
387
.pdfПолучение такой информации для лопаточных машин требует обширных и дорогостоящих экспериментальных исследований, которые можно существенно сократить применением методов математического моделирования.
Реализация разработанного алгоритма на ЭВМ дает возможность автоматизировать процесс виброиспытаний сложных механических конструкций, причем возможно установить наличие и место расположения дефектов, которые визуально не наблюдаются.
В качестве численной процедуры используется МКЭ для определения собственных частот и форм колебаний для различных величин имест расположения дефектов однороднойизотропнойпластины.
Для правомерности использования пакета ANSYS в данном исследовании сравним полуаналитическое решение с использованием пакета Mathcad [2] для однородной изотропной пластинки с численным решением в среде ANSYS.
Для решения вариационной задачи по методу Ритца, т.е. для нахождения форм колебаний пластинки, удовлетворяющих вариационному уравнению, строится минимизирующая форма в виде конечного ряда
n |
|
w(x, y) = ∑ai wi (x, y) , |
(1) |
i=1
где wi (x, y) – базисные функции, которые представляются в виде произ-
ведения функции, одна из которых зависит только от x, другая от y. Ряд (1) в этом случае имеет вид
n n |
|
w(x, y) = ∑∑aij Xi (x) Yj ( y). |
(2) |
i=1 j =1
Функции X i (x) и Yj ( y) – это собственные формы колебаний
однородных стержней, удовлетворяющих краевым условиям, соответствующим способам закрепления краев пластинки. Такие формы строятся с помощью функций Крылова первого рода:
λi |
x |
+ |
λi x |
+ |
||||
Xi (x) = sin |
a |
|
Ai cos |
a |
|
|||
|
|
|
|
|
(3) |
|||
|
|
λi x |
|
|
|
|||
|
λi x |
|||||||
+ Bi sh |
|
a |
|
+ Ci ch |
|
a |
, |
|
|
|
|
|
|
|
|
||
|
|
|
|
|
|
|
|
91 |
|
|
λ j y |
|
|
|
λ j y |
|
||
Y |
( y) = sin |
|
|
+ A |
j |
cos |
|
|
+ |
|
|
||||||||
j |
|
b |
|
|
|
b |
|
|
|
|
|
|
|
|
|
|
|
|
|
|
λ j y |
|
|
|
λ j y |
||
+ B |
j |
sh |
|
|
+ C |
j |
ch |
|
. |
|
|
||||||||
|
|
b |
|
|
|
b |
|
||
|
|
|
|
|
|
|
|
Постоянные Ai , Bi ,Ci , Aj , B j ,C j ,λi ,λ j находятся из краевых ус-
ловий. Предложенный алгоритм может быть протестирован на примере определения основных динамических характеристик пластинки, жестко закреплённой по одной из сторон (длина – 0,15 м; ширина – 0,05 м; толщина – 0,00254 м; модуль упругости – 2 105 МПа; коэффициент Пуассона – 0,3; плотность – 7807 кг/м3).
Для решения тестовой задачи ограничимся четырьмя балочными функциями:
x1(x) = sin |
λ1 |
x |
|
−1.3622 cos |
λ1 |
x |
|
− sh |
λ1 |
x |
|
+1.3622 ch |
λ1 |
x |
|
|
|
|
|
||||||||||||
|
|
|
|
|
|
|
|
|
|
|
|
|
|
|
|
|
|
a |
|
|
a |
|
|
a |
|
|
a |
x2(x) = sin λ3 |
|
x |
− |
0.98187 cos λ3 |
|
x |
− |
|
|||||||||||||||||||||||||
|
|
|
|
|
|
|
|||||||||||||||||||||||||||
|
|
|
|
|
|
|
|
|
a |
|
|
|
|
|
|
|
|
|
|
|
|
|
|
|
|||||||||
|
|
|
|
|
|
|
|
|
|
|
|
|
|
|
|
|
a |
|
|
|
|
||||||||||||
|
|
|
|
x |
|
|
|
|
|
|
|
x |
|
|
|
|
|
|
|
|
|
