
3187
.pdf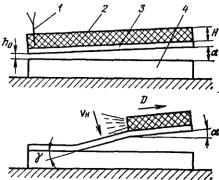
делением газов и теплоты происходит с большой скоростью (несколько тысяч метров в секунду).
Рис. 4.16. Схема сварки взрывом
В месте соударения метаемой пластины с основанием образуется угол γ, который перемещается вдоль соединяемых поверхностей. При соударении из вершины угла выдуваются тонкие поверхностные слои, оксидные пленки и другие загрязнения. Соударение пластин вызывает течение металла в их поверхностных слоях. Поверхности сближаются до расстояния действия межатомных сил взаимодействия, и происходит схватывание по всей площади соединения. Продолжительность сварки взрывом не превышает нескольких микросекунд.
Прочность соединений, выполненных сваркой взрывом, выше прочности соединяемых материалов. Разрушение при испытании происходит на некотором расстоянии от плоскости соединения по наименее прочному металлу. Это объяснятся упрочнением тонких слоев металла, прилегающих к соединенным поверхностям, при их пластической деформации.
Сварку взрывом используют при изготовлении заготовок для проката биметалла, плакирования поверхностей конструкционных сталей металлами и сплавами с особыми физиче-
191
скими и химическими свойствами, при сварке заготовок из разнородных материалов.
4.6.5. Магнитоимпульсная сварка
Соединение образуется в результате соударения соединяемых частей, вызванного воздействием импульсного магнитного поля. Детали устанавливают так, чтобы свариваемые поверхности находились внахлестку под углом друг к другу и с зазором между ними. Магнитная катушка образует магнитное поле. Его силовые линии пересекают одну из деталей и индуцируют в ней вихревые токи. Последние создают собственное магнитное поле вокруг детали. Взаимодействие магнитных полей катушки и детали приводит к отталкиванию детали от катушки. В результате возникает сила, которая придает ускорение этой детали в направлении второй. При их соударении достигается давление, необходимое для сварки. Кратковременностью действия импульса, динамическим характером процесса магнитоимпульсная сварка напоминает сварку взрывом. Строение металла в зоне контакта после сварки этими методами тоже имеет много общего. Так, в обоих случаях соединение получается волнистым. Очевидно, схожим должен быть и механизм удаления оксидной пленки и образования металлических связей. Длительность импульсов при магнитоимпульсной сварке и сварке взрывом составляет 10…100 мкс, т. е. они примерно одинаковы, однако давление при сварке взрывом на порядок выше.
Кроме сварки деталей из одинаковых металлов возможна сварка разнородных материалов, таких, как алюминий — медь, алюминий — коррозионностойкая сталь, цирконий — коррозионностойкая сталь. Кроме того, магнитоимпульсная сварка (по сравнению со сваркой взрывом) проще с точки зрения соблюдения техники безопасности.
192
4.7.Специальные термические процессы
всварочном производстве
Ксварочным процессам помимо процессов соединения относят также термическую резку, наплавку, напыление и ряд других методов обработки материалов.
Резка. Термическая резка базируется на использовании широкого круга источников теплоты. К ним относятся газовое пламя, плазменная дуга, электронный и лазерный луч. Она позволяет разрезать металлы и сплавы самых разных толщин (от десятков миллиметров до долей миллиметра), любого химического состава, обеспечивать достаточно высокую точность и чистоту реза. Причем возможно осуществлять непрерывный процесс резки, прошивать отверстия в заготовках, производить поверхностную резку (снятие слоя металла с заготовки).
Кислородная резка основана на нагреве металла в зоне реза кислородно-ацетиленовым пламенем (вместо ацетилена может использоваться и другое горючее, например пропан) до температуры его воспламенения. За счет экзотермической реакции окисления металла участок реза дополнительно нагревается и расплавляется, а оксиды удаляются кинетической струѐй режущего кислорода.
