
3875
.pdfрасполагается непосредственно под нижней плитой. Пространство для ее размещения образовано двумя башмаками, привинченными к плите снизу. Основным недостатком такой конструкции является малый ход выталкивания, ограничивающий длину штампуемых деталей.
Определение габаритных размеров основных деталей штамповых блоков табл. 3.28). Размеры плит штампов в плане зависят от аналогичных размеров деталей, которые, в свою очередь, определяют наружные размеры матриц, пуансонов, матрице- и пуансонодержателей. Немаловажное значение для определения размеров плит имеет расположение пазов для крепления штампов на рабочих поверхностях ползуна и на плите стола пресса. Опорные поверхности плит шлифуют, при этом предъявляются повышенные требования к параллельности и перпендикулярности.
Опыт эксплуатации штамповой оснастки для холодной объемной штамповки показывает, что минимальная толщина плит должна быть 70…75 мм. В некоторых случаях толщину плит определяют расчетом на изгиб. Аналогичным образом можно производить проверку различных подкладок. Согласно общему правилу опорные под кладки под пуансоны для холодного выдавливания при удельных усилиях штамповки 1800…2000 МПа должны иметь толщину 20…30 мм, а при 2000…2300 МПа — 30…40 мм. Подкладки под матрицы должны иметь толщину 20…25 мм. Размеры направляющих колонок и втулок зависят от габаритных размеров плит. Так, у многопозиционных штампов, имеющих длинные плиты, колонки значительно мощнее, чем у однопозиционных. Диаметры колонок у большинства однопозиционных штампов находятся в пределах 70…75 мм.
3.8.3. Рабочие детали штампов для холодного выдавливания.
Рабочий инструмент в соответствии с технологическими операциями холодного выдавливания можно разделить на три
200
основные группы: для объемной калибровки заготовок перед выдавливанием; для основных формоизменяющих операций холодного выдавливания (конструкция инструмента зависит от схемы деформирования: прямое, обратное и комбинированное); для дополнительных операций (осадки фланца, подчеканки внутренних и наружных элементов, протяжки, просечки отверстий и т. д.).
Геометрические параметры рабочего инструмента зависят от формы и размеров выдавливаемой детали.
Инструмент, предназначенный для калибровки заготовок, состоит из пуансона, матрицы и выталкивателя (рис. 3.47, а). Наиболее нагруженной деталью, подвергаемой большому износу, является матрица. Поэтому при ее конструировании необходимо не допускать острых углов и особенно подрезов в месте перехода от цилиндрической боковой поверхности к фаске на дне (оптимальным считается переходной радиус R = 5 мм). Для уменьшения усилия выталкивания и компенсации неравномерного износа стенки рабочей полости матрицы следует изготовлять с уклоном до 1°; наружная поверхность матрицы должна иметь уклон 1°30' для последующей запрессовки в бандаж.
Незакрепленная часть пуансонов для предварительной калибровки должна быть возможно короче, а переходы от одной ступени к другой — возможно более плавными. На рабочем торце пуансона не допускаются риски от резца, которые являются концентраторами напряжений и ведут к образованию трещин и поломке. В зависимости от необходимости рабочие торцы пуансонов могут быть плоскими, скошенными под углом 1…2°, иметь небольшие выступы и т. п. Прямое выдавливание осуществляют с помощью пуансона, матрицы и выталкивателя (рис. 3.47, б).
При изготовлении полых деталей применяют пуансон со скользящей оправкой. Здесь также необходимо избегать резких переходов сечений. Применение цельных пуансонов с оправкой нецелесообразно, так как наличие большого перепада
201
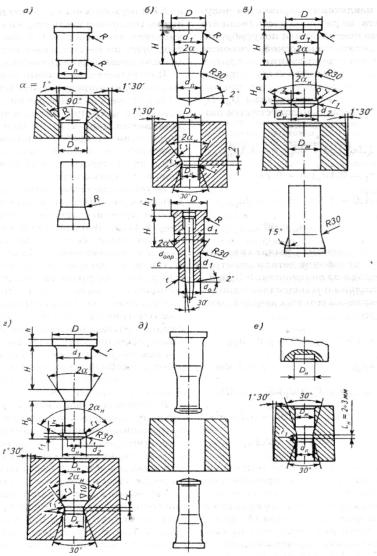
сечений вызывает концентрацию напряжений в переходной зоне уже после термообработки. В процессе
Рис. 3.47. Конструкции рабочих деталей штампов: а — для калибровки заготовок; б — для прямого выдавливания; в — для обратного выдавливания; г — для
202
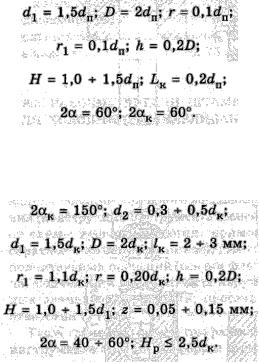
комбинированного выдавливания; д — для двустороннего выдавливания; е — для редуцирования.
