
387
.pdfуровне на каждый отказ на приемосдаточных испытаниях аппаратуры заказчику и термопрогоне заполнялся так называемый КУН (карточка учета неисправности), где фиксировалось, какому пункту ТУ изделие не соответствует, причина, и, главное, мероприятия по недопущению отказа впредь (табл. 2).
|
|
|
Таблица 1 |
|
Применение статистических методов на предприятии |
||
|
|
|
|
№ |
Операция |
Процент |
Условия применения |
|
|
контроля |
|
1 |
Входной контроль |
5 |
Выборочный по ГОСТ |
2 |
Операционный контроль в |
5, но не ме- |
|
|
механическом производстве |
нее 2 изделий |
Выборочный |
|
|
из партии |
|
3 |
Приемочный контроль в |
По таблице |
Статистический по стандар- |
|
механическом производстве |
стандарта |
ту предприятия |
4 |
Приемочный контроль гото- |
20 |
Выборочныйпоплануприе- |
|
вой продукции |
|
мочногоконтроляна |
|
|
|
автоматизированныхстендах |
|
|
|
|
Таблица 2 |
|
Основная структура карточки учета неисправности |
|||
|
|
|
|
|
№ п/п |
|
|
|
|
1 |
|
Этап обнаружения |
Термопрогон, ПСИ, подчеркнуть |
|
2 |
|
Формулировка отказа |
|
|
3 |
|
Причина отказа |
|
|
4 |
|
Способ восстановления |
|
|
|
|
изделия |
|
|
5 |
|
Мероприятия |
|
|
6 |
|
Представитель ЛАО |
|
Дата |
7 |
|
Представитель ОТК |
|
|
8 |
|
Представитель ПЗ |
|
|
Если виновником был конструктор, то должна была быть его подпись со сроком выпуска конструкторского извещения. Второй уровень – обобщение, анализ, систематизация результатов за месяц и направление руководству. В отдел главного конструктора направлялись вместе со статистикой отказов аппаратуры так называемые «Рекомендации» с описанием узких мест и предложениями по их решению.
51
В течение 10 дней должен был поступить ответ на «Рекомендацию». Если в течение нескольких месяцев результата не было, то задействовался третий уровень. Один раз в квартал вопрос в форме отчета выносился на заседание постоянно действующей комиссии по качеству ПДКК под председательством главного инженера с участием главных специалистов предприятия.
Например, был случай, когда ПДКК по одному вопросу заседала не один раз. В изделии применялись магнитострикционные фильтры. Заявленной постоянной рабочей температурой окружающей среды для аппаратуры была температура +50 °С, при которой и проверялись фильтры, изготовляемые на смежном предприятии. Но конструктор не учел температуру их перегрева за счет тепла близко расположенных источников питания. Исследования показали, что температура перегрева доходила до 11 градусов. Контроль фильтров при максимальной суммарной температуре приводил к браку в 50 %, что было экономически неприемлемо. Компромисс нашли в селекции – фильтры с большим запасом по температуре применяли у источников питания, с меньшим – подальше от них.
При таком подходе удалось за два года число отказов уменьшить почти на порядок. Потом началась перестройка. У начальников ЛАО разных цехов не было единой политики, и все ЛАО были объединены в отдел надежности. В качестве отдела подразделение было малочисленным и его через некоторое время присоединили к испытательной станции, поскольку работники ЛАО часто пользовались камерами для поиска отказов аппаратуры. Это было ошибкой – работники ЛАО оторвались от производства. Людей переориентировали на другие задачи, а анализ отказов возложили на регулировщика. Связь с конструктором ослабла. И хотя регулировщик заполняет книги отказов и карты ремонта, а статистика оформляется отделом надежности, сертификации и испытаний (так сейчас называется испытательная станция) во внешне красивый отчет, эти данные недостоверны. Туда попадает не только то, что отказывало, но и то, что менялось во время поиска отказов. Регулировщик часто при поиске действует интуитивно, пока не попадет при замене в нужный элемент и изделие не заработает как положено (соответствие НД) Разобраться в серьезном отказе у него не хватает времени и квалификации.
Время. Некоторые отказы требуют серьезной работы в течение нескольких дней. Часто для выявления причины отказов требуется
52
составлять программу исследования для выявления отказов, особенно так называемых «самоустраняющихся», а кроме того, необходимо время для ее выполнения.
Квалификация. Для того чтобы оппонировать конструктору, нужно иметь не меньшую квалификацию. Часто приходилось изучать нормативную документацию для выявления требований, предъявляемых к элементу, проводить расчеты, чтобы убедиться, не превысил ли их конструктор. И главное – технически грамотно ставить конструктору задачу. Правильно поставленная задача – половина успеха ее решения. В науке квалификация постановщика задачи должна быть не ниже того, кто будет ее решать.