Кислородно-флюсовая резка. Высоколегированные хромистые, хромоникелевые стали, чугун, цветные металлы разрезать обычной кислородной резкой не удается — в основном из-за образования оксидов в зоне реза, которые зашлаковывают рез, препятствуя нормальному процессу резки. При кислородно-флюсовой резке в зону реза вместе с режущим кислородом вводят порошкообразные флюсы. Их назначение
— увеличить тепловыделение, образовать более легкоплавкие шлаки, легко удаляемые струѐй режущего кислорода. Для резки сталей применяют в качестве такого флюса порошок железа.
Плазменная резка. Для резки металлов применяют плазматрон. Дуга может быть прямого действия, когда она возбу-
193
ждается на обрабатываемом металле, и косвенного. В последнем случае вторым электродом служит сопло плазматрона. Из сопла выдувается свободная струя плазмы.
Процесс резки заключается в проплавлении металла и удалении жидкого металла из полости реза плазменной струѐй. В качестве плазмообразующих газов могут быть использованы сжатый воздух, кислород, азотно-кислородная смесь, азот, аргоноводородная смесь. Выбор плазмообразующего газа определяется физико-химическими свойствами разрезаемого металла, необходимым качеством реза, стойкостью плазматрона, стоимостью самих газов. Например, дорогую аргоноводородную смесь применяют в случае повышенного требования к качеству резания алюминия, меди и сплавов на их основе.
Электронно-лучевая и лазерная резка. Эти процессы основаны на испарении металла под воздействием мощного, концентрированного источника нагрева. Электронно-лучевая резка осуществляется в вакууме, в то время как резка лазером может происходить в обычной атмосфере. Резка этими методами отличается высокой чистотой и точностью реза, небольшой зоной термического влияния на кромках разрезаемого материала. Однако установки для электронно-лучевой и лазерной резки имеют повышенную сложность и стоимость.
Наплавка. Наплавка — это процесс нанесения слоя металла или сплава на поверхность изделия. Она позволяет получать детали с поверхностью, отличающейся от основного металла, например жаропрочностью и жаростойкостью, высокой износостойкостью при нормальных и повышенных температурах, коррозионностойкостью и т. п. Наплавка может производиться как при изготовлении новых деталей, так и (особенно широко) в ремонтно-восстановительных работах, существенно удлиняя срок эксплуатации деталей и узлов, обеспечивая этим высокий экономический эффект.
Существуют разнообразные способы наплавки. Основные из них следующие.
194
1.Ручная дуговая электродами со стержнями и покрытиями специальных составов.
2.Автоматическая наплавка под флюсом. Электроды могут быть сплошного сечения и порошковые. Состав флюса, металл электрода и состав наполнителя (для порошковой проволоки) определяют свойства наплавленного слоя.
3.Наплавка плавящимся и неплавящимся электродами в среде защитных газов, прежде всего аргона. Свойства наплавленного слоя здесь зависят от материала присадки (при наплавке неплавящимся, например вольфрамовым, электродом) или электрода (при наплавке плавящимся электродом).
4.Плазменная наплавка. Дуга может быть как прямого, так и косвенного действия. Наплавляемый материал подают в виде проволоки, порошка. Можно плазменной струѐй оплавлять слой легированного порошка, предварительно нанесенный на поверхность детали.
5.Электрошлаковая наплавка. Схема такого процесса наплавки аналогична схеме электрошлаковой сварки, однако формирование шва осуществляют по заданной поверхности плоской или цилиндрической детали.
6.Электронно-лучевая и лазерная наплавка, наплавка полым электродом в вакууме. Эти методы наплавки используют особые свойства источников теплоты — высокую концентрацию тепловой энергии, возможность локального нагрева в условиях качественной защиты металла (электроннолучевая наплавка н наплавка полым катодом в вакууме).
7.Наплавка газокислородным пламенем. Как и при сварке, процесс наплавки этим методом характеризуется большой зоной влияния и деформациями.