||||||||||||
− sh |
λ3 |
|
|
|
|
+ |
0.98187 ch λ3 |
|
|
|
|
|
|
|
|
|
|
|
|
||||||||||||||
|
a |
a |
|
|
|
|
|
|
|
|
|||||||||||||||||||||||
|
|
|
|
|
|
|
|
|
|
|
|
|
|
|
|
|
|
|
|
||||||||||||||
y1( y) = sin |
λ2 |
y |
|
−1.0178 cos |
λ2 |
|
y |
|
+ |
|
|
||||||||||||||||||||||
|
|
|
|
|
|
|
|
||||||||||||||||||||||||||
|
|
|
|
|
|
|
|
|
|
|
|
|
|
|
|
|
|
|
|
|
|
|
|
|
|
|
|
|
|||||
|
|
|
|
|
|
|
|
|
|
|
|
b |
|
|
|
|
|
|
|
|
|
b |
|
|
|
(4) |
|||||||
|
|
|
|
|
|
|
|
y |
|
|
|
|
|
|
|
|
y |
|
|
|
|
|
|
|
|||||||||
|
|
|
|
|
|
|
|
|
|
|
|
|
|
|
|
|
|
|
|
|
|
||||||||||||
+ sh |
λ2 |
|
|
|
|
|
|
−1.0178 ch λ2 |
|
|
|
|
|
|
|
|
|
|
|
|
|||||||||||||
|
|
|
|
|
|
|
|
|
|
|
|
|
|
||||||||||||||||||||
|
|
|
|
|
|
|
|
b |
|
|
|
|
|
|
|
|
b |
|
|
|
|
|
|
|
|
||||||||
y2( y) = sin |
λ4 |
y |
|
− 0.999223 cos |
λ4 |
|
y |
|
+ |
||||||||||||||||||||||||
|
|
|
|
||||||||||||||||||||||||||||||
|
|
|
|
|
|
|
|
|
|
|
|
|
b |
|
|
|
|
|
|
|
|
|
|
|
|
|
|
|
|||||
|
|
|
|
|
|
|
|
|
|
|
|
|
|
|
|
|
|
|
|
|
|
|
|
|
|
b |
|
||||||
|
|
|
|
|
|
|
|
y |
|
|
|
|
|
|
|
y |
|
|
|
|
|
||||||||||||
+ sh |
λ4 |
|
− 0.999223 ch |
λ4 |
. |
|
|
|
|
||||||||||||||||||||||||
|
|
|
|
|
|
||||||||||||||||||||||||||||
|
|
|
|
|
|
|
|
b |
|
|
|
|
|
|
b |
|
|
|
|
||||||||||||||
Коэффициенты |
λ1 = 1.875 ; |
λ2 = 4.73 ; |
|
|
|
λ3 = 4.694 ; |
λ4 = 7.853 |
представлены в таблицах [1]. Тогда ряд (2) запишется следующим образом:
w(x, y) = a11 X1 (x) Y1 ( y) + a12 X1 (x) Y2 |
( y) + |
(5) |
+ a21 X 2 (x) Y1 ( y) + a22 X 2 (x) Y2 ( y). |
|
|
|
|
92
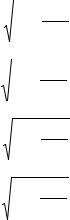
Решая вариационную задачу по методу Ритца
∂ |
(T |
− Π |
|
) = 0 , |
(6) |
|
max |
||||
|
max |
|
|
|
|
∂aij |
|
|
|
|
приходим к системе уравнений вида
(A p2 |
− B ) a = 0, (i = |
1,n |
, j = |
1,n |
) , |
(7) |
ij |
ij ij |
|
которая имеет нетривиальное решение, в случае если определитель системы равен нулю. Спектральная задача решалась в пакете Mathcad. В результате получены приведенные собственные частоты колебаний.
p = −8.103359088, |
8.103359088, |
−48.89086863, |
48.89086863, |
(8) |
||||||
−52.21990492, |
52.21990492, |
−143.7757105, |
143.7757105 |
|
|
|||||
или, с учетом механических свойств материала и размера пластинки, |
|
|||||||||
|
|
|
|
|
|
|
|
|
||
p11 = 8.103359088 |
|
9.8 |
D |
, |
p1 = 95.906 Гц; |
|
|
|||
|
|
|
|
γ h |
|
|
|
|
|
|
|
|
|
|
|
|
|
|
|||
p12 = 48.89086863 |
9.8 |
D |
, |
p2 = 588.35 Гц; |
|
|
||||
|
|
|
|
γ h |
|
|
|
|
|
|
p21 = 52.21990492 |
9.8 |
D |
, |
p3 = 601.16 Гц; |
|
(9) |
||||
|
|
|
|
γ h |
|
|
|
|
|
|
p22 =143.7757105 |
9.8 |
D |
, |
p4 =1694.3 Гц. |
|
|
||||
|
|
|
|
γ h |
|
|
|
|
|
Далее находим амплитудные коэффициенты аij. Подставляя их в уравнение (5), можем построить формы колебаний. Далее представленную выше тестовую задачу решаем с помощью пакета ANSYS [3].
При этом были выбраны элементы PLANE 42. Результаты расчетов и сравнения приведены в табл. 1.
