
книги / Резание материалов
..pdf
Рис. 215. Изменение предела усталостной прочности σ–1 на различной базе испытаний N циклов дисков компрессора из титанового сплава ВТ3-1, протянутых на серийных (1) и скоростных (2) режимах, σm = 140 МПа
В результате совместного исследования усталостной прочности образцов дисков турбин из сплава ЭП742-ПД и двухзамковых лопаток турбин из сплава ЖС6К при переменных напряжениях в пределах 90 МПа для сечения по первой впадине замка лопатки на базе испытаний N = 5 107 циклов и характера их разрушения установлено (рис. 216), что снижения усталостной прочности при использовании методов скоростного протягивания пазов не обнаружено; наоборот, на ряде деталей установлено увеличение усталостной прочности от 10 до 60 %.
Разрушения при усталостных испытаниях происходили в основном по профильной части пера двухзамковых лопаток турбины. Очаги усталостных трещин на профильной части располагались, как правило, на входной кромке, долговечность профильной части составляла 2 105…5 107 циклов.
371
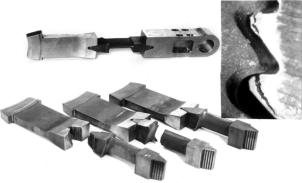
Рис. 216. Характер разрушения дисков и лопаток при совместных усталостных испытаниях замковых соединений
Таким образом, проведение усталостных испытаний убедительно показало, что применение нового метода скоростного протягивания замковых соединений дисков и лопаток компрессоров и турбин ГТД на повышенных до 25…30 м/мин скоростях резания вместо применяемых низких скоростей 1,5…2 м/мин не снижает сопротивление усталости, а часто повышает его до 60 %, что обеспечивает более высокую надежность и долговечность авиационных двигателей в эксплуатации.
5.5. Особенности образования поверхности при чистовой лезвийной и абразивной обработке
Чистовая лезвийная обработка деталей машин проводится на таких операциях окончательной обработки, как чистовое точение, чистовое фрезерование, зенкерование и развертывание отверстий, протягивание наружных и внутренних поверхностей. Основная задача чистовой обработки – обеспечить заданное качество поверхностного слоя и заданную точность поверхности. В качестве режущих инструментов применяются лезвийные инструменты с доведенными режущими гранями и кромками. Припуски на обработку обычно составляют 0,2…0,5 мм. Требуется обеспечить шероховатость обработанной поверхности по Ra не более 2 мкм, а точность в пределах 0,02…0,1 мм.
372
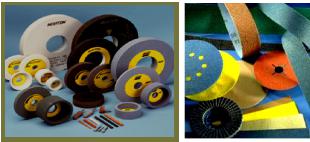
Для этого применяют специальные прецизионные станки, приспособления и инструменты. Обработку ведут на повышенных скоростях резания, минимальных подачах с оптимальной геометрией инструмента.
Чистовая абразивная обработка проводится с помощью раз-
личных видов абразивного инструмента методами шлифования, полирования, доводки, притирки, обдувки и т.п. Припуски на обработку составляют 0,05…0,2 мм. При этом шероховатость поверхности может достигать величиныпо Ra впределах0,05…1,25 мкм.
5.5.1. Понятие об абразивном инструменте. Характеристики абразивного инструмента
Шлифование представляет собой операцию обработки поверхности заготовки абразивным инструментом. Абразивный инструмент чаще всего включает в себя три элемента: абразивный материал, связку и поры.
Под абразивными понимаются материалы естественного или искусственного происхождения, зерна которых обладают высокой твердостью и способностью резания. Абразивные инструменты могут быть изготовлены со связанными зернами (шлифовальные круги, головки, сегменты, бруски, шкурки) (рис. 217) и в виде несвязанных, свободных зерен (пасты, суспензии, порошки). Абразивные инструменты характеризуются материалом зерен и их величиной, видомсвязки, твердостью, структурой, формойиразмерами.
Рис. 217. Общий вид абразивных инструментов со связанным абразивом: круги, бруски и ленты
373
Алмазные круги и бруски дополнительно характеризуются конструкцией и маркой алмазов.
Абразивные материалы делятся на искусственные (синтетические) и естественные (природные).
Искусственные абразивные материалы. К ним относятся электрокорунд, карбид кремния (карборунд), карбид бора, синтетические алмазы, кубический нитрид бора (эльбор). Более широко применяются в промышленности, чем естественные.
Электрокорунд (А12О3). Большая часть (≈80 %) абразивного инструмента изготавливается из электрокорунда, который получают путем плавки глинозема в электрических печах. Существует несколько разновидностей электрокорунда:
Э – электрокорунд нормальный (91…99 % А12О3) (марки: 16А, 15А, 14А, 13А, 12А); применяется при черновом, получистовом и чистовом шлифовании сталей и чугунов, а также для обдирки литья и при заточке режущих инструментов из инструментальной стали.
