
3187
.pdf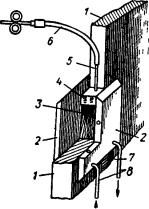
кающей между нижней соединительной планкой и электродом
5.
Рис. 4.8. Схема процесса электрошлаковой сварки
После зажигания дуги и расплавления определенного количества флюса дуга шунтируется расплавленным шлаком и самопроизвольно гаснет. Длина шлаковой ванны практически равна толщине основного металла, а ее ширина определяется зазором между свариваемыми кромками, который изменяется в пределах 20…40 мм.
Глубина шлаковой ванны выбирается в зависимости от технологических условий (состава основного металла, режима сварки) и равна 25…70 мм.
Ток подводится к шлаковой ванне от источника переменного или постоянного тока через металл изделия 1 и плавящийся электрод 5, погруженный в шлаковую ванну 4. Электрод 1 располагается в зазоре кромок по середине шлаковой ванны или совершает возвратно-поступательные движения от одного ползуна к другому. Ток к электроду подводится при помощи мундштука 6. Проходя через шлаковую ванну, ток нагревает ее до температуры, превышающей температуру плавления основного и электродного металлов. Шлак расплавляет кромки металла изделия и электрода, который пода-
171
ется в шлаковую ванну со скоростью, равной скорости его плавления.
Расплавленный металл изделия и электрода стекает на дно шлаковой ванны, образуя сварочную (металлическую) ванну 3. По мере накопления и увеличения объема жидкого металла, полученного от оплавления кромок изделия и электрода, шлаковая ванна вытесняется вверх. Вследствие этого отвод тепла в нижних слоях жидкого металла сварочной ванны становится больше притока из шлаковой ванны, что вызывает кристаллизацию металла и образование шва 7, соединяющего кромки свариваемого изделия.
Для того чтобы жидкий шлак не переливался через края ползунов, они передвигаются вместе с механизмом подачи электродной проволоки со скоростью подъема уровня шлаковой ванны.
Процесс электрошлаковой сварки применяют для сварки углеродистых конструкционных, легированных и высоколегированных сталей, чугуна и титана. При этом сварка продольных швов может выполняться одним или несколькими проволочными и пластинчатыми электродами.
Электрошлаковая сварка является производительным процессом, позволяющим сваривать за один проход изделия толщиной до 2 м. Сварку производят без скоса кромок.
Высокие прочностные показатели электрошлаковой сварки позволяют широко использовать ее при изготовлении сварно-литых, сварно-кованых и сварно-прокатных конструкций.
4.4.9. Газовая сварка
При сварке место соединения нагревают до расплавления высокотемпературным газовым пламенем (рис. 4.9). При нагреве газосварочным пламенем 4 кромки свариваемых заготовок 1 расплавляются, а зазор между ними заполняется присадочным металлом 2, который вводят в пламя горелки 3 из-
172
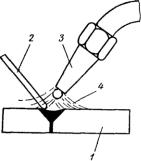
вне. Газовое пламя получают при сгорании горючего газа в атмосфере технически чистого кислорода.
Рис. 4.9. Схема газовой сварки
Кислород, используемый для сварочных работ, поставляют к месту потребления в стальных баллонах под давлением 15 МПа. Баллоны окрашивают в голубой цвет с черной надписью «Кислород». Средняя жидкостная вместимость баллона 40 дм3. При давлении 15 МПа он вмещает 6000 дм3 кислорода.
Для снижения давления газа на выходе из баллона и поддержания постоянной величины рабочего давления применяют газовые редукторы. Кислородные редукторы понижают давление от 15 до 0,1 МПа, а ацетиленовые — от 1,6 до 0,02 МПа. Редукторы, применяемые в сварочной технике, обычно имеют два манометра, один из которых измеряет давление газа до входа в редуктор, второй — на выходе из него.
К сварочной горелке кислород от редуктора подают через специальные резиновые шланги.
