
3187
.pdfриной реза 0,015…0,4 мм при наибольшей глубине обработки 3 мм.
ЭЛО обеспечивает высокую точность и малую шероховатость обработанной поверхности. Так, шероховатость составляет: при сверлении отверстий — Ra = 0,4…1,6 мкм; контурной резке - 0,8…20 мкм, а точность получаемых отверстий составляет ~1 % от диаметра.
К недостаткам метода относятся: необходимость использования вакуумной среды при обработке любых материалов; ограниченный круг выполняемых операций; высокая стоимость высоковольтного и вакуумного оборудования.
5.2.2. Физико-химические способы обработки
Анодно-механическая обработка является процессом воздействия на металл, основанным на электрохимическом растворении последнего с его механическим удалением; дополнительно может иметь место еще и электроэрозионное разрушение. Принципиальная схема процесса обработки показана на рис. 5.29. При сближении электродов 3 (обрабатываемое изделие) и 1 (инструмент) и при наличии между ними электролита (рабочей жидкости) 2 во время прохождения тока происходит разрушение электрода, соединенного с положительным источником тока (анодом). Это разрушение при низких плотностях тока происходит в виде анодного растворения металла, а при высоких плотностях в виде его электроэрозионного разрушения. Образующиеся продукты распада 4 плохо проводят ток и изолируют один электрод от другого. Для удаления их осуществляют движение электрода 1 (инструмента) с небольшим усилием. В этом случае процесс протекает непрерывно, обнажающийся материал продолжает разрушаться, и требуемая обработка осуществляется независимо от его твердости.
Процесс анодно-механической обработки зависит от электрического режима (плотности тока, напряжения) и механических параметров (давления на обрабатываемую поверх-
271
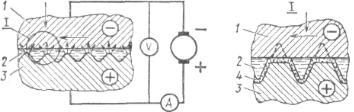
ность, скорости движения инструмента). На рисунке (см. выноску I) показана одна из предполагаемых схем процесса.
Рис. 5.29. Принципиальная схема анодно-механической установки и процесса обработки
Электролитический режим определяет производительность процесса и качество обработанной поверхности. Напряжение источника тока обычно составляет 14…28 В, плотность тока в А/см2 колеблется от десятых долей на чистовых операциях до нескольких сотен на черновых.
Скорость перемещения инструмента относительно обрабатываемой поверхности влияет на скорость и степень нагрева поверхностного слоя металла заготовки и соответственно на его структурные изменения, а также на шероховатость поверхности.
Наилучший состав рабочей жидкости — раствор жидкого стекла (силиката натрия) в воде.
Анодно-механическая обработка характеризуется: малым износом электрода-инструмента относительно электродазаготовки, обычно не превышающим 20…30% на грубых и 2…3% на чистовых режимах; высокой производительностью на грубых режимах, достигающей 35…100 мм3/с при шероховатости поверхности Rz = 500…600 мкм, и малой шероховатостью поверхности на мягких режимах, достигающей Rz < 1 мкм при небольшой производительности (около 0,01 мм3/с).
На рис. 5.30, а показана схема анодно-механичсского долбления, а на рис. 5.30, б — схема анодно-механической резки металлов. Долблением обрабатывают отверстия разно-
272

образной формы в деталях из твердого сплава и закаленной стали твердостью HRC 60…65.
Рис. 5.30. Схемы анодно-механического долбления (а)
ирезки (б): 1 — электрод-инструмент; 2 - рабочая жидкость; 3 — обрабатываемая заготовка
Электрохимическая обработка материалов основана на химических процессах, возникающих в результате прохождения электрического тока через цепь, образованную проводниками (электродами) и находящейся между ними проводящей ток жидкостью (электролитом). При электрохимической обработке происходит растворение и удаление некоторых количеств металла с обрабатываемой заготовки и их переход в неметаллическое состояние (химические соединения) (рис.
5.31, а).
Поддержание заданной плотности тока — одно из важнейших условий правильного ведения процесса. Скорость растворения находится в прямой зависимости от плотности тока.
Большинство материалов хорошо обрабатываются на установках, питаемых постоянным током. Однако в некоторых случаях, например при обработке нержавеющей стали, целесообразно применение импульсного тока.
Наиболее распространен в качестве электролита раствор хлористого натрия ввиду его низкой стоимости и длительной работоспособности.