выдавливания оправка под действием изгибающих и растягивающих напряжений отрывается. Оптимальной конструкцией является составной пуансон с подвижной оправкой, которая перемещается в пуансоне по скользящей оправке. Торцы пуансонов и поверхность оправки должны быть тщательно отшлифованы и отполированы. Острые кромки рабочих торцов следует притуплять. Чтобы облегчить извлечение оправки из полуфабриката, ее рабочую часть (если это допустимо конструкцией полуфабриката) надо делать конической с уклоном 30'. При конструировании матриц и пуансонов для прямого выдавливания (рис. 3.47, б) рекомендуется принимать следующие соотношения DM, DK и dопр по минимально допустимым размерам готовых изделий:
При обратном выдавливании (рис. 3.47, в) рабочие детали конструируют исходя из соотношений DH и dK по минимально и максимально допустимым размерам готовых деталей соответственно:
При холодном обратном выдавливании с большими
203
степенями деформации и высокими удельными усилиями выталкиватель может деформироваться (осадка) и застрять в матрице. Во избежание этого рекомендуется применять выталкиватель, показанный на рис. 3.47, в. Его головка диаметром входит в отверстие матрицы по посадке h7 и осуществляет рабочее направление. Остальная часть стержня выталкивателя занижена на 0,2 мм, благодаря чему он не застревает в матрице даже в случае деформирования.
Инструмент для комбинированного выдавливания представляет собой сочетание пуансона для обратного выдавливания с матрицей для прямого выдавливания (рис. 3.47, г). При конструировании этих рабочих деталей придерживаются правил, изложенных выше для каждого технологического способа в отдельности.
Двустороннее выдавливание полых деталей с перемычкой осуществляется одновременно двумя пуансонами (рис. 3.47, д). Верхний пуансон конструируют, как и обычные пуансоны для обратного выдавливания. Нижний имеет такую же конфигурацию рабочего торца, но, как правило, значительно длиннее. Это связано с тем, что кроме необходимости крепить его приходится предусматривать установку трубчатого нижнего выталкивателя, обеспечивающего удаление детали из матрицы. Такая конструкция может оказаться неработоспособной из-за недостаточной прочности нижнего пуансона и ненадежного его крепления.
В модернизированной конструкции рабочего инструмента выталкивание полуфабриката осуществляется двумя стержнями, имеющими в поперечном сечении вид круговых сегментов. Нижний пуансон надежно закрепляют в плите штампа с помощью втулки.
Рабочими деталями при выполнении технологической операции редуцирования являются матрица и пуансон (рис. 3.47, е). Внутренняя полость редуцировочной матрицы по своей конфигурации аналогична полости матрицы для прямого
204
выдавливания (рис. 3.47, б).
Основные отличия заключаются в значительно более коротком контейнере и меньшем угле раствора (2α < 30°) конического переходного участка. Контейнер служит здесь только для центрирования заготовки, и его длина не превышает 1…l,5dM. Остальные размеры определяют аналогично прямому выдавливанию.
В случае необходимости в пуансоне может быть предусмотрено дополнительное центрирующее углубление.
При сложной ступенчатой форме полости матриц и различной форме сечений ступеней рекомендуется конструировать матрицу составной. Разделение производится по горизонтальной (перпендикулярной к главной оси полости матрицы) плоскости по месту перехода. При многоугольном сечении полости матриц сопряжение граней осуществляется по дуге окружности радиусом 1…1,5 мм. При значительных нагрузках матрицу с многогранной полостью изготовляют из отдельных секторов.
При конструировании пуансонов и матриц для холодного выдавливания следует иметь в виду, что неперпендикулярность опорного торца относительно главной оси не должна превышать 0,01…0,02 мм.
При необходимости рабочим элементам выталкивателя и пуансона можно придавать различные формы (рис. 3.48).
Матрицы для выдавливания подвергают воздействию распорных усилий. Увеличение прочности таких матриц достигается за счет напрессовки на них бандажей с определенным натягом. В результате матрице (вставке) сообщается предварительная нагрузка, противоположная по знаку распорному усилию, вызываемому радиальными напряжениями при штамповке.
По типу посадочной поверхности различают цилиндрические и конические бандажи. Запрессовку можно производить в подогретом (до 400°С) и в холодном состояниях. В подогретом состоянии напрессовывают
205
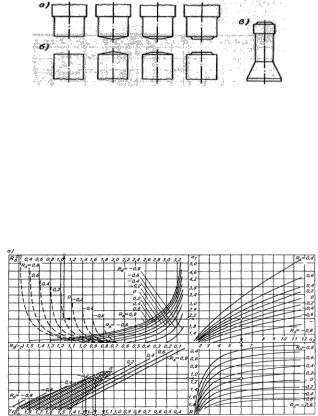
цилиндрические бандажи, а в холодном — конические с углом наклона образующей на сторону 1°30' ± 5'. К качеству конических поверхностей бандажей предъявляют весьма высокие требования — боковые поверхности должны быть тщательно прошлифованы, а углы сопрягаемых конусов — совпадать, в противном случае не будет обеспечено точного прилегания посадочных поверхностей друг к другу и предварительное напряжение окажется недостаточным по значению и неравномерно распределенным.
