
книги / Резание материалов
..pdfзывают доводочной пастой или тонким слоем мелкого корундового порошка. Деталь при доводке смазывают жидким машинным маслом или керосином. Припуск на доводку составляет 5...20 мкм на диаметр. Скорость вращения заготовки V = 10….20 м/мин. В крупносерийном и массовом производстве процесс механизирован и часто называется процессом лаппингования. Притирка осуществляется между двумя чугунными (свинцовыми, медными) притирами. Диски вращаются в разные стороны. Детали закладываются в сепаратор, закрепленный на кривошипе. Финишная прецизионная обработка высокоточных плоских поверхностей деталей нефтегазового, приборостроительного машиностроения с требованиями по точности геометрической формы менее 1 мкм и высотным параметрам микрорельефа Ra 0,1…0,05 мкм. В основе растрового метода финишной обработки, разработанного для доводки плоскостей, лежит усложненная траектория рабочего движения инструмента (притира) с регулируемыми параметрами, наиболее простые из таких траекторий известны как фигуры Лиссажу. На основе комплексных исследований в ПНИПУ разработан и изготовлен плоскодоводочный станок «Растр220м» с жесткой кинематической связью между инструментом и деталью, для этого в нагружающем устройстве установлен синхронный привод с регулируемыми параметрами, сообщающий детали или кассете с деталями вращательное движение по заданному закону. Скорость резания устанавливается близко к максимальной и составляет 13…15 м/мин. При этом обеспечивается максимальная плотность сеткина поверхности.
5.5.3. Физическая сущность процесса шлифования, особенности образования поверхностного слоя
При шлифовании толщина среза измеряется сотыми и тысячными долями миллиметра. Процесс стружкообразования при снятии тонких стружек в значительной мере определяется отношением K = а/ , гдеа– толщина среза; – радиусокругления лезвия.
Чем больше K, тем в более благоприятных условиях протекает процесс стружкообразования и становится сходным с процессом стружкообразования при снятии толстых стружек.
401
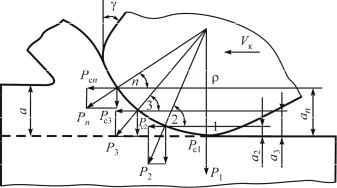
Процесс стружкообразования при обработке пластичных металлов со снятием тонких стружек представлен на рис. 233. На округленном участке лезвия действуют нормальные силы Р1, Р2, Р3, ..., Рn. Составляющие этих сил Рс1, Рс2, …, Рсп обеспечивают скалывание элементов стружки.
Рис. 233. Процесс стружкообразования при шлифовании
В точке 1 толщина среза а = 0, также сила Р1 = 0, а передний угол в этой точке 1 = 90°. С увеличением толщины среза при а1 < а2 < ... < аn уменьшается отрицательный передний угол 1 < 2 < < … < п и увеличиваются силы скалывания Рс1 < Рс2 < ...<Рсп. При малых значениях силы, вызывающей скалывание элемента стружки, т.е. при малой величине K срезания материала не произойдет. На этом участке слой материала, подлежащий удалению, будет сминаться, подвергаясь деформации. При этом возникают высокие удельные давления, измеряемые тысячами и десятками тысяч Н/мм2. Рассмотренную схему срезания тонкой стружки можно применять к процессу резания абразивным зерном. При шлифовании возникают мгновенные высокие температуры, вследствие чего обрабатываемый материал в зоне резания становится более пластичным. Это создает возможность срезания стружки округлым лезвием при довольно больших отрицательных передних углах, например при = –50°, где K = 0,5…0,6. При K = 1 процесс срезания стружки становится стабильным для всех условий.
402
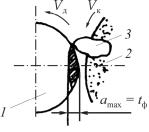
К примеру, электрокорунд зернистостью 16 имеет среднее значение = 13·10–3 мм; у синтетического алмаза зернистостью 12 = 2,2·10–3 мм; у естественного алмаза = 3,3·10–3 мм.
Таким образом, зерна алмаза являются более острыми, чем абразивные зерна. Это позволяет при использовании алмазного круга снимать более тонкие стружки.