Ацетилен взрывоопасен при избыточном давлении свыше 0,175МПа, хорошо растворяется в ацетоне (в одном объеме ацетона при давлении 0,15 МПа растворяется 23 объема ацетилена) Последнее свойство используют для его безопасного хранения в баллонах.
Ацетиленовые генераторы могут быть различных систем и размеров, их различают по способу взаимодействия воды и
173
карбида кальция, по давлению выходящего газа, по производительности
Ацетиленовые генераторы взрывоопасны и нуждаются в специальном обслуживании. При работе одного-двух сварочных постов и в полевых условиях целесообразно использовать баллонный ацетилен. Ацетиленовые баллоны окрашивают в белый цвет и делают на них красной краской надпись «Ацетилен». Давление ацетилена в баллоне 1,5 МПа. В баллоне находятся пористая масса (активированный уголь) и ацетон. Растворение ацетилена в ацетоне позволяет поместить в малом объеме большое количество ацетилена. Растворенный в ацетоне ацетилен пропитывает пористую массу и становится безопасным.
Газосварочные горелки используют для образования газосварочного пламени. В промышленности наиболее распространена инжекторная горелка, так как она более безопасна и работает на низком и среднем давлениях.
Горелки этого типа имеют сменные наконечники с различными диаметрами выходных отверстий инжектора и мундштука, что дозволяет регулировать мощность ацетиленокислородного пламени. Обычно горелки имеют семь номеров сменных наконечников.
Для газовой сварки сталей присадочную проволоку выбирают в зависимости от состава сплава свариваемого металла. Для сварки чугуна применяют специальные литые чугунные стержни; для наплавки износостойких покрытий — литые стержни из твердых сплавов. Для сварки цветных металлов и некоторых специальных сплавов используют флюсы, которые могут быть в виде порошков и паст.
При газовой сварке заготовки нагреваются более плавно, чем при дуговой; это и определяет основные области ее применения:
для сварки металлов малой толщины (0,2…3 мм); легкоплавких цветных металлов и сплавов; для металлов и сплавов, требующих постепенного нагрева и охлаждения, например инструментальных сталей, чугуна, латуней; для пайки и на-
174
плавочных работ; для подварки дефектов в чугунных и бронзовых отливках.
4.4.10. Плазменная сварка
Плазменная струя, применяемая для сварки, представляет собой направленный поток частично или полностью ионизированного газа, имеющего температуру 10 000…20 000 °С. Плазму получают в плазменных горелках, пропуская газ через столб сжатой дуги. Дуга горит в узком канале сопла горелки, через который продувают газ. При этом столб дуги сжимается, что приводит к повышению в нем плотности энергии и температуры. Газ, проходящий через столб дуги, нагревается, ионизируется и выходит из сопла в виде высокотемпературной плазменной струи. В качестве плазмообразующих газов применяют азот, аргон, водород, гелий, воздух и их смеси. Газ выбирают в зависимости от процесса обработки и вида обрабатываемого материала.
Применяют два основных плазменных источника нагрева: плазменную струю, выделенную из столба косвенной дуги, и плазменную дугу, в которой дуга прямого действия совмещена с плазменной струѐй. Соответственно применяют две схемы плазменных горелок.
Плазменная струя представляет собой независимый источник теплоты, позволяющий в широких пределах изменять степень нагрева и глубину проплавления поверхности заготовок. Тепловая мощность плазменной струи ограничена и ее применяют для сварки и резки тонких металлических листов и неэлектропроводных материалов, а также напыления тугоплавких материалов на поверхность заготовок.
Плазменная дуга, обладающая большей тепловой мощностью по сравнению с плазменной струѐй, имеет более широкое применение при обработке материалов. Ее используют для сварки высоколегированной стали, сплавов титана, никеля, молибдена, вольфрама и других материалов. Плазменную дугу применяют для резки материалов, особенно тех, резка
175
которых другими способами затруднена, например меди, алюминия и др. С помощью плазменной дуги наплавляют тугоплавкие материалы на поверхность заготовок.