ЭБ – электрокорунд белый (97…99 % А12О3) (марки: 25А, 24А, 23А, 22А); превосходит по своим режущим свойствам электрокорунд нормальный, так как содержит меньше примесей. Применяется при шлифовании прочных и вязких сталей (незакаленных и закаленных), ковкого чугуна, заточки инструментов из быстрорежущих сталей.
ЭХ – электрокорунд хромистый (97 % А12О3+2%CrO) (марки: 34А, 33А, 32А); получают в электропечах при плавке глинозема с добавлением хромистой руды. Зерна имеют розовую окраску.
ЭТ – электрокорунд титанистый марки 37А (содержит
≈97 % А12О3 и 2 % ТiO2); при плавке глинозема добавляют соединения титана. ЭХ и ЭТ применяют при повышенных режимах шлифования углеродистых и конструкционных сталей и при чистовой обработке.
М – монокорунд (97 % А12О3), зерна которого представляют отдельные кристаллы и имеют большое число режущих граней (марки: 45А, 44А). Он получается из боксита оксисуль-
374
фидным способом в виде зерен, состоящих из изометрических кристаллов корунда различной величины. Сущность способа получения монокорунда состоит в сплавлении боксита с сернистым железом и восстановителем – антрацитом или коксом – в электропечах. Применяется для обработки весьма прочных сталей, ковкого чугуна, быстрорежущей стали.
Титанистый электрокорунд (ЭТ) представляет собой соединения 98,5 % А12О3 + 1,5 % ТiO2, отличается от нормального электрокорунда большей вязкостью и стабильностью свойств, что хорошо для доводочно-притирочных работ.
Зерна электрокорунда ЭХ, ЭТ и М имеют более высокие режущие свойства, чем Э и ЭБ.
Карбид кремния (SiС) – химическое соединение кремния с углеродом, получается при спекании кварцевого песка и кокса. Зерна SiС имеют более высокую твердость, чем электрокорунд. Применяются две разновидности карбида кремния: черный КЧ
(95…97 % SiС) марок 55С, 54С, 53С, 52С и зеленый КЗ (98…99 % SiС) марок 64С, 63С, 62С. Недостаток карбида кремния – высокая хрупкость и малая прочность. Поэтому при обработке сталей он почти не используется. Карбид кремния применяется при заточке твердосплавного инструмента, при шлифовании титана, при абразивной обработке хрупких материалов: чугунов, бронзы; тугоплавких сплавов, металло- и минералокерамики, а также неметаллических материалов – резины, кожи, стекла, мрамора и т.д.
Карбид бора (В4С) – химическое соединение бора с углеродом – получают плавлением борной кислоты В2О2 с нефтяным коксом при температуре 2000...2350 °С. Карбид бора имеет высокую твердость, большую хрупкость и применяется в виде порошков для доводочных процессов и при ультразвуковой обработке хрупких материалов и весьма твердых – рубина, корунда, кварца. При доводке твердосплавных режущих инструментов обеспечивает минимальный радиус округления режущей кромки до 6…10 мкм, тогда как электрокорунд обеспечивает только до 15 мкм.
Борсиликарбид в отличие от карбида бора не содержит вредной примеси графита, отличается большей стабильностью свойств, бо-
375
лее прочен и дешевле. На операциях доводки показал на 30…40 % более высокую производительность, чем карбидбора.
Окись хрома – порошок темно-зеленого цвета для доводки. Получается из бихромата калия с примесью серы.
Окись железа (крокус) – тонкий полировальный порошок, состоящий в основном из кристаллической окиси железа. Получается переработкой железного купороса и щавелевой кислоты.
Синтетические алмазы (АС) получают в виде мелких кристаллов, размером обычно не более 1 мм. Синтез алмазов происходит в результате воздействия на графит высоких давлений (до 1,7·10 кгс/см2) и высоких температур (до 2500 °С). В присутствии металлического катализатора происходит перекристаллизация углерода из гексагональной структуры графита в кубическую структуру алмаза. Синтетические алмазы в зависимости от прочности делятся на пять марок: низкой прочности (АСО), повышенной прочности (АСР), высокой прочности (АСВ), монокристальные (АСК и АСС).
Марка АС2 обычной прочности, предназначена для изготовления инструментов на органической связке, а также паст и порошков.
Марка АС4 повышенной прочности, применяется для инструментов на керамической и металлической связках.
Марка АС6 высокой прочности, применяется для инструментов на металлической связке, для чернового шлифования.
