
книги / Резание материалов
..pdf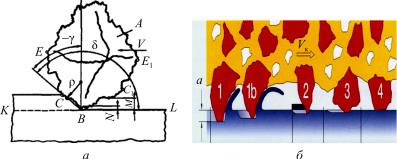
3.Скорость резания (30…70 м/мин) в десятки раз превышает скорость резания лезвийным инструментом.
4.Абразивные зерна имеют неправильную форму в виде
многогранника (рис. 222, а). Радиус округления вершин различный – от 8 до 20 мкм, часто соизмерим с толщиной среза. Передний угол зерен в большинстве случаев отрицательный. Угол резания обычно больше 90°. У каждого зерна можно выделить переднюю поверхность СВ, острые микровыступы М и N, участвующие в микрорезании.
Рис. 222. Типичная форма шлифующего зерна А при микрорезании (а)
исхема резания различными зернами круга (б)
Вто же время нужно отметить, что не все зерна на периферии круга могут участвовать в резании. Часть зерен снимает стружку,
ачасть зерен давит на поверхность или вообще не режет (рис. 222, б). Абразивные зерна можно разделить на режущие (1, 1b), скоблящие (2), давящие (3) и нережущие (4). В реальных условиях 85…90 % всех зерен не режет, а давит, пластически деформирует, наклепывает поверхностный слой.
5. Высокие скорости резания и неблагоприятная геометрия режущих зерен вызывает высокие температуры в зоне резания до 1000…1800 °С (рис. 223). Это может привести к неблагоприятным последствиям в виде шлифовочных прижогов и трещин.
6. Управлять процессом шлифования можно только за счет изменения режимов резания. Геометрией зерен и их расположением в круге практически нельзя управлять. При изготовлении
391

шлифовальных абразивных лент имеется возможность располагать абразивные зерна строго вертикально в электростатическом поле, что повышает режущую способность.
Рис. 223. Схема образования высокой температуры в зоне шлифования при взаимодействии абразивного зерна и поверхности
7.Шлифовальные круги обладают возможностью самозатачиваться при затуплении зерен. Затупленные зерна под действием силы резания вырываются из связки и обнажают новые режущие зерна в круге.
8.Обработанная шлифованием поверхность образуется в ре-
зультате копирования траектории движения режущих |
зерен |
и действующей пластической деформации, искажающей |
этот |
профиль (рис. 224). |
|
а |
б |
Рис. 224. Образование шероховатости (а) и ее искажение (б) при шлифовании из-за пластической деформации
392
Виды шлифования. Наиболее распространенными видами шлифования являются круглое (наружное и внутреннее), плоское, бесцентровое (наружное и внутреннее), фасонное, зубошлифование и резьбошлифование. Процесс шлифования обычно осуществляется при помощи трех движений: вращения шлифовального круга, вращения или возвратно-поступательного движения обрабатываемой детали и движения подачи, осуществляемого кругом или обрабатываемой деталью.
Скоростью резания при шлифовании является скорость вращения шлифовального круга Vк (м/с)
Vк = Dnд /1000 · 60,
где D – диаметр круга, мм; n – число оборотов круга, мин. Скорость вращения обрабатываемой детали V (м/мин):
V = Dnд /1000,
где D – диаметр обрабатываемой детали, мм; пд – число оборотов детали, мин.
Существуют три способа наружного круглого шлифования: шлифование продольной подачей; шлифование за один проход – глубинное; шлифование методом врезания (рис. 225).
Круглое наружное шлифование с продольной подачей (рис. 225, а) применяют при обработке относительно длинных (нежестких) деталей. Глубина резания, равная поперечной подаче, измеряется за время двойного продольного хода детали. При черновом шлифовании стали Sпоп = 0,01…0,07 мм/дв. ход; при чистовом Sпоп = 0,005…0,02 мм/дв. ход. Величина продольной подачи выбирается в зависимости от ширины круга Вк. Для чернового шлифования Sпрод = (0,3…0,85) Вк, для чистового
Sпрод = (02…0,3) Вк.
Шлифование методом врезания (см. рис. 225, б) применяется при обработке деталей относительно малой длины, особенно при шлифовании фасонных поверхностей. Поперечную подачу Sпоп принимают 0,002…0,007 мм/об. Иногда задается минутная подача 0,8…3 мм/мин.
393

Рис. 225. Схемы круглого наружного шлифования: а – шлифование с продольной подачей (L – длина шлифования, а – толщина среза); б– шлифованиеспоперечнойподачей; в– шлифованиеуступаишейкивала
Шлифование круглое глубинное наклонным кругом (см. рис. 225, в) применяется при обработке жестких относительно коротких деталей. Припуск в данном случае снимается за один про-
ход. Подача Sпоп = 1...6 мм/об. Чем больше диаметр обработки, тем больше подача. Основную работу осуществляет коническая часть
круга, а цилиндрическая только служитдля зачисткиповерхности. Внутреннее шлифование. При внутреннем шлифовании
(рис. 226) круг и деталь вращаются в разные стороны.
Скорость резания определяется так же, как скорость вращения круга, хотя действительная скорость резания больше скорости круга на величину Vд вращения детали. Круг вращается
394

