
3187
.pdf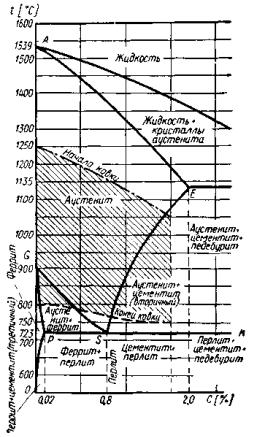
ратурный интервал обработки сужается. Особенно резко при этом снижается температура начала обработки.
Рис. 3.2. Температурный интервал ковки углеродистых сталей по диаграмме состояния железо-углерод
При нагреве металлов и сплавов выше температуры начала горячей обработки начинается интенсивный рост аустенитного зерна. Благодаря этому структура становится крупнозернистой, и происходит понижение ее пластических свойств. Сталь с крупнозернистой структурой получается при пе-
91
регреве. Перегрев является дефектом и его можно устранить отжигом или нормализацией.
При дальнейшем повышении температуры нагрева происходит расплавление легкоплавких составляющих, расположенных по границам зерен. Окисление этих границ кислородом, содержащимся в рабочем пространстве печи, вызывает явление, называемое пережогом. Пережог металла — неисправимый брак, так как при этом наступает полная потеря пластичности металла.
Металл нагреваемой заготовки, соприкасаясь и химически взаимодействуя с печными газами, содержащими кислород (водяной пар и углекислый газ), окисляется и обезуглероживается. При этом на поверхности металла образуется окалина, состоящая из окислов железа. Кроме печных газов на количество образующейся окалины влияют температура нагрева, химический состав металла заготовки и отношение ее поверхности к объему. С повышением отношения поверхности заготовки к ее объему количество окалины возрастает. С увеличением содержания углерода в стали количество окалины при нагреве уменьшается. Уменьшают окалинообразование и некоторые химические элементы — алюминий, хром, кремний. Кроме прямых убытков от угара металла, достигающего 3% при нагреве в пламенных печах, окалина является весьма твердым веществом, увеличивающим износ инструмента. Толщина обезуглероженного слоя металла достигает 1,5…2 мм, что вынуждает увеличивать припуски на механическую обработку для его удаления.
Нагрев должен обеспечить равномерное распределение температуры по сечению и длине заготовки, минимальное обезуглероживание поверхностного слоя и минимальное образование окалины.
Холодные слитки и заготовки, загруженные в печь, нагреваются неравномерно. Вначале нагреваются их наружные слои, а затем по мере выдержки в печи они прогреваются по всему сечению. Наружные слои, нагретые до более высокой температуры, расширяются больше, чем внутренние, поэтому
92
в металле появляются температурные напряжения растяжения. Если температурные напряжения превышают предел прочности металла, то в нем возникают трещины.
Во избежание образования трещин, металл необходимо нагревать с определенной скоростью. Скорость нагрева до заданной температуры зависит от теплопроводности и теплоемкости металла, размеров и формы заготовок, характера расположения заготовок в печи.
Температура окончания процесса горячей обработки давлением не должна быть слишком низкой, так как происходящий при этом процесс упрочнения и снижения пластичности может вызвать образование трещин. Эта температура не должна быть и чрезмерно высокой вследствие опасности получения крупнозернистой структуры.
Если сталь или сплав имеет структурные и фазовые превращения, то в области перекристаллизации при термической обработке зерно можно измельчить. Если же такие превращения отсутствуют, то зерно остается таким, каким оно было получено после обработки давлением.
В зависимости от сечения и химического состава заготовки ее охлаждение после горячей обработки давлением может производиться либо на воздухе, либо медленно в теплоизолирующих средах (песке, шлаке и др.) или в печи. Заготовки крупного сечения и заготовки из легированных сталей, предрасположенных к образованию макро- и микротрещин водородного происхождения, охлаждают медленно.
3.3. Нагревательные устройства
Оборудование, применяемое для нагрева заготовок перед обработкой давлением, подразделяется на нагревательные печи и электронагревательные устройства.
К нагревательным печам относят оборудование, в котором теплота к заготовке передается конвекцией и излучением из нагревательной камеры. Пол, стены и свод печей выполняются из огнеупорных материалов. Необходимую температуру
93
(до 1300 °С и более) в печах получают сжиганием газообразного или жидкого топлива либо с помощью электрических нагревателей. По принципу действия печи подразделяются на камерные и методические.
К камерным относят печи, имеющие одинаковую температуру по всему рабочему пространству. Загрузку и выгрузку заготовок производят по мере необходимости. Такие печи обычно имеют одно окно.
Методические печи, как правило, вытянутые в одном направлении, имеют загрузочное окно, в районе которого устанавливается относительно невысокая температура, удлиненную камеру печи, по длине которой температура повышается, вплоть до конечной, вблизи у окна выгрузки. Нагреваемые заготовки перемещаются с установленной скоростью от загрузочного до окна выгрузки. В методических печах пламенного типа поток нагревающих газов направлен навстречу движению заготовок, что способствует их равномерному нагреву.