Марка АС15 по прочности близка к прочности природных алмазов.
Наряду с монокристаллическими алмазными зернами выпускаются поликристаллические, которые обозначаются АР.
Алмазные микропорошки марок АСМ, АМ, АСН, АН предназначены для притирочных и доводочных работ при доводке твердых сплавов и сталей, а также алмазов и рубинов.
Отрицательное свойство алмазов заключается в том, что при обработке стальных заготовок при температуре 850…900 °С наблюдается активная диффузия углерода из алмаза в железо, что резко повышает износ алмаза. В таких случаях лучше применять кубический нитрид бора.
376
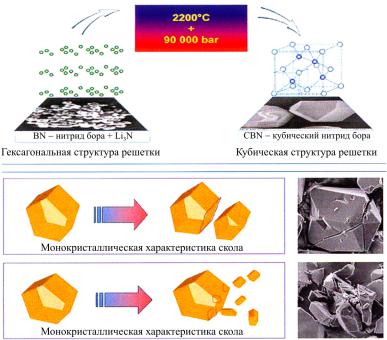
Кубический нитрид бора (КНБ, боразон или эльбор) состоит из 44 % бора и 56 % азота. Твердость его ненамного уступает алмазу, а теплостойкость в 2 раза выше алмаза (до 1500…1900 °С). Процесс изготовления достаточно сложен (рис. 218). Требуется обеспечить высокое давление до 90 000 бар и высокую температуру до 2200 °С. В результате гексогональная структура решетки исходного материала BN переходит в высокопрочную кубическую структуру решетки CBN. Круги из эльбора наиболее эффективны при чистовом шлифовании, заточке и доводке инструментов из быстрорежущих сталей повышенной производительности (кобальтовых и высокованадиевых). Эльбор в России выпускается двух марок: ЛО – обычной механической прочности с обычным содержанием основной фракции и ЛП – повышенной механической прочности, с повышенным содержанием основной фракции.
Рис. 218. Схема производства кубического нитрида бора CBN
377
В сводной табл. 22 приведены основные механические свойства рассмотренных искусственных абразивных материалов.
Таблица 2 2 Механические свойства искусственных абразивных материалов
Абразивный материал |
Микротвердость |
Термостойкость, °С |
НV, кгс/мм2 |
||
Алмаз |
10000 |
800…900 |
Кубический нитрид бора |
9000 |
1500…1900 |
Карбид бора |
3700…55000 |
700…800 |
Карбид кремния |
3300…3600 |
1300…1400 |
Электрокорунд |
2000…2300 |
1700…1800 |
Естественные материалы. К ним относятся кварц (кремнезем SiО2), наждак, корунд и алмаз. Природные абразивные материалы, за исключением алмаза, имеют низкие режущие свойства и для абразивной обработки металлов почти не применяются.
Природный алмаз – минерал, состоящий из кристаллического углерода. Природные технические алмазы содержат небольшие примеси окислов алюминия, железа, кальция, кремния, марганца, которые придают им различный цвет. Атомы углерода в кристаллической решетке алмаза очень прочно связаны, что обеспечивает высокую твердость и износостойкость. Твердость алмаза по шкале Мооса равна 10, микротвердость 10 060 кгс/мм2, модуль упругости 9·104 кгс/см2, плотность 3,52 г/см3.
Недостатки алмазов: высокая хрупкость, большая способность к адгезии с титаном, сталью и другими металлами, сравнительно низкая теплостойкость (800…900 °С). Натуральные технические алмазы применяются для правки шлифовальных кругов.
Зернистость абразивных материалов. Абразивные материа-
лы подвергаются дроблению, обогащению согласно ГОСТ 3647–80 ониделятсяпо зернистости натри группы (табл. 23).
Шлифовальные зерна от № 200 до 16 – зерна основной фракции размером от 2000 до 160 мкм; шлифовальные порошки от № 12 до 3 – зерна от 125 до 28 мкм; микропорошки от М40 до М5 – зерна от 40 до 3 мкм.