и имеет возвратно-поступательное движение и поперечную подачу на каждый двойной ход. Учитывая, что скорость вращения детали во много раз меньше скорости круга Vк, ее в расчет не принимают. Шлифование протекает в более тяжелых условиях, чем наружное, так как длина дуги контакта больше и сила резания больше. При этом попадание СОЖ в зону резания затруднено. Диаметр шлифовального круга небольшой и составляет 0,75…0,25 % от диаметра отверстия. Диаметр посадочного отверстия небольшой, а вылет шлифовального шпинделя значителен, поэтому жесткость шпинделя недостаточна и подачи на глубину не должны быть большими. Они в два раза меньше, чем при наружном шлифовании.
Рис. 226. Схема внутреннего шлифования заготовки 1 кругом 2 (l0 – длина шлифования; L – длина шпинделя)
Плоское шлифование. Плоское шлифование осуществляется периферией круга и торцом на станках с прямоугольным и круглым столами (рис. 227). Применяется при обработке нежестких и массивных деталей.
Для плоского шлифования глубина резания t выбирается в зависимости от толщины обрабатываемой детали в пределах 0,05…0,1 мм. При шлифовании торцом круга поверхность контакта значительно больше, чем при шлифовании периферией и сопровождается большим тепловыделением в зоне резания. Поэтому выбирают более мягкие круги для торцового шлифования, чем для периферийного. Глубинарезания принимается равной0,05…0,1 мм.
395

Рис. 227. Схема плоского шлифования периферией круга
иторцом круга соответственно на прямоугольном столе станка (а, б)
ина круглом столе станка (в, г)
Бесцентровое шлифование. Применяется для шлифования наружных и внутренних поверхностей напроход и в упор. На бесцен- трово-шлифовальных станках заготовки обрабатывают в незакрепленномсостоянии (рис. 228). Преимущества бесцентрового метода:
1)высокие режимы резания за счет устойчивой опоры детали по всей длине;
2)отсутствие прогиба детали при шлифовании обеспечивает
еегеометрическую форму;
3)самый производительный метод в массовом и крупносерийном производствах с наивысшей точностью и качеством поверхности.
Рис. 228. Общий вид расположения кругов и детали (а) и схема бесцентрового шлифования (б)
396
Заготовку 2 устанавливают на опорный нож 4 между рабочим 1 и ведущим 3 кругами (см. рис. 228). Эти круги вращаются в одном направлении, но с разными скоростями. Трение между ведущим кругом и заготовкой больше, чем между ней и рабочим кругом. Вследствие этого заготовка увлекается во вращение со скоростью, близкой к окружной скорости ведущего круга. Ось детали устанавливается выше осей кругов на 0,1…0,3 диаметра детали. Скорость рабочего круга 30…35 м/мин, а ведущего – 15…20 м/мин. В результате различных скоростей вращения кругов сила трения между ведущим кругом и деталью значительно больше окружной силы резания, что обеспечивает вращательное движение детали. Для увеличения силы трения ведущий круг изготавливают на вулканитовой связке малой зернистостью и средней твердостью. Перед шлифованием ведущий круг устанавливают наклонно под углом = 1…7° к оси вращения заготовки. Вектор скорости этого круга разлагается на составляющие, в результате чего обеспечивается продольная подача Sпpод деталей за счет поворота и возникновения осевой составляющей окружной скорости ведущего круга. Угол = 1…7° влияет на производительность. Для чернового шлифования рекомендуют 4…7°, адля чистового– 1…3°.
Наиболее эффективен этот метод для изготовления крупных серий деталей в автоматическом режиме.
Методы отделочной абразивной обработки. На этапе отде-
лочной обработки обеспечиваются повышенные требования к шероховатости поверхности. При этом могут повышаться в небольшой степени точность размеров и формы обрабатываемых поверхностей. К методам отделочной обработки относятся хонингование, доводка, притирка, суперфиниширование, полирование ипр.
Хонингование деталей. Применяется для снижения шероховатости и повышения точности предварительно изготовленных отверстий. Может быть вертикальное и горизонтальное исполнение операций. В качестве инструмента применяются цилиндрические оправки – хоны с абразивными вставками (рис. 229). При вращении со скоростью Vx хон-головки совершают возвратнопоступательное движение Sx. Абразивные вставки имеют нагру-
397
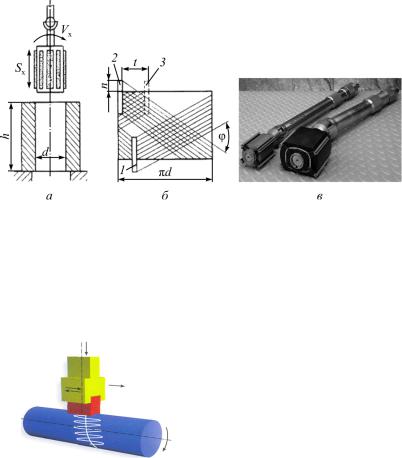
жающие пружины и плотно прижимаются к поверхности детали, снимая микростружки. Обработанная поверхность имеет сетчатый вид (рис. 229, б) с шагом t, числом сеток n и углом наклона φ.
Рис. 229. Общая схема процесса хонингования (а, б) и хон-головки (в) отверстия диаметром d и длиной h
При хонинговании обеспечивается шероховатость Ra = = 0,2…0,1 мкм. Обработка методом хонингования высокоточных отверстий деталей с отклонением геометрической формы не более 0,002 мм и шероховатостью поверхности по параметру Ra от
|
0,080 до 0,025 мкм сегодня |
|
проводится на многих предпри- |
|
ятиях авиационного, приборо- |
|
строительного и нефтегазового |
|
машиностроения. |
|
Суперфиниширование. При- |
|
меняется для снижения шерохо- |
Рис. 230. Общая схема процесса |
ватости предварительно обрабо- |
суперфиниширования |
танных цилиндрических поверх- |
|
ностей деталей (рис. 230). |
При вращении детали абразивный сегмент прижимается к наружной поверхности и совершает возвратно-поступательные движения. Суперфиниширование возможно выполнять после операций точения или шлифования. При этом шероховатость по-
398

