
3187
.pdfзаливкой в них сплава (сырые, сухие, подсушиваемые и химически твердеющие).
Песчано-глинистые смеси. Основным компонентом формовочных и стержневых смесей является кварцевый или цирконовый песок. Вторым основным компонентом смеси (до 16%) является глина. Широко применяют бентонитовые и каолиновые глины, которые обладают высокой связующей способностью и обеспечивают тем самым прочность и податливость форм. В формовочные и стержневые смеси вводят также в небольших количествах дополнительные связующие (1,5…3%); их подразделяют на органические и неорганические, растворимые и нерастворимые в воде (сульфитноспиртовая барда, битум, канифоль, цемент, жидкое стекло, термореактивные смолы и др.).
Стержневые смеси. К стержневым смесям предъявляют более жесткие требования по огнеупорности, поверхностной твердости, податливости, низкой гигроскопичности, высокой газопроницаемости, лучшей выбиваемости, чем к формовочным смесям. Среди стержневых смесей, не требующих тепловой обработки, наиболее распространены песчаножидкостекольные смеси, а также холоднотвердеющие смеси на синтетических смолах, в которых в качестве связующего используют карбамидные, фенолофурановые и другие смолы. Среди стержневых смесей, отверждаемых тепловой обработкой, можно выделить песчано-масляные (связующее — раствор растительных масел и канифоли в уайт-спирте), песчаноглинистые и песчано-смоляные (связующее — синтетические смолы КФ-90, ОФ-1, пульвербакелит и др.).
Литейная форма должна обладать прочностью (выдерживать силовые нагрузки), газопроницаемостью (пропускать газы, образующиеся в литейной форме), податливостью (уменьшаться в объеме при усадке отливки), огнеупорностью (не оплавляться под действием тепла жидкого металла) и др.
Комплект приспособлений, используемых для изготовления отливок, называют литейной оснасткой. Часть оснастки, включающая все приспособления, необходимые для образо-
51
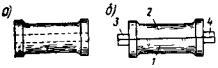
вания рабочей полости литейной формы при ее формовке, называется модельным комплектом. В комплект входят модели отливки и элементов литниковой системы, модельные и сушильные плиты, стержневые ящики, формующие, контрольные и сборочные шаблоны для конкретной отливки.
Модель — это часть модельного комплекта, предназначенная для образования отпечатка в литейной форме, соответствующего наружной конфигурации и размерам отливки. При этом размеры модели увеличивают по сравнению с соответствующими размерами отливки с учетом линейной усадки сплава (0,8…2%) и припусков на механическую обработку. Модели изготавливают из древесины, металлических и специальных модельных сплавов, а также из пластмасс. Различают модели разовые и многократные. Деревянные модели отличаются простотой изготовления, относительно малой массой и невысокой стоимостью. Однако они недолговечны.
По сравнению с деталью модель имеет выступающие части, так называемые стержневые знаки (рис. 2.1), с помощью которых получают полость в форме для установки стержня. Стержень, являясь элементом литейной формы, служит для образования отверстия, полости или иного сложного контура в отливке.
Рис. 2.1. а – отливка втулки, б – модель отливки: 1 – нижняя полумодель, 2 – верхняя полумодель, 3 и 4 – стержневые знаки
Для удержания формовочной смеси при изготовлении литейной формы, а также при транспортировке последней и ее заливке жидким металлом используют опоки, представляю-
52
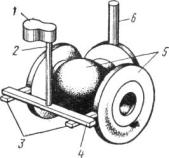
щие собой сварные, литые или сборные жесткие металлические рамы различной конфигурации.
Систему каналов, подводящих металл в форму, называют литниковой. Она состоит (рис. 2.2) из литниковой чаши или воронки 1, стояка 2, горизонтального канала или шлакоуловителя 4 и питателей 3. Литниковая чаша служит для приема металла из ковша и задерживает шлак. Стояк представляет собой вертикальный канал, по которому металл из чаши поступает в шлакоуловитель, расположенный в верхней полуформе в плоскости разъема формы.
Рис. 2.2. Элементы литниковой системы
Шлакоуловитель, находящийся обычно в верхней половине формы, задерживает шлак и неметаллические включения, попавшие в стояк. Из шлакоуловителя, имеющего в поперечном сечении форму трапеции, металл поступает в питатели.
