
3187
.pdfПоверхности Rо и Roп называются, соответственно, обрабатываемой поверхностью заготовки и обработанной поверхностью детали (см. рис. 5.9).
В процессах точения, сверления, фрезерования и шлифования главное движение и движение подачи выполняются одновременно, а в процессах строгания, хонингования движение подачи выполняется после главного движения.
5.1.9.Параметры технологического процесса резания
Косновным параметрам режима резания относятся скорость главного движения резания, скорость подачи и глубина резания.
Скорость главного движения резания (или скорость резания) определяется максимальной линейной скоростью главного движения режущей кромки инструмента. Эта скорость выражается в м/с.
Если главное движение резания вращательное, как при точении, сверлении, фрезеровании и шлифовании, то скорость резания будет определяться линейной скоростью главного движения наиболее удаленной от оси вращения точки режущей кромки — максимальной линейной скоростью главного движения (см. рис. 5.10):
v= ω D/2,
где D — максимальный диаметр обрабатываемой поверхности заготовки, определяющий положение наиболее удаленной от оси вращения точки режущей кромки, м; ω — угловая скорость, рад/с.
Выразив угловую скорость ω через частоту вращения шпинделя станка, получим: v = πnD.
При строгании и протягивании скорость резания v определяется скоростью перемещения строгального резца и протяжки в процессе резания относительно заготовки.
221
При хонинговании и суперфинишировании скорость резания определяется с учетом осевого перемещения (см. рис. 5.10, е, ж) инструмента.
Скорость резания оказывает наибольшее влияние на производительность процесса, стойкость инструмента и качество обработанной поверхности.
Подача инструмента определяется ее скоростью vs. В технологических расчетах параметров режима при точении, сверлении, фрезеровании и шлифовании используется понятие подачи на один оборот заготовки So и выражается в мм/об. Подача на оборот численно соответствует перемещению инструмента за время одного оборота: So = vs / n.
При строгании подача определяется на ход резца. При шлифовании подача может указываться на ход или двойной ход инструмента. Подача на зуб при фрезеровании определяется числом зубьев Z инструмента и подачей на оборот:
Sz = So / Z.
Глубина резания h определяется расстоянием по нормали от обработанной поверхности заготовки до обрабатываемой, мм. Глубину резания задают на каждый рабочий ход инструмента. При точении цилиндрической поверхности глубину резания определяют как полуразность диаметров до и после обработки: h = (Dзаг - d)/2, где d — диаметр обработанной поверхности заготовки, мм.
Величина подачи и глубина резания определяют производительность процесса и оказывают большое влияние на качество обрабатываемой поверхности.
К технологическим параметрам процесса относятся геометрия режущего инструмента, силы резания, производительность обработки и стойкость инструмента.
222
5.1.10. Геометрические параметры токарных резцов
Геометрические параметры режущего инструмента определяются углами, образуемыми пересечением поверхностей головки резца, а также положением этих поверхностей и режущих лезвий относительно обрабатываемой поверхности и направлением главного движения. Указанные параметры идентичны для различных видов инструмента, что позволяет рассмотреть их на примере резца, используемого при точении.
Токарный прямой проходной резец (рис. 5.11) имеет головку — рабочую часть I и тело — стержень II, который служит для закрепления резца в резцедержателе. Головка резца образуется при заточке и имеет следующие элементы: переднюю поверхность 1, по которой сходит стружка; главную заднюю поверхность 2, обращенную к поверхности резания заготовки; вспомогательную заднюю поверхность 5, обращенную к обработанной поверхности заготовки; главную режущую кромку 3 и вспомогательную 6; вершину 4. Инструмент затачивают по передней и задним поверхностям. Для определения углов, под которыми расположены поверхности рабочей части инструмента относительно друг друга, вводят координатные плоскости (рис. 5.12).
Основная плоскость (рис. 5.12, а, 4) — плоскость, параллельная направлениям продольной и поперечной подач. Плоскость резания (рис. 5.12, а, 1) проходит через главную режущую кромку резца, касательно к поверхности резания. Главная секущая плоскость (рис. 5.12, а, 3) — плоскость, перпендикулярная к проекции главной режущей кромки на основную плоскость. Вспомогательная секущая плоскость — плоскость, перпендикулярная к проекции вспомогательной режущей кромки на основную плоскость.
Перечисленные элементы имеют и другие режущие инструменты. Кроме этих элементов, инструменты могут иметь переходную (дополнительную) режущую кромку, распола-
223
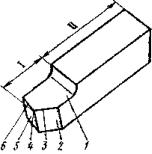
гающуюся между главной и вспомогательной режущими кромками. В этом случае рабочая часть инструмента имеет переходную заднюю поверхность
Рис. 5.11. Элементы токарного прямого проходного резца
Углы резца по передним и задним поверхностям измеряют в указанных координатных плоскостях. На рис. 5.12, а изображены координатные плоскости при точении, а на рис. 5.12, б — углы резца в статике.
