
3187
.pdfшве; флюсовые и шлаковые включения; трещины; непропай; деформации местные и общие.
4.9.2.Методы контроля качества сварных
ипаяных соединений
Методы контроля бывают двух типов: разрушающие и неразрушающие.
К разрушающим относятся испытания сварных образ- цов-свидетелей. Сваривают их при тех же самых режимах, что
иизделия, обычно непосредственно перед началом сварки последних. Всесторонние испытания образцов позволяют косвенным образом судить о качестве сварных соединений в изделиях.
Более точно воспроизвести характер нагружения сварных соединений можно на модельных конструкциях или на самих изделиях, которые выборочно подвергают испытаниям вплоть до разрушения.
Неразрушающие методы контроля включают в себя контроль параметров режимов сварки, некоторые испытания свойств сварного шва без его разрушения (например, измерение твердости, химический анализ металла шва, не затрагивающий целостности конструкции), наконец, физические методы контроля (дефектоскопия).
Необходимо отметить особое значение контроля основного металла, сварочных материалов, состояния оборудования
итехнологии сварки.
Виды контроля сварных и паяных конструкций, применяемые в промышленности, достаточно разнообразны. К ним относятся технический осмотр, контроль радиационный, акустический, магнитный, капиллярный и др. Для проверки герметичности и прочности сварных конструкции применяются гидравлические испытания, испытания сжатым воздухом, различного типа течеискателями. Последние методы контроля представляют вид контроля, называемый течеисканием.
201
5. ОСНОВЫ РАЗМЕРНОЙ ОБРАБОТКИ ЗАГОТОВОК ДЕТАЛЕЙ МАШИН
Эксплуатационные свойства машин и механизмов в значительной мере определяются точностью изготовления деталей, качеством их рабочих поверхностей. Под точностью изготовления понимают отклонение фактических геометрических размеров и формы поверхности (неплоскостность, конусообразность, перекос и неперпендикуляpнocть осей и т. д.) от предельных значений, указанных в рабочих чертежах. Качество поверхности характеризуется ее шероховатостью, величиной и знаком остаточных напряжений в поверхностном слое,
ееструктурой и химическим составом. Требования точности и качества назначает конструктор на основе эксплуатационных требований к детали и рекомендаций ГОСТа. Несоблюдение заданных требований точности и качества детали в процессе
ееизготовления может стать причиной снижения эксплуатационных свойств, надежности машин и их преждевременного выхода из строя. Рассмотренные в предыдущих разделах способы формообразования деталей методами литья, обработки давлением и способы с применением сварки по своим технологическим возможностям не в состоянии обеспечить заданную точность, необходимую для изготовления большинства деталей машин и механизмов. Поэтому полученные указанными методами изделия используются в качестве заготовок. Эти заготовки изготавливают несколько больших размеров с технологическим припуском. Наличие припуска позволяет методами размерной обработки получать деталь требуемой точности путем управляемого съема металла припуска. Чем точнее изготовлена заготовка, тем меньше требуемая величина припуска и тем ниже трудоемкость последующей размерной обработки заготовки.
Все способы размерной обработки деталей классифицируют по виду используемой энергии на механические, физи- ко-химические и комбинированные.
202
Задачей всех способов размерной обработки является получение деталей требуемых размеров, формы и качества поверхностей, отвечающих требованиям чертежа, и с максимальной производительностью.
5.1. Основы механической обработки резанием
Обработка резанием является универсальным методом размерной обработки. Метод позволяет обрабатывать поверхности деталей различной формы и размеров с высокой точностью из наиболее используемых конструкционных материалов. Он обладает малой энергоемкостью и высокой производительностью. Вследствие этого обработка резанием является основным, наиболее используемым в промышленности процессом размерной обработки деталей.
Под обработкой материалов резанием понимают механическую обработку, заключающуюся в образовании новых поверхностей путем деформирования и последующего отделения слоев припуска, т. е. путем снятия стружки инструментами, которые называют режущими.
Стружка, таким образом, представляет собой деформированный и отделенный от обрабатываемой детали слой припуска.
Обрабатываемой деталью (заготовкой) называют деталь, обрабатываемую на данной технологической операции.
Обработанной деталью в отличие от обрабатываемой называют деталь, подвергшуюся обработке на данной технологической операции.
Технологической операцией при обработке резанием называют все выполняемые на данном станке действия, связанные с обработкой одной или нескольких деталей.
Припуск на обработку — слой металла, удаляемый при обработке.
203
Впроцессе срезания припуска на детали различают характерные поверхности: обрабатываемую, обработанную и поверхность резания.
Обрабатываемой поверхностью называют исходную поверхность обрабатываемой детали, которая частично или полностью удаляется при обработке.
Обработанная поверхность — это поверхность, полученная на детали в результате обработки.
Поверхностью резания называют поверхность, описываемую режущей кромкой инструмента в движении резания. В большинстве случаев она является переходной между обрабатываемой и обработанной поверхностями, существует только во время резания и исчезает после окончания обработки.