Выводы:
1.Чтобы вторая модель работала в полную силу, нужно повышать достоверность анализа отказов, вернуться к принципам работыЛАО.
2.Затраты на зарплату инженеров с лихвой окупятся повышением качества изделий как стратегическим показателем в условиях рыночной экономики.
Библиографический список
1.Статистические методы повышения качества / под ред. Х. Куме; пер. с англ. – М.: Финансы истатистика,1990. – 304 с.
2.ГОСТ Р ИСО/ТО 10 017 – 2005. Статистические методы. Руководство по применению в соответствии с ГОСТ Р ИСО 9001.
Получено 25.01.2007
53
УДК 621.3
В.Н. Осколков, Л.Г. Бабушкина
Пермский государственный технический университет
ОПЫТ ПРИМЕНЕНИЯ ОТБРАКОВОЧНЫХ ИСПЫТАНИЙ
Представлено проведение отбраковочных испытаний на серийно выпускаемой аппаратуре гибкого мультиплексирования на 30 каналов OGM-30 Е, а также плат средней сложности, имеющих самостоятельную поставку.
Всоответствии с требованиями ГОСТ В 15.307 – 77 аппаратура на стадии серийного изготовления подвергается периодическим испытаниям (ПИ) с целью контроля ее качества и стабильности технологического процесса в период между предшествующими и очередными испытаниями.
Периодически проводя испытания отдельных образцов (партий) готовой продукции, можно контролировать стабильность технологического процесса изготовления продукции, что является одним из важнейших факторов обеспечения ее высокого качества и надежности. Эти положения закреплены не только в отечественных, но и зарубежных стандартах, например, МЭК и ИСО.
Считается, что более оперативно и эффективно выявлять дефекты производства и получать информацию о текущем состоянии
истабильности технологического процесса производства аппаратуры можно путем внедрения отбраковочных испытаний [1, 2, 3].
Взарубежной практике отбраковочные испытания под названи-
ем «Envizonmental Stress Screcning» (ESS) были внедрены в 1988 году в ВВС США директивой «R & M 2000 Envizonmental Stress Sc».
Вразработанном техническим комитетом по стандартизации ТК № 319 «Надежность ЭВМ и РЭА военного назначения» руководящем документе РД В 319. 02. 24 – 99 «Комплексная система контроля качества. Аппаратура, приборы, устройства и оборудование военного назначения. Методы проведения отбраковочных испытаний» был учтен передовой отечественный и зарубежный опыт в части методов планирования и проведения отбраковочных испытаний.
54
Целями внедрения отбраковочных испытаний, указанных в РД В, являются:
−выявление и устранение скрытых дефектов аппаратуры, возникающих при ее изготовлении и являющихся причиной повышения интенсивности отказов в начальный период эксплуатации;
−разработка мероприятий по недопущению появления дефектов при производстве аппаратуры;
−оценка стабильности технологического процесса производства аппаратуры.
С учетом указанных целей в руководящем документе РД В 319.
02.24– 99 дано следующее определение отбраковочных испытаний: «Отбраковочные испытания – составная часть технологического про-
цесса изготовления аппаратуры, в ходе которой для выявления и устранения скрытых дефектов производства аппаратура и ее составные части подвергаются воздействиям различных внешних факторов, в том числе с нормами испытаний, которые могут превышать нормы, установленные в НД или эксплуатационные».
При внедрении отбраковочных испытаний аппаратуры целесообразно придерживаться следующей последовательности процедур, изложенных в РД В 319. 02.24 – 99:
−определить составные части (уровни разукрупнения) аппаратуры (плата, блок, стойка и т.д.) которые целесообразно подвергнуть отбраковочным испытаниям;
−выбрать виды воздействующих вредных факторов, в наибольшей степени влияющих на проявление скрытых дефектов;
−на основе анализа информации о предполагаемых видах дефектов, характерных для собственного производства, информации о стойкости материалов и изделий, используемых в аппаратуре, и с учетом опыта ее разработки, установить уровни и продолжительность воздействия внешних факторов.