Существенным показателем эффективности того или иного способа наплавки является степень перемешивания при наплавке основного металла и присадочного: чем она меньше, тем ближе будут свойства наплавленного слоя к заданному.
Напыление. При напылении расплавленные по всему объему или по поверхности частицы материала будущего по-
195
крытия направляются на поверхность нагретой заготовки. При соударении с поверхностью частица деформируется, обеспечивая хороший физический контакт с деталью. Характер взаимодействия частицы с материалом подложки (детали), последующая кристаллизация частиц определяют качество адгезии покрытия с подложкой. Последующие слои формируются уже за счет связей частиц друг с другом, имеют чешуйчатое строение и существенно неоднородны.
Для напыления используют источники тепла: газовое пламя, плазму, ионный нагрев, нагрев в печах, лазер и др.
Наибольшее распространение получили процессы газоплазменного и плазменного напыления. Материал для напыления подается в пламя горелки или плазменную дугу в виде проволоки или порошка, где происходит нагрев и распыление частиц, которые тепловым потоком источника нагрева разгоняются и попадают на поверхность напыляемой детали. Иной способ формирования покрытий при нагреве в печах. В этом случае нагретая деталь контактирует с материалом покрытия, находящимся в виде порошка или газовой фазы. Получаемое таким методом покрытие имеет высокую адгезию к поверхности детали за счет активных диффузионных процессов, происходящих в период достаточно длительной выдержки в печи при высокой температуре.
Все большее распространение получают ионноплазменные методы нанесения износостойких и декоративных покрытий.
4.8.Пайка металлов
4.8.1.Основные понятия и определения
Пайкой называют образование соединения с межатомными связями в результате нагрева соединяемых материалов ниже температуры их плавления, смачивания их припоем, затекания припоя в зазор и последующей его кристаллизации.
196
В качестве припоя при пайке используется металл или сплав с температурой плавления ниже температуры плавления паяемых материалов. Для удаления оксидов с поверхности паяемого материала и припоя и предотвращения их образования в процессе пайки применяется вспомогательный материал, называемый паяльным флюсом.
Свойство материалов образовывать паяное соединение при заданном режиме пайки называется паяемостью.
Наиболее прочные и пластичные паяные швы обеспечиваются при образовании твердых растворов, которые возникают при пайке металлов, обладающих общим типом кристаллических решеток и имеющих близкие значения межатомных расстояний.
Процесс пайки металлов имеет много общего с процессом сварки плавлением. Однако пайка отличается от сварки следующими характерными особенностями.
1.Пайка производится при температуре ниже температуры плавления обоих или хотя бы одного из соединяемых металлов.
2.В процессе пайки между соединяемыми деталями в определенный момент находится жидкая металлическая прослойка припоя.
3.В отличие от сварки плавлением паяное соединение образуется не в результате непосредственного взаимодействия металлов соединяемых деталей, а вследствие взаимодействия припоя и основного металла.
4.Обязательным условием пайки являются смачивание паяемых поверхностей припоем, диффузия компонентов припоя в сторону основного металла и компонентов основного металла в сторону припоя и последующая кристаллизация жидкой прослойки.
Возможность варьировать размеры соединяемых пайкой поверхностей (величины нахлестки) позволяет обеспечить равнопрочные с основным металлом соединения. При этом
197
получается более благоприятная форма соединения с меньшей концентрацией напряжений, чем при контактной сварке.
Физико-химическое взаимодействие расплавленного припоя с паяемым материалом, проявляющееся в растекании припоя или образовании мениска с краевым углом смачивания, называют смешиваемостью.
