
3187
.pdf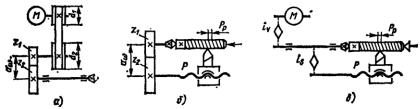
тельных движений и т. д.). Кинематическая цепь представляет собой систему последовательно расположенных кинематических пар (передач) — ременных, зубчатых и т. п. (рис. 5.13). Ромбы – органы настройки.
Рис. 5.13. Кинематические цепи
Для изменения соотношения движений начального и конечного звеньев в кинематическую цепь вводят орган настройки, который позволяет изменять передаточное отношение цепи. В качестве органа настройки чаще всего применяют сменные зубчатые колеса, коробки скоростей и подач, сменные или ступенчатые шкивы, вариаторы и т.п.
Кинематическая цепь передает движение от начального ее звена к конечному. Обычно начальное звено совершает вращательное движение; конечное звено получает либо вращательное, либо прямолинейное поступательное движение. С помощью кинематических цепей осуществляется передача движения от двигателя к исполнительным органам станка, а также изменение скоростей и направления движения исполнительных органов, согласование движений отдельных узлов станка и преобразование одного вида движения в другой (например, вращательного в поступательное или наоборот).
Передаточное отношение кинематической цепи определяется как произведение передаточных отношений всех m составляющих ее передач:
iкц = i1i2 … im .
241
Взаимосвязанные перемещения начального и конечного звеньев кинематической цепи называются расчетными перемещениями. Расчетные перемещения определяют исходя из формы обрабатываемой детали и типа применяемого станка.
После определения расчетных перемещений по кинематической цепи составляют уравнение кинематического баланса, связывающее эти перемещения. С помощью уравнения кинематического баланса можно по заданной скорости движения начального звена найти скорость движения конечного звена, если известно передаточное отношение кинематической цепи.
При подготовке станка к выполнению определенной работы производят его настройку и (или) наладку. Настройка станка заключается в установлении жесткой кинематической связи между исполнительными органами станка (нарезание резьбы на токарно-винторезном станке, обработка зубчатого колеса по методу обката). Наладка станка не связана с кинематическими расчетами (установка и регулировка режущего и вспомогательного инструмента, упоров, кулачков, копиров и т. п.).
5.1.17. Приводы главного движения и подач
Приводом называется совокупность устройств, приводящих в движение исполнительные органы станка. Обычно привод состоит из электродвигателя и передачи-механизма, передающего движение от двигателя к исполнительным органам (коробки скоростей или подач, сменных шестерен, ременной передачи и т. п.). Наряду с наиболее распространенными электромеханическими приводами в станках применяют также гидропривод, в котором роль двигателя играет гидронасос и питаемый им гидроцилиндр (гидромотор), а функции передачи выполняет рабочая жидкость. В некоторых случаях применяется пневмопривод (для вспомогательных движений, подачи и зажима заготовок и т. п.).
242
Современные станки оснащаются индивидуальными приводами, т. е. каждый станок приводится в действие либо от одного, либо от нескольких электродвигателей. В последнем случае различают привод главного движения, привод подачи, привод быстрых перемещений и т.. д. Электродвигатель, чаще всего асинхронный, с короткозамкнутым ротором, устанавливается на станке или в непосредственной близости от него. В станках с ЧПУ применяются преимущественно электродвигатели постоянного и трехфазного тока (асинхронные и синхронные) с регулируемой частотой вращения в широких пределах.
Привод должен обеспечивать возможность изменения скорости движения исполнительных органов станка в определенных интервалах.
Отношение пределов регулирования
R = nmax / nmin
называется диапазоном регулирования частот вращения и является важной характеристикой привода, определяющей степень универсальности станка. Для станков токарных, расточных, фрезерных R = 50…150, для сверлильных R = 15…50, для шлифовальных R = 1…3.
В приводах станков применяется ступенчатое или бесступенчатое регулирование скоростей главного движения и подачи.
Наиболее широкое применение в станках нашли электрические, гидравлические и электрогидравлические приводы.
Интенсивное развитие электрических приводов привело к созданию регулируемых приводов постоянного тока, переменного тока и силовых шаговых приводов.
Самый распространенный привод главного движения в металлорежущих станках (токарных, фрезерных, расточных) средних размеров — привод с механическим регулированием скорости, состоящий из односкоростного электродвигателя переменного тока и коробки скоростей.
243
Вагрегатных и других станках применяют привод с односкоростным электродвигателем переменного тока и коробкой скоростей со сменными зубчатыми колесами или шкивами.
Привод главного движения станков с ЧПУ строится на основе регулируемого привода в сочетании с двумя, а иногда
иболее ступенчатыми переборными группами. В них применяют электродвигатели постоянного тока с широким диапазоном регулирования частот вращения.
Вприводах подач станков с ЧПУ в основном используют регулируемые приводы на высокомоментных двигателях или асинхронных с частотным регулированием, иногда применяют шаговые электродвигатели. Для перемещения исполнительного органа станка по каждой из координат обычно предусматривают самостоятельный привод подач.
