
3875
.pdfПри рабочем ходе усилие через несущую плиту и шарики сепаратора передается на нижнюю плиту и через подкладную плиту и опорную плиту — на штамп. При появления боковых усилий и вибраций в горизонтальной плоскости несущая плита перемещается по отношению к нижней плите, не передавая боковых нагрузок на штамп. При возникновении усилий, превышающих расчетные, несущая плита упирается в ограничители, предохраняя поверхности плит и шариков от повреждения. При появлении перекосов в процессе работы (что особенно ощутимо при вырубке тонких материалов толщиной 0,05…0,2 мм) опорная плита перемещается по сфере подкладной плиты и компенсирует эти перекосы.
При ходе вверх несущая плита через шарики сепаратора передает усилие на верхнюю плиту и через промежуточную плиту, гайку, сферический винт — на опорную плиту и штамп. При появлении боковых нагрузок и вибраций несущая плита перемещается на шариках сепаратора, не передавая эти нагрузки на верхнюю плиту и штамп. Эластичные втулки и штифты центрируют узел. При появлении перекосов сферическая часть опорной плиты, взаимодействуя со сферическим винтом, компенсирует перекос. При ходе вниз цикл повторяется.
Практика применения перемещающихся узлов крепления штампов к прессам-автоматам свидетельствует о том, что при правильном использовании эти узлы обеспечивают повышение стойкости штампов в 1,5…2 раза, расширяют возможность применения твердосплавных штампов: ранее для использования таких штампов необходимо было наличие прессового оборудования более высокой жесткости. Применение перемещающихся (компенсационных) узлов позволяет увеличить безаварийную работу пресса при эксплуатации штампов на прессах-автоматах и снизить число случайных поломок рабочих элементов штампов.
160
3.6. Конструкционные материалы для изготовления деталей штампов.
Основные виды, марки, сортамент и размеры стального проката, применяемого для изготовления деталей штампов, приведены в табл. 3.16.
В табл. 3.17 приведены марки конструкционных материалов, используемые для изготовления стандартных заготовок набора плит узла типовых пакетов разделительных штампов (см ГОСТ 15861).
Рабочие детали штампов (пуансоны и матрицы) подвергаются ударной нагрузке с сильной концентрацией напряжений на рабочих кромках или на рабочей поверхности. Поэтому к материалу пуансонов и матриц предъявляется, требование высоких или повышенных твердости и износоустойчивости при наличии достаточной вязкости. К материалу пуансонов и матриц для холодного выдавливания предъявляется также требование повышенной теплостойкости.
Рекомендации по выбору материалов для изготовления рабочих элементов в зависимости от условий их эксплуатации приведены в табл. 3.18.
Из табл. 3.18 видно, что поставки основных инструментальных и легированных сталей, используемых в качестве конструкционного материала для рабочих частей штампов, — это прутки, полосы и мотки проволоки по ГОСТ 1435, а также сортовой прокат по ГОСТ 5210.
Вид поставок высокоуглеродистых инструментальных и легированной сталей марок У7, У12, У7А, У12А и ХВГ, а также штамповых сталей Х12, Х12Ф1, Х12МФ и Х12ВМФ регламентирован ГОСТ 1435 (прутки, полосы и мотки проволоки) и ГОСТ 5210 (прокат сортовой).