Главный передний угол γ — угол между передней поверхностью и плоскостью, перпендикулярной к плоскости резания и проходящей по главной режушей кромке; главный задний угол α — угол между задней поверхностью и плоскостью резания; угол заострения β — угол между передней и задней поверхностями. Из принципа построения углов следу-
ет, что α + β + γ = π/2.
Угол наклона режущей кромки λ — угол в плоскости резания между режущей кромкой и основной плоскостью.
Углы в плане: главный угол в плане θ — угол в основной плоскости между следом плоскости резания и направлением продольной подачи; вспомогательный угол в плане θ1 — угол в основной плоскости между следом вспомогательной плоскости резания и направлением обратным направлению продольной подачи.
224
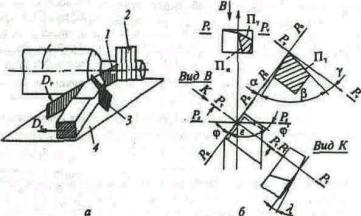
Рис. 5.12. Геометрические параметры токарного резца:
а— координатные плоскости; б — углы резца в статике;
1— плоскость резания Рп; 2 — рабочая плоскость Ps; 3 — главная секущая плоскость Рη;
4 — основная плоскость Pv
Геометрические параметры режущего инструмента оказывают существенное влияние на усилие резания, качество поверхности и износ инструмента. Так, с увеличением угла γ инструмент легче врезается в материал, снижаются силы резания, улучшается качество поверхности, но повышается износ инструмента. Угол α снижает трение инструмента о поверхность резания, уменьшая его износ, но чрезмерное его увеличение ослабляет режущую кромку, способствуя ее разрушению при ударных нагрузках.
5.1.11. Определение параметров режима резания
Параметры оптимального режима резания определяются с учетом стойкости инструмента, качества и производительности обработки. В справочной литературе приведены эмпири-
225
ческие формулы для определения параметров процесса для каждого способа механической обработки.
За оптимальный режим резания для конкретного вида обработки и детали принимается наилучшее сочетание параметров резания, обеспечивающее максимальную производительность и качество обработанной поверхности. Как правило, этот режим соответствует и наибольшей экономичности обработки.
Рассмотрим схему определения оптимального режима резания применительно к черновой обработке точением. Вначале задаются глубиной резания. Так как глубина резания не является определяющим фактором стойкости инструмента и качества поверхности, стремятся весь припуск срезать за один проход, тем самым увеличивая производительность точения. Если требования точности и возможности станка не допускают этого, то припуск срезается за два прохода. При первом (черновом) проходе снимается 80% припуска, а при чистовых проходах — остальные 20%. Затем, пользуясь нормативными справочными данными, выбирают станок, инструмент и максимальную подачу s, обеспечивающую заданную шероховатость поверхности Ra с учетом мощности станка, жесткости и динамических характеристик СПИД. После этого определяется скорость резания. Скорость главного движения резания оценивается по эмпирической формуле, связывающей все параметры обработки:
v Cv / T mhxv s yv ,
где Cv – коэффициент, характеризующий вид и условия обработки, учитывающий материал изделия и резца; xv, yv, m – показатели, зависящие от свойств обрабатываемого материала, материала резца и вида обработки.
Стойкость резца Т задается по справочным значениям, исходя из обеспечения допустимого значения износа для инструмента из выбранного материала. После вычисления ско-
226
рости резания определяется соответствующая этой скорости частота вращения шпинделя станка, м/с: n = 1000v / (60πDзаг).
Затем рассчитываются усилие резания Рz и величина прогиба заготовки z от силы Рz , после чего определяют ожидаемую точность размера. Если величина прогиба 2z > 0,3δ, где δ — заданный допуск на обрабатываемый диаметр заготовки, то расчет повторяется при новой, измененной, величине подачи. Выбранный таким образом режим обработки обеспечивает максимальную производительность точения при заданных значениях точности детали и шероховатости ее поверхности.
5.1.12. Металлорежущие станки. Классификация металлорежущих станков
Металлорежущим станком называется технологическая машина, предназначенная для размерной обработки металлических и неметаллических заготовок с целью получения деталей заданной формы и размеров с требуемой точностью и заданным качеством поверхности.
Современные металлорежущие станки — это разнообразные и совершенные рабочие машины, использующие механические, электрические и гидравлические методы осуществления движений и управления рабочим циклом, решающие самые сложные технологические задачи.
В зависимости от характера выполняемых работ станки классифицируются на группы. По классификации, разработанной Экспериментальным научно-исследовательским институтом металлорежущих станков (ЭНИМСом), все станки делятся на 9 групп:
1) токарные; 2) сверлильные и расточные; 3) шлифовальные и доводочные; 4) комбинированные; 5) зубо- и резьбообрабатывающие; 6) фрезерные; 7) строгальные, долбежные и протяжные; 8) разрезные; 9) разные.
227
Каждая из групп, в свою очередь, делится на 9 типов, характеризующих назначение станка, его компоновку, степень автоматизации, вид применяемого инструмента и т. п.