Анализируя данные табл. 1, можно сделать вывод, что решение, полученное с помощью пакета ANSYS 7.0, с достаточной точностью для инженерной практики совпадает с аналитическим решением. Следовательно, ANSYS 7.0 можно эффективно использовать для решения динамических задач и получения результатов для автоматизации процесса вибродиагностики в реальном режиме времени.
93
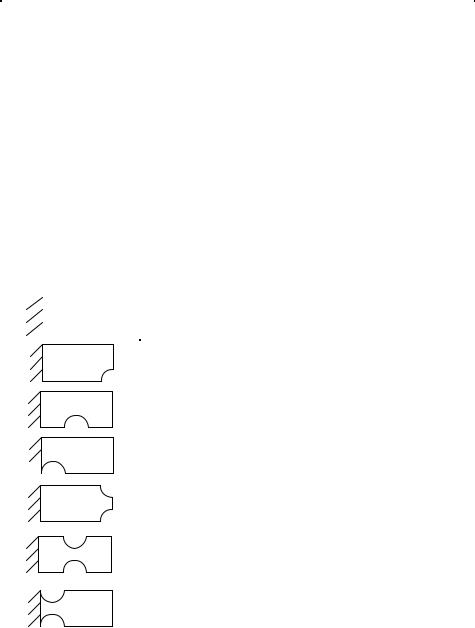
|
|
|
Таблица 1 |
|
|
|
|
|
Приведенные частоты пластинки |
|
|
ANSYS 7.0, Гц |
Аналитически, Гц |
|
Погрешность, % |
98,69 |
95,906 |
|
2,82 |
595,437 |
588,35 |
|
1,19 |
625,981 |
601,19 |
|
3,96 |
1751,03 |
1694,3 |
|
3,2 |
В качестве иллюстрации приведем промежуточные результаты обработки динамических характеристик, полученных для систем с дефектами. Из рисунков и табл. 2 видно место расположения дефекта и его размер.
|
|
|
|
|
|
Таблица 2 |
|
|
|
|
|
|
|
Расположение |
Р1 |
Р2 |
Р3 |
Р4 |
||
|
дефекта |
|||||
|
|
|
|
|
||
|
|
|
95,906 |
588,35 |
601,19 |
1694,3 |
|
|
|
||||
|
|
|
|
|
|
|
|
|
|
|
|
|
|
|
|
|
95,889 |
581,66 |
607,27 |
1667,70 |
|
|
|
|
|
|
|
|
|
|
93,789 |
565,05 |
586,68 |
1635,50 |
|
|
|
|
|
|
|
|
|
|
90,850 |
547,81 |
580,80 |
1417,80 |
|
|
|
|
|
|
|
|
|
|
98,004 |
603,75 |
607,88 |
1698,80 |
|
|
|
|
|
|
|
|
|
|
92,862 |
560,01 |
570,34 |
1533,60 |
|
|
|
|
|
|
|
|
|
|
83,542 |
523,27 |
553,10 |
1104,60 |
|
|
|
|
|
|
|
Графики представляют зависимости собственных частот от местоположения и размера трещины.
На рис.1, а, б, в, г представлены соответственно зависимости 1, 2, 3, 4-й частот от местоположения трещины [4].
94

|
94,5 |
|
|
|
|
|
94 |
|
|
|
|
, Гц |
93,5 |
|
|
|
|
93 |
|
|
|
|
|
частота |
|
|
|
|
|
92,5 |
|
|
|
|
|
92 |
|
|
|
|
|
|
91,5 |
|
|
|
|
|
91 |
|
|
|
|
|
90,5 |
|
|
|
|
|
0,025 |
0,05 |
0,075 |
0,1 |
0,125 |
|
|
|
Длина, м |
|
|
|
|
|
а |
|
|
|
576 |
|
|
574 |
|
Гц |
572 |
|
570 |
||
частота, |
568 |
|
566 |
||
|
||
|
564 |
562
560
558
556
0,025 0,05 0,075 0,1 0,125
длина, м
в
94,5 |
|
|
|
|
|
|
|
94 |
|
|
|
|
|
93,5 |
|
|
|
|
|
|
Гц |
93 |
|
|
|
|
|
|
|
|
|
|
|
|
92,5 |
|
|
|
|
|
|
частота, |
92 |
|
|
|
|
|
91,5 |
|
|
|
|
|
|
|
91 |
|
|
|
|
|
90,5 |
|
|
|
|
|
|
|
0,025 |
0,05 |
0,075 |
0,1 |
0,125 |
|
|
|
|
|
длина, м |
|
|
|
|
|
|
б |
|
|
|
1700 |
|
|
|
|
|
|
1650 |
|
|
|
|
|
Гц |
1600 |
|
|
|
|
|
частота, |
|
|
|
|
|
|
1550 |
|
|
|
|
|
|
1500 |
|
|
|
|
|
|
|
1450 |
|
|
|
|
|
|
1400 |
|
|
|
|
|
|
0.025 |
|
0.05 |
0.075 |
0.1 |
0.125 |
|
|
|
|
длина, м |
|
|
|
|
|
|
г |
|
|
Рис. 1. Зависимости 1, 2, 3, 4-й частот от местоположения трещины
На рисунке 2, а, б, в, г– зависимость частот от величины трещины.
