
книги / Резание материалов
..pdf3 – допускаемые отклонения размеров – точность пластин; 4 – метод крепления пластин – через отверстие винтом или
косой тягой и др.; 5 – длина главной режущей кромки;
6 – толщина пластины; 7 – величина радиуса закругления кромок при вершине резца;
8 – тип режущей кромки – плоская поверхность или фаска; 9 – направление резания – вправо или влево; 10 – ширина фаски; 11 – угол наклона фаски на кромке;
12 – маркировка: МР3 обозначает геометрию стружколома (геометрию передней поверхности пластины) для получистовой обработки (М – middle) сталей группы обрабатываемости (Р) на средних режимах резания (3). Для чистовой обработки стружколом может обозначаться FP5 (finish), а для черновой cтружколом обозначается RP5 (rise).
Данная маркировка наносится на упаковку пластин и служит для постоянного контроля за расходованием их в кладовых и на инструментальном складе цехов и предприятий.
Применение износостойких покрытий. Существенно по-
высить эффективность использования режущих инструментов из различных инструментальных материалов позволила разработка новых видов износостойких покрытий. В последнее время появились различные методы нанесения этих покрытий. В табл. 15 представлены основные методы нанесения покрытий, из которых нужно отметить методы PVD и CVD. Эти покрытия представляют собой тонкие слои 2…12 мкм карбидов, нитридов, оксидов титана, тантала, ниобия, циркония повышают стойкость в 2…10 раз.
Метод PVD (Phisical vapor deposition) – метод физического осаждения из парогазовой фазы (ФОП). Происходит плазмохимическая реакция при слабом взаимодействии со структурой материала инструмента. Мала прочность удержания покрытия. Наносятся на быстрорез, твердый сплав. Работает на низких скоростях резания (рис. 144, а).
251
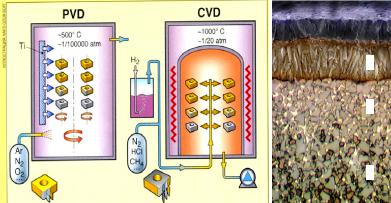
|
|
Таблица 1 5 |
|||
|
Методы нанесения износостойких покрытий |
||||
|
|
|
|
|
|
№ |
Вид нанесения |
Способ нанесения |
|||
п/п |
|||||
|
|
|
|
||
1 |
Химико-термическое |
Диффузионное насыщение азотом |
|||
|
|
Диффузионное насыщение азотом и углеродом |
|||
|
|
Диффузионное насыщение бором, хромом и др. |
|||
2 |
Термомеханическое |
Плазменное напыление |
|||
|
|
Детонационное напыление |
|||
3 |
Электрофизическое |
Ионно-плазменное напыление (PVD) (для б/с) |
|||
4 |
Химическое |
Химическое осаждение из газовой среды |
|||
|
|
(CVD). Износостойкость самая высокая. |
|||
|
|
Плазмоактивированное химическое осаждение |
|||
|
|
из газовой среды |
|||
5 |
Электрохимическое |
Электроисковое легирование |
|||
|
|
|
|
|
|
|
|
1 |
|
2
3
4
а |
б |
в |
Рис. 144. Методы нанесения покрытий PVD (а), CVD (б) и общий вид многослойного покрытия (в)
Метод CVD (Chemical vapor deposition) – метод химического осаждения покрытий из парогазовой среды (ХОП). Происходит химическая реакция между элементами парогазовой смеси и структурой материала инструмента. Наносят на пластинки твердого сплава любой формы. Наиболее прочное соединение обеспечивает возможностьувеличивать скоростирезания иподачи (рис. 144, б).
252
Алюминиевое покрытие (Аl2О3) – высокая износостойкость и твердость при высоких скоростях резания, сопротивление диффузионному и окислительному износу.
Карбид титана (ТiС) – высокая износостойкость при низких скоростях резания. Хорошее сцепление с основой.
Нитрид титана (ТiN) (золотой цвет) – высокое сопротивление окислению при высоких температурах.
Титаноалюминиевый нитрид (ТiАlN) – высокая теплостойкость и износостойкость. Высокоскоростная и прерывистая обработка нержавеющих сталей.
На рис. 144, в представлено многослойное покрытие твердого сплава, цифрами обозначены следующие слои:
1– полированный слой из Al2O3, стойкий к абразивному
ихимическому износу;
2– слой TiCN – адгезионное покрытие MT CVD и дополнительная износоустойчивость;
3– градиентный слой для повышения прочности;
4 – многокарбидная основа твердого сплава, устойчивая к пластической деформации.
Покрытия наносятся на инструменты из быстрорежущих сталей и твердых сплавов.
Особенности износа инструмента из быстрорежущей стали с покрытием:
1.Покрытие позволяет увеличить скорости резания в 1,5…2 раза
сувеличением стойкости инструментов, но есть ограничение по пластическомуразрушениюосновы.