273
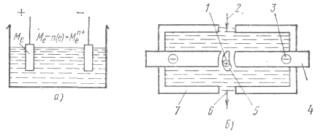
Рис. 5.31. Электрохимическая обработка (принципиальные схемы): а - схема процесса; б — схема обработки ;
1 — подвод тока к детали; 2 — подвод электролита; 3 — подвод тока к катодам; 4 - профильные катоды; 5 - обрабатываемая деталь; 6 — отвод электролита; 7 — корпус камеры
Электрохимическая размерная обработка характеризуется: малой шероховатостью обработанной поверхности, высокой производительностью, достигающей 1000 мм3/с, большой энергоемкостью процесса — 1000 А-ч на 1 кг снятого металла. Метод используется в основном при образовании отверстий и полостей, при профилировании и формообразовании копированием, для удаления заусенцев и грата, при резке и долблении. На рис. 5.31, б приведена принципиальная схема электрохимической обработки турбинных лопаток.
274
ЗАКЛЮЧЕНИЕ
Данное учебное пособие содержит сведения по курсу «Технологические процессы машиностроительного производства», которые соответствуют современным рациональным и распространенным в промышленности прогрессивным методы формообразования заготовок и деталей машин.
Заготовка является объектом машиностроительного производства, из которой посредством механической, термической, электро-физико-химической и упрочняющей обработки осуществляется изготовление детали, включающее в себя изменение размеров, формы и расположения поверхностей, формирование физико-механических и микрогеометрических свойств поверхностного слоя (ГОСТ 3.1109-82). Понимание всех этих вопросов при создании конструкций машин и приборов, возможность обеспечения на практике их заданных характеристик и надежности работы с учетом экономических показателей позволит инженеру успешно решать производственные задачи. Для этого он должен обладать глубокими технологическими знаниями.
Данная работа будет полезна для студентов машиностроительных специальностей для понимания в дальнейшем тех задач, которые будут решаться в специальных дисциплинах.
275
БИБЛИОГРАФИЧЕСКИЙ СПИСОК
1.Афонькин М.Г., Магницкая М.В. Производство заготовок в машиностроении. – Л.: Машиностроение, Ленингр.
отд-ние, 1987. – 256 с.
2.Горбунов Б.И. Обработка металлов резанием, металлорежущий инструмент и станки. Учеб. Пособие для студентов немашиностроительных специальностей вузов. – М.: Машиностроение, 1981. – 287 с.
3.Лахтин Ю.М. Материаловедение. – М.: Машино-
строение, 1993. – 448 с.
4.Материаловедение и технология металлов: Учеб. для студентов машиностроит. спец. вузов / Г.П. Фетисов, М.Г. Карпман, В.М. Матюнин и др.; Под ред. Г.П. Фетисова. – М.:
Высш. шк., 2001. – 638 с.
5.Справочник технолога-машиностроителя: В 2 т. /Под ред. А.Г. Косиловой и Р.К. Мещерякова. – М.: Машинострое-
ние, 1985. Т. 1 - 656 с.
6.Технология конструкционных материалов: Учебник для машиностроит. спец. вузов / А.М. Дальский, И.А. Арутюнова, Т.М. Барсукова и др.; Под общ. ред. А.М. Дальского. – М.: Машиностроение, 1985. – 448 с.
7.Технология металлов и материаловедение / Б.В. Кнорозов, Л.Ф. Усова, А.В. Третьякова и др. – М.: Металлургия,
1987. – 800 с.
276
ОГЛАВЛЕНИЕ
Введение…………………………………………………...3
1.Основы металловедения……………………………….4
1.1.Кристаллические решетки металлов……………..4
1.2.Реальное строение металлических кристаллов….5
1.3.Анизотропия кристаллов………………………….7
1.4.Кристаллизация металлов…………………………7
1.5.Аллотропия (полиморфизм) металлов…………..10
1.6.Кристаллическое строение сплавов……………..11
1.7.Свойства металлов и сплавов……………………12
1.8.Железо и его сплавы……………………………...15
1.8.1.Фазы в железоуглеродистых сплавах…….16
1.8.2.Диаграмма состояния железо — цементит.17
1.8.3.Применение диаграммы Fe—Fe3C………..19
1.8.4.Основные виды термической обработки стали………………………………………...20
1.8.5.Поверхностная закалка стали……………...25
1.8.6.Химико-термическая обработка…………..26
1.8.7.Диффузионное насыщение сплавов металлами и неметаллами…………………28
1.8.8.Лазерная термическая обработка………….29
1.8.9.Классификация углеродистых сталей…….30
1.8.10.Стали обыкновенного качества………….31
1.8.11.Углеродистые качественные стали………33
1.8.12.Автоматные стали…………………..…….34