В соответствии с изложенными рекомендациями на нашем предприятии, занимающемся серийным производством аппаратуры систем передачи, был разработан стандарт предприятия по проведению отбраковочных испытаний и составлена программа отбраковочных испытаний, согласно которой для отбраковочных испытаний была выбрана серийно выпускаемая аппаратура гибкого мультиплексирования на 30 каналов ОGM–30Е, входящие платы средней
55

сложности, имеющие самостоятельную поставку: платы ОК–120 – 650 шт., СХ–120 – 50 шт., СВ–120 – 50 шт. и блок ОGM–12 – 3 шт. (табл. 1).
|
Таблица 1 |
|
Выполнение рекомендаций нормативного документа |
||
|
|
|
Рекомендации РД В 319.02.24-99 |
Вошли в программу ОИ |
|
1. Уровень разукрупнения определяет кон- |
Модуль, блок |
|
структор с изготовителем |
|
|
2. Широкополосная случайная вибрация, |
Синусоидальная с ручным ка- |
|
допускается синусоидальная в режиме |
чанием частоты |
|
качающейся частоты: |
Частотный диапазон 20–2000 Гц |
|
частотный диапазон 20–2000 Гц; |
|
|
среднеквадратическое значение уровня ус- |
6 g |
|
корения – 6 g; |
|
|
максимальная спектральная плотность уско- |
Соответствует |
|
рения в диапазоне от 50–80 Гц до 350–500 Гц |
|
|
– до 0,04 g2/Гц; |
10 мин |
|
время воздействия ШСВ 5–10 мин на ось; |
|
|
число осей – 2, перпендикулярно плоскости |
В плоскости разъемов |
|
платы, в плоскости разъемов |
|
|
3. Циклирование |
|
|
Тmin – минус 50–60 °С |
Минус 60 °С |
|
Тmax – 50–70 °С |
Плюс 70 °С |
|
∆Т/∆t – однокамерный –5–10 °С мин |
Не принят |
|
– двухкамерный – 50 °С мин |
Двухкамерный |
|
Время выдержки (по табл. 2) |
По табл. 2 |
|
Число циклов (по РД) |
2 |
|
4. Электротермотренировка |
Не введена, отсутствие отказов |
|
|
в серийной термотренировке |
|
Внешними воздействующими факторами были выбраны испытания на вибропрочность и испытания термоциклированием.
Испытания на вибропрочность проводились следующим образом. Платы устанавливались в технологическую кассету, которая фиксировалась на столе вибростенда.
Частота вибрации стенда плавно от руки изменялась от 20 Гц до 2000 Гц и обратно при среднеквадратичном ускорении 6 g в течение 10 мин.
Термоциклирование проводилось при температуре +70°С и –60°С. Время выдержки выбиралось из табл. 2.
56

|
|
Таблица 2 |
|
Время выдержки при термоциклировании |
|
|
|
|
|
Масса, кг |
Время выдержки, ч |
До 2 включительно |
2 |
|
От 2 до 10 включительно |
3 |
|
От 10 |
до 20 включительно |
4 |
От 20 |
до 50 включительно |
6 |
От 50 |
до 100 включительно |
8 |
Для термоциклирования использовалось две камеры, предварительно выведенные на режим. Изделия сначала подвергались воздействиюположительнойтемпературы, затем отрицательной, всего два цикла.
Анализ отказов проводила специальная комиссия с участием ин- женера-конструктора, инженера надежности, ОТК и испытателя. До и после испытаний проводились приемо-сдаточные испытания изделий.
Технико-экономический эффект от внедрения отбраковочных испытаний обусловлен следующими факторами:
−сокращение затрат на проведение ремонтов аппаратуры в эксплуатации, так как уменьшается их число, стоимость работ по устранению дефектов в заводских условиях ниже, чем в условиях эксплуатации (примерно в 5–7 раз), а качество ремонта существенно выше;
−сокращение простоев аппаратуры в эксплуатации, снижение штрафовзаотказыаппаратурывпериодгарантийногообслуживанияидр.
Численное значение эффективности определяется разницей между экономией, достигаемой за счет сокращения числа ремонтов аппаратуры в условиях эксплуатации, а также за счет поставки в эксплуатацию аппаратуры, имеющей более высокую надежность, и затратами на организацию и проведение отбраковочных испытаний.
Эои – Собщ > 0,
где Эои – экономия от внедрения отбраковочных испытаний; Собщ – общие затраты на проведение отбраковочных испытаний.
При проведении отбраковочных испытаний из всех изделий отказало только одно изделие из-за покупного трансформатора при проведении испытаний на термоциклирование. Поставщику претензия не предъявлялась из-за отсутствия согласования превышения норм воздействия при проведении отбраковочных испытаний.
57
Учитывая большую трудоемкость испытаний и отсутствие отказов аппаратуры, было решено отбраковочным испытаниям аппаратуру не подвергать.