Для того чтобы инструмент мог резать, он должен углубиться в обрабатываемую деталь и перемещаться относительно детали с определенной скоростью и в определенном направлении. Это общее относительное движение заготовки и инструмента в процессе резания называют движением резания. Оно обеспечивается сложением простых движений, сообщаемых инструменту и обрабатываемой детали механизмами станка. Совокупность определенного количества и взаимного расположения простых движений, составляющих движение резания, называют кинематической схемой резания.
Взависимости от числа и характера сочетаемых простых движений различают восемь групп кинематических схем резания: 1) одно прямолинейное движение; 2) два прямолинейных движения; 3) одно вращательное движение; 4) одно вращательное и одно прямолинейное движение; 5) два вращательных движения; 6) два прямолинейных и одно вращательное движение; 7) два вращательных и одно прямолинейное движение; 8) три вращательных движения. Кинематические схемы резания определяют метод обработки, вид станка и режущего инструмента.
Наиболее распространена обработка с одним прямолинейным или с одним прямолинейным и одним вращательным
204
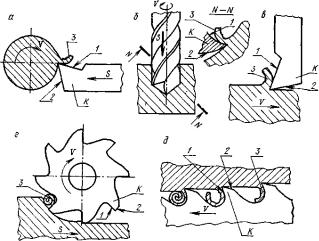
движением. Так, при обработке на строгальных станках (рис. 5.1, в) резец движется относительно детали прямолинейно. В зависимости от типа станка это движение получает или резец, или обрабатываемая деталь. Прямолинейное перемещение инструмента относительно детали реализуется также в процессе протягивания (рис.5.1, д). В процессе точения (рис. 5.1, а), сверления (рис. 5.1, б) и фрезерования (рис. 5.1, г) сочетаются одно вращательное движение и одно поступательное. Вращательное движение сообщается или детали (точение), или режущему инструменту (фрезерование). Поступательное перемещение придают инструменту (точение, сверление) или детали (фрезерование). При сверлении вращается и поступательно движется только сверло (обработка на сверлильных станках), если вращается деталь, а сверло поступательно перемещается, то сверление выполняют на токарных станках.
Рис. 5.1. Основные виды обработки резанием: а — точение; б — сверление; в — строгание;
г — фрезерование; д — протягивание; 1 — передняя поверхность; 2 — задняя поверхность режущего клина К;
3 — стружка
205
В зависимости от того, какое из простых движений сообщают детали, а какое инструменту, определяется тип станка. Сущность метода обработки от этого не зависит и устанавливается только кинематической схемой резания, а также соотношением скоростей простых движений резания.
Простое составляющее движение, имеющее наибольшую скорость, называют главным движением, а его скорость
— скоростью главного движения, которую в соответствии с принятой терминологией будем называть просто скоростью резания. Это движение необходимо для превращения срезаемого слоя металла в стружку. Чтобы процесс резания осуществлялся непрерывно (точение) или повторялся периодически (строгание), дополнительно необходимо еще одно простое движение — движение подачи. Скорость движения подачи во много раз меньше скорости резания, и ее принято называть просто подачей. Геометрическую сумму скоростей главного движения и подачи называют истинной скоростью резания, которую можно определить так же, как скорость движения резания рассматриваемой точки режущей кромки инструмента. Истинную скорость резания и другие условия выполнения процесса резания, характеризуемые значениями его параметров, называют режимом резания, а скорость резания, подачу и другие элементы условий выполнения процесса — элементами режима резания.
5.1.1. Сущность обработки резанием
Основным режущим элементом любого инструмента является режущий клин (рис. 5.1). Его твердость и прочность должны существенно превосходить твердость и прочность обрабатываемого материала, обеспечивая его режущие свойства. К инструменту прикладывается усилие резания, равное силе сопротивления материала резанию, и сообщается перемещение относительно заготовки со скоростью v.
206
Во всех случаях режущий клин имеет по меньшей мере две рабочие поверхности: переднюю и заднюю. По передней поверхности 1 сходит отделяемая в процессе резания стружка 3, а задняя поверхность 2 обращена в сторону обрабатываемой детали (рис. 5.1). Пересечение передней и задней поверхностей образует край клина, называемый режущей кромкой или режущим лезвием. Форму рабочих поверхностей режущего клина, расположение этих поверхностей относительно друг друга и относительно составляющих движения резания называют геометрией режущей части или геометрическими параметрами, от которых зависит работоспособность инструмента.