Наряду со стальным прокатом для изготовления рабочих элементов применяют твердые порошковые сплавы марок ВК15, ВК20, ВК25 по ГОСТ 3882: иногда используют отливки из серого чугуна с пластинчатым графитом марок СЧ24, СЧ25,
161
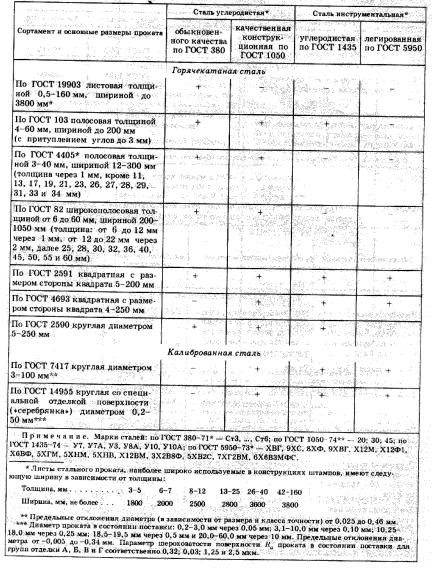
Таблица 3.16 Стальной прокат, применяемый для изготовления деталей
штампов.
162
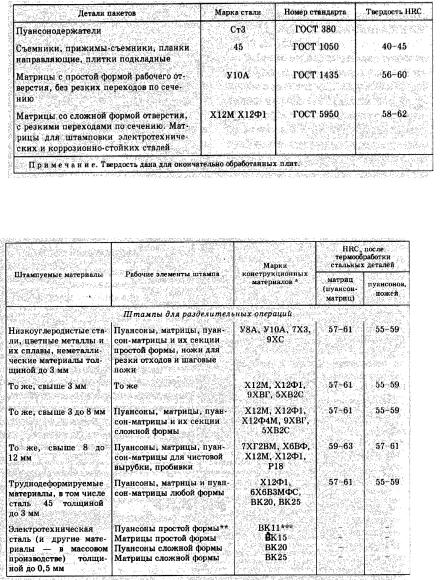
Таблица 3.17 Конструкционные материалы для изготовления заготовок
плит пакетов разделительных штампов.
Таблица 3.18 Выбор марок конструкционных материалов для рабочих
элементов штампов и требуемая твѐрдость
163
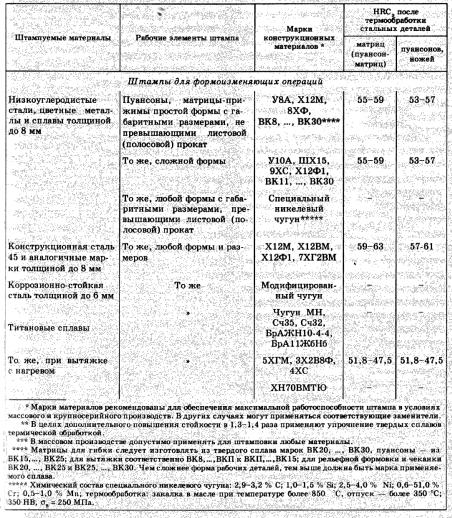
Продолжение табл. 3.18
СЧ40 по ГОСТ 1412, отливки из безоловянной бронзы БрАПЖбНб по ГОСТ 493 или поковки из безоловянной бронзы БрАЖН10-4-4 по ГОСТ 18175, отливки из жаропрочного сплава ХН70ВМТЮ (ЭИ617) по ГОСТ 5632.
164
Допускаются замена указанных материалов другими с равноценными механическими свойствами, а также снижение твердости термически обработанных деталей штампов до 15 % на расстоянии не более 10 мм от рабочих поверхностей (кромок).
Стали, применяемые для изготовления рабочих частей штампов холодной штамповки, делятся на следующие группы: углеродистые стали небольшой прокаливаемости диаметром до 25 мм: (У8А, У10А, У8, У10); легированные стали повышенной прокаливаемости диаметром 40…50 мм (ШХ15, Х09, ШХ9, 9Х, 9ХС, 9ХФ, ХВГ, 9ХВГ, ХГСВФ); высокохромистые стали высокой прокаливаемости диаметром до 80 мм, высокой износоустойчивости, малодеформируемые при закалке (Х12Ф1, Х12Ф, Х12М, Х12, ХГЗСВФ); легированные стали повышенной вязкости при твердости
56…58 HRCэ, (4ХС, 6ХС, 4ХВ2С, 5ХВ2С, 6ХВ2С, 5ХВГ).