1.8.13.Легированные стали………………………34
1.8.14.Классификация легированных сталей…..35
1.8.15.Маркировка легированных сталей………37
1.8.16.Чугуны….…………………………………38
1.9.Инструментальные материалы………………….40
1.9.1.Характеристика свойств инструментальных материалов…………...40
277
1.9.2.Углеродистые инструментальные стали…41
1.9.3.Легированные инструментальные стали...42
1.9.4.Быстрорежущие стали…………………….42
1.9.5.Твердые сплавы……………………………42
1.9.6.Минералокерамика………………………...43
1.9.7.Синтетические сверхтвердые материалы (СТМ)………………………….44
1.9.8.Абразивные материалы…………………...44
1.9.9.Алмазные инструменты…………………...45
1.10.Цветные металлы и сплавы………………..……46
2.Основы литейного производства……………………..49
2.1.Сущность литейного производства……………...49
2.2.Литье в песчаные формы…………………………50
2.3.Литейные сплавы и их свойства…………………55
2.4.Специальные способы литья…………………….59
2.4.1.Кокильное литье……………………………59
2.4.2.Литье в оболочковые формы………………63
2.4.3.Литье по выплавляемым моделям………...65
2.4.4.Литье под давлением………………………67
2.4.5.Литье с кристаллизацией под давлением…69
2.4.6.Литье вакуумным всасыванием…………...70
2.4.7.Центробежное литье……………………….71
2.4.8.Литье выжиманием………………………...72
2.4.9.Электрошлаковое литье (ЭШЛ)…………..73
2.4.10.Получение отливок методом направленной кристаллизации…………..74
2.4.11.Обеспечение технологичности литых деталей…………………………………….75
2.4.12.Технологичность конструкции отливок………………………………….…79
2.4.13.Выбор способов литья……………………85
3.Обработка металлов давлением………………………86
3.1.Понятие о механизме пластического деформирования при обработке давлением…….87
278
3.2.Нагрев металла для обработки давлением………90
3.3.Нагревательные устройства……………………...93
3.4.Прокатное производство…………………………95
3.4.1.Сущность процесса………………………...95
3.4.2.Продукция прокатного производства….…97
3.4.3.Инструмент и оборудование для прокатки…………………………………….99
3.4.4.Производство бесшовных и сварных труб………………………………………...102
3.4.5.Производство специальных видов проката…………………………………….105
3.5.Волочение………………………………………..107
3.6.Прессование……………………………………...110
3.7.Ковка……………………………………………..112
3.7.1.Основные операции свободной ковки…..112
3.7.2.Оборудование для ковки…………………115
3.7.3.Типы поковок……………………………..116
3.8.Горячая объемная штамповка…………………..118
3.8.1.Сущность процесса……………………….118
3.8.2.Конструкции штампов……………………122
3.8.3.Основные этапы технологического процесса горячей объемной штамповки…126
4.8.4.Оборудование для горячей объемной штамповки…………………………………150
3.9.Холодная объемная штамповка………………...132
3.9.1.Холодное выдавливание………………….133
3.9.2.Холодная высадка………………………...134
3.9.3.Холодная формовка ………………….......135
3.10.Листовая штамповка…………………………...137
3.10.1.Разделительные операции листовой штамповки………………….....138
3.10.2. Формоизменяющие операции листовой штамповки……………..……...141
3.10.3.Штампы для холодной листовой штамповки…………………………….…145
279
3.10.4.Оборудование для холодной листовой штамповки………………………..………147
4.Сварка и пайка металлов…………………………….148
4.1.Физические основы образования сварного соединения……………………………148
4.2.Классификация видов сварки…………………..149
4.3.Свариваемость металлов и сплавов…………….151
4.4.Термические виды сварки………………………152
4.4.1. Источники теплоты при дуговой сварке...152 4.4.2. Электронно- и ионно-лучевой нагрев…...159
4.4.3. Световые источники нагрева…………….159
4.4.4. Газовое пламя……………………………..161 4.4.5. Ручная дуговая сварка……………………162
4.4.6. Автоматическая дуговая сварка
под флюсом……………………………….166
4.4.7.Дуговая сварка в защитном газе…………169
4.4.8.Электрошлаковая сварка…………………170
4.4.9.Газовая сварка…………………………….172
4.4.10.Плазменная сварка………………………175
4.4.11.Электронно-лучевая сварка……………..176
4.4.12.Лазерная сварка………………………….177
4.5.Термомеханические методы сварки……………178
4.5.1.Контактная сварка………………………...178
4.5.2.Конденсаторная сварка…………………...183
4.5.3.Диффузионная сварка…………………….184
4.5.4.Индукционно-прессовая (высокочастотная)
сварка………………………………………185
4.6.Механические методы сварки………………….186
280