Плазменной дугой можно сваривать металл толщиной до 10 мм без разделки кромок и применения присадочного металла. При этом снижается тепловое влияние дуги на свариваемый металл и уменьшаются сварочные деформации. Вовторых, плазменная дуга обладает более высокой стабильностью горения, что обеспечивает повышенное качество сварных швов. Это позволяет выполнять так называемую микроплазменную сварку металла толщиной 0,025…0,8 мм на токах
0,5…10 А.
4.4.11. Электронно-лучевая сварка
Движение электронов в сварочной установке происходит
вглубоком вакууме. Поэтому установка включает в себя герметичную камеру с системой откачивающих насосов.
Узкий шов, незначительные деформации, малые размеры зоны термического влияния, хорошая защита металла от взаимодействия с газами, экономичность и возможность автоматизации способствовали быстрому прогрессу электроннолучевой сварки.
Для сварки крупногабаритных конструкций были созданы установки с местным вакуумированием или выводом луча
ватмосферу. Наиболее рационально применение электроннолучевой сварки в промышленности в следующих случаях:
1.Сварка изделий из тугоплавких активных металлов.
2.Сварка с минимальными деформациями и зоной термического влияния.
3.Сварка в труднодоступных местах, узких щелях.
4.Соединение разнородных металлов. Меньшее значение сварочных напряжений при электронно-лучевой сварке благоприятно сказывается на уменьшении склонности к образованию трещин при сварке разнородных металлов.
176
5.Сварка деталей малых толщин. Возможность тонкого регулирования мощности и диаметра электронного луча, небольшое давление его на сварочную ванну позволяют соединять детали толщиной в десятые и сотые доли миллиметра, что широко используется при изготовлении изделий электронной техники.
6.Сварка в космосе. Вакуум космического пространства может быть в перспективе использован для автоматической и ручной электронно-лучевой сварки отдельных деталей, узлов, при сборке космических платформ и различных ремонтных работах.
Недостатки электронно-лучевой сварки, заключаются в необходимости, как правило, использования камер, ограничивающих размеры свариваемых деталей; наличия рентгеновского излучения, которое должно поглощаться стенками камеры и требует периодического контроля; сложности и высокой стоимости оборудования.
4.4.12. Лазерная сварка
Лазерная сварка впервые стала применяться в радиоэлектронике при изготовлении электронных приборов. Для сварки использовались лазеры с твердым рабочим телом, работающие в импульсном режиме. Имея сравнительно небольшую мощность, низкий КПД, подобные лазерные установки не могли найти применения для изготовления конструкций. Однако создание мощных газовых лазеров непрерывного действия, имеющих более высокий КПД, чем твердотельные, внесло существенные коррективы в развитие лазерной сварки, в том числе в расширение использования ее в промышленности.
При выборе лазерной сварки необходимо учитывать, что она обеспечивает высококонцентрированный нагрев, а размеры самого пятна соответствуют диаметру не более десятых долей миллиметра. Поэтому лазерная сварка позволяет получать швы с минимальным расплавлением металла, снижает
177
напряжения и деформации в сварных конструкциях по сравнению с другими способами сварки.
Импульсной лазерной сваркой сваривают чаще всего между собой проволоку или проволоку с более массивными деталями, при этом лазерный луч позволяет вести сварку без зачистки контактов от изоляции, что увеличивает производительность сварки.
Непрерывная лазерная сварка металлов значительных толщин производится газовыми лазерами. При сварке непрерывным лазерным лучом большой мощности приходится устранять экранирующее влияние ионизированного облака, которое возникает при взаимодействии лазерного луча с атмосферой и испаряющимся металлом. Облако рассеивает луч и препятствует нагреву металла сварочной ванны. Устраняют облако, сдувая струѐй газа, чаще всего аргона, направляя ее перпендикулярно оси луча. Одновременно инертный газ защищает металл от окисления. Применение для защиты вместо аргона гелия или смеси гелия с водородом увеличивает проплавление лазерным лучом, но более легкий, чем аргон, гелий плохо вытесняет облако плазмы.