Кроме того, чем острее лезвие, тем меньше нагрузка на зерно и ниже температура резания. Все это приводит к повышению точности и чистоты обрабатываемой поверхности.
Наибольшее влияние на про- |
|
цесс шлифования оказывает тол- |
|
щина среза, так как она в значи- |
|
тельной мере определяет удельную |
|
силовую нагрузку на абразивное |
|
зерно и износ круга. В связи с тем, |
|
что зерна в круге расположены |
|
хаотично, то, как бы близко они ни |
|
находились, работа двух соседних |
Рис. 234. Схема определения |
зерен происходит в разных плоско- |
|
стях. В этом случае стружка имеет |
максимальной толщины среза |
форму чечевицы (рис. 234). |
|
Максимальная толщина среза amax (мм) определяется по формуле
аmах = t ~ х ± у,
где t – глубина резания; х – величина упругого отжатия шлифовального шпинделя и обрабатываемой детали в сторону уменьшения толщины стружки; у – некоторая часть выступа (+) или впадины (–), оставшейся неснятой при предыдущем проходе.
Абразивные зерна выступают на поверхности круга на разную величину. Поэтому чем больше t, тем большее количество зерен участвуют в работе и большее число царапин возникают в единицу времени. С увеличением же числа царапин в единицу времени повышается чистота обработанной поверхности.
Большое влияние на процесс шлифования оказывает мгновенная температура в местах контакта абразивных зерен с обра-
403
батываемым материалом. При высоких температурах возможны изменения механических свойств и микроструктуры поверхностного слоя обрабатываемой детали, а также возникновение на отдельных участках обработанной поверхности напряжений, превосходящих предел прочности, что приводит к образованию трещин. В связи с этим необходимо стремиться, чтобы температура при шлифовании была минимальной.
Установлено, что самая большая температура концентрируется в тонком поверхностном слое. Снижение температуры шлифования достигается применением СОТС и выбором оптимальной характеристики шлифовального круга. При работе алмазным кругом мгновенная температура ниже, чем при шлифовании абразивным кругом. Это объясняется тем, что алмазное зерно острее абразивного, а поэтому, естественно, прилагаются меньшие усилия резания. Кроме того, алмаз обладает хорошей теплопроводностью, что способствует быстрому отводу тепла из зоны резания.
5.5.4. Силы резания при шлифовании
При шлифовании силы резания обычно небольшие, в среднем не более 300…400 Н, так как в процессе обработки снимается стружка малого сечения. Вместе с тем мощность при шлифовании, т.е. энергия, затрачиваемая на шлифование, может быть значительна ввиду большой скорости резания.
При шлифовании рассматривают отдельно силу резания при работе одним зерном и силу резания шлифовального круга в целом. Вследствие округления вершин абразивных зерен и срезания тонких стружек процесс шлифования осуществляется с большими углами резания, порядка 130…145°. Рассмотрим силы, действующие на абразивное зерно (рис. 235). Силу Р, действующую на поступательно перемещающееся зерно, разложим на две составляющие: силу Рz, действующую в направлении скорости резания, и силу Ру, прижимающую зерно к обрабатываемой поверхности. На переднюю поверхность зерна действуют элементарные нормальные силы и силы трения.
404

Элементарные силы заменим суммарными, приложенными в точке х, и тогда из условия равновесия сил имеем:
Рz = N(cos x – · sin x); Рy = N(sin x + · cos x),
где x – передний угол режущего элемента в точке х.
По уравнениям видно, что сила Ру > Рz. Произведение силы Р, действующей на одно
Рис. 235. Схема сил, действующих на абразивное зерно (Vк – скорость круга; а – толщина среза; S – подача; t – глубинарезания)
абразивное зерно, на количество зерен, одновременно участвующих в работе, равно суммарной силе резания R, действующей на шлифовальный круг. Эту силу, так же как и при продольном точении, разлагают на три составляющие силы: тангенциаль-
ную Рz, радиальную Ру и осевую Рх (рис. 236). Как правило, сила Ру больше силы Рz примерно в 1,5…3 раза. Сила Рх значительно меньше силы Рy.
