
книги / Резание материалов
..pdf
В результате проведенного анализа микроструктуры поперечного сечения замков лопаток из жаропрочных сталей ЭИ961Ш, ЭИ736Ш и ЭП517Ш установлено, что в процессе протягивания незначительные структурные изменения происходят в весьма тонком поверхностном слое, малоразличимомприувеличении 300.
Влияния изменения скорости протягивания в диапазоне от 2 до 30 м/мин на микроструктуру поверхностного слоя не обнаружено. Не обнаружено и заметного влияния на формирование микроструктуры марки инструментального материала Р18 и ВК8 (см. рис. 205, а, в). Однако с увеличением износа протяжек до hз = 0,2 мм увеличивается глубина пластической деформации, а на поверхности деталей остаются следы срывов наростов и налипаний на режущие кромки протяжек.
Протягивание жаропрочных деформируемых и литейных сплавов на никелевой и железоникелевой основах сопровождается значительными пластическими деформациями поверхностного слоя, искажением характера его микроструктуры. Это наглядно представлено на рис. 206, 207.
Рис. 206. Микроструктура поперечного сечения поверхностного слоя деталей из сплава ВЖ102, протянутых на скоростях резания 2 м/мин (а) и 26 м/мин (б) многосекционными протяжками (×300)
Структура тонкого поверхностного слоя представляет собой вытянутые в направлении движения резца зерна твердого раствора. Особенно значительная деформация обнаружена на образцах, вырезанных из пазов в кольцах направляющих аппаратов из сплава ВЖ102, протянутых на низкой скорости резания 2 м/мин (см. рис. 206, а), и на образцах, вырезанных из замков лопаток из сплава ЭИ787-ВД, также на скорости 2 м/мин (см. рис. 207, а).
361

Рис. 207. Микроструктура поперечного сечения поверхностного слоя замков лопаток из сплавов ЭИ787-ВД, протянутых на скоростях резания 2 м/мин (а) и 26 м/мин (б)
Здесь на поперечных сечениях микрошлифов (2 м/мин) обнаружено измельчение кристаллических зерен, искажение кристаллической решетки поверхностного слоя, изменяется форма, размеры и ориентация зерен в тонком граничном поверхностном слое.
При скоростном протягивании этих деталей (26 м/мин) деформация граничного слоя намного меньше по глубине залегания и степени искажения кристаллической решетки. Это согласуется с даннымиобуменьшении силрезания сувеличением скоростирезания.
Исследование микроструктуры «елочных» пазов в дисках турбин из жаропрочных сплавов ЭИ437БУ-ВД, ЭИ698-ВД и ЭП742-ПД проводилось на торцовых поверхностях дисков вдоль кромки пазов. Особое внимание обращалось на состояние микроструктуры в наиболее опасных точках – во впадинах под первым
ивторым зубчиками и в самих зубчиках. Кроме того, проводилось исследование протянутой поверхности снаружи поверхностного слоя вдоль пути резания. Для этого вырезанные из пазов образцы полировались по обработанной поверхности весьма тонкими пастами на глубину 0,002…0,003 мкм. Затем с помощью растрового электронного микроскопа РЭМА-202 проводилось наблюдение и фотографирование с различным увеличением поверхности образцов, протянутых на различных режимах резания.
При протягивании «елочных» пазов в дисках турбин из ЭИ437БУ-ВД проведено сравнение микроструктуры торцовых поверхностей образцов, обработанных по серийной (Р18, V = 2 м/мин)
искоростной (ВК8, V = 26 м/мин) технологиям. Анализ фотографий (рис. 208) показывает, что торцовая поверхность образца паза после полированияи травленияпредставляетсобоймозаичную структуру.
362
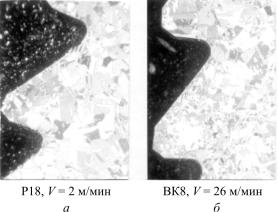
Рис. 208. Микроструктура «елочных» пазов в дисках турбин из сплава ЭИ437БУ-ВД, протянутых на серийных (а)
и скоростных (б) режимах резания (×20)
Отдельные блоки мозаики имеют разную травимость и различный цвет. На фотографиях видно, что у границ поверхностного слоя блоки мозаики меньше, чем в глубине поверхностного слоя, т.е. происходит дробление блоков мозаики под воздействием сил резания и возникающей пластической деформации.
