
книги / Резание материалов
..pdfK |
|
hл |
, |
b |
|
||
|
f |
||
|
2 |
|
|
где hл – глубина лунки; b2 f – расстояние до центра лунки от
режущей кромки; b – ширина лунки.
Допустимый относительный износ передней поверхности связан с прочностью фактического режущего клина, поэтому зависит от инструментального материала. Для твердосплавных резцов допустимый износ hл = 0,3…0,4 мм; для быстрорежущих hл = 0,1…0,2 мм.
Допустимая величина износа по задней поверхности hз может быть достигнута при превалирующем износе по задней поверхности. При этом различают оптимальный hз.опт и технологический hз.техн критерии затупления. При hз.опт обеспечивается максимальная суммарная стойкость или долговечность инструмента
Д = кТ,
где к – общее количество возможных переточек инструмента,
к = 2/3 b1/y = 2b1/3(hr/cos + ), где b1 – длина пластины;
у = р + – укорочение пластины за период стойкости Т; р – величина износа за период стойкости; р = hr/cos ; – дополнительный слой, снимаемый при переточке ( = 0,1…0,15 мм).
Износ (hз.опт), при котором наблюдается максимум долговеч-
ности, называется оптимальным критерием затупления.
Это соответствует концу участка нормального износа инструмента т. В (см. рис. 159). Оптимальный критерий затупления hз.опт = = f(а, β) зависит от cечения среза, вида обрабатываемого металла и материалаинструмента, геометриирежущей части, СОТС идр.
Критерий затупления hз.опт используется в том случае, когда на процесс резания не налагаются дополнительные требования (по шероховатости, точности и т.д.), т.е. в условиях черновой обработки деталей. Для твердосплавных резцов при черновой обработке сталей величина допустимого износа задней поверхности
291
принимается в пределах hз.опт = 0,8...1 мм, а при обработке чугу-
нов hз.опт = 0,8...1,7 мм.
Применение критерия оптимального износа, обеспечивающего максимальный суммарный срок службы инструмента, возможно не всегда. Им нельзя пользоваться в случае, когда на кривой износа нет участка катастрофического износа. Отсутствие точки перегиба не позволяет провести касательную к кривой износа и определить величину hопт. Если по каким-либо причинам износ инструмента нельзя доводить до величины hопт, то применение критерия оптимального износа также невозможно. В этих случаях используют критерий технологического износа.
Критерий технологического износа. Под технологическим износом понимают такой износ, при котором перестают удовлетворяться технологические требования, предъявленные к детали (изделию): точность, шероховатость, наклеп и т.д. Технологический критерий затупления используют в основном при чистовой (окончательной) обработке.
Инструмент считают затупившимся, когда линейный износ задней поверхности достигает значения, равного технологическому износу.
Под технологическим износом понимают такой, при котором работу инструмента прекращают по технологическим ограничениям: резкое увеличение шероховатости обработанной поверхности, вызываемое изнашиванием инструмента; потеря инструментом необходимого размера; возникновение вибраций в технологической системе; чрезмерный нагрев детали; поломка малопрочного инструмента и т.п. Критерий технологического износа в основном используют при исследовании и эксплуатации инструмента, предназначенного для чистовой (окончательной) обработки.
Критерий блестящей полоски. Процесс резания прекраща-
ется, когда на поверхности резания появляется блестящая полоска – след от изношенной режущей кромки резца (рис. 161). Требуется большое внимание токаря. Обработка идет без СОЖ.