2.Увеличение подачи повышает вероятность хрупкого разрушения покрытия.
3.При скоростях активного наростообразования покрытие не дает эффект.
Особенности износа инструмента из твердого сплава с покрытием:
1.При скоростях резания 20…100 м/мин наблюдается рост усталостных трещин и хрупкого отрыва покрытия.
2.При скоростях резания 100…150 м/мин появляется коррозионное растрескивание и глубинная коррозия с образованием поверхностных очагов окисления.
253
3. При скоростях более 150 м/мин работоспособность покрытия резко возрастает, так как повышается сопротивление диффузионному износу.
Минералокерамика. В основе минералокерамики лежит окись алюминия Аl2О3. Минералокерамику на основе оксида алюминия можно разделить на три группы.
1. Чисто оксидная керамика (белая) (АlО3 – до 99,7 %):
ЦМ-332, ВО-13. Оксидная минералокерамика ЦМ-332 дешевле других инструментальных материалов, имеет (на 2…5 единиц) более высокую твердость и теплостойкость 1200 °С, а также повышенную износостойкость по сравнению с твердыми сплавами. Однако этот материал хрупок и малопрочен ( b ≈ 300 МПа). Вследствие ее малой прочности используемая до настоящего времени оксидная минералокерамика ЦМ-332 не нашла широкого применения в качестве режущего материала.
Всесоюзный научно-исследовательский институт абразивов
ишлифования (ВНИИАШ) создал оксидную керамику марки ВШ-75. Ее рекомендуется применять при чистовой и получистовой обработке сталей и чугунов. Минералокерамика допускает скорость резания в 1,5…2 раза выше, чем твердые сплавы.
2.Оксидно-карбидная (черная) керамика – это оксид алюми-
ния с добавлением карбидов тугоплавких металлов (титана, вольфрама, молибдена) для повышения ее прочностных свойств
итвердости. Всесоюзный научно-исследовательский институт тугоплавких металлов и твердых сплавов (ВНИИТС) разработал минералокерамку оксидно-карбидного типа, полученную методом горячего прессования марок В-3, ВОК-60 и ВОК-63 и методом холодного прессования ВО-13, ВО-15, ВО-16. В основе ее лежат окись алюминия и добавки карбидов тугоплавких металлов – вольфрама, титана. Режущие свойства их выше керамики оксидной; стойкость в 3…5 раз выше, чем стойкость сплавов Т3ОК4, В-3, ВОК-60, ВОК-63. Минералокерамика применяется для получистовой и чистовой обработки сталей и высокопрочных чугунов. Однако минералокерамика уступает этим сплавам по теплопроводности, имеет более низкий предел прочности на изгиб.
254
3. Нитридная керамика. Наряду с материалами на основе оксида алюминия выпускается материал на основе нитрида кремния – силинит-Р и кортинит ОНТ-20 (с добавками оксидов алюминия и некоторых других веществ). Физико-механические свойства режущейминералокерамики приведеныв табл. 16.
Таблица 1 6 Физико-механические свойства режущей минералокерамики
|
|
|
|
|
Марка |
Плотность, г/см3, |
Твердость |
Предел прочности при |
|
не менее |
НRА |
изгибе, МПа, не менее |
||
|
||||
ЦМ-332 |
3,85 |
90…92 |
295…350 |
|
ВО-13 |
3,95 |
90…92 |
450…500 |
|
ОНТ-20 |
4,30 |
92…94 |
500…650 |
|
В-3 |
4,50 |
92…94 |
560…600 |
|
ВОК-60 |
4,20 |
92…94 |
560…600 |
|
ВОК-63 |
4,20 |
92…93 |
635…700 |
|
Силинит-Р |
– |
94…96 |
500…700 |
Высокие режущие свойства инструментов из минералокерамики проявляются при скоростной обработке сталей и высокопрочных чугунов (500…1000 м/мин), причем чистовое и получистовое точение и фрезерование повышает производительность обработки деталей до 2 раз при одновременном возрастании периодов стойкости инструментов до 5 раз по сравнению с обработкой инструментами из твердого сплава.
Минералокерамика выпускается в виде неперетачиваемых пластин, что существенно облегчает условия ее эксплуатации.
Инструмент, оснащенный пластинами из керамики, прошел промышленные испытания. На ВАЗе режущую керамику применяют на семи позициях чистовой обработки деталей из серого чугуна. На КамАЗе режущую керамику широко используют при обработке тормозных барабанов, гильз деталей. На заводе «Красный пролетарий» при чистовой обработке деталей из серого чугуна резцы ВК3-М были заменены керамикой ВОК-60. Машинное время сократилось за счет увеличения скорости резания почти в 6 раз при одновременном увеличении стойкости в 5…6 раз.