Питатели, расположенные в нижней полуформе и имеющие также трапецеидальное сечение, служат для подвода металла непосредственно к отливке 5. Выпор 6 предназначен для вывода воздуха, газов и шлака из формы.
В зависимости от размера отливок и характера их производства применяют следующие способы изготовления разовых литейных форм:
53
1)ручная формовка в опоках для мелких, средних и иногда для крупных отливок в литейных цехах с низкой степенью механизации при индивидуальном и мелкосерийном производстве;
2)ручная формовка в почве (открытая и закрытая) пре-
имущественно для крупных отливок при индивидуальном их производстве;
3) машинная формовка для мелких и средних отливок в современных механизированных литейных цехах.
Машинную формовку применяют для производства отливок в массовом и серийном производствах. При формовке на машинах формы изготовляют в парных опоках с использованием односторонних металлических модельных плит. Машинная формовка механизирует установку опок на машину, засыпку формовочной смеси в опоку, уплотнение смеси, удаление моделей из формы, транспортирование и сборку форм. Машинная формовка обеспечивает высокую геометрическую точность полости формы по сравнению с ручной формовкой, повышает производительность труда, исключает трудоемкие ручные операции, сокращает цикл изготовления отливок. При машинной формовке формовочную смесь уплотняют прессованием, встряхиванием, пескометом, вакуумной формовкой и др.
Важное значение при заливке форм имеет выбор температуры заливки расплавленного металла. При повышенной температуре заливки возрастает жидкотекучесть металла, улучшается питание отливок, но горячий металл более газонасыщен, сильнее окисляется, вызывает пригар на поверхности отливки. В то время как низкая температура заливки увеличивает опасность незаполнения полости формы, захвата воздуха, ухудшается питание отливки. Температуру заливки сплавов целесообразно назначать на 100…150 °С выше температуры ликвидуса.
Охлаждение отливок в литейных формах после заливки продолжается до температуры выбивки. Небольшие тонкостенные отливки охлаждаются в форме несколько минут, а
54
толстостенные (массой 50…60 т) — в течение нескольких суток и даже недель. Для сокращения продолжительности охлаждения отливок, особенно массивных, используют различные методы принудительного охлаждения.
Выбивка отливок — процесс удаления затвердевших и охлажденных до определенной температуры отливок из литейной формы, при этом литейная форма разрушается. Выбивку отливок осуществляют на различных выбивных установках.
Обрубка отливок — процесс удаления с отливки прибылей, литников, выпоров и заливов (облоев) по месту сопряжения полуформ. Обрубку производят пневматическими зубилами, ленточными и дисковыми пилами, газовой резкой и на прессах. После обрубки отливки зачищают, удаляя мелкие заливы, остатки прибылей, выпоров и литников. Зачистку выполняют маятниковыми и стационарными шлифовальными кругами, пневматическими зубилами, газо-плазменной обработкой и другими способами.
Очистка отливок — процесс удаления пригара, остатков формовочной и стержневой смеси с наружных и внутренних поверхностей отливок. Ее осуществляют в галтовочных барабанах периодического или непрерывного действия, в гидропескоструйных и дробеметных камерах, химической или электрохимической обработкой и другими способами.
2.3. Литейные сплавы и их свойства
Для производства отливок используются сплавы черных металлов: серые, высокопрочные, ковкие и другие виды чугунов; углеродистые и легированные стали; сплавы цветных металлов; медные (бронзы и латуни), цинковые, алюминиевые и магниевые сплавы; сплавы тугоплавких металлов: титановые, молибденовые, вольфрамовые и др.
Литейные сплавы должны обладать высокими литейными свойствами; требуемыми физическими и эксплуатационными свойствами. Выбор сплава для тех или иных литых
55
деталей является сложной задачей, поскольку все требования
вреальном производстве учесть не представляется возможным.
Наиболее важные литейные свойства сплавов: жидкотекучесть, усадка (линейная и объемная), склонность к образованию трещин, склонность к поглощению газов и образованию газовых раковин и пористости в отливках и др.
Жидкотекучесть — это способность металлов и сплавов течь в расплавленном состоянии по каналам литейной формы, заполнять ее полости и четко воспроизводить контуры отливки.