Высокохромистые износоустойчивые стали имеют некоторые различия по механическим свойствам после закалки. Сталь Х12Ф1 несколько пластичнее сталей Х12Ф и Х12М. Но сталь Х12М имеет несколько более высокую твердость (на одну единицу по Роквеллу) и большую износоустойчивость. Сталь Х12 при высокой твердости обладает несколько меньшей вязкостью и применяется для штампов простой формы, которые работают без значительных ударных нагрузок, но от которых требуется повышенная износоустойчивость.
Для вытяжных штампов рекомендуется применять стали Х12, Х12Ф1 с азотированием поверхности при твердости наружного слоя 68…69 HRCэ. и твердости закаленного подслоя 58 HRCэ. Стали этой группы подвергаются закалке с нагревом до высоких температур (Х12М, Х12Ф, Х12 — 1020…1040°С; Х12Ф1 — 1070…1090°С) и низкому отпуску
(150…170°С). Твердость 61…63 HRCэ.
Наряду с достоинствами высокохромистые стали обладают некоторыми недостатками: повышенной карбидной неоднородностью, являющейся зачастую причиной
165
выкрашивания поверхностей и рабочих кромок; необходимостью повышенной температуры закалки (1020…1090°С) и высокой чувствительностью к возможным колебаниям температур закалки.
При изготовлении пуансонов и матриц сложной формы и небольших сечений (30…40 мм) применяются стали ХГЗСВФМ и 7ХГ2ВФМ. Их закалка с охлаждением на воздухе обеспечивает твердость 59…62 HRCэ. По сравнению со сталями марок Х12М и Х12Ф1 эти стали обладают значительно меньшей карбидной неоднородностью (менее 1 балла) и не требуют высокой температуры нагрева при закалке. Стойкость их выше стойкости стали Х12Ф1.
Графитизированные стали марок ЭИ293 и ЭИ366 являются износоустойчивым материалом, также применяемым для изготовления штампов. На инструмент из этих высокоуглеродистых сталей не налипают частицы металла, что предотвращает возникновение задиров и царапин на изделии.
Большое содержание углерода и кремния приводит к графитизации стали при термической обработке. Графит придает стали износоустойчивость и высокие антифрикционные свойства. Графитизированная сталь успешно применяется при вытяжке коррозионно-стойкой стали и титановых сплавов. Термическая обработка графитизированной стали состоит из графитизирующего отжига и закалки. Твердость стали ЭИ366 58…62 HRCэ, а стали ЭИ293 60…65 HRCэ. В мелкосерийном производстве нет надобности стремиться к высокой стойкости рабочих частей штампов. В этом случае могут быть применены пуансоны и матрицы из более дешевой стали марки 45 с закалкой в воде и отпуском при 200…250°С до твердости 45…50 HRCэ.
При малых партиях штампуемых деталей (единичное и мелкосерийное производства) рабочие части могут выполняться с твердостью, незначительно превышающей твердость разделяемого материала. Например, допускается применять незакаленные стали типа ЭКБ.
166
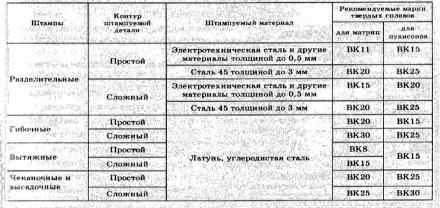
Для обеспечения максимальной работоспособности штампа формоизменяющих операций ХШ в условиях массового и крупносерийного производств при штамповке полуфабрикатов из низколегированных сталей, цветных металлов и их сплавов толщиной до 8 мм для рабочих элементов любой формы с габаритными размерами, превышающими имеющийся листовой (полосовой) прокат, рекомендуется использовать специальный никелевый чугун.
