
3875
.pdfпуансонах осуществляют также с помощью выступа и шпонки. На многих инструментальных предприятиях используется диффузионная сварка твердосплавных элементов пуансонов со стальными. Диффузионное соединение обладает достаточно высокой прочностью. Возникающие в процессе сварки термические напряжения могут быть в значительной мере устранены путем оптимального термического цикла и применения промежуточных компенсационных прокладок. Опыт показал, что такие материалы, как никель 50НП и пермаллой 50НХС наиболее полно удовлетворяют требованиям, предъявляемым к. промежуточным компенсационным прокладкам. При сварке твердых сплавов с углеродистыми сталями без промежуточных прокладок в
сварном соединении образуется хрупкая переходная зона. Обычная пайка элементов пуансона встык твердыми
припоями не гарантирует его надежной работы. При длительных ударных нагрузках в месте спая появляется наклеп, после чего место соединения разрушается. Для крепления сборных элементов пуансонов применяют специальные конструктивные элементы. Примером может служить конструкция круглого пуансона для пробивки, у которого опорная поверхность твердосплавной вставки выполнена по конусу. Стойкость такого пуансона не уступает стойкости цельно-твердосплавного пуансона. Двусторонний зазор под пайку принимают 0,02…0,04 мм. Державку пуансона изготовляют из стали Х12М (55…59 HRCэ).
Стойкость современных твердосплавных штампов в десятки раз выше стойкости штампов со стальными рабочими элементами. Такое повышение может быть достигнуто при тщательном выборе геометрических размеров основных и вспомогательных деталей твердосплавных штампов.
80
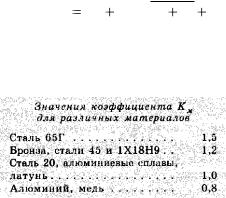
3.2. Основные и вспомогательные детали штампов.
3.2.1. Расчет габаритных размеров матриц разделительных штампов.
Толщину плиты цельной матрицы разделительного штампа рассчитывают по формуле
HM 2S KM ao bo 5 ,
где S — толщина обрабатываемого материала, мм;
Км — коэффициент, зависящий от прочности штампуемого материала;
aQ, bQ — размеры рабочей зоны в матрице, мм.
Значение расчетной толщины матрицы округляют то ближайшего значения в ряду 10; 12; 16; 20; 25 мм. В матрицах, которые имеют несколько длинных (более 50 мм) окон с перемычками шириной менее 8 мм между ними, рекомендуется применять не ближайшее, а следующее за ним значение толщины матрицы в приведенном ряду. В малогабаритных матрицах (80×100 мм и менее) применяют меньшее в ряду значение толщины матрицы. Плита матрицы может проектироваться как сборочная единица (узел), состоящая из обоймы и вкладыша. Как правило, толщина малогабаритного вкладыша матрицы равна 10 мм. В этом случае под матрицу устанавливают термообработанную плиту с окнами, на 0,5 мм эквидистантно большими окон в матрице. Малые перемычки между рабочими окнами матрицы в плане могут привести к преждевременной поломке штампа, а необоснованное увеличение расстояния между окнами—к повышению расхода конструкционного материала и
81
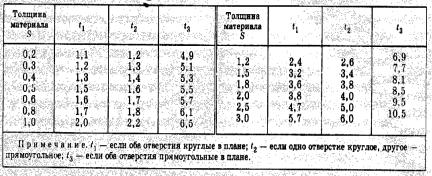
ухудшению качества штампуемых деталей.
Размеры перемычек между двумя круглыми рабочими отверстиями матрицы в плане, между круглым и фигурным рабочими отверстиями, между вершинами углов прямоугольных окон при вырубке стали и бронзы принимают по табл. 3.5. При вырубке латуни, меди и алюминия ширину перемычки принимают на 10 % меньше, чем при вырубке стали.
Таблица 3.5 Наименьшая ширина перемычек меду рабочими
отверстиями матрицы, мм.
Если рабочее отверстие в матрице выполнено с провальным окном, минимальную ширину перемычки увеличивают на высоту ступени провального окна.
