ру, Рх, создающими сложное напряженно-деформированное состояние в державке резца. Однако, как показывает анализ, с достаточной для практики точностью прочность резца может быть рассчитана по силе Рz. Итак,
Mизг = Pz l; [Mизг] = W [ изг],
где W – момент сопротивления; [ изг] – допускаемое напряжение на изгиб.
Для прямоугольного сечения B×H момент сопротивлений
W = B·H2/6;
для круглого сечения диаметром D
W= D3/32.
6.Жесткость державки резца. Под действием сил резания державка резца деформируется, и в результате отклонения вершины резца от первоначального положения возникают погрешности. Стрелка прогиба f при черновом точении равна 0,1 мм, при получистовом и чистовом точении f = 0,03...0,05 мм; момент инерции
для круглого сечения J = D4/64, для квадратного J = B·H3/32. Далее производится расчет скорости резания Vрез. Скорость
резания ограничивает или материал резца, или мощность станка. Скорость резания (Vрез, м/мин) рассчитывается из условия полного использования режущих свойств инструмента:
460