Непрерывная сварка лазером обеспечивает значительно большие скорости сварки по сравнению с импульсной.
4.5. Термомеханические методы сварки 4.5.1. Контактная сварка
Контактная сварка относится к одному из наиболее распространенных видов сварки. Различают несколько способов контактной сварки: стыковая, точечная, шовная.
Стыковая сварка. Стыковая сварка является разновидностью контактной сварки, при которой соединение осуществляется по всей поверхности соприкосновения свариваемого изделия.
При стыковой сварке детали 3 (рис. 4.10) закрепляют в зажимах (электродах) стыковой машины. Зажим 4 установлен на подвижной плите 5, перемещающейся в направляющих станины. Зажим 2 укреплен на неподвижной плите 1. Вторич-
178
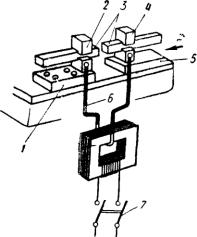
ная обмотка сварочного трансформатора соединена с зажимами машины гибкими шинами 6. Питание трансформатора осуществляется от сети переменного тока через включающее устройство 7. Перемещение плиты и сжатие свариваемых деталей осуществляется механизмом осадки Р.
Рис. 4.10. Схема стыковой машины
Стыковую сварку с разогревом кромок деталей до пластического состояния называют сваркой сопротивлением, а при разогреве кромок деталей до оплавления — сваркой оплавлением.
При сварке сопротивлением детали, зажатые в электродах машины, сжимаются небольшим усилием, обеспечивающим образование физического контакта свариваемых поверхностей. Затем включается ток, металл разогревается до пластического состояния и производится осадка, сопровождающаяся пластическими деформациями и образованием активных центров взаимодействия. В результате образуется соединение, характерное для процессов сварки в твердой фазе.
Сварку сопротивлением применяют для деталей малого сечения (диаметром до 20 мм), так как при сварке стержней
179
большого диаметра наблюдается их неравномерный нагрев по сечению.
При сварке сопротивлением требуется тщательная подготовка свариваемых поверхностей (шлифовка) с обеспечением плотного прилегания одной поверхности к другой.
Сварку оплавлением успешно используют для элементов с малым периметром (круг, квадрат) и элементов с большим периметром (тонкостенные трубы, листы, угольники и т. д.).
При этом способе сварки различают сварку прерывистым и непрерывным оплавлением. При прерывистом оплавлении зажатые детали под током приводятся в кратковременное соприкосновение и вновь разводятся на небольшое расстояние. При разведении деталей между их торцами происходит электрический разряд, сопровождающийся оплавлением торцов.
Замыкания и размыкания сварочной цепи повторяются до появления на контактируемых поверхностях тонкого защитного слоя жидкого металла. Затем включается механизм осадки. Сварку прерывистым оплавлением используют в тех случаях, когда возникает необходимость в предварительном подогреве свариваемых деталей (для сплавов, склонных к закалке).
При непрерывном оплавлении происходит энергичный нагрев металла, непосредственно прилегающего к стыку. После образования тонкого защитного слоя жидкого металла на торцах деталей благодаря непрерывному оплавлению и последующему сдавливанию происходит образование сварного соединения так же, как и при прерывистом оплавлении.
Способ непрерывного оплавления удобен, главным образом, для массового производства однотипных деталей.
Сварка оплавлением имеет ряд преимуществ перед сваркой сопротивлением: достигается более высокое качество соединения, поверхности деталей не требуют шлифовки; свариваются детали с сечением сложной формы, а также детали с различными сечениями; легко свариваются разнородные ме-
180