При определении минимального расстояния от рабочего окна до края прямоугольной твердосплавной матрицы (толщины стенки матрицы) при наибольшей длине рабочего окна матрицы в плане следует руководствоваться данными, приведенными в табл. 3.6.
Минимальную ширину стенки круглой вставки матрицы с круглым окном определяют по табл. 3.7. Размеры установлены для матриц или вставок, изготовленных из сплава ВК20.
Распирающее усилие, приходящееся на миллиметр длины окна матрицы (кроме острых углов) при равномерном зазоре и
82
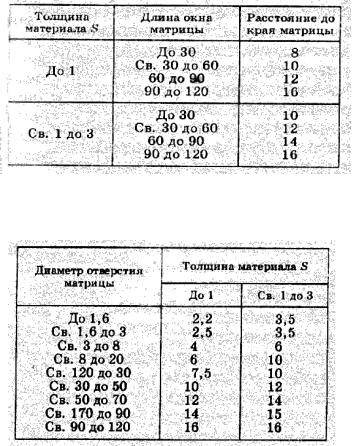
прямолинейном расположении режущих кромок пуансона и матрицы, рассчитывают по формуле
Рр = 0,4P/L,
где Р — усилие вырубки (пробивки), Н, L — периметр рабочего окна матрицы, мм.
При Р > 600 Н/мм минимальную ширину стенок увеличивают в 1,5 раза.
Таблица 3.6 Расстояние от рабочего окна до края матрицы, мм.
Таблица 3.7 Наименьшая ширина стенки круглой матрицы или
вставки, мм.
83
Твердосплавные вставки матрицы крепят в обойме с определенным натягом. В цельных вставках матрицы, как и в сборных, различают три вида натягов: нормальные Нн, уменьшенные Нум и увеличенные Нув.
В большинстве конструкций штампов принимается, как правило, нормальный натяг. Его получают горячей запрессовкой при нагреве обоймы до 370 ± 10 °С. Нормальный натяг (мм) рассчитывают по формуле
Нн = LП/1000 + 0,02,
где LП — размер посадочной части вставки (матрицы), мм. Уменьшенный натяг применяют при запрессовке
твердосплавных матриц (вставок) в закаленную обойму при ее твердости 48…54 HRCэ:
Нум = 0,52Нн.
Увеличенный натяг применяют для запрессовки матриц вырубных штампов при больших распирающих усилиях (для вырубки материалов толщиной более 2,5 мм), для матриц, работающих в особо тяжелых условиях, а также для матриц вытяжных штампов. Его рассчитывают по формуле:
Нув = 1,8Нн.
В матрицах с большими распирающими односторонними усилиями при запрессовке рекомендуется применять увеличенный натяг и односторонние бурты.
Чтобы не допустить прогиба стенки при запрессовке твердосплавных вставок матриц с прямоугольными рабочими окнами длиной более 50 мм при ширине стенки между рабочим окном и обоймой до 12 мм, по краям матрицы рекомендуется выполнять нормальный натяг, а в середине, у рабочего окна, — уменьшенный.
Матрицы с нормальным и увеличенным натягом запрессовываются в горячем состоянии, матрицы с уменьшенным натягом — в холодном.
Увеличение размера любой стороны окна обоймы в результате термического расширения при нагреве до 370 °С для запрессовки рассчитывают по формуле:
lt = l20(1 + αt),
где lt — длина любой стороны окна обоймы при нагреве ее до
84
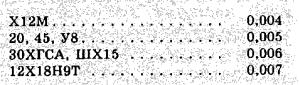
температуры 370 °С, мм; l20 — длина этой стороны при исходной температуре 20 °С, мм; αt — температурный коэффициент линейного расширения при нагреве обоймы до
370 °С.
Значения коэффициента αt для различных марок сталей приведены ниже:
Минимальная ширина стенок обоймы с нагруженным диаметром D0 цельной твердосплавной вставки матрицы диаметром D, которая запрессована с нормальным натягом, при твердости обоймы 29…33 HRCэ, выполненной из стали 45, принимается по отношению DО /D: 2…3 при толщине штампуемого материала до 1 мм; 2,5…4 при толщине свыше 1 до 3 мм; меньшие значения отношения для вставок диаметром D свыше 50 мм.
