
3187
.pdfРабочие клети по числу и расположению валков могут быть двухвалковые; четырехвалковые (рис. 3.5, г), у которых два валка рабочих и два опорных; многовалковые (рис. 3.5, д), у которых также два валка рабочих, а остальные — опорные. Использование опорных валков позволяет применять рабочие валки малого диаметра, благодаря чему увеличивается вытяжка и снижается усилие деформирования.
Прокатные станы могут быть одноклетьевыми (с одной рабочей клетью) и многоклетьевыми.
Наиболее совершенные многоклетьевые станы — непрерывные, у которых рабочие клети располагают последовательно одну за другой. Прокатываемая полоса через каждую клеть проходит только один раз, т. е. число рабочих клетей этих станов равно требуемому числу проходов полосы. Расстояние между клетями обычно меньше длины прокатываемой полосы, следовательно, она прокатывается одновременно в нескольких клетях. На непрерывных станах достигается высокая производительность при полном исключении ручного труда.
По назначению прокатные станы подразделяют на станы для производства полупродукта и станы для выпуска готового проката. К первой группе относят обжимные станы для прокатки слитков в полупродукт крупного сечения (блюминги, дающие заготовки квадратного сечения с размерами сторон от 450450 до 150 150 мм, называемые блюмами, для сортового проката, и слябинги, дающие заготовки прямоугольного сечения с максимальной толщиной до 350 мм и шириной до 2300 мм, называемые слябами, для листового проката) и заготовочные для получения полупродукта квадратного сечения от 150150 до 60 60 мм, которые направляют на средне- и мелкосортные либо на проволочные станы.
К станам для производства готового проката относят сортовые, листовые, трубные и специальные. Размер блюмингов, слябингов, заготовочных и сортовых станов характеризуется диаметром бочки валков (например: блюминг 1500; сортовой стан 350); размер листовых станов — длиной бочки
101
(например: стан 3600), а размер трубопрокатных станов — наружным диаметром прокатываемых труб.
3.4.4. Производство бесшовных и сварных труб
Бесшовные трубы прокатывают диаметром 30…650 мм с толщиной стенки от 2 до 160 мм, сварные — диаметром от 5 до 2500 мм. Материалом для производства труб могут быть как углеродистые, так и легированные стали, цветные металлы.
Используются заготовки диаметром 50…60 мм и массой 0,6…3 т. Процесс прокатки состоит из двух основных операций: прошивки отверстия в слитке или заготовке на прошивном стане и прокатки прошитой заготовки на пилигримном, автоматическом реверсивном стане дуо или на непрерывном стане.
Перед прошивкой заготовку нагревают в методической печи до температуры горячей обработки давлением и направляют на прошивочный стан с двумя бочкообразными валками, оси которых расположены под углом 10…15° друг к другу (см. рис. 3.6). Таким образом, при прошивке отверстия используется принцип поперечно-винтовой прокатки.
Оба рабочих валка вращаются в одном направлении. Для удержания заготовки между рабочими валками имеются две направляющие линейки или заменяющие их холостые валки.
При вращении рабочих валков вращающаяся заготовка втягивается в зону деформации. Так как по мере продвижения заготовки зазор между валками уменьшается, то окружная скорость металла на ее поверхности возрастает. Это приводит к скручиванию заготовки, уменьшению ее диаметра и появлению в металле больших внутренних напряжений, в результате чего металл в центре заготовки доводится до состояния разрыхления и сравнительно легко прошивается оправкой.
Рассмотрим прокатку трубной заготовки, установленной на оправку, на пилигримном стане. Рабочие валки этого стана (рис. 3.7, а) вращаются в разные стороны с одинаковой скоро-
102
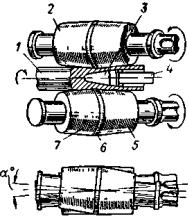
стью. При этом направление движения заготовки, вызванное валками, обратно направлению подачи заготовки. Валки имеют переменный профиль, вследствие чего размеры калибра в свету непрерывно изменяются при каждом обороте валков.
Рис. 3.6. Схема прошивки заготовки на стане косой прокатки: 1 — заготовка, 2 — валки, 3 — оправка, 4 — стержень, 5 — конус раскатки, 6 — калибровочный
пояс; 7 — конус прошивки
При максимальном размере калибра заготовка с оправкой продвигается в валки на величину подачи (положение I). При дальнейшем вращении валков размеры калибра уменьшаются и валки производят обжатие заготовки (положение II), которая вместе с оправкой перемещается назад (положение III). После того как валки сделают полный оборот, заготовку поворачивают вокруг оси на 90° и подают снова в валки для обжатия. Этот цикл повторяется до получения трубы. На станах пилигримной прокатки получают трубы диаметром 48…605 мм и выше при толщине стенки 2,25…50 мм и длине до 30 м.
Прокатку прошитых заготовок на автоматическом стане производят на неподвижной оправке в круглых калибрах (рис.