Следует отметить, что при работе алмазными кругами силы резания меньше, чем при работе абразивнымикругами. Это объяс-
няется тем, что алмазные зерна более острые, а при использовании круга на бакелитовой связке последние обладают лучшей самозатачиваемостью. Удельные силы резания при шлифовании весьма велики и составляют 100…200 ГПа, тогда как при точении только 2…3 ГПа.
5.5.5.Износ и стойкость абразивного инструмента
Взависимости от условий шлифования круг может работать как в режиме затупления, так и в режиме самозатачивания. Под самозатачиванием понимается способность круга обновлять свою
405
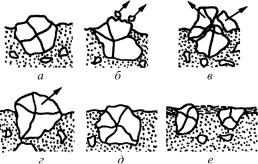
рабочую поверхность под влиянием сил резания. Если поры круга в процессе шлифования забиваются стружкой и частицами износа, то круг теряет свои режущие свойства еще до того, как его зерна затупятся, и пределом стойкости круга является процесс «засаливания» круга, т.е. забивание пор стружкой. Когда же круг не «засаливается», его стойкость лимитируется затуплением зерен. Самозатачивание круга наступает тогда, когда нагрузка и другие условия работы становятся такими, что зерна раскалываются, образуя новые острые выступы. В дальнейшем силы, действующие на зерно, увеличиваются и зерно удаляется.
В различных условиях обработки абразивный инструмент подвергается следующим видам износа:
истирание вершин режущих зерен с образованием площадок износа (рис. 237, а);
микроразрушение на мелкие частицы (рис. 237, б);
крупное разрушение зерен (рис. 237, в);
полное вырывание зерен из связки (рис. 237, г);
химическое разрушение зерна при высокой температуре
(рис. 237, д);
засаливание круга (забивание пор между зернами стружкой и частицами связки (рис. 237, е).
Рис. 237. Основные виды износа шлифовального круга
Одновременно изнашивается и связка круга. При работе изношенным кругом возрастают усилие и температура резания, появляются вибрации, чтоухудшает качество обработаннойповерхности.
406
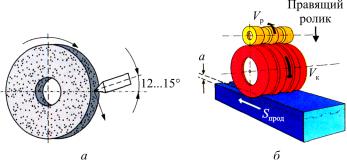
Правка кругов. Для исправления геометрической формы круга и восстановления его режущей способности применяют правку, чаще всего алмазным инструментом (карандаши, ролики и т.д.). При правках удаляется более 60…70 % рабочего объема круга. Схемы правкиалмазнымикарандашамиизображенынарис. 238.
Рис. 238. Схемы правки шлифовальных кругов алмазным карандашом (а) и профильным алмазным роликом при профильном шлифовании (б)
При правке алмазным карандашом (алмазное зерно 0,2…0,25 карата, закрепленное в оправе, или несколько мелких алмазных зерен, закрепленных связкой) для повышения стойкости необходимо располагать карандаш под углом 12…15°, периодически поворачивая его по мере образования площадки износа.
Стойкость шлифовального круга. Время работы абразивного инструмента между двумя правками характеризует его стойкость. В зависимости от точности, чистоты обработанной поверхности и режима резания стойкость кругов колеблется от 300 до 2400 с. С увеличением диаметра круга стойкость круга повышается, так как уменьшается нагрузка и толщина среза одним зерном
иуменьшается износ самих зерен.
5.5.6.Назначение режимов резания при шлифовании
Порядок назначения режимов шлифования следующий:
1. Выбирают характеристику шлифовального круга в зависимости от данных условий шлифования.
407
2.Находят глубину резания (поперечную подачу).
3.Определяют скорость вращения обрабатываемой детали
сучетом твердости обрабатываемого материала, точности обработки, твердости шлифовального круга и т.д.
4.Подсчитанное число оборотов детали корректируют по станку и затемопределяютдействительнуюскоростьвращения детали.
5.Определяют продольную и минутную подачи.
6.Выбирают скорость вращения шлифовального круга (скорость резания) с учетом жесткости станка и прочности шлифовального круга. По выбранной скорости определяют число оборотов шпинделя и корректируют по станку.