В электронагревательных устройствах теплота выделяется непосредственно в самой заготовке в виде теплоты сопротивления при пропускании через нее большой силы тока либо при возбуждении в ней вихревых токов в специальных индукционных печах.
При нагревании заготовки проходящим током основной частью является трансформатор, обеспечивающий необходимую силу тока. Сила тока выбирается исходя из рода материала, сечения нагреваемой заготовки и необходимой скорости нагрева.
Основной частью установки для индукционного нагрева, являются генератор повышенной частоты (50…8000 Гц) и собственно индуктор, выполненный в виде многовитковой спирали из медной круглой или прямоугольной трубы. Внутрь спирали помещается корпус камеры, выполненный из огнеупорного диэлектрического материала. Нагреваемые заготовки помещаются в корпус и перемещаются в нем с помощью толкателя.
94
В заготовках, находящихся в переменном магнитном поле, возникают вихревые токи, сосредоточенные, в основном, в поверхностных слоях заготовки. Толщина нагреваемого слоя зависит от частоты тока; чем она выше, тем более поверхностным и интенсивным будет нагрев. Поэтому для разогрева массивных заготовок иногда применяют промышленную частоту (50 Гц). Глубина прогрева в этом случае может достигать 25…30% от толщины заготовки. Прогрев по всему сечению, т. е. центральной части заготовки, происходит за счет теплопроводности. За время прохождения заготовки от входа в индуктор до выхода должен быть обеспечен нагрев до необходимой температуры.
Нагревательные устройства имеют преимущества перед печами: высокая скорость нагрева (в 10…15 раз выше, чем в печах), почти полное отсутствие окалины (в 4…5 раз меньше), удобство в работе, легкая автоматизация, экологичность. Серьезными их недостатками являются ограничения по габаритам нагреваемых заготовок, требования их постоянного сечения, необходимость для каждого типа и размера заготовки иметь соответствующий индуктор. Кроме того, КПД индукторов относительно невелик.
3.4.Прокатное производство
3.4.1.Сущность процесса
Прокатке подвергают до 90 % всей выплавляемой стали и большую часть цветных металлов. При прокатке металл пластически деформируется вращающимися валками. Взаимное расположение валков и заготовки, форма и число валков могут быть различными. Выделяют три основных вида прокатки: продольную, поперечную и поперечно-винтовую.
При продольной прокатке (рис. 3.3, а) заготовка 2 деформируется между двумя валками 1, вращающимися в разные стороны, и перемещается перпендикулярно к осям валков.
95

Рис. 3.3. Основные виды процессов прокатки
При поперечной прокатке (рис. 3.3, б) валки 1, вращаясь в одном направлении, придают вращение заготовке 2 и деформируют ее.
При поперечно-винтовой прокатке (рис. 3.3, в) валки 1 расположены под углом и сообщают заготовке 2 при деформировании вращательное и поступательное движения.
В процессе прокатки металл непрерывно втягивается в зазор между валками под действием сил трения между металлом и валками. Для осуществления процесса прокатки необходима определенная величина этих сил трения. Так, при наиболее распространенной продольной прокатке на заготовку со стороны валков действуют нормальные силы N и сила трения Т (рис. 3.3, а). Спроектировав эти силы на горизонтальную ось, можно записать условие захвата металла валками (по отношению к одному валку, так как система симметрична):
N sin α < T cos α.
Угол α называется углом захвата. Выразив силу трения как Т = fN, где f — коэффициент трения, и подставив это выражение в условие захвата, получим
sin α < f cos α или f > tg α.
96
Таким образом, для осуществления захвата металла валками необходимо, чтобы коэффициент трения между валками и заготовкой был больше тангенса угла захвата.
При горячей прокатке стали гладкими валками угол захвата равен 15…24°, при холодной — 3…8°. При установившемся процессе прокатки коэффициент трения может быть примерно вдвое меньше.
В процессе прокатки уменьшается толщина заготовки при одновременном увеличении ее длины и ширины. Деформацию заготовки обычно определяют относительным обжати-
ем, %:
εн = (Н0 – Н1) 100 / Н0,
где Н0 и Н1 — высота заготовки соответственно до и после прокатки.
Площадь поперечного сечения заготовки всегда уменьшается. Поэтому для определения деформации (особенно, когда обжатие по сечению различно) используют показатель, называемый вытяжкой,
μ = l / l0 = F0 / F,
где l0 и F0 — первоначальные длина и площадь поперечного сечения; l и F — те же величины после прокатки.
Вытяжка при прокатке обычно составляет 1,1…1,6 за проход, но может быть и больше.