С учетом возможности выкрашивания твердого сплава и высокой износостойкости деталей зазор между пуансоном и матрицей в твердосплавных штампах при вырубке материала толщиной до 2 мм обычно увеличивают по сравнению с зазором, принятым в штампах со стальными рабочими элементами, на 2…3 % от толщины штампуемого материала. Такие зазоры применяют при частоте ходов пресса до 240 в минуту. При более высоких скоростях штамповки зазор между матрицей и пуансоном увеличивают (см. табл. 3.4).
3.2.2. Использование количественных критериев при выборе конструкции пуансонов разделительных штампов.
Максимально допустимое удельное усилие на опорную поверхность пуансона зависит от марки стали и термической обработки опорной плиты (Н/мм3):
Ст 3………………………………………100 У8 (29…33HRCэ)……………......………250
У8, Х12(49…52HRCэ)…………………..500.
Цельные твердосплавные пуансоны крепят в пуансонодержателе с помощью буртов. Диаметр бурта в целях
85
экономии твердого сплава выполняют меньшим, чем в стальных пуансонах, на 20…25%.
При вырубке и пробивке материалов толщиной 2…4 мм для предотвращения разрыва рабочей части пуансонов, сколов и выкрашиваний, а также для уменьшения усилия снятия отхода или отштампованной детали пуансоны следует выполнять с уклоном по рабочей части. Для круглых пуансонов принимают аук = z/3, для прямоугольных и фигурных аук = z/4, где z — двусторонний зазор между режущими кромками пуансона и матрицы.
Поверхность по рабочему контуру желательно полировать до достижения параметра шероховатости Ra = 0,16 мкм. Торцовая поверхность, напротив, должна быть грубой (Ra = 2,5 мкм). При односторонней вырубке (обрезке, отрезке) и угле резания менее 90° параметр шероховатости поверхности пуансона по рабочему контуру и по торцу Ra < 1,25 мкм.
3.2.3. Расчет габаритных размеров обойм твердосплавных вставок матриц вытяжных штампов.
Исполнительные размеры твердосплавных вставок вытяжных матриц определяют так же, как и стальных. Кроме того, необходимо рассчитывать наружный диаметр обоймы Doб, высоту вставки Нм и радиус закругления матрицы rм, а при двойном бандажировании — наружный диаметр первого и второго бандажей D1 и D2. Элементы матрицы штампа с одинарным и двойным бандажированием показаны на рис. 3.6.
Наружный диаметр обоймы: Doб = 2Dн, где Dн — наружный диаметр вставки.
Для штамповки деталей из низкоуглеродистой стали радиус закругления принимают rм = (6…8)S, из латуни и алюминия — rм = (5…6)S.
При двойном бандажировании наружный диаметр первого и второго бандажей определяют по формулам:
D1= 1,6Dн; D2 = 2,6Dн.
86
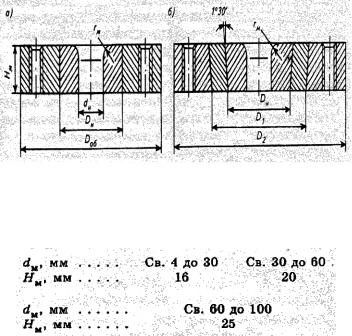
Двойное бандажирование рекомендуется выполнять при вытяжке с утонением деталей из латуни и стали при толщине свыше 0,8 мм.
Рис. 3.6. Матрицы с одинарным (а) и двойным (б) бандажированием в обойме.
Рекомендуемая высота твердосплавной вставки Нм зависит от внутреннего диаметра или диагонали вставки dм:
Диаметры упорных колонок выбирают в зависимости от усилия вырубки. Допускаемое усилие на все упорные колонки должно в 1,5 раза превосходить технологическое усилие вырубки.