4.8.2. Способы пайки
Современные способы пайки принято классифицировать по следующим независимым признакам:
-удалению оксидной пленки: флюсовая пайка, пайка в активной газовой среде, в нейтральной газовой среде, в вакууме, ультразвуковая;
-кристаллизации паяного шва: при охлаждении, при выдержке (диффузионная пайка);
-получению припоя: готовый полностью расплавляемый припой, композиционный припой, контактнореактивная пайка, реактивно-флюсовая пайка;
-заполнению зазора припоем: капиллярная пайка, некапиллярная пайка;
-источнику нагрева: пайка в печи, индукционная, электросопротивлением, электролитная, погружением, электронно-лучевая, лазерная, газопламенная, плазменная, паяльником;
-наличию давления на паяемые детали;
-одновременности выполнения паяных соединений.
4.8.3. Технологический процесс пайки
Технологический процесс пайки включает комплекс выполняемых операций, основными из которых являются следующие: подготовка поверхностей под пайку; сборка деталей; укладка припоя, в ряде случаев нанесение флюса; пайка; обработка деталей после пайки.
198
Подготовка поверхности под пайку. Качество подготовки поверхности под пайку во многом определяет уровень и стабильность свойств паяного соединения. Существуют следующие основные способы очистки поверхности: термический, механический, химический.
Укладка припоя. Часто сборка включает в себя нанесение припоя, укладку его в виде дозированных заготовок из проволоки или фольги. При размещении припоя необходимо учитывать условия пайки: расположение изделия в печи или другом нагревательном устройстве, режимы нагрева и охлаждения.
Нанесение флюса. Иногда при сборке деталей под пайку требуется нанести флюс. Порошкообразный флюс разводят дистиллированной водой до состояния негустой пасты и наносят шпателем или стеклянной палочкой, после чего детали подсушивают в термостате при 70…80 °С в течение 30…60 мин. При газопламенной пайке флюс подают на прутке разогретого припоя, при пайке паяльником — рабочей частью паяльника или вместе с припоем, в случае применения оловян- но-свинцового припоя — в виде трубок, наполненных канифолью.
Пайка (нагрев места соединения или общий нагрев собранных деталей) выполняется при температуре, превышающей температуру плавления припоя, как правило, на 50…100 °С.В зависимости от температуры плавления применяемых припоев пайка подразделяется на высокотемпературную и низкотемпературную.
При низкотемпературной пайке нагрев в месте контакта паяемых материалов и припоя не превышает 450 °С, при высокотемпературной — превышает 450 °С.
Обработка после пайки включает в себя удаление остатков флюса.
199
4.9.Контроль качества сварных
ипаяных соединений
4.9.1.Дефекты сварных и паяных соединений
При производстве сварных и паяных конструкций могут возникать дефекты, т. е. отдельные несоответствия продукции нормативным требованиям. Влияние дефекта на работоспособность конструкции определяется многими факторами. Оно зависит не только от характера самого дефекта — его размеров, расположения, но и от свойств материала, условий эксплуатации.
Дефекты сварки термического класса: непровар, который представляет собой частичное отсутствие сплавления свариваемых кромок со стороны корня шва или частичное отсутствие сплавления наплавленного металла с основным; пористость, представляющая собой газовые пузырьки в металле; трещины; шлаковые включения; пережог — окисление по границам зерен; прожог — сквозное проплавление металла; подрез — углубление основного металла в месте его перехода к поверхности шва.
Дефекты сварки термомеханического класса. Дефекты при точечной сварке: непровар — отсутствие или малый диаметр ядра; выплеск металла; прожог; трещины; раковины и пористость; вмятины (более 10…20% толщины листа).
Дефекты при шовной сварке: негерметичность шва; подплавление поверхности деталей вследствие плохой очистки деталей и роликов; прожог.
Дефекты при стыковой сварке: смещение свариваемых деталей; непровар; перегрев и пережог; подгар поверхности деталей в зажимах; чрезмерно большое количество выдавленного металла; трещины; остатки шлаков и оксидов в сварном шве.
При пайке возможны следующие дефекты: смещение паяемых элементов; раковины в швах; пористость в паяном
200