
3187
.pdf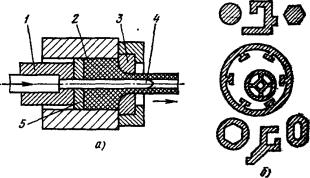
предварительно обтачивают на станке; после нагрева поверхность заготовки тщательно очищают от окалины.
Рис. 3.13. Схема прессования полого профиля (а) и примеры прессованных профилей (б)
Прессованием изготовляют изделия разнообразного сортамента из цветных металлов и сплавов, в том числе прутки диаметром 3…250 мм, трубы диаметром 20…400 мм со стенкой толщиной 1,5…12 мм и другие профили (рис. 3.13, б). Из углеродистых сталей 20, 35, 45, 50, конструкционных 30ХГСА, 40ХН, коррозионно-стойких 12Х18Н10Т и других высоколегированных сталей прессуют трубы с внутренним диаметром 30…160 мм со стенкой толщиной 2…10 мм, профили с полкой толщиной 2…2,5 мм и линейными размерами поперечных сечений до 200 мм.
Прессованием можно обрабатывать такие специальные стали, цветные металлы и их сплавы, которые ввиду низкой пластичности (особенно в литом состоянии) другими видами обработки давлением деформировать невозможно или затруднительно.
К недостаткам прессования следует отнести большие отходы металла: весь металл не может быть выдавлен из контейнера, и в нем остается так называемый пресс-остаток, который после окончания прессования отрезается от полученно-
111
го профиля. Масса пресс-остатка может достигать 40 % массы исходной заготовки (при прессовании труб большого диаметра).
Инструмент для прессования работает в исключительно тяжелых условиях, испытывая кроме действия больших давлений действие высоких температур. Инструмент для прессования изготовляют из высококачественных инструментальных сталей и жаропрочных сплавов. Износ инструмента уменьшают применением смазочных материалов, например, Для уменьшения трения при прессовании, а также во избежание налипания металла на инструмент применяют графитомасляные и другие смазки.
Основным оборудованием для прессования являются вертикальные или горизонтальные гидравлические прессы.
3.7.Ковка
3.7.1.Основные операции свободной ковки
Ковкой называют процесс горячей обработки металлов давлением, при котором путем многократного и прерывистого действия инструмента металл пластически деформируется, постепенно приобретая заданные форму, размеры и свойства.
Ковку называют свободной потому, что при деформировании металл течет свободно в направлениях, не ограниченных поверхностями инструмента. Свободная ковка является рациональным и экономически выгодным процессом изготовления качественных изделий в условиях мелкосерийного и индивидуального производства. Свободной ковкой изготовляют поковки, масса которых составляет от нескольких десятков граммов до 300 т и более. Все поковки, масса которых превышает 1 т, изготовляют только свободной ковкой.
Свободную ковку разделяют на ручную, применяемую для штучного изготовления поковок небольшой массы, и машинную, осуществляемую с помощью молотов и прессов.
112
Основными операциями свободной ковки являются осадка, протяжка, прошивка, гибка, закручивание, рубка и кузнечная сварка.
Осадка (рис. 3.14, а) — уменьшение высоты заготовки с одновременным увеличением ее поперечных размеров. Заготовки, в которых отношение высоты к диаметру или меньшей стороне сечения больше 2,5, осаживать не рекомендуется во избежание возможного продольного искривления. Осадку выполняют для получения из заготовки малого сечения поковки с большим поперечным сечением, а также для улучшения структуры и механических свойств металла поковок, в том числе для выравнивания свойств вдоль и поперек оси поковок. Поковки дисков, шестерен и аналогичных им деталей изготовляют только осадкой. Осадку производят бойками или осадочными плитами.
Высадка (рис. 3.14, б) является разновидностью осадки, при которой увеличивается поперечное сечение части заготовки с одновременным уменьшением ее продольных размеров.
Протяжка (рис. 3.14, в) — увеличение длины заготовки с одновременным уменьшением ее поперечных размеров. Протяжку применяют для изготовления валов различного назначения, тяг, рычагов, колонн и т. д. Протяжку выполняют в верхнем и нижнем плоских, верхнем плоском и нижнем вырезном и в обоих вырезных бойках.
Разновидности протяжки: раскатка (рис. 3.14, г) и протяжка на оправке (рис. 3.14, д). При раскатке происходит увеличение наружного и внутреннего диаметров прошитой заготовки за счет последовательного (по участкам) уменьшения толщины ее стенки. Инструментами для раскатки служат плоский боек, оправка и люнет.
При протяжке осаженная и прошитая заготовка, надетая на оправку, протягивается в нижнем вырезном и верхнем плоском или в обоих вырезных бойках.
Раскаткой делают кольца, венцы зубчатых шестерен и другие подобные поковки, а протяжкой на оправке — обечай-
113

ки, сосуды высокого давления, стволы артиллерийских орудий и другие поковки.