378

Таблица 2 3 Зернистость абразивных материалов
Зерни- |
|
Марки абразивных материалов |
|
|||
FEPA (Запорожье)1 |
2 |
2 |
FEPA3 |
|||
стость, мкм |
|
|
ГЕРА 43-D |
ГЕРА 42-D |
(Боксито- |
|
гибкие |
твердые |
|||||
|
гибкие |
твердые |
горск) |
|||
|
|
|
|
|
||
1 |
2 |
3 |
4 |
5 |
6 |
|
|
|
Шлифовальное зерно |
|
|
||
200/2000 |
– |
– |
– |
F10 |
– |
|
160/1600 |
Р12 |
F12 |
Р12 |
F12 |
– |
|
– |
– |
F14 |
Р16 |
F14 |
– |
|
125/1250 |
Р16 |
F16 |
Р20 |
F16 |
F16 |
|
100/1000 |
Р20 |
F20 |
– |
F20 |
F20 |
|
– |
– |
– |
Р24 |
F22 |
– |
|
80/800 |
|
F22 |
Р30 |
F24 |
F24 |
|
– |
Р24 |
F24 |
– |
– |
F36 |
|
63/630 |
Р30 |
F30 |
– |
F30 |
F30 |
|
50/500 |
Р36 |
F36 |
Р36 |
F36 |
F36 |
|
40/400 |
Р40 |
F40 |
Р40 |
F40 |
F46 |
|
– |
– |
F46 |
– |
F46 |
– |
|
32/320 |
Р50 |
F54 |
Р50 |
F54 |
F54 |
|
25/250 |
Р60 |
F64 |
Р60 |
F64 |
F60 |
|
20/200 |
|
F70 |
Р70 |
F70 |
F70 |
|
16/160 |
Р80 |
F80 |
– |
F80 |
F80 |
|
– |
Р100 |
F90 |
Р100 |
F90 |
– |
|
|
|
Шлифпорошки |
|
|
||
12/120 |
P120 |
F100 |
P120 |
F100 |
F100 |
|
10/100 |
P150 |
F120 |
P150 |
F120 |
F120 |
|
8/80 |
P180 |
F150 |
P180 |
F150 |
F150 |
|
6/60 |
P220 |
F180 |
P220 |
F180 |
F180 |
|
5/50 |
– |
F220 |
– |
F220 |
F230 |
|
|
|
Микрошлифпорошки |
|
|
||
М63 |
Р240 |
F220 |
Р240 |
– |
F230 |
|
– |
– |
– |
Р280 |
F230 |
F240 |
|
М50 |
Р280 |
F230 |
Р320 |
F240 |
F280 |
|
– |
Р320 |
F240 |
– |
– |
F320 |
|
– |
Р360 |
– |
Р360 |
– |
– |
|
– |
Р400 |
F280 |
|
|
|
|
М40 |
Р500 |
F320 |
Р400 |
F280 |
F360 |
|
– |
– |
– |
Р500 |
FЗ00 |
– |
|
М28 |
Р600 |
F360 |
Р600 |
– |
F400 |
379

|
|
|
Окончание |
табл. 2 3 |
||
|
|
|
|
5 |
|
|
1 |
2 |
3 |
4 |
6 |
||
– |
Р800 |
F400 |
Р800 |
F360 |
|
– |
М20 |
Р1000 |
F500 |
Р1000 |
F400 |
|
F500 |
– |
– |
– |
Р1200 |
– |
|
– |
М14 |
Р1200 |
F600 |
– |
F500 |
|
F600 |
М10 |
Р1500 |
F800 |
– |
F600 |
|
F800 |
М7 |
Р2000 |
F1000 |
|
|
|
|
1ТУ 02-00222226-016–96.
2ISO 8486–86.
3ТУ 3987-075-00224450–90.
Сортировка зерен от № 200 до 3 производится просеиванием через сита, и зернистость определяется размером стороны ячейки сита (в сотых долях миллиметра). Например, зерно № 16 просеивается через сито с размером ячейки 0,16 мм и остается на сите с размером ячейки 0,12 мм. Размеры зерен микропорошков определяются микроскопическим методом измерения или фотоэлектрическим – по скорости осаждениязерен.
Согласно ГОСТ 3647–80 в связанных абразивных инструментах размер зерна определяется процентом содержания основной фракции: В – высокое, 60…55 %; П – плотное, 55…45 %; Н – нормальное, 45…40 %.
Эльборовые зерна делятся на три группы зернистости: шлифзерно (Л25–Л16), шлифпорошки (Л12–Л4), микропорошки (ЛМ40–ЛМ1). Алмазные зерна (по ГОСТ 9204–70) делятся на две группы: шлифпорошки, получаемые путем рассева на ситах с контролем зернистости ситовым методом (12 зернистостей от 630/500 до 50/40); микропорошки, полученные путем классификации в жидкости и контролем размера зерен под микроскопом (11 зернистостей от 60/40 до 1/0). Зернистость алмазов обозначается дробно: числитель соответствует наибольшему, а знаменатель – наименьшему размеру зерен основной фракции.
В нашей стране освоено промышленное производство алмазных субмикропорошков, т.е. порошков с размером зерен 0,7; 0,5; 0,3 и 0,1 мкм. При помощи паст на основе субмикропорошков
380