5.4. Влияние качества поверхностного слоя на эксплуатационные свойства деталей
Установлено, что в результате приработки на трущихся поверхностях образуется оптимальная шероховатость, характерная для данных конкретных условий работы соединения. Поэтому если в процессе обработки деталей на поверхности обеспечить шероховатость, близкую к оптимальной, то время приработки на износ будет наименьшим. Оптимальная по износостойкости шероховатость поверхности зависит от вида соединений и конкретных условий эксплуатации.
На износ деталей оказывают влияние не только высота, но и направление неровностей исходной шероховатости трущихся поверхностей. Шероховатость поверхности оказывает сущест-
363
венное влияние на усталостную прочность деталей и коррозионную стойкость. С уменьшением шероховатости поверхности коррозионная стойкость деталей повышается.
Установлено, что наклеп поверхностного металла, созданный специальными технологическими приемами или полученный
врезультате механической обработки, приводит к увеличению контактной жесткости и контактной выносливости. Кроме того, наклепанный поверхностный слой деталей уменьшает интенсивность проявления всевозможных геометрических и структурных концентраторов напряжений в поверхностных слоях, повышая тем самым усталостную прочность деталей. Вместе с тем наклеп поверхностного слоя деталей после механической обработки понижает в большинстве случаев коррозионную стойкость деталей.
Наиболее заметно влияние остаточных напряжений в поверхностном слое на усталостную прочность деталей. При этом сжимающие напряжения повышают предел выносливости, а растягивающие уменьшают его. Имеются данные о том, что сжимающие остаточные напряжения в поверхностных слоях детали повышают прочность и надежность соединений с натягом, поэтому необходимо стремиться, чтобы в поверхностном слое формировались сжимающие напряжения возможно большей величины.
Высокие требования к обеспечению надежности деталей при работе в условиях эксплуатации предъявляются к деталям
ваэрокосмической отрасли машиностроения. Для контроля надежности и долговечности при внедрении новых технологических процессов резания предъявляется обязательное условие проведения усталостных испытаний опытных деталей. Такая комплексная работа проведена при внедрении нового процесса
скоростного протягивания деталей ГТД на АО «ОДК-ПМ». В замковых соединениях дисков и лопаток компрессора и турбины ГТД вследствие действия значительных центробежных сил, вибраций и высоких температур могут зародиться и развиться трещины усталостного характера, которые вызывают разрушение этих соединений, снижают ресурс и надежность газотурбинных двигателей.
364
Образование усталостных трещин обычно начинается с дефектов поверхности и распространяется по телу или по границам зерен структуры металла. Поэтому важной задачей является установление влияния на усталостную прочность обрабатываемых деталей основных параметров качества поверхностного слоя и режимов резания. В свою очередь эти параметры поверхностного слоя, как было установлено выше, в значительной степени определяются режимами резания. Поэтому при разработке и внедрении новых технологических процессов, связанных с изменением режимов обработки, в авиационном моторостроении предусматривается обязательный сравнительный контроль усталостной прочности деталей после обработки на новых режимах.
В связи с этим проведено исследование влияния скорости протягивания V и марки инструментального материала на предел выносливости (число наработки циклов до разрушения) протянутых поверхностей пазов в кольцах направляющих аппаратов (НА) из стали ЭИ962Ш и титанового сплава ОТ4, а также протянутых поверхностей пазов в дисках компрессоров из титановых сплавов ВТ3-1 и ВТ18У и в дисках турбин из жаропрочного деформируемого сплава ЭП742-ПД. Пазы в кольцах НА протягивались протяжками из Р18 на скорости резания 12 м/мин (одна половина кольца) и на повышенной скорости 26 м/мин (вторая половина кольца). Кольца разрезались на секторы с тремя пазами. На каждый вариант подготовлено по 6 таких образцов. Для измерения напряжений на протянутую поверхность паза и противоположную сторону кольца наклеивались тензометрические датчики
1, 2, 3, 4 (рис. 209) с базой 5 мм.