Жидкотекучесть литейных сплавов зависит от температурного интервала кристаллизации, вязкости и поверхностного натяжения расплава, температуры заливки и формы, свойств литейной формы и т. д.
Жидкотекучесть литейных сплавов определяют путем заливки специальных технологических проб. Наибольшей жидкотекучестью обладает серый чугун, наименьшей - магниевые сплавы.
Усадка — свойство литейных сплавов уменьшать объем при затвердевании и охлаждении. Усадочные процессы в отливках, протекают с момента заливки расплавленного металла
влитейную форму вплоть до полного охлаждения отливки. Различают линейную и объемную усадку, выражаемую в относительных единицах.
Линейная усадка — уменьшение линейных размеров отливки при ее охлаждении от температуры, при которой образуется прочная корка, способная противостоять давлению расплавленного металла, до температуры окружающей среды. Линейную усадку определяют соотношением, %:
εлин = (lф – lот)100 / lот ,
где lф и lот — размеры полости формы и отливки при температуре 20 °С.
56
На линейную усадку влияют химический состав сплава, температура его заливки, скорость охлаждения сплава в форме, конструкция отливки и литейной формы. Так, усадка серого чугуна уменьшается с увеличением содержания углерода и кремния. Усадку алюминиевых сплавов уменьшает повышенное содержание кремния, усадку отливок — снижение температуры заливки. Увеличение скорости отвода теплоты от залитого в форму сплава приводит к возрастанию усадки отливки.
Линейная усадка для серого чугуна составляет 0,9…1,3 %, для углеродистых сталей 2…2,4 %, для алюминиевых сплавов 0,9…1,5 %, для медных 1,4…2,3 %.
Объемная усадка — уменьшение объема сплава при его охлаждении в литейной форме при формировании отливки. Объемную усадку определяют соотношением, %:
εоб = (Vф – Vот)100 / Vот ,
где Vф и Vот — объем полости формы и объем отливки при температуре 20°С.
Усадка в отливках проявляется в виде усадочных раковин, пористости, трещин и короблений.
Усадочные раковины — сравнительно крупные полости, расположенные в местах отливки, затвердевающих последними.
Усадочная пористость — скопление пустот, образовавшихся в от тестах отливки, которые затвердевали последними без доступа к ним расплавленного металла.
В отливках в результате неравномерного затвердевания тонких и толстых частей и торможения усадки формой при охлаждении возникают внутренние напряжения. Эти напряжения тем выше, чем меньше податливость формы и стержней. Если величина внутренних напряжений превзойдет предел прочности литейного сплава в данном участке отливки, то в теле ее образуются горячие или холодные трещины. Если литейный сплав имеет достаточную прочность и пластичность
57
и способен противостоять действию возникающих напряжений, искажается геометрическая форма отливки.
Горячие трещины в отливках возникают в процессе кристаллизации и усадки металла при переходе из жидкого состояния в твердое при температуре близкой к температуре солидуса. Горячие трещины проходят по границам кристаллов и имеют окисленную поверхность. Кроме того, образование горячих трещин вызывают резкие переходы от тонкой части отливки к толстой, острые углы, выступающие части и т. д.
Холодные трещины возникают в области упругих деформаций, когда сплав полностью затвердел. Тонкие части отливки охлаждаются и сокращаются быстрее, чем толстые. В результате в отливке образуются напряжения, которые и вызывают появление трещин.
Коробление — изменение формы и размеров отливки под влиянием внутренних напряжений, возникающих при охлаждении. Для предупреждения короблений в отливках необходимо увеличивать податливость формы; создавать рациональную конструкцию отливки и т. д.
Ликвация — это неоднородность химического состава сплава в различных частях отливки. Развитие химической неоднородности может происходить как в микрообъемах сплава (внутри отдельных дендритов слитка) — внутрикристаллическая (дендритная) ликвация, так и по отдельным его зонам (макрообъемам) — зональная ликвация. Одной из разновидностей зональной ликвации является ликвация по плотности (гравитационная ликвация). Дендритную ликвацию устраняют гомогенизацией — высокотемпературным диффузионным отжигом, приводящим к выравниванию химического состава в пределах микрозерна. Гравитационную ликвацию подавляют перемешиванием расплава, его быстрым охлаждением, а также применением легирующих добавок, образующих с основой разветвленные кристаллы (дендриты), мешающие перемещению в расплаве твердой фазы.