255
Разработанные отечественные марки керамики не уступают по своим свойствам физико-механическим свойствам керамики зарубежных фирм. Применение режущих пластин из керамики позволило повысить скорость резания в 2…4 раза при одновременном повышении стойкости до двух раз.
Абразивные материалы. Абразивные материалы – это вещества природного или синтетического происхождения, содержащие минералы высокой твердости и прочности, зерна и порошки которых способны обрабатывать поверхности других тел путем царапания, скобления или истирания. Их применяют для изготовления шлифовальных и заточных кругов, головок, брусков, хонов, доводочных порошков и паст. Абразивные материалы разделяют на естественные и искусственные. К первым относятся
кварц, наждак и корунд.
Для абразивных инструментов в основном применяют искусственные абразивные материалы: электрокорунд, карбид кремния, карбид бора, силикокарбид бора.
Электрокорунд получают методом электрической плавки в дуговых печах при температуре 2000…2500 °С из материалов, богатых окисью алюминия (бокситы, глинозем). В зависимости от процентного содержания А12О3 электрокорунд бывает нормальный (14А), белый 25А, легированный 34А и монокорунд 45А.
Карбид кремния SiC получают в печах при температуре 1800…1850 °С из нефтяного кокса, антрацита, т.е. из материалов, богатых кремнеземом и высоким содержанием углерода. Карбид кремния разделяется на черный 54С и зеленый 63С. Лучший из них зеленый: он имеет большую твердость и острые режущие кромки.
Карбид бора В4С получают при плавке борной кислоты В2О3 и нефтяного кокса в электропечах. Применяется в виде порошков или паст для доводки твердосплавного инструмента.
Сверхтвердые инструментальные материалы и алмазы.
Одним из направлений совершенствования режущих свойств инструментов, позволяющих повысить производительность труда при механической обработке, является повышение твердости и тепло-
256
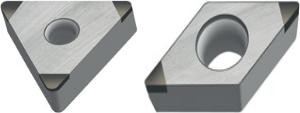
стойкости инструментальных материалов. Наиболее перспективными в этом отношении являются синтетические сверхтвердые материалы (СТМ) наоснове алмаза иликубического нитрида бора.
Для обработки закаленных сталей, высокопрочных чугунов и других твердых материалов на основе железа созданы сверхтвердые материалы, химически инертные к железу и углероду. Такие материалы получены по технологии, близкой к технологии получения алмазов, но в качестве исходного вещества используется не графит, а нитрид бора.
Кубический нитрид бора (КНБ) представляет собой соединение двух химических элементов – бора (43,6 %) и азота (56,4 %). По твердости он близок к алмазу. Теплостойкость КНБ – 1300 °С. КНБ выпускается в разных странах под названиями эльбор (Россия), кубонит (США), белбор (Беларусь), киборит (Украина).
На основе кубического нитрида бора в нашей стране создано много сверхтвердых материалов под общим названием композиты. Наиболее широкое применение получили композиты 01 (эльбор-Р), 10 (гексонит-Р), композиты 05 и 09.
Область применения СТМ до недавнего времени ограничивалась из-за сравнительно небольших размеров поликристаллов. В настоящее время освоен выпуск двухслойных неперетачиваемых пластин, состоящих из твердого сплава (основа) и слоя из поликристаллов алмаза или нитрида бора толщиной до 0,5 мм, что повысит общую эффективность использования инструментов из сверхтвердых материалов (рис. 145). В зависимости от размера зерен эльбор выпускается в виде шлифпорошков и микропорошков.
Рис. 145. Общий вид вставок из кубического нитрида бора, напаянных на твердосплавные пластины
257
Сверхтвердые синтетические материалы – это композиционные поликристаллические материалы, обладающие весьма высокой твердостью, приближающейся к твердости алмаза. Существует три их разновидности: композиты (композит 01 – эльбор-Р; композит 05; композит10 (гексонит-Р); исмит, карбонадоисилинит.
Композиты обладают высокой твердостью и теплостойкостью (табл. 17) и поэтому применяются для резцов, фрез, сверл и т.д., для тонкой и чистовой обработки стальных и чугунных деталей, закаленных сталей и материалов с большой твердостью (до НRС 60), а также для обработки материалов при высоких скоростях резания (свыше 600 м/мин). Применение инструмента, оснащенного композитом, позволяет в 2…5 раз повысить производительность обработки материалов с высокой твердостью и обеспечивает высокое качество обработанной поверхности.