Допускаемое усилие на одну упорную колонку определяют по формуле:
Ру.к = 0,7851D2у.к [σсж],
где Dу.к — диаметр колонки, мм; [σсж] — допускаемое напряжение на сжатие, МПа; для стали 45 при твердости 29…33 HRCэ принимают σсж = 200 МПа.
В штампах с большим усилием вырубки применяют упорные втулки или упорные планки, термообработанные до твердости 44…49 HRCэ. Площадь опорной поверхности упорной втулки или упорной планки определяется расчетом допускаемых удельных усилий (до 200 Н/мм2).
87
3.2.4. Твердосплавные штампы повышенной стойкости, изготовляемые с применением обратной электроэрозионной
прошивки.
Эти штампы отличаются высокой жесткостью, специальной конструкцией подвижного съемника и пуансонодержателя, наличием рабочего износостойкого слоя (полученного в результате электроэрозионной обработки), обратного уклона на пуансонах, обеспечивающего постоянство зазоров после перешлифовки.
Эта конструкция штампов применяется главным образом для последовательной вырубки листов статора и ротора малогабаритного электродвигателя (размер штампуемой детали не более 100 мм). Полная стойкость этих штампов 80…100 млн комплектов деталей.
Каждый элемент твердосплавной матрицы выполняется цельным. Элементы крепят в обойме горячей запрессовкой. Окна в матрице выполняют с уклоном 8…12' по контуру, параметр шероховатости Ra = 2,5÷1,25 мкм, высота рабочей части 10…12 мм.
Фигурные и сложноконтурные пуансоны выполняются из заготовок простой конфигурации в сечении (прямоугольник, круг), запрессованных в пуансонодержатель. Длину рабочей части пуансонов принимают 6…12 мм. Все пуансоны для пробивки, кроме круглых, изготовляют в сборе (монолитный блок штампа) обратной электроэрозионной прошивкой. На пуансонах выполнен обратный уклон, составляющий 0,7 уклона матрицы. Монолитный пуансон для пробивки всех пазов ротора выполняют из одной заготовки, внутри него крепят круглый пуансон для пробивки центрального отверстия листа ротора.
Съемник в этих штампах подвижно-навесной, в нем сочетаются преимущества подвижного съемника и надежность неподвижного. В период вырубки съемник приближен к ленте, а во время съема ленты он упирается в жесткие Г - образные
88
захваты - ограничители хода съемника, связанные с нижней плитой штампа, и работает как жесткий. При необходимости Г-образные захваты раздвигают, после чего съемник поднимают. Съемник имеет шариковые направляющие. Узел прижима съемника представляет собой специальный стакан со спиральной пружиной небольшого усилия и толкателем. Подъем съемника осуществляют твердосплавные ступенчатые отлипатели, которые служат и для направления ленты. Со стороны матрицы к съемнику крепят термообработанную пластину.
Врабочей зоне отверстия съемника со стороны пуансонодержателя выполнен уступ, в который входит пуансонодержатель, что позволяет повысить жесткость пуансонов. Общая высота пуансонов при этом минимальная. В штампе могут быть применены до четырех подпружиненных выносных ловителя.
Все пуансоны имеют равномерный зазор по всему контуру. Их изготовление и автоматическое выставление по матрице осуществляют с помощью одной операции — обратной злектроэрозионной прошивки непосредственно в блоке штампа методом комплексного сопряжения.
Верхняя плита и нижняя плита выполнены из стали 45 и термообработаны. Для рабочих элементов (матрицы и пуансонов) применяют твердый сплав ВК15 и ВК20.
Впроцессе эксплуатации заточку штампов проводят принудительно через 1 млн штампоударов. При заточке с матрицы и пуансонов снимают слой 0,05 мм.
3.2.5.Упругие вспомогательные элементы твердосплавных штампов.
Вразличных конструкциях твердосплавных штампов и, в первую очередь, в конструкциях штампов для разделительных операций с подвижным съемником, большое значение имеет надежность применяемых упругих элементов. Упругие элементы должны выдерживать без значительного изменения
89