
книги / Резание материалов
..pdfне превышающих 900 °С. При более высоких температурах окислительные и защитные свойства газовых сред весьма мало влияет на интенсивность изнашивания.
|
|
Таблица 1 8 |
Влияние различных сред на стойкость инструмента |
||
|
|
|
Среда |
Стойкость, мин |
Повышение или понижение |
Воздух |
11 |
– |
Азот |
45 |
Повышение в 4 раза |
Кислород |
2 |
Снижение в 5,5 раза |
Аргон |
17 |
Повышение в 1,5 раза |
Углекислый газ |
6 |
Снижение в 2 раза |
Согласно гипотезе, при температурах резания 700…800 °С кислород воздуха вступает в химическую реакцию с кобальтовой фазой твердого сплава и карбидами вольфрама и титана, причем наиболее сильно окисляется кобальт. Вследствие значительной пористости металлокерамических твердых сплавов окислительным процессам подвергаются не только сами контактные поверхности инструмента, но и зерна твердого сплава, лежащие на некоторой глубине от этих поверхностей. Продуктами окисления кобальтовой фазы являются окислы Со3О4 и СоО и карбидов WO3 и TiO2. Твердость продуктов окисления в 40…60 раз ниже твердости твердых сплавов. В результате значительного размягчения кобальтовой фазы нарушается монолитность сплава и ослабляются связи между зернами карбидов вольфрама и титана и цементирующей связкой. Это создает благоприятные условия для выравнивания карбидных зерен силами трения, действующими на передней и задней поверхностях инструмента, и изнашивания этих поверхностей.
Склонность твердых сплавов к окислению определяется их химическим составом. Однокарбидные сплавы окисляются сильнее, нежели двухкарбидные. С увеличением содержания кобальта в твердом сплаве интенсивность и скорость окисления возрастают. Развитию коррозионных явлений в значительной степени препятствует применение при резании инертных газовых сред.
281
Применение аргона, гелия, азота существенно уменьшает интенсивность изнашивания инструмента. Наиболее сильными защитными свойствами обладает гелий, затем аргон и азот. Однако, как показали опыты, влияние газовой среды заметно только при температурах резания, не превышающих 900 °С. При более высоких температурах окислительные и защитные свойства газовых сред весьма мало влияют на интенсивность изнашивания, что свидетельствует о том, что в суммарном механизме изнашивания инструмента окислительные процессы имеют существенное значение только в интервале температур 700…900 °С.
Оценивая достоверность различных гипотез изнашивания инструментов, следует отметить, что только абразивное и адгезионное изнашивание получило экспериментальное подтверждение. Прямых экспериментальных доказательств, подтверждающих существование диффузионного и окислительного изнашивания, нет.
Хрупкий износ. Хрупкому износу подвергаются твердосплавные инструменты, алмазы, минералокерамика, керметы. Вследствие неравномерного строения, твердости, зернистости, вследствие вибраций в процессе резания часто происходит выкрашивание, осыпание лезвия. Хрупкому износу может способствовать истирание связки. Хрупкий износ проявляется главным образом в зоне низких скоростей резания.
В результате анализа всех видов разрушения и износа режущих инструментов можно представить обобщенную схему износа
(рис. 156).
На рис. 159 обозначены следующие виды износа и разрушения режущей пластины токарного резца: 1 – износ по задней поверхности; 2 – кратерный износ (B – B) по передней поверхности; 3 – выработка (износ) под действием торца стружки; 4 – мaксимальный износ на задней поверхности; 5 – окислительный износ; 6 – пластическая деформация вершины резца (C); 7 – нарост на режущей кромке (A – A); 8 – трещины на кромке поперечные; 9 – трещины продольные; 10 – выкрашивание режущей кромки; 11 – разрушение режущей кромки.