Применение в приводах подач шаговых электродвигателей объясняется простотой конструкции и надежностью в работе. Шаговые электродвигатели (ШД) бывают как силовые, с
вращательным моментом более 100 Н м, так и маломощные, с вращательным моментом менее 1 Н м, снабженные усилителем. Применение силовых шаговых электродвигателей упрощает систему привода перемещения исполнительного узла. Однако мощные электродвигатели имеют плохую динамическую характеристику.
Линейные электрогидравлические приводы с шаговыми электродвигателями (ЛЭГШП) позволяют выполнять управляемое по программе перемещение рабочих органов непосредственно, без применения традиционных винтовых, зубча- то-реечных и других механических передач.
Конструкции линейных электрогидравлических приводов с задающим электродвигателем отвечают требованиям, предъявляемым к станкам с ЧПУ по точности позиционирования, диапазонам рабочих скоростей, жесткости нагрузочной характеристики и весовым показателям.
244
5.1.18. Технологические возможности токарной обработки
Точение является основным способом обработки поверхностей тел вращения. Процесс резания осуществляется на токарных станках при вращении обрабатываемой заготовки (главное движение) и перемещении резца (движение подачи). С помощью точения выполняют операции: обтачивание — обработку наружных поверхностей; растачивание — обработку внутренних поверхностей; подрезание — обработку торцевых поверхностей; резку — разрезание заготовки на части; резьбонарезание — нарезание резьбы.
По технологическим возможностям точение условно подразделяется на: черновое; получистовое; чистовое; тонкое. К черновому точению относят обдирку, отрезку и подрезку торцов заготовок. Обычно черновое точение используют для предварительной обработки заготовок. Чистовое обтачивание и растачивание обеспечивают обработку по 10…8-му квалитету и шероховатость поверхности Rz = 40…20 мкм. Тонкое точение позволяет при обтачивании получить 6,7-й квалитет и шероховатость Rа = 1,6 мкм. При точении параметры резания определяются скоростью резания, подачей и глубиной резания.
В качестве режущего инструмента при точении используются резцы. Головку резца изготавливают из инструментальных, быстрорежущих сталей, твердых сплавов, минералокерамики и сверхтвердых материалов; стержень изготавливают из конструкционной стали.
Резцы классифицируют по материалу режущей головки, ее форме (прямые, отогнутые, изогнутые, оттянутые), виду выполняемой операции (проходные, отрезные и т. п.), виду точения (черновые, чистовые).
Обтачивание наружных цилиндрических поверхностей выполняют прямыми, отогнутыми или упорными проходными резцами с продольной подачей (рис. 5.14, а); гладкие валы, —
245
при установке заготовки на центрах. Вначале обтачивают один конец заготовки, а затем ее поворачивают на 180° и обтачивают остальную часть.
Ступенчатые валы обтачивают по схемам деления припуска на части (рис. 5.14, б) или деления длины заготовки на части (рис. 5.14, в). В первом случае обрабатывают заготовки с меньшей глубиной резания, однако общий путь резца получается большим и резко возрастает То. Во втором случае припуск с каждой ступени срезается сразу за счет обработки заготовки с большой глубиной резания. При этом Т о уменьшается, но требуется большая мощность привода станка.
Нежесткие валы рекомендуется обрабатывать упорными, проходными резцами, с главным углом в плане θ = 90°. При обработке заготовок валов такими резцами радиальная составляющая силы резания Ру = 0, что снижает деформацию заготовок.
Подрезание торцов заготовки выполняют перед обтачиванием наружных поверхностей. Торцы подрезают подрезными резцами с поперечной подачей к центру (рис. 5.14, г) или от центра заготовки. При подрезании от центра к периферии поверхность торца получается менее шероховатой.
Обтачивание округлений между ступенями валов (рис. 5.14, д) выполняют проходными резцами с закруглением между режущими кромками по соответствующему радиусу с продольной подачей или специальными резцами с поперечной подачей.
Протачивание канавок (рис. 5.14, е) выполняют с поперечной подачей прорезными резцами, у которых длина главной режущей кромки равна ширине протачиваемой канавки. Широкие канавки протачивают теми же резцами сначала с поперечной, а затем с продольной подачей.
Сверление, зенкерование и развертывание отверстий выполняют соответствующими инструментами, закрепляемыми в пиноли задней бабки. На рис. 5.14, ж показана схема сверления в заготовке цилиндрического отверстия.
246
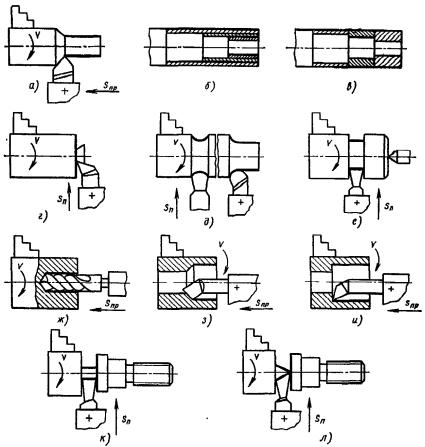
Рис. 5.14. Схемы обработки заготовок на токарно-винторезном станке
Растачивание внутренних цилиндрических поверхностей выполняют расточными резцами, закрепленными в резцедержателе станка, с продольной подачей. Гладкие сквозные отверстия растачивают проходными резцами (рис. 5.14, з); ступенчатые и глухие — упорными расточными резцами (рис.