Кроме того, критериями износа могут быть предельные значения шума резания, вибрации, мощности, силы и температуры резания. Для оценки износа в процессе резания на станках с ЧПУ сего-
292
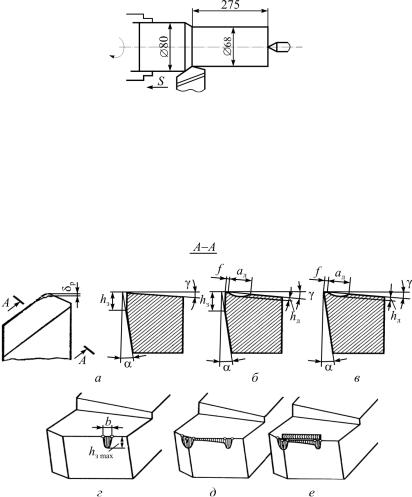
дня применяют систему диагностики и адаптивного управления режимами резания, позволяющей в автоматическом режиме изменять скорость резания, подачу и глубину резания или прекращать процесс резания при превышении допустимой величины износа.
Рис. 161. Появление блестящей полоски на поверхности резания при износе резца
Методы измерения износа.
Визуальное наблюдение с лупой Бринеля. Визуально наблю-
даемые признаки износа режущих инструментов с помощью увеличительной 5–7-кратной лупы Бринеля показаны на рис. 162.
Рис. 162. Измерение визуально наблюдаемых видов износа резцов по передней и задней поверхности с помощью увеличительной лупы Бринеля
293
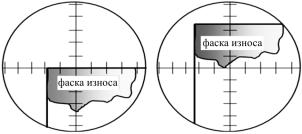
Радиальный износ и фаска износа на задней поверхности показаны на рис. 162, а; фаска износа на задней поверхности и лунка на передней поверхности – на рис. 162, б; лунка износа на передней поверхности – на рис. 162, в; проточина на задней поверхности – на рис. 162, г; комбинированный износ по задней поверхности – на рис. 162, д; все признаки износа отмечены одновременно – на рис. 162, е.
Допустимая величина линейного износа h задней поверхности при обработке: стали – 0,8…1 мм; чугуна с подачей
0,3 мм/об – 1,4…1,7 мм.
Измерение износа с помощью инструментального микроско-
па ММИ-2. Для измерения износа резца по главной задней поверхности используется микроскоп ММИ-2. В поле зрения микроскопа (рис. 163) видны две сплошные взаимно перпендикулярные риски со шкалой.
Рис. 163. Поле зрения микроскопа при измерении износа резца по задней поверхности – цена деления 0,1 мм
(износ hз = 0,35 мм)
Вращая микрометрические винты стола микроскопа, совмещаем одну из взаимно перпендикулярных рисок окуляра с главной режущей кромкой и считываем показания на барабане микрометрического винта. Сдвигаем шкалу на максимальное значение износа и снова считываем показания барабана. Разница этих показаний даст величину, соответствующую ширине фаски износа по задней поверхности.
294
Метод фотографирования степени износа по числу проходов. Через определенное число проходов резание прекращают и фотографируют износ, затем сравнивают увеличение износа по числу проходов и вычисляют интенсивность износа.
4.3.4. Зависимость скорость резания – стойкость инструмента
Скорость резания является одним из основных параметров, определяющих производительность обработки. С увеличением скорости резания возрастает производительность, но быстрее изнашивается инструмент.
Затраты времени на частые смены инструмента, частые его переточки и связанные с этим расходы могут свести на нет преимущества, полученные от применения высокой скорости резания. Поэтому для каждого отдельного случая надо выбирать допустимую скорость резания, при которой обеспечивается наибольшая производительность и наименьшая себестоимость обработки.
Скорость резания зависит от целого ряда факторов. Основные из них следующие: стойкость инструмента, глубина резания и подача, геометрия инструмента, свойства обрабатываемого и инструментального материалов, СОТС и др.
Под стойкостью (или периодом стойкости) инструмента Т понимают время его работы между переточками (в мин). Суммарная стойкость инструмента – произведение стойкости на количество переточек.
Размерная стойкость инструмента – время работы инструмента,
втечение которого обеспечиваются заданные размеры и шероховатость обрабатываемой детали. При этом за критерий затупления
принимают радиальный износ hr, так как радиальный износ инструмента непосредственно влияет на точность и шероховатость обработанной поверхности. Температура (скорость резания), при которой наблюдается наименьшая интенсивность износа инструмента, называется оптимальной температурой(скоростью) резания.