282
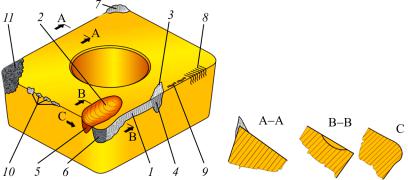
Рис. 156. Виды разрушения и износа режущей пластины
Взависимости от условий резания степень износа резца различается. Например, при точении без СОЖ детали из стали 45 резцом из твердого сплава Т15К6 в диапазоне скоростей резания 50…210 м/мин при подаче 0,08 мм/об доля износа задней поверхности составляет 60…80 %, а доля износа передней поверхности – 10…15 % в общем износе резца. С увеличением подачи до 0,46 мм/об доля износа передней поверхности увеличивается до 60…90 %, а задней поверхности – уменьшается до 5…7 %. При подаче 0,24 мм/об и диапазоне скоростей резания 80…150 м/мин доли износапередней изаднейповерхностей приблизительноодинаковы.
Взаключение можно отметить, что в действительности мы наблюдаем суммарный износ инструмента и разграничить доли каждого износа довольно трудно. Измерение износа проводится по передней и задней граням с помощью измерительных луп
иинструментальных микроскопов.
4.3. Понятие о стойкости режущих инструментов
4.3.1. График износа за время работы инструмента
Изображение закономерности нарастания износа за время работы инструмента называют кривой или графиком износа. Характерные кривые износа задней поверхности инструмента представлены на рис. 157.
283

а |
б |
в |
г
Рис. 157. Кривые износа инструмента: по передней поверхности (а, б); только по задней поверхности (в); классический вид кривой износа (г)
Если инструмент изнашивается одновременно по передней и задней поверхностям, то классическая кривая износа задней поверхности (рис. 157, а, г) состоит из трех более или менее отчетливо выраженных участков. Участок кривой износа ОА соответствует периоду приработки инструмента – l1. На этом участке происходит интенсивное нарастание износа hз. При дальнейшей работе инструмента нарастание износа замедляется, так как это связано с уменьшением контактных касательных напряжений на площадке износа по мере увеличения ее размеров. Участок кривой АВ – участок, соответствующий периоду нормального изнашивания инструмента, – l2. По достижении некоторой величины В износ начинает резко расти и кривая износа идет круто вверх. Участок кривой за точкой В соответствует периоду катастрофического износа инструмента – l3. В этом периоде износ нарастает
284
настолько быстро, что если не прекратить дальнейшую работу, то это может привести к чрезмерно большому износу задней поверхности, при котором резко сократится число переточек, допускаемых инструментом, и увеличится время, затрачиваемое на переточку. Поэтому рациональная эксплуатация инструмента исключает работу в периоде катастрофического изнашивания. По мере износа инструмента в ряде случаев наблюдается рост температуры в зоне резания. При обработке фасонным инструментом по мере износа может теряться профиль.
При средних значениях скоростей резания период нормального изнашивания составляет 85…90 % периода стойкости инструмента. По мере увеличения скорости резания период нормального изнашивания сокращается и при очень высоких скоростях резания становится настолько малым, что после периода приработки почти сразу наступает период катастрофического изнашивания. Геометрические параметры инструмента должны быть такими, чтобы максимально увеличить период нормального изнашивания и сократить или полностью устранить период приработки.
При изнашивании инструмента преимущественно по задней поверхности, когда износ передней поверхности незначителен, кривая износа (см. рис. 157, б) вогнута относительно оси абсцисс. В этом случае период приработки отсутствует и на участке АВ кривой износа, соответствующем периоду нормального изнашивания, износ вначале медленно, а затем более быстро возрастает до точки В – начала периода катастрофического изнашивания.
Если инструмент изнашивается только по задней поверхности, то кривая износа имеет вид, изображенный на рис. 157, в. После периода приработки период нормального изнашивания продолжается значительно дольше, чем в первых двух случаях. Период нормального изнашивания в последнем случае настолько велик, что, как правило, работу инструмента прекращают еще до перехода в период катастрофического изнашивания.
На рис. 158, а изображена схема износа передней поверхности инструмента. Образовавшаяся на передней поверхности лунка износа характеризуется шириной lл, длиной bл и глубиной hл.