5.14, и).
Отрезку обработанных деталей выполняют отрезными резцами с поперечной подачей. При отрезке детали резцом с
247
прямой главной режущей кромкой (рис. 5.14, к) разрушается образующаяся шейка и приходится дополнительно подрезать торец готовой детали. При отрезке детали резцом с наклонной режущей кромкой (рис. 5.14, л) торец получается чистым.
Обтачивание наружных конических поверхностей заготовок осуществляют на токарно-винторезных станках одним из следующих способов.
1.Широкими токарными резцами.
2.Поворотом каретки верхнего суппорта (короткие конические поверхности).
3.Смещением корпуса задней бабки в поперечном направлении.
4.С помощью конусной линейки, которую закрепляют на кронштейнах на станине станка.
Обтачивание внутренних конических поверхностей выполняют широким резцом, поворотом каретки верхнего суппорта, с конусной линейкой. Часто внутренние конические поверхности обрабатывают специальными коническими зенкерами.
Нарезание резьбы на токарно-винторезных станках выполняют резцами, метчиками и плашками. Форма режущих кромок резцов определяется профилем и размерами поперечного сечения нарезаемых резьб.
На токарно-винторезных станках нарезают метрические, дюймовые, модульные и специальные резьбы. Нарезание многозаходных резьб на токарно-винторезном станке требует точного углового деления обрабатываемой заготовки при переходе от одной нитки нарезаемой резьбы к другой.
5.1.19. Технологические возможности обработки заготовок на сверлильных станках
Сверление является основным способом получения глухих и сквозных цилиндрических отверстий в сплошном материале заготовки. В качестве инструмента при сверлении используется сверло, имеющее две главные режущие кромки,
248
переднюю кромку и две винтовые канавки, служащие для удаления стружки. Для сверления используются сверлильные и токарные станки. На сверлильных станках сверло совершает вращательное (главное) движение резания и продольное (движение подачи) вдоль оси отверстия, заготовка неподвижна. При работе на токарных станках вращательное (главное) движение совершает обрабатываемая деталь, а поступательное движение вдоль оси отверстия (движение подачи) совершает сверло.
Параметрами режима резания при сверлении являются скорость резания (окружная скорость на периферии сверла) и подача.
При сверлении получают точность не выше 14…12-го квалитета и шероховатость поверхности Rz = 80…60 мкм.
Для получения отверстий более высокой точности и чистоты поверхности после сверления на том же станке выполняются зенкерование и развертывание.
Точность обработки зенкерами цилиндрических отверстий находится в пределах 11…9 квалитетов, а шероховатость обработанной поверхности достигает Rа = 2,0 мкм.
Развертками производится окончательная (чистовая) обработка предварительно просверленных и расточенных резцом или зенкером цилиндрических и конических отверстий с точностью до 7 квалитета и с шероховатостью обработанных поверхностей до Rа = 0,6 мкм.
Сверление сквозного отверстия показано на рис. 5.15, а. Режущим инструментом служит спиральное сверло. В зависимости от требуемой точности, и величины партии обрабатываемых заготовок отверстия сверлят в кондукторе или по разметке.
Рассверливание — процесс увеличения диаметра ранее просверленного отверстия сверлом большего диаметра (рис. 5.15, б). Диаметр отверстия под рассверливание выбирают так, чтобы поперечная режущая кромка в работе не участвовала. В этом случае осевая сила уменьшается.
249
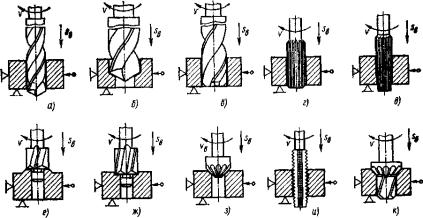
Рис. 5.15. Схемы обработки заготовок на вертикально-сверлильных станках
Зенкерование — обработка предварительно полученных отверстий для придания им более правильной геометрической формы, повышения точности и снижения шероховатости многолезвийным режущим инструментом — зенкером (рис. 5.15,
в).
Развертывание — окончательная обработка цилиндрического или конического отверстия разверткой (обычно после зенкерования) в целях получения высокой точности и малой шероховатости обработанной поверхности (рис. 5.15, г, д).
Цекование — обработка торцовой поверхности отверстия торцовым зенкером для достижения перпендикулярности плоской торцовой поверхности к его оси (рис. 5.15, е).
Зенкованием получают в имеющихся отверстиях цилиндрические или конические углубления под головки винтов, болтов, заклепок и других деталей. На рис. 5.15, ж, з показано зенкование цилиндрического углубления цилиндрическим зенкером (зенковкой) и конического углубления коническим зенкером.
250