Упрощенно процесс резания можно представить следующей схемой. В начальный момент процесса резания, когда движущийся резец под действием силы Р (рис. 5.2) вдавливается в металл, в срезаемом слое возникают упругие деформации. При движении резца упругие деформации, накапливаясь по абсолютной величине, переходят в пластические. В прирезцовом срезаемом слое материала заготовки возникает сложное упругонапряженное состояние. В плоскости, перпендикулярной к траектории движения резца, возникают нормальные напряжения ζy, а в плоскости, совпадающей с траекторией движения резца, — касательные напряжения ηx. В точке приложения действующей силы значение ηx наибольшее. По мере удаления от точки А ηx уменьшается. Нормальные напряжения ζy вначале действуют как растягивающие, а затем быстро уменьшаются и, переходя через нуль, превращаются в напряжения сжатия. Срезаемый слой металла находится под действием давления резца, касательных и нормальных напряжений.
Сложное упругонапряженное состояние металла приводит к пластической деформации, а рост ее — к сдвиговым деформациям, т. е. к смещению частей кристаллов относительно друг друга. Сдвиговые деформации происходят в зоне стружкообразования АВС, причем деформации начинаются по плоскости АВ и заканчиваются по плоскости АС, в которой завершается разрушение кристаллов, т. е. скалывается элемен-
207
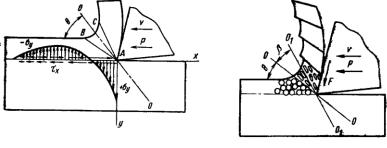
тарный объем металла и образуется стружка. Далее процесс повторяется и образуется следующий элемент стружки.
Рис. 5.2. Упругонапряженное |
|
состояние металла |
Рис. 5.3. Схема процесса |
при обработке резанием |
образования стружки |
Условно считают, что сдвиговые деформации происходят по плоскости 00 (рис. 5.2), которую называют плоскостью сдвига. Она располагается примерно под углом θ = 30° к направлению движения резца. Угол θ называют углом сдвига. Срезанный слой металла дополнительно деформируется вследствие трения стружки о переднюю поверхность инструмента. Структуры металла зоны АВС и стружки резко отличаются от структуры основного металла. В зоне АВС расположены деформированные и разрушенные кристаллы, сильно измельченные и вытянутые в цепочки в одном, вполне определенном направлении, совпадающем в направлением плоскости 0101, которая с плоскостью сдвига составляет угол β (рис.
5.3).
Характер деформирования срезаемого слоя зависит от физико-механических свойств материала обрабатываемой заготовки, геометрии инструмента, режима резания, условий обработки. В процессе резания заготовок из пластичных металлов и сталей средней твердости превалирует пластическая деформация. У хрупких металлов пластическая деформация практически отсутствует. Поэтому при резании деталей из хрупких металлов угол β близок к нулю, а при резании дета-
208
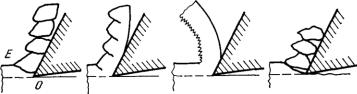
лей из пластичных металлов β доходит до 30°, что свидетельствует о сложном внутреннем процессе деформирования кристаллов и формировании новой структуры.
Внешний вид стружки характеризует процессы деформирования и разрушения материала, происходящие при резании. Различают четыре возможных типа образующихся стружек: элементная, суставчатая, сливная и стружка надлома
(рис. 5.4).
а) |
б) |
в) |
г) |
Рис. 5.4. Типы образующихся при резании стружек:
а – элементная, б – суставчатая, в – сливная, г - надлома
Сливная стружка обычно получается при обработке относительно мягких пластичных материалов. Пластичные материалы повышенной и высокой твердости дают суставчатую и элементную стружку. При резании хрупких материалов чаще образуется элементная стружка, в случае повышенной твердости — стружка надлома.
Для снижения сил трения и нагрева инструмента применяют принудительное охлаждение зоны резания смазочноохлаждающими средами (СОС), подавая их в зону резания специальными устройствами.
Детали и инструменты закрепляются в специальных органах станка или приспособлениях. Станок, приспособление, инструмент и деталь образуют силовую систему (СПИД), передающую усилие и движение резания от привода станка режущему инструменту и детали.
209

5.1.2. Усадка стружки и наростообразование при резании
Длина стружки всегда значительно меньше длины пути, проходимого резцом. При этом стружка, утолщаясь, остается примерно той же ширины. Объясняется это явление относительным перемещением элементов при образовании стружек. Усадка численно характеризуется коэффициентом продольной усадки
k1 L0 1 L1
или коэффициентом поперечной усадки (утолщения стружки)
k2 a 1, ac
где L0 — длина стружи; L1 — путь резца; ас — толщина стружки; а — толщина срезаемого слоя.
Полагают, что k1 = k2, так как значительного уширения срезаемого слоя не наблюдается.
Иногда используется термин «усадка»:
k |
1 |
|
L1 |
1. |
|
k1 |
L0 |
||||
|
|
|
Коэффициент усадки k1 = 0,4…0,7. Известны материалы с k1 = 0,2 и даже k1 = 0,15.
Усадка характеризует степень деформации при резании, т. е. является весьма универсальным показателем процесса резания: при отрицательных передних углах усадка больше, чем при положительных, применение смазывающеохлаждающей жидкости (СОЖ) облегчает процесс стружко-
210