верхности обеспечивается в пределах Ra = 0,1…0,32 мкм. Суперфиниширование – обработка различных поверхностей деталей, в том числе цилиндрических, абразивными брусками. В результате суперфиниширования шероховатость поверхности снижается до Ra = 0,1...0,012 мкм, увеличивается относительная опорная длина профиля поверхности с 20 до 90 %. Существенного изменения размеров и макрогеометрии поверхности не наблюдается. Обработка производится мелкозернистыми (зернистость не ниже 320) брусками с добавлением смазочного вещества (смесь керосина с маслом) при небольшой скорости (до 2,5 м/с) и с весьма малыми давлениями инструмента на поверхность детали (0,1...0,3 МПа – для заготовок деталей из стали; 0,1...0,2 МПа – для заготовок деталей из чугуна и 0,05...0,1 МПа – для заготовок деталей из цветных металлов). В простейших схемах обработки на различных станках общего назначения осуществляются следующие движения: вращение заготовки (окружная скорость 0,05...2,5 м/с); воз- вратно-поступательное движение (колебание инструмента или заготовки – ход 2...6 мм, число двойных ходов 200...1000 в 1 мин); перемещение инструмента вдоль поверхности заготовки. Толщина снимаемого слоя металла 0,005...0,02 мм.
Полирование. Полирование предна- |
|
значено для уменьшения параметров |
|
шероховатости поверхности без устра- |
|
нения отклонений размеров и формы |
|
деталей. При окончательном полирова- |
|
нии достигается (при малых давлениях |
|
резания 0,03...0,2 МПа) параметр шеро- |
|
ховатости Ra = 0,1...0,012 мкм. Абра- |
|
зивными инструментами являются эла- |
|
стичные круги (войлок, ткань, кожа |
Рис. 231. Полирование |
и т.п.), покрытые полировальными пас- |
|
тами (рис. 231), шлифовальные шкурки |
лопаток турбины |
и свободные абразивы (обработка мел- |
фетровыми накатными |
ких заготовок в барабанах и виброкон- |
кругами |
|
|
тейнерах). |
|
399
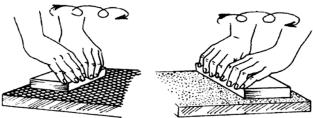
В качестве абразивных материалов применяют электрокорунд, карбиды кремния, бора, окись хрома, железа, алюминия, пасты ГОИ, алмазные и эльборовые шкурки и др. Более подробные характеристики, типы и области применения абразивных инструментов и шлифовальных материалов приведены в соответствующих справочниках
Притирка. Это обработка поверхностей деталей с помощью мелкозернистых шлифовальных порошков или паст, при которой снимается тончайший слой материала. Абразивная притирка является окончательным методом обработки заготовок деталей типа тел вращения, обеспечивающим малые отклонения размеров, отклонение формы обрабатываемых поверхностей и Rа = 0,16…0,01 мкм. Этот метод характеризуется одновременным протеканием механических, химическихифизико-химическихпроцессов.
Доводка – окончательная притирка, обеспечивающая высокую износо- и коррозиестойкость при изготовлении измерительных, поверочных инструментов и очень точных деталей. Для обработки материалов типа твердых сплавов, стекла, рубина, керамики применяют алмазосодержащие пасты с размерами зерна 40...1 мкм. Доводку выполняют с помощью ручных притиров (рис. 232) или на специальных доводочных станках.
аб
Рис. 232. Общий вид ручной притирки плоских поверхностей:
а– предварительная; б – окончательная
Вединичном производстве, при ремонте доводку производят на токарном станке притиром в виде втулки, сделанной по размеру притираемой детали, с одной стороны втулка разрезана. Втулку сма-
400