Рис. 3.48. Формы рабочих частей пуансона для калибровки заготовок (а), выталкивателя для калибровки заготовок или обратного выдавливания (б) и конструкция
выталкивателя для обратного выдавливания (в).
3.8.4. Расчет конструкций узлов бандажированных матриц штампов холодного выдавливания.
Матрицу с одним бандажом (двухслойную) рассчитывают с помощью номограммы (рис. 3.49).
Рис. 3.49. Номограммы для расчета матриц со стальными (а и б) и твердосплавными (в) вставками (а — для двухслойной матрицы), (начало)
206
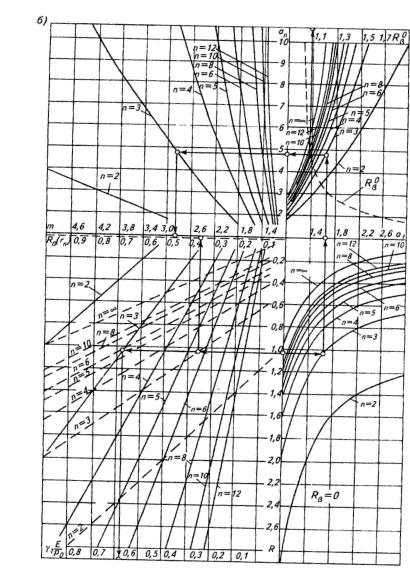
Рис. 3.49. Номограммы для расчета матриц со стальными (а и б) и твердосплавными (в) вставками (б — для многослойных), (продолжение)
207
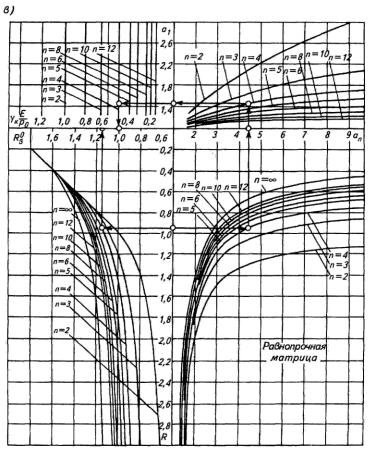
Рис. 3.49. Номограммы для расчета матриц со стальными (а и б) и твердосплавными (в) вставками (б — для многослойных), (окончание)
Номограмма позволяет по двум известным или заданным безразмерным параметрам определить все другие необходимые величины (табл. 3.29). В первой четверти номограмм (рис. 3.49) представлены зависимости a1 = f(а2) для значений Rθ ОТ + 0,8 (растягивающие) до -0,8 (сжимающие). Во второй четверти приведены зависимости R = f(а2) для тех же значений Rθ. В третьей четверти — зависимости Y1 = Е/ρ0 = f(R), в четвертой
208
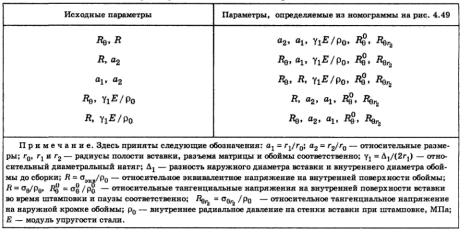
— зависимости Rθ оr = f1(a1) (сплошные кривые) и Rθ f2(a1) (штриховые кривые). Заштрихованный в третьей четверти номограммы участок показывает область допустимых отклонений величины γ1 = Е/Ро при 10% -ном отклонении от оптимальных значений при Rθ = 0.
Таблица 3.29. Состав параметров, необходимых для расчета бандажей.
Порядок расчета бандажей следующий.
Задаются два исходных параметра. Согласно табл. 3.30, это могут быть: геометрические соотношения, относительные напряжения или различные комбинации этих параметров и натягов. На практике чаще всего приходится решать задачу об определении радиуса разъема составной матрицы, натяга и напряжении при известном диаметре посадочного гнезда (известно а2). Такая задача возникает при проектировании сменных рабочих деталей к имеющемуся штамповому блоку. В этом случае задается одно из напряжений: R или Rθ.
Второй типичный вариант расчета состоит в определении размеров составной матрицы по известному диаметру рабочей полости и заданным напряжениям R и Rθ. Обычно принимают Rθ = 0, R ≤ [σ''p], где [σ''p] — предел текучести термообработанного материала бандажа при растяжении.
209