Таблица 1 7 Сравнительные характеристики СТМ на основе нитрида бора
Марка |
Первоначальное |
Твердость |
Теплостойкость, |
|
название |
НV |
°С |
||
|
||||
Композит 01 |
Эльбор-Р |
60…80 |
1100…1300 |
|
Композит 02 |
Белбор |
60…90 |
900…1000 |
|
Композит 03 |
Исмит |
60 |
1000 |
|
Композит 05 |
Композит |
70 |
1000 |
|
Композит 09 |
ПТНБ |
60…90 |
1500 |
|
Композит 10 |
Гексанит-Р |
50…60 |
750…850 |
Эффективность применения лезвийных инструментов из различных марок композитов связана с совершенствованием конструкции инструментов и технологии их изготовления и с определением рациональной области их использования. Композиты 01 (эльбор-Р) и 02 (белбор) используют для тонкого и чистового точения и фрезерования без ударов деталей из закаленных сталей твердостью 55...70 НRС, чугунов и твердых сплавов ВК15, ВК20 и ВК25 с подачами до 0,20 мм/об и глубиной резания до 0,8 мм. Композит 05 применяют для чистового и получистового точения без ударов деталей из закаленных сталей твердостью 40...58 НRС,
258
чугунов твердостью до 300 НВ с подачами до 0,25 мм/об и глубиной до 2,5 мм. Композит 10 (гексанит-Р) используют для тонкого, чистового и получистового точения и фрезерования с ударами деталей из закаленных сталей твердостью не выше 58 HRC, чугунов любой твердости, сплавов ВК15, ВК20, ВК25 с подачей до 0,15 мм/об и глубиной резания до 0,6 мм. При этом период стойкости инструментов возрастает в десятки раз по сравнению с другими инструментальными материалами. Применяются они при обработке титановых, высококремнистых алюминиевых сплавов, стеклопластиков и пластмасс, твердых сплавов и других материалов.
Поликристаллы плотных модификаций нитрида бора превосходят по теплостойкости все материалы, применяемые для лезвийного инструмента: алмаз – в 1,9 раза, быстрорежущую сталь –
в |
2,3 |
раза, |
твердый сплав – в 1,7 раза, минералокерамику – |
в |
1,2 |
раза. |
Эти материалы изотропны (одинаковая прочность |
в различных |
направлениях), обладают микротвердостью мень- |
шей, но близкой к твердости алмаза, повышенной теплостойкостью, высокой теплопроводностью и химической инертностью по отношению к углероду и железу.
Алмазы. Алмаз – самый твердый в природе минерал (105 МПа), устойчивый к физическим и химическим воздействиям. Теплостойкость алмаза сравнительно невысока 700…900 °С (в среде кислорода). Природные алмазы кристаллизовались на большой глубине при огромном давлении земных недр и высокой температуре (2000…2500 °С) из расплавленной магмы, содержащей углерод.
Алмазы бывают естественные и искусственные, ювелирные и технические.
На технические цели используют 80 % природных алмазов. Они используются при изготовлении шлифовальных кругов и паст, а также для алмазно-металлических карандашей.
Технические алмазы разделяются на бортсы, балласы и карбонадо. Наилучшие из них – карбонадо. Это весьма тонкозернистые, твердые и плотные кристаллы, имеющие острые ребра.
259
Учитывая высокую стоимость природных алмазов, а также недостаточность их для промышленного использования, Институт физики высоких давлений Академии наук СССР в 1960 году синтезировал алмаз в лабораторных условиях, а Киевский институт сверхтвердых материалов в 1961 году начал промышленное производство искусственных алмазов из графита при высоких давлениях и температуре. Синтетические алмазы имеют те же химические и физико-механические свойства, что и природные.
Для изготовления режущих инструментов основное применение получили искусственные алмазы, которые по своим свойствам близки к естественным. При больших давлениях и температурах в искусственных алмазах удается получить такое же расположение атомов углерода, как и в естественных. Масса одного искусственного алмаза обычно составляет 1/8…1/10 карата (1 карат = 0,2 г). Вследствие малости размеров искусственных кристаллов они непригодны для изготовления таких инструментов, как сверла, резцы
ит.п., а поэтому применяются при изготовлении порошков для алмазных шлифовальных кругов и притирочных паст.
Алмаз как инструментальный материал имеет существенный недостаток: при повышенной температуре он вступает в химическую реакцию с железом и теряет работоспособность. Лезвийные алмазные инструменты выпускаются на основе поликристаллических материалов типа «карбонадо» или «баллас». Эти инструменты имеют длительные размерные периоды стойкости. Алмазы
иалмазные инструменты широко используются при обработке деталей из различных материалов. Для алмазов характерны исключительно высокая твердость и износостойкость. По абсолютной твердости алмаз в 4…5 раз тверже твердых сплавов и в десятки и сотни раз превышает износостойкость других инструментальных материалов при обработке цветных сплавов и пластмасс. Кроме того, вследствие высокой теплопроводности алмазы лучше других материалов отводят теплоту из зоны резания, что способствует гарантированному получению деталей с бесприжоговой поверхностью. Однако алмазы весьма хрупки, что сильно сужает область их применения.
260