Рис. 3.14. Схемы основных операций свободной ковки
Гибка (рис. 3.14, е) — придание заготовке изогнутой формы по требуемому контуру. Гибку осуществляют в подкладных штампах и приспособлениях.
Закручивание (рис. 3.14, ж) — поворот вокруг продольной оси одной части заготовки относительно другой на заданный угол. Закручивание осуществляют вручную или с помощью крана воротками или вилками. Наиболее часто закручивание применяют при изготовлении коленчатых валов.
114
Рубка (рис. 3.14, з) — отделение одной части поковки или заготовки от другой. Рубку осуществляют топорами для удаления лишних концов поковок или для разделения длинной поковки на более короткие части. Разновидность рубки — вырубка, при которой часть металла в поковке или заготовке удаляется по замкнутому контуру.
Прошивка (рис. 3.14, и, к) — образование отверстия в заготовке вследствие вытеснения металла. Прошивка может служить самостоятельной операцией для образования отверстия, либо подготовительной операцией для последующей раскатки или протяжки заготовки на оправке. Отверстия диаметром до 400…500 мм прошивают сплошным прошивнем с применением подкладного кольца, а отверстия с диаметром более 300…900 мм прошивают полым прошивнем, применяя в случае большой высоты заготовки, надставки.
3.7.2. Оборудование для ковки
Ковку выполняют на ковочных молотах и ковочных гидравлических прессах.
Молоты — машины динамического, ударного действия. Продолжительность деформации на них составляет тысячные доли секунды. Металл деформируется за счет энергии, накопленной подвижными (падающими) частями молота к моменту их соударения с заготовкой. Поэтому при выборе молотов руководствуются массой их падающих частей. Энергия, накопленная падающими частями, не вся расходуется на деформирование заготовки. Часть ее теряется на упругие деформации инструмента и колебания шабота — детали молота, на которую устанавливают нижний боек. Чем больше масса шабота, тем больше КПД. Практически масса шабота бывает в 15 раз больше массы падающих частей, что обеспечивает КПД удара
ηуд = 0,8…0,9.
Одним из основных типов молотов для ковки являются паро-воздушные молоты. Такие молоты приводятся в действие паром или сжатым воздухом давлением 0,7…0,9 МПа. В
115
зависимости от конструкции станины паровоздушные ковочные молоты бывают арочные, мостовые и одностоечные.
Ковочные паровоздушные молоты строят с массой падающих частей 1000…8000 кг. На этих молотах изготовляют поковки средней массы (20…350 кг), преимущественно из прокатанных заготовок.
Гидравлические прессы — машины статического действия; продолжительность деформации на них может составлять от единиц до десятков секунд. Металл деформируется приложением усилия, создаваемого с помощью жидкости (водной эмульсии или минерального масла), подаваемой в рабочий цилиндр пресса. Ковочные гидравлические прессы строят усилием 5…100 МН для изготовления крупных поковок в основном из слитков.
3.7.3. Типы поковок
Ковкой получают поковки простой формы массой до 300 тонн с большими напусками. Применяя специальный инструмент, уменьшают напуски. Припуски и допуски на поковки,
изготовляемые на молотах, от 5 12 мм до (34 10) мм, а на по-
ковки, изготовляемые на прессах, от (10 3) мм до (80 ± 30) мм; для необрабатываемых участков предельные отклонения снижают на 25…50%. С применением подкладных штампов (закрытых и открытых) получают поковки массой до 150 кг (главным образом мелкие до 5 кг) с относительно сложной формой, без напусков; припуски — от 3 мм и выше, допуски
1,5 мм и более.
1
Горячей ковкой изготовляют поковки: цилиндрические сплошные гладкие и с уступами (штоков, осей, валов, колонн, цапф, роторов и т.п., рис. 3.15, а); прямоугольного сечения гладкие и с уступами (плат, пластин, штамповых кубков, вкладышей, шпинделей, дышел, баб и т. п., рис. 3.15, б); со смешанными сечениями сплошные с уступами и с расположением отдельных частей в одной, двух, трех и более плоскостях
116

(коленчатых валов и т. п., рис. 3.15, в); цилиндрические полые гладкие и с малыми уступами (дисков, фланцев, колес, покрышек, муфт и т. п., рис. 3.15, г); цилиндрические полые гладкие с малым отношением длины к размеру сечения (бандажей, колец и т. п., рис. 3.15, д); цилиндрические полые гладкие и с большими уступами при большом отношении длины к размеру сечения (барабанов, полых валов, цилиндров и т. п., рис. 3.15, е), с криволинейной осью (крюков, бугелей, скоб, днищ, вилкообразные и т. п., рис. 3.15, ж).