103

3.7, б). Толщина стенки трубы зависит от просвета между калибром и оправкой. При получении требуемой толщины стенки наружный диаметр трубы уменьшается. Прокатку независимо от толщины стенки выполняют за два прохода с поворотом трубы на 90° после первого прохода.
Рис. 3.7. Схемы прокатки бесшовных труб:
а — на пилигримном стане; 1 — трубная оправка; 2 — пилигримные валки; 3 — прокатываемая труба;
б — на автоматическом стане: 1 — гильза; 2 — верхний валок; 3 — оправка; 4 — стержень оправки;
в — на непрерывном стане: 1 — гильза; 2 — трубная оправка; 3 — валки
На автоматическом стане изготовляют трубы диаметром 57…400 мм при толщине стенки 3…30 мм.
Прокаткой на непрерывных станах (рис. 3.7, в) получают трубы диаметром 29…108 мм и толщиной стенки 8…12 мм из катаной заготовки диаметром 90…140 мм, прошитой на стане косой прокатки обычного типа. Прокатка производится на оправке. После прокатки и извлечения оправки трубу подогре-
104
вают и прокатывают без оправки на непрерывном редукционном стане, имеющем 10…32 клети.
Сварные трубы из низкоуглеродистых и низколегированных сталей изготавливают из прокатанных полос, называемых штрипсами, или листов, ширина которых равна длине диаметра (или половине диаметра) трубы. Процесс производства трубы включает в себя формовку плоской заготовки в трубу, сварку (печную, электрическую, газовую, высокочастотную и др.), правку, калибровку.
Печной сваркой получают трубы небольшого диаметра до 10…114 мм и толщиной 2…5 мм из низкоуглеродистой стали. Процесс включает в себя нагрев полос в газовой печи до 1300…1350 °С, формовку нагретого участка в сварочной воронке и обжатие со значительной пластической деформацией. Процесс осуществляется на непрерывных станах со скоростью до 200 м/мин.
Большое распространение при производстве труб большого диаметра для магистральных трубопроводов получил способ с применением электросварки под флюсом.
Производят сварные трубы с прямыми и спиральными швами. По первой технологии из листа формируют трубную заготовку, затем ее сваривают с наложением наружного и внутреннего швов. При производстве труб со спиральным швом в качестве исходной заготовки используют ленту, которую сворачивают по спирали в трубу нужного диаметра и затем сваривают по кромке наружным и внутренним швами. Прочность, а главное надежность, труб со спиральным швом выше, чем с прямым.
3.4.5. Производство специальных видов проката
Профили специального назначения, производимые методами прокатки, отличаются большим разнообразием. Многие из них производятся не на металлургических, а на машиностроительных предприятиях. Все их можно отнести к двум группам: периодический и специальный прокат. Как правило,
105
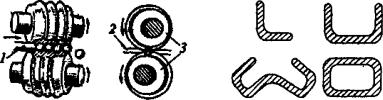
все разновидности специальных профилей производят на станах поперечной либо поперечно-винтовой прокатки. Принцип прокатки периодических профилей, служащих заготовками для других видов обработки, заключается в применении валков, периодически смещающихся по мере продвижения заготовки. Большую группу заготовок производят на станах попе- речно-винтовой прокатки: шары для подшипниковой промышленности (рис. 3.8), заготовки для шатунов двигателей, ролики, ребристые трубы, вагонные оси, цельнокатаные вагонные колеса, зубчатые колеса и др.
Рис. 3.8. Прокатка шаров: |
Рис. 3.9. Виды гнутых |
1 – заготовка; 2 - ограничите- |
профилей |
ли; 3 – прокатные валки |
|
Применение специальных технологий и оборудования для производства ряда изделий прокаткой взамен традиционно существующих методов позволяет резко увеличить производительность и повысить качество изделий.
Поперечное сечение горячекатаных профилей очень часто оказывается существенно завышено по сравнению с требованиями расчета и конструктивными особенностями изделия. Поэтому во многих случаях более рациональным является применение гнутых профилей, изготавливаемых в холодном состоянии на роликовых листогибочных станах. Заготовкой для производства гнутых профилей является горяче- и холоднокатаная полоса или лента. Процесс профилирования прокаткой является непрерывным и заключается в изменении
106
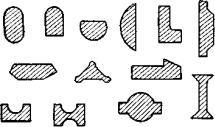
формы поперечного сечения полосы при сохранении толщины, равной толщине исходной ленточной заготовки.
Высокая производительность процесса (до 3 м/с) наряду с существенным снижением массы элементов определяет широкое применение гнутых профилей в автомобильной и авиационной промышленности, машиностроении и строительстве.
На рис. 3.9 представлены примеры закрытых и открытых гнутых профилей. Процесс профилирования прокаткой легко совмещается со сваркой, пробивкой отверстий, окраской и другими технологическими процессами.