7.Определяют силу Рz и мощность, необходимую для шлифования. Шлифовальные круги перед установкой на станок должны быть отбалансированы и испытаны на прочность при окружной скорости, в 1,5 раза превышающей рабочую скорость.
8.Определяют машинное время. При круглом наружном шлифовании расчет ведут по формуле
t0 |
l |
|
h |
Kз, |
nd Sпp |
|
|||
|
|
Sпоп |
где l – длина шлифования, мм; h – припуск, мм; Sпоп – поперечная подача, мм; Sпр – продольная подача, мм; Kз – коэффициент зачистных ходов, равный 1,2…1,7 в зависимости от требуемой шероховатости.
5.5.7.Техника безопасности при работе на шлифовальных станках
Шлифовальные круги перед установкой на станок должны быть в инструментальном цехе отбалансированы и испытаны на прочность при окружной скорости, в 1,5 раза превышающей рабочую скорость, указанную на круге. Контроль качества кругов проводится шлифовщиком перед установкой на станок по звуку ударным методом (рис. 239, а). Звук должен быть ясным и звонким. Глухой звук свидетельствует о дефектах в круге. После установки круга на станок проводится вращение круга в течение
408
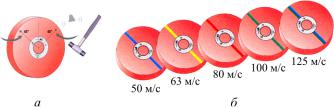
5…10 мин на холостом режиме. Скорость круга не должна превышать замаркированную скорость изготовителем кругов. Иначе круг может разорваться на мелкие части и вылетая с большой скоростью травмировать рабочего.
Рис. 239. Контроль кругов на трещины ударным методом (а)
иобозначение скоростных кругов цветными лентами (б) (50 м/с – голубой, 63 м/с – желтый, 80 м/с – красный, 100 м/с – зеленый, 125 м/с – зеленый/голубой)
Для применения повышенных скоростей шлифования применяют специальные скоростные круги. Скоростные круги имеют специальное обозначение в виде цветной ленточки на торце круга (рис. 239, б).
Контрольные вопросы и задания
1.Что такоеповерхностный слой, возникающий прирезании?
2.Перечислите основные параметры, определяющие качество поверхностного слоя.
3.Как параметры качества поверхностного слоя зависят от условий обработки?
4.Как качество поверхностного слоя влияет на эксплуатационные свойства деталей?
5.Перечислите особенности образования поверхности при чистовой лезвийной и абразивной обработке.
6.Что такое абразивный инструмент? Перечислите характеристики абразивного инструмента.
7.Какие виды шлифования вам известны?
8.Какова физическая сущность процесса шлифования?
9.Каковы характерные особенности износа абразивного инструмента?
409
Глава 6 ОПТИМИЗАЦИЯ ПРОЦЕССА РЕЗАНИЯ
6.1. Понятие об обрабатываемости материалов резанием
Способность материалов поддаваться резанию принято называть обрабатываемостью. Понятие «обрабатываемость» охватывает совокупность нескольких технологических свойств материала, характеризующих его влияние на различные стороны процесса резания. В машиностроении используются различные материалы, легко и трудно обрабатываемые резанием. Углеродистые, конструкционные, легированные, нержавеющие, закаленные стали, чугуны, цветные сплавы, жаропрочные стали и сплавы, титановые и тугоплавкие сплавы и др. Основные показатели обрабатываемости – производительность, качество и себестоимость.
6.1.1. Основные параметры обрабатываемости
На рис. 240 приведены основные параметры, характеризующие обрабатываемость металлов. Наиболее значимые из них следующие:
1. Скорость резания, с которой наиболее рационально обрабатывается металл: скорость резания VT, соответствующая заданному периоду стойкости Т при износе инструмента до принятого критерия затупления hз. Например, V60, V120 или Vhз = 0,4, оптимальная скорость резания Vо, при которой наблюдается наименьшая интенсивность изнашивания инструмента и наименьший относительный поверхностный износ hо.п, экономическая скорость резания Vэ, при которой достигается наименьшая себестоимость обработки условной детали при заданной стоимости станкоминуты, времени на смену затупившегося инструмента и стоимости его эксплуатации за период стойкости.
410