285
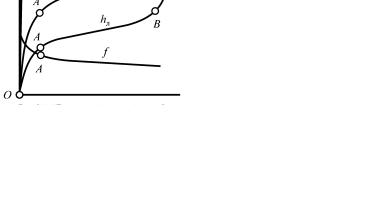
По мере работы инструмента первые следы износа появляются в точке, соответствующей максимальной температуре передней поверхности. Ширина и глубина лунки постепенно увеличиваются, а радиус кривизны кривой, очерчивающей дно лунки, уменьшается. Одновременно сокращается перемычка f от края лунки до главного лезвия. Центр кривизны лунки по мере изнашивания передней поверхности отодвигается от главного лезвия, а поэтому по ширине лунка от главного лезвия удаляется значительно быстрее, чем приближается к нему. Перемычка f между главным лезвием и краем лунки имеется только в том случае, когда на передней поверхности образуется хорошо развитый и устойчивый нарост, отодвигающий стружку от главного лезвия инструмента. Когда нароста нет или он настолько мал, что не может оказать защитного действия по отношению к инструменту, то перемычка отсутствует и лунка полностью не формируется.
а |
|
б |
|
Рис. 158. Схема износа передней поверхности (а) и изменения размеров лунки во времени (б)
Изменение размеров лунки по мере изнашивания передней поверхности изображено на рис. 158, б. Длина bл лунки, равная рабочей длине главного лезвия, за все время работы инструмента остается одинаковой. Глубина hл лунки вначале возрастает быст-
286
ро, затем ее рост замедляется и только после определенного периода работы инструмента вновь интенсивно возрастает. Таким образом, на кривой, характеризующей рост глубины лунки, наблюдаются периоды приработки, нормального и катастрофического изнашивания. Ширина lл лунки, как и ее глубина, вначале возрастает быстро, а затем ее рост замедляется. Перемычка f, если она имеется, интенсивно уменьшается при быстром росте ширины лунки. Когда же темп роста ширины лунки замедляется, то замедляется и уменьшение перемычки.
Величина износа передней и задней поверхностей инструмента (ширина площадки износа и глубина лунки) зависит от времени работы инструмента, температуры резания и скоростей перемещения поверхности резания и стружки относительно задней и передней поверхностей. В результате обработки опытных данных, полученных при изучении влияния времени работы инструмента, глубины резания, подачи и скорости резания на ширину площадки износа и глубину лунки износа, были составлены эмпирические формулы, описывающие связь между величиной износа h и факторамирежима резаниядля периода Тнормального изнашивания инструмента.
Интенсивность влияния параметров режима резания на величину износа задней поверхности такая же, как и на температуру резания. Параметры режима, которые оказывают большее влияние на температуру резания, также сильнее влияют и на износ задней поверхности инструмента, и наоборот. Последнее подтверждает, что величина линейного износа инструмента пропорциональна температуре резания.
При нарастании износа может происходить изменение шероховатости обрабатываемой поверхности в ту или иную сторону.
С изменением износа меняются и качественные показатели поверхностного слоя (наклеп, остаточные поверхностные напряжения и шероховатость поверхности).
4.3.2. Период стойкости инструмента
Период стойкости Т (мин) – это время непосредственного резания заготовки инструментом между двумя переточками или
287
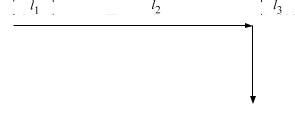
сменой режущих кромок. Суммарный период стойкости Тсум (мин) с достаточной точностью определяют следующим образом:
Тсум i · Т,
где i – число переточек, допускаемых инструментом до его полной амортизации.