Таким образом, причины неэффективности отбраковочных испытаний в данных условиях следующие:
−при изготовлении аппаратуры применяются надежные комплектующие импортного производства;
−сборка изделий производится на автоматической линии по технологии поверхностного монтажа, позволяющей минимизировать производственные дефекты;
−отбраковочные испытания не эквивалентны периодическим испытаниям, поскольку последние проводятся по гораздо большей номенклатуре параметров, особенно для аппаратуры систем передачи информации.
Библиографический список
1.Доминич А.П. Отбраковочные испытания радиоэлектронной аппаратуры – эффективный путь повышения ее качества и надежности / А.П. Доминич, В.Н. Писарев // Технологии, оборудование, материалы. Экономика и производство. – 1998. – №12.
2.Доминич А.П. К вопросу о проведении периодических испытаний аппаратуры / А.П. Доминич, В.Н. Писарев // Вестник Военного Регистра. – 2001. – №7.
3.РД В 319.02.24 –99 Комплексная система контроля качества. Аппаратура, приборы, устройства и оборудование военного назначения. Методы проведения отбраковочных испытаний.
Получено 25.01.2007
58
УДК. 621.3.17.3
А.С. Патрикеев, А.А. Старков
Пермский государственный технический университет
КОНТРОЛЬ ПРОЦЕССА СУШКИ ГИПСОКАРТОННЫХ ЛИСТОВ ЕМКОСТНЫМИ ДАТЧИКАМИ
Приводятся результаты исследования емкостного датчика, с помощью которого можно контролировать процесс сушки при производстве гипсокартонных и гипсополимерных листов.
При изготовлении гипсокартонных (ГКЛ) и гипсополимерных листов возникает необходимость постоянного контроля за влажностью листов в процессе их сушки в конвейерной сушилке. В настоящее время это осуществляется термогравиметрическим методом, путем отбора проб и высушивания их в лабораторных условиях. Этот процесс занимает более четырех часов и не дает возможности оперативно управлять параметрами сушильной установки для сохранения заданного качества продукции при оптимальном расходе тепловой и электрической энергии.
Для решения задачи непрерывного автоматического контроля влажности ГКЛ можно использовать емкостные датчики. Основным информативным параметром емкостного датчика при измерении влажности является изменение емкости конденсатора в зависимости от влажностиконтролируемого материала, помещенного между его электродами.
Однако эта задача при измерении влажности трехслойного материала, каким являются ГКЛ, имеет свои особенности: емкость датчика существенно зависит от диэлектрических характеристик каждого слоя, а они, в свою очередь, меняются от влажности по-разному на разных стадиях процесса сушки.
Рассмотрим, как изменяется диэлектрическая проницаемость трехслойного диэлектрика при изменении диэлектрических характеристик отдельных слоев.
Емкость конденсатора с несовершенным диэлектриком рассматривают в виде кажущейся емкости.
Cк = C0 ε(1+ tg2 δ) , |
(1) |
|
59 |
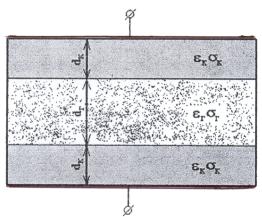
где С0 – воздушная емкость, т.е. емкость конденсатора при отсутствии исследуемого материала; ε – диэлектрическая проницаемость материала; tg δ – тангенс угла активных потерь.
В свою очередь, воздушная емкость плоскопараллельного конденсатора определяется выражением
C0 = ε0 S / d , |
(2) |
где ε0 – диэлектрическая постоянная воздуха; S – площадь электро-
дов; d – расстояние между электродами.
Тангенсуглаактивныхпотерьзависитотпроводимостиматериала. На рис. 1 изображен плоскопараллельный конденсатор с образ-
цом гипсокартонного листа.
Рис.1. Плоскопараллельный конденсатор с гипсокартонным листом
Эквивалентную схему замещения емкостного первичного преобразователя для гипсокартонных листов (см. рис. 1) можно представить в виде последовательного соединения трех кажущихся емкостей, две из которых представляют собой емкости с картоном Cкк, а одна емкость с гипсовым сердечником Cкг. Каждая из этих емкостей будет выражаться формулой
C |
кк |
= ε C |
|
(1+ tg2δ |
к |
) , |
(3) |
|
|
к |
0к |
|
|
|
|||
C |
= ε |
С |
0г |
(1+ tg2δ |
) , |
(4) |
||
|
кг |
г |
|
|
г |
|
|
где εк , εг – диэлектрические проницаемости картона и гипса соответственно; tgδк, tgδг – тангенс угла активных потерь с картоном и гипсовым сердечником; С0к ,С0г – воздушные емкости плоскопараллель-
60