В условиях крупносерийного и массового производств рабочие части штампов должны быть высокостойкими. В табл. 3.19 приведены уточненные данные для выбора марок твердых сплавов для высокостойких штампов ХШ.
Таблица 3.19 Выбор марок твѐрдых сплавов для высокостойких штампов.
В мелкосерийном производстве предпочтительны процессы разделения листового материала с применением эластичной, газовой, пластично-вязкой или жидкостной сред, а также импульсных магнитных полей высокой плотности.
Заготовки деталей штампов из инструментальных и легированных сталей необходимо подвергать первичной термической обработке, обеспечивающей возможность их дальнейших механической и термической обработок и стабильность размеров. Заготовки деталей штампов из серого чугуна должны иметь твердость не более 240 НВ, стальные отливки — не более 215 НВ. Заготовки деталей штампов из
167
серого и легированного чугунов необходимо подвергать естественному или искусственному старению.
Для изготовления деталей технологического (кроме рабочих элементов), конструктивного, кинематического и вспомогательного назначений используются в основном углеродистые обыкновенного качества, углеродистые конструкционные, а также легированные конструкционные стали (например, 40Х, 45Х) по ГОСТ 4543, поставляемые в виде полосы по ГОСТ 103-76, квадрата по ГОСТ 2591 и круга по ГОСТ 2590 и ГОСТ 14955. В отдельных случаях применяется шарикоподшипниковая сталь марок ШХ15, ШХ4, ШХ15СГ, ШХ2ССГ по ГОСТ 801, поставляемая в виде прутков (круглых диаметром 5…250 мм, квадратных со стороной квадрата 5…200 мм), полос (толщиной 4…60 мм, шириной до 200 мм), калиброванных прутков (диаметрами 3…100 и 0,2…50 мм) со специальной обработкой поверхности.
Для изготовления пружин сжатия, растяжения, кручения применяются проволока диаметром 0,2…8,0 мм по ГОСТ 9389 из сталей по ГОСТ 1050 и ГОСТ 1435, а также проволока диаметром 3…12 мм по ГОСТ 14963.
Для изготовления тарельчатых пружин применяются стали марок 60С2А, 60С2, 50ХФА, 65С2ВА, 70СЗА по ГОСТ
14959.
Для изготовления пластинчатых пружин применяется сталь марки 65Г по ГОСТ 14959, поставляемая в виде ленты по ГОСТ 2283 толщиной 0,1…4,0 мм, шириной 4…465 мм и в виде листов толщиной 0,5…4,0 мм, шириной до 2300 мм.
Наряду со стальным прокатом используются отливки из конструкционной нелегированной и легированной сталей по ГОСТ 977 марок 40Л, 45Л и отливки из серого чугуна марок СЧ24, СЧ25 по ГОСТ 1412.
Применяются также неметаллические материалы — листовая маслобензостойкая резина по ГОСТ 7338, полиуретан по ТУ 84-404 и ТУ 38-103-133, а также различные пластические массы.
В табл. 3.20 приведены рекомендации по выбору материалов для изготовления базовых и вспомогательных деталей штампов (кроме рабочих элементов).
168
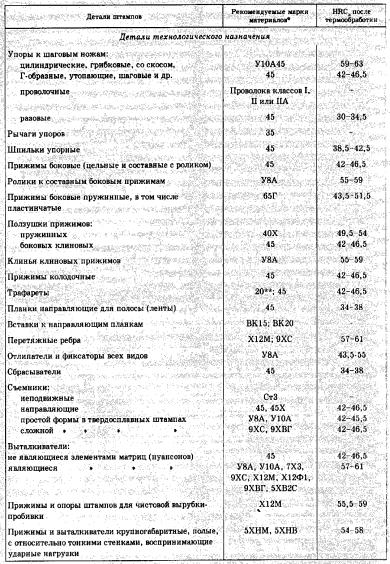
Таблица 3.20 Материалы и нормы твѐрдости деталей различного назначения
169