Рис. 3.15. Основные типы поковок
Для уменьшения отхода металла и снижения трудоемкости как в процессе ковки, так и в процессе последующей обработки, желательно поковкам (и изготовляемым из них деталям) придать наиболее простую форму, ограниченную плоскими или цилиндрическими поверхностями. Нежелательны конические и клиновые формы поковок, пересече-
117
ние цилиндрических поверхностей и призматических поверхностей с цилиндрическими. Односторонние выступы предпочтительнее двусторонних. Нельзя выполнять ковкой ребра жесткости, платики и выступы. Детали со значительной разницей поперечных сечений целесообразно заменять сочетанием нескольких скрепленных или сваренных, а детали сложной формы выполнять сварными из нескольких поковок или сварными из поковок и отливок.
Заготовки для ковки выбирают в зависимости от массы поковок: сортовой прокат – при массе до 40 кг; крупный прокат и обжатые болванки – при массе 40…300 кг; слитки при массе более 300 кг.
3.8. Горячая объемная штамповка
3.8.1. Сущность процесса
Объемной штамповкой называют процесс обработки давлением, при котором происходит принудительное перераспределение металла заготовки с заполнением полости инструмента, называемого штампом. Полость штампа, которую заполняет металл при штамповке, называют ручьем.
Объемную штамповку разделяют на горячую и холодную. Горячая штамповка получила в машиностроении большее применение, чем холодная. Это объясняется тем, что при холодной штамповке пластичность холодного металла ниже, а, следовательно, и стойкость штампов более низкая. Кроме того, для осуществления холодной штамповки необходимо применение машин значительно большей мощности, чем для горячей. Объемная штамповка наиболее эффективна при массовом и крупносерийном изготовлении поковок. Так, горячей объемной штамповкой изготовляют более 65% массы всех поковок и до 20% массы всех деталей машин.
По сравнению со свободной ковкой горячая объемная штамповка позволяет получать поковки более сложной формы и с лучшим качеством поверхности. Кроме того, благодаря ее
118
применению снижаются припуски и допуски в два-три раза и обеспечивается лучшая точность изготовления поковок. При горячей объемной штамповке повышается производительность труда и уменьшается расход металла на изделие. Для штампованных поковок резко сокращается объем механической обработки.
Горячей объемной штамповкой получают заготовки для ответственных деталей автомобилей, тракторов, сельскохозяйственных машин, железнодорожных вагонов, самолетов, металлообрабатывающих станков, швейных машин и т.д. Более 65% массы всех поковок и до 20% массы деталей большинства машин изготавливаются из заготовок, полученных горячей объемной штамповкой. Этот способ штамповки наиболее эффективен при массовом, крупносерийном и серийном производствах деталей массой от нескольких граммов до нескольких тонн (примерно до 3 т). Наиболее целесообразно изготовление штамповкой поковок массой не более 50…100 кг.
По методу изготовления поковок горячую объемную штамповку разделяют на облойную штамповку в открытых штампах (рис. 3.16, а), безоблойную штамповку в закрытых штампах (рис. 3.16, б) и штамповку в штампах для выдавливания (рис. 3.17).
Открытыми называют штампы, у которых вдоль всего внешнего контура штамповочного ручья сделана специальная облойная канавка.
Облойная канавка при штамповке имеет следующее назначение: 1) в нее вытекает избыточный объем металла заготовки, 2) при соударении верхней и нижней половин штампа облой, находящийся, в канавке, предохраняет их от жесткого удара, что способствует продлению срока службы штампа, 3) мостик облойной канавки в виде узкой щели создает в кон-
це штамповки большое сопротивление течению металла, чем способствует лучшему заполнению полости штампа. Этому же способствует и быстрое остывание облоя.
Для штамповки в открытых штампах характерны следующие особенности: 1) объем металла, находящегося в ру-
119
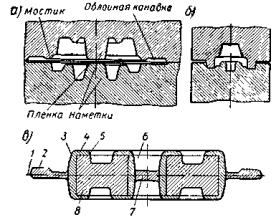
чье, не постоянен; при штамповке часть металла вытесняется в облой, который обеспечивает заполнение углов полости штампа; 2) направление вытесняемого металла в облойную щель перпендикулярно к направлению движения штампа, поэтому в месте обрезки облоя у поковки волокна металла оказываются перерезанными; 3) из заготовки низкой точности получаются поковки высокой точности за счет различного объема металла, вытесняемого в облой.
Рис. 3.16. Штамповка облойная в открытом штампе а; безоблойная в закрытом штампе б и штампованная поковка с облоем в:
1 — плоскость разъема; 2 — облой; 3 — штамповочные уклоны; 4 — припуски; 5 — закругления;
6 — наметки; 7 — пленка; 8 — тело поковки
Штампы, в которых металл деформируется в замкнутом пространстве (рис. 3.16, б), называют закрытыми, а штамповку в них безоблойной. Для штамповки в закрытых штампах характерны следующие особенности: 1) изменения объема заготовки должны быть незначительными, так как облой не предусматривается, а объем металла в полости штампа практически не изменяется; 2) микроструктура поковок весьма
120