Образец закреплялся в специальном приспособлении таким образом, чтобы плоскость, в которой производилось знакопеременное нагружение, была параллельна оси протянутого паза.
Сравнительные усталостные испытания образцов выполнены в лаборатории усталостных испытаний при изгибных колебаниях по симметричному циклу с частотой основного тона, составляющей 330…340 Гц на электродинамическом стенде ВЭДС-200А. Образцы из стали ЭИ962Ш испытывались на уровне напряжения
365
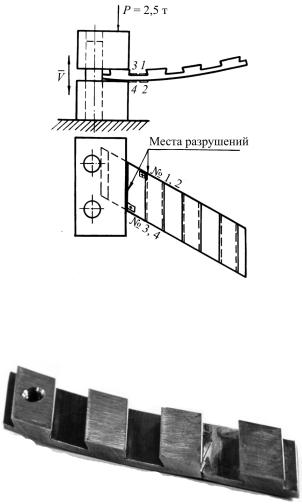
200…230 МПа. Число наработки циклов ограничивалось базой 20·106 циклов. Режим испытаний задавался и контролировался по тензодатчикам 1 и 3 и амплитуде перемещения конца верхней кромки паза образца 2А = 2…3 мм. Образцы из сплава ОТ4 испытаны на уровне напряжении 190 МПа.
Рис. 209. Схема препарирования тензодатчиков и нагружения образцов при усталостных испытаниях колец НА
Рис. 210. Характерный вид усталостной трещины в секторе кольца направляющего аппарата
366
Разрушение доводили до видимой усталостной трещины, характерный вид которой представлен на рис. 210. Число наработки циклов фиксировалось началом уменьшения колебаний образца и снижения частоты колебаний не более 1 Гц.
Анализ результатов сравнительных усталостных испытаний образцов, протянутых на различных скоростях резания, показал, что существенной разницы по наработке числа циклов между вариантами нет. Однако с увеличением скорости резания с 12 до 26 м/мин обнаруживается незначительное (на 8 %) возрастание числа наработки циклов от 19,02·106 до 20,55·106 для ЭИ962Ш, что можно объяснить снижением величины шероховатости и наклепа с увеличением скорости резания. Число наработки циклов испытаний образцов из титанового сплава ОТ4 для скорости резания 12 м/мин составляет в среднем 3,14·106, а для повышенной скорости резания 26 м/мин это число составляет 3,43·106 циклов, что на 10 % больше. Таким образом, применение скоростного протягивания пазов в кольцах НА не снижает усталостную прочность деталей, а незначительно (на 8…10 %) ее повышает.
Для проведения усталостных испытаний дисков компрессоров и турбин подготовлены семь дисков первой ступени ротора компрессора из титанового сплава ВТ3-1 (число пазов 35), три диска четвертой ступени ротора компрессора из титанового сплава ВТ18У (75 пазов в диске) и шесть дисков третьей ступени турбины из жаропрочного деформируемого сплава ЭП742-ПД (81 паз в диске) под операцию протягивания.
Протягивание дисков компрессоров и турбины проводилось непосредственно в производственных условиях механического цеха на модернизированном протяжном станке мод. 7А540 в диапазоне скоростей резания от 1,5 до 26,0 м/мин. Для протягивания спроектированы и впервые в отрасли изготовлены твердосплавные протяжки из ВК8 для обработки пазов типа «ласточкин хвост» (рис. 211) и «елка» (рис. 212).
При протягивании соблюдались все требования и инструкции по изготовлению, контролю пазов и сдаче годных протяжек в работу ссоответствующим заполнениемпаспортовна диски ипротяжки.