При резании на скоростях (температурах) резания ниже оптимальных происходит рост интенсивности износа инструмента
врезультате следующих причин (физических):
295
уменьшения отношения твердости Ни/Нм, а следовательно, усиления явлений адгезии;
повышения коэффициентов трения на передней и задней поверхностях инструмента;
повышения объема пластической деформации; оно выражается в повышении усадки стружки, повышении микротвердости стружки и обработанной поверхности, увеличении удельной работы стружкообразования. Это объясняется увеличением механического и адгезионного износа;
улучшения условий при работе на низких скоростях реза-
ния для абразивного действия карбидов и |
других |
включений |
в обрабатываемый материал, которые при |
низких |
скоростях |
сильнее удерживаются и чувствительнее царапают инструмент.
4.3.5. Характеристики размерной стойкости инструмента
Стойкость режущих инструментов может выражаться в длине пути резания, времени резания или в количестве обработанных деталей до допустимого износа инструмента. Размерная стойкость инструмента имеет важное значение для анализа вопросов, связанных с работой инструмента в автоматизированном производстве. Размерную стойкость инструмента зачастую характеризуют временем его работы Т, в течение которого текущее, среднее значение размера обрабатываемых деталей располагается в пределах части поля допуска, выделенной на переменные систематические погрешности размера, связанные с износом режущих кромок.
Иногда размерную стойкость инструмента характеризуют количеством деталей N, изготовленных в пределах допуска без вмешательства оператора для регулирования или замены инструмента.
Одним из основных факторов, определяющих период стойкости инструмента, является скорость резания. Чтобы получить график зависимости Т = f(V), проводят для различных скоростей резания эксперименты по изнашиванию инструмента до допустимых пределов. Размерную стойкость можно также характеризовать длиной пути резания l или площадью обработанной по-
296

верхности деталей до регулирования или замены инструмента (рис. 164). На графиках износа можно увидеть, например, что для допустимого износа hз = 0,25 мм длина пути резания для трех скоростей резания будет различной. Наибольшая стойкость инструмента будет при скорости V3 и составит 57 м пути резания. А для скорости V1 путь резания составит всего 13 м.
Рис. 164. Зависимость износа hз от длины пути резания l:
V1; V2; V3
Одной из характеристик размерной стойкости инструмента может служить линейный относительный износ (hо.з, мкм/м), т.е.
укорочение инструмента в радиальном направлении, отнесенное на 1000 м пути резания:
hо.з hi 1 hi ,
li 1 li
где hi+1 – hi – линейное приращение износа по задней грани на
(i + 1)-м режиме, мкм; li+1 – li – путь резания на (i + 1)-м режиме, м. Размерную стойкость инструмента может характеризовать
и скорость размерного износа Vн. Под скоростью размерного износа понимается скорость укорочения инструмента в радиальном направлении в периоде нормального износа, стойкости при принятом критерии затупления.
Все отмеченные характеристики размерной стойкости являются частными и в общем случае оказываются непригодными для проведения анализа вопросов, связанных с проблемой размерной
297
стойкости инструмента, так как первая характеристика Т (время работы без подналадки или замены инструмента) имеет ограничения со стороны скорости резания V, подачи S, величины износа инструмента hз или hr; вторая характеристика N – количество обработанных деталей без подналадки инструмента размера обрабатываемой детали и износа (hз или hr); третья – l – ограничения со стороны подачи S, величины износа hз или hr; четвертая – П (площадь обработанной поверхности) – со стороны величины износа hз или hr; пятая – hо.л – со стороны подачи; шестая – Vh (скорость размерного износа) – со стороны скорости резания V и подачи S; наконец, последние две характеристики – поверхностный относительный износ hо.п и удельная размерная стойкость Туд. Поверхностный относительный износ – это радиальный износ инструмента, отнесенный к 1000 см2 обработанной поверхности. Удельная размерная стойкость инструмента Туд – площадь поверхности, которую способен обрабатывать инструмент при затуплении в радиальном направлении на 1 мкм. Последние две характеристики являются универсальными, так как на них не накладываются ограничения ни со стороны скорости резания, ни со стороны подачи, критерия затупления и т.д.