Таким образом, суммарный период стойкости численно характеризует срок службы инструмента до того, как он будет направлен в утилизацию. Связь между суммарным периодом стойкости и периодом стойкости инструмента немонотонна. С увеличением периода стойкости Тсум растет. Однако при этом возрастает и ширина площадки износа задней поверхности, что сокращает допускаемое число i переточек инструмента. Последнее же уменьшает суммарный период стойкости. Поэтому вначале при увеличении периода стойкости Тсум также возрастает, достигая максимума при некотором значении Т, а следовательно, и износа h. Дальнейшее увеличение Т (и износаh) уменьшает суммарныйпериод стойкости.
Период стойкости режущих инструментов назначается экспериментально по предельно допустимой величине износа hз.доп (рис. 159), количеству обработанных деталей требуемого качества или по требуемой производительности. Допустимая максимальная величина линейного износа hз задней поверхности при обработке: стали – 0,8…1 мм; чугуна с подачей 0,3 мм/об. – 1,4…1,7 мм. На графике износа допустимая величина износа hз.доп определяется исходя из условия недопущения катастрофического износа (т. В) или поломки инструмента.
hз.доп
Т
Рис. 159. Определение периода стойкости Т по предельно допустимому износу hз.доп
288
4.3.3. Критерии износа-затупления инструмента
Момент затупления инструмента устанавливают с помощью критерия износа. Под критерием износа понимают сумму признаков (или один решающий признак), при которых работа инструментом должна быть прекращена. Используют несколько кри-
териев: критерий оптимального износа, критерий технологического износа и критерий блестящей полоски. В двух первых критериях за основу принимают линейный износ задней поверхности, так как задняя поверхность инструмента изнашивается всегда, при обработке любых материалов и при любых режимах резания, и измерение ширины площадки износа значительно проще, чем глубины лунки износа.
Критерий оптимального износа. Инструмент считают зату-
пившимся, когда линейный износ задней поверхности достигает значения, равного оптимальному износу. Под оптимальным износом понимают такой, при котором суммарный период стойкости инструмента достигает максимальной величины.
Критерий оптимального износа широко применяют в лабораторных условиях при установлении стойкостных зависимостей для инструментов, предназначенных для черновой и получистовой обработки. Применение критерия в производственных условиях целесообразно при массовом производстве и при эксплуатации дорогостоящего инструмента.
При эксплуатации инструмента по мере его изнашивания наступает такой момент, когда дальнейшее резание инструментом должно быть прекращено, а инструмент отправлен на переточку. Например, при протягивании жаропрочных сплавов наблюдается повышенный износ протяжек в виде выкрашивания (рис. 160), при котором протяжку нужно отправить в переточку. Причиной выкрашивания в данном случае является адгезионное приваривание стружки после окончания процесса резания к передней поверхности зуба протяжки. При удалении стружки удаляется часть режущей кромки.
Появление выкрашиваний на режущих зубьях протяжек приводит к резкому увеличению нагрузки на последующих зубьях
289
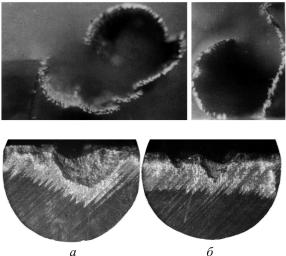
и их разрушению. Постепенно происходит лавинообразное разрушение всех последующих режущих и чистовых зубьев протяжек, что вызывает значительное ухудшение шероховатости и точности протягиваемых поверхностей деталей.
Рис. 160. Типичный характер сцепления стружки с зубом протяжки (а), выкрашивания и разрушения режущих кромок твердосплавных протяжек при удалении стружки (б)
Наиболее крупные выкрашивания протяжек обнаружены при низких скоростях резания. С увеличением скорости резания до оптимальных значений уровень выкрашиваний снижается, а при дальнейшем увеличении вновь увеличивается.
Когда износ передней поверхности имеет превалирующее значение, то критерием затупления будут размеры лунки. Однако если ориентироваться на какой-либо один линейный размер лунки, то при одном и том же абсолютном износе степень изношенности передней поверхности падает с увеличением подачи. Поэтому целесообразно ввести понятие относительного износа передней поверхности, выражаемое отношением
290