367
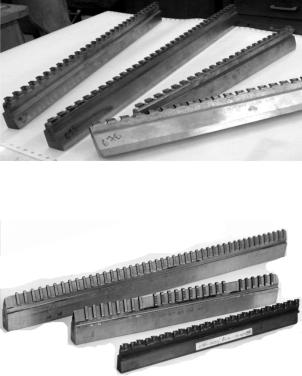
Рис. 211. Твердосплавные протяжки для протягивания пазов типа «ласточкин хвост»
Рис. 212. Твердосплавные протяжки для протягивания пазов типа «елка»
Для получения объективных сравнительных данных при исследовании параметров качества поверхности пазов и усталостной прочности половину всех пазов каждого диска протягивали на серийных низких режимах резания с применением серийных быстрорежущих протяжек из Р18, а вторую половину диска протягивали на скоростных режимах с применением твердосплавных протяжек из ВК8.
После протягивания из дисков вырезались на токарных станках ободы дисков с обработанными пазами. Затем ободы дисков разрезались на секторы и специальные образцы по методике, согласованной с ЦИАМ. Исследования усталостной прочности вырезанных образцов проводились в лабораториях ЦИАМ.
368
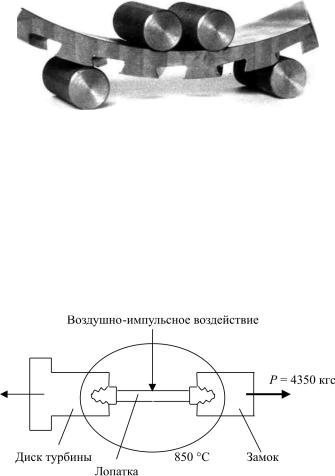
Образцы из дисков компрессора из материалов ВТ3-1 и ВТ18У испытывались согласно схеме, приведенной на рис. 213, при асимметричном цикле нагружения ( m = 140 и 250 МПа) с частотой 15…20 Гц при нормальной температуре на гидравлическом пульсаторе ZD-10PИ.
Рис. 213. Схема установки образцов из дисков компрессора для усталостных испытаний
Образцы с «елочными» пазами из дисков турбин (материал ЭП742-ПД) испытывались вместе со специально изготовленными двухзамковыми лопатками турбин из сплава ЖС6УВИ (рис. 214) на специальном вибростенде при асимметричном цикле нагружения – симметричный изгиб со статическим растяжением под нагрузкой 43,5 кН при температуре в сечении по первой впадине хвостовика 900 К.
Рис. 214. Схема соединения образцов дисков и двухзамковых лопаток турбины для усталостных
испытаний замковых соединений
369
Исследовались следующие варианты:
1.Серийные режимы для замков лопаток турбин и для пазов диска турбины (протягивание Р18, V = 1,5 м/мин).
2.Серийные режимы для замка и скоростные – для диска
(ВК8, V = 14 м/мин).
3.Скоростные режимы для замка и серийные – для диска турбины.
4.Скоростные режимы для замка и для диска турбины. Такое изменение режимов лезвийной обработки позволяет
оценить влияние скорости резания на изменение усталостной прочности обработанной детали, что может быть рекомендовано
идля сравнения процессов скоростного и серийного протягивания замков лопаток турбин.
Вкачестве примера на рис. 215 приведены результаты исследования влияния скорости протягивания V, материала протяжек
иасимметрии цикла нагружения m на предел выносливостизамковых пазов в дисках компрессора из титанового сплава ВТ3-1.
Врезультате анализа этих результатов усталостных испытаний установлено, что на базе испытаний N = 107 циклов предел
выносливости при нагрузке m = 140 МПа составляет 30 МПа для образцов, протянутых на низкой серийной скорости резания 1,5 м/мин быстрорежущими протяжками. Скоростное протягивание пазов (V = 26 м/мин, ВК8) способствует увеличению предела усталостной прочности в 1,6 раза, так как на базе N = 107 циклов = 50 МПа. Во всех случаях разрушение образцов происходило по следам обработки пазов (по продольным рискам у галтелей пазов) так же, как у пазов в кольцах НА. Меньшая шероховатость и рисочность способствует большой усталостной прочности замковых соединений, что наглядно проявилось при скоростном протягивании пазов в дисках компрессора из титанового сплава ВТ3-1. Аналогичные результаты получены и при усталостных испытаниях пазов в дисках компрессора из титанового сплава ВТ18У.
370