3.4.2. Продукция прокатного производства
Форму поперечного сечения прокатанной полосы называют профилем. Совокупность форм и размеров профилей, получаемых прокаткой, называют сортаментом. Почти весь сортамент проката изготовляется в соответствии с ГОСТом. В ГОСТах на сортамент проката приведены площадь поперечного сечения, размеры, масса 1 м длины профиля и допусти-
97
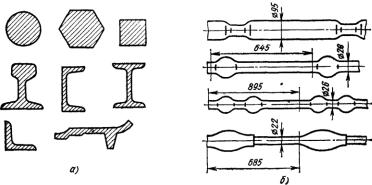
мые отклонения от номинальных размеров. Сортамент прокатываемых профилей разделяется на четыре основные группы: сортовой прокат, листовой, трубы и специальные виды проката.
Сортовой прокат (рис. 3.4, а) делят на профили простой геометрической формы (квадрат, круг, шестигранник, прямоугольник) и фасонные (швеллер, рельс, угловой и тавровый профили и т. д.). Круглую и квадратную сталь прокатывают соответственно с диаметром или стороной квадрата 5…250 мм; шестигранную — с диаметром вписанного круга 6…100 мм; полосовую — шириной 10…200 мм и толщиной 4…60 мм.
Рис. 3.4. Примеры профилей проката
Цветные металлы и их сплавы прокатывают преимущественно на простые профили — круглый, квадратный, прямоугольный.
Листовой прокат из стали и цветных металлов используют в различных отраслях промышленности. В связи с этим листовую сталь, например, делят на автотракторную, трансформаторную, кровельную жесть и т. д. Расширяется производство листовой стали с оловянным, цинковым, алюминиевым и пластмассовым покрытиями. Кроме того, листовую сталь разделяют на толстолистовую (толщиной 4…160 мм) и
98
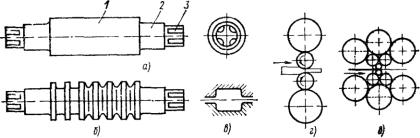
тонколистовую (толщиной менее 4 мм). Листы толщиной менее 0,2 мм называют фольгой.
Трубы разделяют на бесшовные и сварные. Бесшовные трубы прокатывают диаметром 30…650 мм с толщиной стенки 2…160 мм из углеродистых и легированных сталей, а сварные — диаметром 5…2500 мм с толщиной стенки 0,5…16 мм из углеродистых и низколегированных сталей.
K специальным видам проката относят колеса, кольца, шары, периодические профили с периодически изменяющейся формой и площадью поперечного сечения вдоль оси заготовки
(рис. 3.4, б).
3.4.3. Инструмент и оборудование для прокатки
Инструментом для прокатки являются валки, которые в зависимости от прокатываемого профиля могут быть гладкими (рис. 3.5, а), применяемыми для прокатки листов, лент и т. п., ступенчатыми, например, для прокатки полосовой стали, и ручьевыми (рис. 3.5, б) для получения сортового проката. Ручьем называют вырез на боковой поверхности валка, а совокупность двух ручьев образует калибр (рис. 3.5, в). Каждая пара ручьевых валков обычно образует несколько калибров.
Рис. 3.5. Инструмент для прокатки:
а— гладкий валок; б — ручьевой валок; в — калибр;
г— расположение валков в четырехвалковой клети;
д— то же, в 12-валковой клети
99
Валки состоят из рабочей части — бочки 1, шеек 2 и трефы 3. Шейки валков вращаются в подшипниках, которые у одного из валков могут перемещаться специальным нажимным механизмом для изменения расстояния между валками и регулирования взаимного расположения их осей.
В зависимости от назначения валки изготовляют из чугуна или стали. Мягкие валки, т. е. валки с небольшой твердостью, отливают из чугуна в земляные формы. Такие валки используют при горячей черновой прокатке стали. Твердые валки отливают из чугуна в металлические формы, либо изготовляют из кованой стали. Эти валки используют при прокатке листов и сортового металла. Особо твердые валки применяют для холодной прокатки листов. Их изготовляют из кованой стали, легированной хромом, никелем, молибденом и некоторыми другими элементами. Для обеспечения высокой твердости такие валки подвергают поверхностной закалке.
Листовую, полосовую сталь и ленту прокатывают в гладких цилиндрических валках (рис. 3.5, а). Сортовую сталь прокатывают в ручьевых валках (рис. 3.5, б). Вырезы-ручьи в паре валков образуют калибр.
Калибры бывают открытые и закрытые (рис. 3.5, в). В зависимости от назначения калибры подразделяют на обжимные, черновые и чистовые. Обжимные или вытяжные калибры (прямоугольные, ромбические, квадратные и овальные) предназначены для уменьшения сечения прокатываемого металла. Черновые, или подготовительные, калибры используют для постепенного приближения поперечного сечения прокатываемой заготовки к готовой форме. Чистовые калибры имеют форму, которая обеспечивает получение соответствующего готового профиля.
Комплект прокатных валков со станиной называют рабочей клетью; последняя вместе со шпинделем для привода валков, шестеренной клетью для передачи вращения с одного на два вала, редуктором, муфтами и электродвигателем образуют рабочую линию стана.
100