3.5. Волочение
Волочение — процесс протягивания обрабатываемой заготовки через постепенно сужающееся отверстие в инструменте, называемом волокой или матрицей. Исходным материалом для волочения является горячекатаный сортовой прокат различного поперечного сечения (круглого, квадратного, шестигранного), проволока, трубы из стали, цветных металлов
исплавов.
Врезультате волочения поперечное сечение заготовки уменьшается, а ее длина увеличивается. Волочение применяют для получения тонкой проволоки диаметром 0,002…5 мм, тонкостенных труб, фасонных профилей (рис. 3.10), а также для калибровки, т. е. для придания точных размеров и высокого качества поверхности материала изделия.
Рис. 3.10. Профили, изготовляемые волочением
107
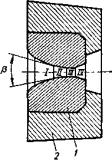
Инструмент для волочения (рис. 3.11) состоит из обоймы 2, в которую вставлена волока 1. Волока имеет по длине четыре характерные зоны: I — входную, или смазочную, с углом около 40°; II — рабочую, или деформирующую, с углом 10…24°; III — калибрующую, обычно цилиндрической формы, и IV — выходную с углом 45…60°. Угол рабочей зоны волоки зависит от вида изделия и свойств металла. Волоку обычно крепят в обойме и изготовляют из углеродистых и легированных сталей с последующей цементацией и закалкой для волочения крупных прутков и труб или из твердых сплавов и алмазов для волочения очень тонкой проволоки.
Рис. 3.11. Инструмент для волочения
На рис. 3.12 представлены схемы волочения прутков и труб. Трубы обрабатывают волочением несколькими способами: на длинной оправке, движущейся вместе с трубой (рис. 3.12, б), для значительного уменьшения толщины стенки; на неподвижной оправке (рис. 3.12, в) для уменьшения внешнего диаметра и толщины стенки; без оправки (рис. 3.12, г) для уменьшения внешнего диаметра.
Во всех случаях, для того чтобы осуществить волочение, необходимо заострить конец заготовки или трубы, продвинуть в волоку, зажать выступающий конец захватами машины и приложить соответствующее усилие. Степень деформации при волочении не превышает обычно 30…35%.
108
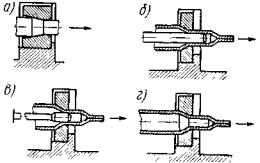
Рис. 3.12. Схемы волочения:
а — прутка; б — трубы на длинной подвижной оправке, в — трубы на короткой неподвижной оправке;
г — трубы без оправки
Обычно при волочении коэффициент вытяжки составляет 1,25…1,30 и может достигать 1,8 (например, при волочении труб на оправке). Если волочение невозможно осуществить за один проход вследствие большого обжатия, то назначают несколько последовательных проходов через ряд волок.
Для уменьшения трения (усилия волочения), а также для улучшения качества поверхности и повышения стойкости волок с поверхности заготовок удаляют окалину и ржавчину путем электрохимического или химического травления. После травления заготовки промывают водой.
На поверхность заготовок, предназначенных для последовательного волочения через несколько волок, наносят подсмазочный слой.
В качестве смазок используют минеральные и растительные масла, животные жиры, мыло, графит и некоторые эмульсии.
Волочение металла осуществляют в холодном состоянии, вследствие чего металл упрочняется. В большинстве случаев упрочнение готового изделия снимается отжигом. При многократном волочении для восстановления пластических
109
свойств металла эту операцию применяют между отдельными протяжками.
Волоку изготовляют из инструментальных сталей, металлокерамических сплавов и технических алмазов (для волочения проволоки диаметром менее 0,2 мм). Волочение производят на барабанных и цепных волочильных станах. Барабанные станы служат для волочения проволоки, труб небольшого диаметра, наматываемых в бунты. На цепных станах тянущее устройство совершает прямолинейное возвратнопоступательное движение. Такие станы применяют для волочения прутков и труб, которые нельзя наматывать в бунты.
3.6. Прессование
Прессованием называют процесс выдавливания металла из замкнутой полости через отверстие, соответствующее сечению прессуемого профиля. При прессовании металл подвергается всестороннему неравномерному сжатию и поэтому имеет весьма высокую пластичность, это позволяет обрабатывать даже малопластичные материалы. Обычно коэффициент вытяжки при прессовании составляет 10…50, а в отдельных случаях может быть значительно выше. Этим процессом изготовляют не только сплошные профили, но и полые (рис. 3.13, а). В этом случае в заготовке необходимо предварительно получить сквозное отверстие. Часто отверстие прошивают на том же прессе. В процессе прессования при движении пуансона 1 с пресс-шайбой 5 металл заготовки 2 выдавливается в зазор между матрицей 3 и иглой 4. Прессование по рассмотренным схемам называется прямым. Значительно реже применяют обратное прессование, схема деформирования которого сходна со схемой обратного выдавливания.
Исходной заготовкой при прессовании служит слиток или прокат. Состояние поверхности заготовки оказывает значительное влияние на качество поверхности и точность прессованных профилей. Поэтому во многих случаях заготовку
110