Растворенные в расплаве газы (водород, азот и др.) при затвердевании и охлаждении отливки могут выделяться в виде
58
химических соединений, а также образовывать газовые раковины и поры. Существенное уменьшение газонасыщенности сплавов достигается при их плавке в вакууме.
2.4. Специальные способы литья
Точность геометрических размеров, шероховатость поверхности отливок, полученных в песчаных формах, во многих случаях не удовлетворяет требованиям современной техники. Поэтому быстрыми темпами развиваются специальные способы литья: в оболочковые формы, по выплавляемым моделям, кокильное, под давлением, центробежное и другие, позволяющие получать отливки повышенной точности, с малой шероховатостью поверхности, минимальными припусками на механическую обработку, а иногда полностью исключающие ее, обеспечивают высокую производительность труда и т.д.
Некоторые характеристики отливок приведены в табли-
це 2.1.
2.4.1. Кокильное литье
Кокильным литьем называют процесс производства фасонных отливок в металлических формах, изготовленных из чугуна, стали, сплавов алюминия и других сплавов.
По конструкции различают кокиля: вытряхные, с вертикальным разъемом, с горизонтальным разъемом и др.
На рис. 2.3 показан вытряхной кокиль для изготовления опорного катка. Внутренняя полость формы воспроизводит наружную поверхность катка. Отверстие в отливке и внутренняя полость получаются с помощью песчаных стержней 1 и 2, последний из них перекрывает верхнюю часть формы. В стержнях 2, 3, 4 размещена литниковая система, состоящая из литниковой чаши, стояка, литникового канала, подающего металл в отливку, и двух прибылей.
59
|
|
|
|
Таблица 2.1 |
||
|
Допуски размеров и шероховатость |
|||||
|
|
поверхности отливок |
|
|
|
|
|
|
|
|
|
|
|
|
Габарит- |
Сплавы цвет- |
Сплавы цвет- |
Ковкий и |
|
|
|
ный |
|
||||
Способ |
ных метал- |
ных металлов с |
легирован- |
|
|
|
размер |
|
|||||
литья |
лов с |
tпл > 700о С, |
ный |
|
|
|
отливки, |
|
|||||
|
tпл < 700о С |
серый чугун |
чугун, сталь |
|
||
|
мм |
|
|
|
|
|
|
|
|
|
|
|
|
Под давлением |
|
IT 11 - IT 13, |
IТ 12 - IT 14, |
|
|
|
в металличе- |
> 100 |
Ra = 0,63 |
— |
|
|
|
Ra = 1,25 мкм |
|
|||||
ские формы |
|
мкм |
|
|
|
|
|
|
|
|
|
||
|
|
|
|
|
|
|
По выплав- |
|
IT 12 - IT 14, |
IT 13 - IT 15; |
IT 14 - IT 15, |
|
|
ляемым |
> 100 |
|
||||
Ra = 2,5 мкм |
Ra = 20 мкм |
Rz = 20 мкм |
|
|
||
моделям |
|
|
||||
|
|
|
|
|
|
|
|
|
|
|
|
|
|
В кокиль, |
100…630 |
IT 13 - IT 17, |
IT 14 - IT 17; |
IТ 15 - IТ 18; |
|
|
под давлением |
Rz = 20 мкм |
Rz = 40 мкм |
Rz = 80 мкм |
|
|
|
|
|
|||||
|
|
|
|
|
|
|
В песчаные |
|
|
|
|
|
|
формы, |
|
|
|
|
|
|
отверждаемые |
630…4000 |
IT 14 - IT 18, |
IТ 15- IT 19; |
IT 16 - IT 20, |
|
|
вне |
|
Rz = 40 мкм |
Rz = 80 мкм |
Rz = 80 мкм |
|
|
контакта |
|
|
|
|
|
|
с оснасткой; |
|
|
|
|
|
|
центробежное |
|
|
|
|
|
|
|
|
|
|
|
|
|
Примечание. В таблице приведены максимальные значения шерохова- |
|
|||||
тости. |
|
|
|
|
|
|
Заливка металла в кокиль производится до заполнения обеих прибылей. Для извлечения отливки кокиль на цапфах поворачивают на 180° и отливка вместе со стержнями вытряхивается из кокиля.
60