В связи с этим поверхностный относительный износ и удельная размерная стойкость могут быть использованы для сравнительной оценки размерной стойкости выбираемых режущих инструментов, для анализа точности и экономичности вариантов технологических процессов и режимов резания, а также для конструирования систем автоматическогоуправления технологическимисистемами.
4.3.6. Влияние скорости (температуры) резания на характеристики размерной стойкости. Зависимость стойкость–скорость (Т–V)
Экспериментально установлено, что при изменении скорости резания в широком диапазоне для различных процессов резания при обработке деталей из различных материалов инструментами из быстрорежущих сталей зависимость Т = f (V) носит монотонно убывающий характер, а для твердых сплавов имеет экстремальный вид (рис. 165).
298

Тм
Vм
Рис. 165. Зависимость стойкость–скорость
Зависимость длины пути резания от скорости l = f(V) также носит экстремальный характер (l = V · Т).
Максимум размерной стойкости инструмента Тм и общей стойкости наблюдается при разных скоростях резания, а следовательно, и температурах в зоне резания. Для определения оптимальной скорости резания Vо, соответствующей максимуму пути резания, надо первую производную пути по скорости резания приравнять к нулю:
l = ТV = f(V);
(l)V = T + (Т)V V = 0,
откуда
V = Vо = – T/ (Т)V' .
Поскольку Vо и Т являются положительными величинами, то равенство может наблюдаться при отрицательном значении (Т)V' ,
что возможно лишь для ниспадающей ветви кривой. Следовательно, оптимальная скорость резания соответствует правой ниспадающей ветви кривой T = f(V). Поэтому всегда справедливо не-
299
равенство Vм < Vо, где Vм – скорость резания, соответствующая максимуму периода стойкости инструмента Тм.
Даже в тех случаях, когда период стойкости Тм, наблюдаемый при Vм, выше периода стойкости То, наблюдаемого при более высокой оптимальной скорости резания Vо, работа на скорости Vм по сравнению со скоростью Vо является нерациональной, так как это привело бы к снижению производительности обработки, размерной стойкости инструмента и ухудшению качества обрабатываемой поверхности.
Оптимальные скорости резания могут быть выявлены на основе обычных испытаний по кривым Т = f(V), при исследовании интенсивности размерного износа инструмента по кривым hо.л = f(V) и hо.п = f(V). Главным фактором, обусловливающим экстремальный характер зависимостей l = f(V) и hо.п = f(V), является рост температуры контактных поверхностей и изменение характера износа.
Построив зависимости Т–V в двойной логарифмической сетке координат, можно определить величину оптимальной скорости резания путем проведения касательной к кривой Т–V, проходящей под углом 45° к осям Т и V. Касательную ОK можно назвать линией постоянной размерной стойкости, так как для любой ее точки l = соnst l (l = VТ). Зависимость Т = f(V) для правой ветви может быть выражена формулой
T = CT /Vm или V = CV/Tm,
где CT и СV – постоянные величины для данных условий резания, зависящие от обрабатываемого и инструментального материалов, t, S и прочих условий; Т – стойкость инструмента, мин; m – показатель относительной стойкости, m = a/b = tg .
При = 45° m = 1, т.е. Vо = C/T , а С = V – Т при lmax.
Для любой точки линии MN lm = Vм Tм (см. рис. 165). Если MN ближе к оси ординат, то Vм и Tм меньше. Несмотря на то, что Тм >То, lo > lм. Поэтому Vо – это тот предел, до которого можно снижать скорость резания в целях повышения точности и производительности обработки.
300