Для большинства типов станков стандартами установлены основные параметры, характеризующие размеры обрабатываемых деталей или геометрические размеры станка. Например, для токарных, круглошлифовальных и зубообрабатывающих станков основным параметром является наибольший диаметр обрабатываемой детали; для сверлильных и внутришлифовальных станков - наибольший диаметр обрабатываемого отверстия; для фрезерных и плоскошлифовальных станков — размеры рабочей поверхности стола; для поперечнострогальных и долбежных станков — наибольший ход ползуна и т д.
Однотипные станки экономически целесообразно создавать по размерным рядам. В размерный ряд входят станки подобные по кинематической схеме, конструкции и внешнему виду, но имеющие разные основные параметры-размеры. За каждым станком ряда закреплен определенный диапазон размеров обрабатываемых деталей. Для основного параметра того или иного размерного ряда установлен ряд стандартных значений, обычно в геометрической прогрессии с некоторым знаменателем θ. Так, для токарных станков принят θ = 1,25 и стандартный ряд наибольших диаметров обрабатываемой де-
тали: 100; 125; 160; 200; 250; 320; 400; 500; 630; 800; 1000; 1250; 1600; 2000; 2500; 3200; 4000; 5000; 6300 мм.
Конструкции станков размерного ряда состоят в основном из унифицированных узлов и деталей, одинаковых или подобных, что удешевляет производство станков и облегчает эксплуатацию.
Типоразмер станка характеризуется его классификационным типом и максимальным значением основного параметра — размера, выбранным из размерного ряда. Конкретное конструктивное исполнение станка данного типоразмера, предназначенного для заданных условий обработки, называ-
228
ется моделью станка. Таким образом, одному типоразмеру может соответствовать несколько различных моделей.
Станки классифицируются по степени универсальности, степени автоматизации, степени точности и по массе.
По степени универсальности (специализации) станки делят на универсальные, специализированные и специальные.
Универсальные станки (станки общего назначения) применяют для выполнения разнообразных операций при обработке деталей самой широкой номенклатуры, различных по форме и размерам. К числу универсальных относятся токарновинторезные; револьверные; вертикально- и радиальносверлильные; консольно-фрезерные; строгальные; долбежные; кругло-, внутри- и плоскошлифовальные и другие станки. Универсальные станки применяют главным образом в единичном, мелкосерийном и серийном производствах. Для них характерна частая смена обрабатываемых деталей и, следовательно, частая переналадка.
Специализированные станки предназначаются для обработки однотипных деталей сравнительно узкой номенклатуры, сходных по конфигурации, но имеющих различные размеры. Примером таких станков являются зубо- и резьбообрабатывающие станки, станки для обработки коленчатых и кулачковых валов, колец подшипников качения, труб, муфт и т. п. Специализированные станки имеют высокую степень автоматизации и используются в серийном и крупносерийном производстве при больших партиях обрабатываемых деталей, требующих редкой переналадки.
Специальные станки используют для высокопроизводительной обработки одной или нескольких почти одинаковых деталей (например, турбинных лопаток) в условиях крупносерийного и массового производства.
Применение специальных станков позволяет свести к минимуму время обработки за счет ее автоматизации и оптимизации режимов резания и конструкции инструмента.
По степени автоматизации различают простые (неавтоматизированные) станки, полуавтоматы и автоматы.
229
На простых станках механизированы только рабочие движения, сообщаемые режущему инструменту и обрабатываемой заготовке. Все же остальные, движения (установка заготовки, подвод инструмента, изменение режима резания и т. д.) выполняются рабочим вручную. Такие станки применяют в единичном, мелкосерийном и серийном производствах.
В полуавтоматах автоматизированы все движения, составляющие цикл обработки, за исключением движений, связанных с установкой заготовки и снятием обработанной детали, которые выполняются рабочим вручную.
Автоматами называются станки, на которых весь цикл обработки, включая установку заготовки и снятие обработанной детали, осуществляется автоматически. Рабочий лишь периодически загружает в станок сортовой прокат (прутки) или партии заготовок (периодическое питание автомата) и контролирует размеры и качество поверхности обработанных деталей.
Станки—автоматы и полуавтоматы могут быть с механическим или гидравлическим управлением и с ЧПУ. Первые при изменении объекта производства требуют трудоемкой переналадки и поэтому применяются только в условиях крупносерийного и массового производства. Вторые применяются в условиях производства любой серийности.
По степени точности станки делят на пять классов: нормальной Н, повышенной П, высокой В, особо высокой А точности и особо точные С (мастер-станки).
Большинство универсальных станков относится к классу Н. Эти станки предназначены для изготовления деталей с точностью 7 - 10-го квалитетов. При переходе к станку более высокого класса точности выдерживаемый допуск обрабатываемой детали ужесточается в 1,6 раза.
Станки класса П изготовляются на базе станков класса Н, но при повышенных требованиях к точности обработки ответственных деталей станка, а также к качеству его сборки и регулировки.
230