95 |
|
|
|
94 |
|
|
|
93 |
|
|
|
92 |
|
|
|
91 |
|
|
|
90 |
|
|
|
89 |
|
|
|
88 |
|
|
|
87 |
|
|
|
0.004 |
0.008 |
0.012 |
0.016 |
|
|
а |
|
595 |
|
|
|
590 |
|
|
|
585 |
|
|
|
580 |
|
|
|
575 |
|
|
|
570 |
|
|
|
565 |
|
|
|
0.004 |
0.008 |
0.012 |
0.016 |
580 |
|
|
|
570 |
|
|
|
560 |
|
|
|
550 |
|
|
|
540 |
|
|
|
530 |
|
|
|
520 |
|
|
|
510 |
|
|
|
500 |
|
|
|
0.004 |
0.008 |
0.012 |
0.016 |
|
|
б |
|
1800 |
|
|
|
1600 |
|
|
|
1400 |
|
|
|
1200 |
|
|
|
1000 |
|
|
|
800 |
|
|
|
600 |
|
|
|
400 |
|
|
|
200 |
|
|
|
0 |
|
|
|
0.004 |
0.008 |
0.012 |
0.016 |
в |
г |
Рис. 2. Зависимостьчастототвеличинытрещины
95
Таким образом, величина собственных частот колебаний служит надежным диагностическим признаком при решении задач вибродиагностики методами математического моделирования.
Методика позволяет строить эффективные математические модели элементов механических конструкций САУ ГТД и может быть использована для более широкого класса объектов.
Библиографический список
1.Бабаков И.М. Теория колебаний / И.М. Бабаков. – М.: Машиностроение, 1968.
2.Бублик Б.Н. Численное решение динамических задач теории пластин и оболочек / Б.Н. Бублик. – М.: Машиностроение, 1976.
3.Каплун А.Б. ANSYS в руках инженера / А.Б. Каплун. – М.:
Мир, 2003.
4.Морозов Н.Ф. Математические вопросы теории трещин / Н.Ф. Морозов. – М.: Машиностроение, 1984.
Получено 25.01.2007
96
ЭЛЕКТРОМЕХАНИЧЕСКИЕ ОБЪЕКТЫ И СИСТЕМЫ УПРАВЛЕНИЯ
УДК 681.322; 681.325
С.И. Белов
Пермский государственный технический университет
МОДУЛЬ РЕГИСТРАЦИИ АВАРИЙНЫХ РЕЖИМОВ РАБОТЫ СИЛОВЫХ ТРАНСФОРМАТОРОВ
Дается краткое описание регистратора аварийных режимов работы силовых трансформаторов. Приводится функциональная схема модуля. Статья может быть полезна преподавателям, аспирантам и студентам электротехнических специальностей, а также инженерам-проектировщикам, занимающимся автоматизацией трансформаторныхподстанций.
В энергетической отрасли сложилась ситуация, когда около 50 % мощных силовых трансформаторов выработали свой ресурс. Однако опыт эксплуатации показывает, что более 80 % отказов связано не с выработкой ресурса, а в результате образования и развития различных дефектов. При этом в подавляющем большинстве случаев дефекты связаны с неудовлетворительным состоянием изоляции – бумажной или масляной.
Для нормальной работы любого предприятия важно, чтобы оборудование находилось в хорошем состоянии как можно большее время. Неожиданные поломки могут быть причиной значительных экономических потерь. Снижение производства и дорогостоящие ремонтные работы приводят к уменьшению доходов, что может значительно снизить прибыль предприятия. Кроме того, при этом возникают проблемы, связанные с уменьшением степени безопасности персонала, снижением качества продукции и, как следствие, возможным ухудшением репутации предприятия. Поэтому очевидно, что такие поломки не могут быть допущены. Для решения этих проблем должен быть найден качественно новый подход к проведению технического обслуживания машинного оборудования [1].
Традиционные подходы заключаются в эксплуатации машины до тех пор, пока она не выйдет из строя, или в проведении запланированных ремонтов через заданные интервалы времени. Оба подхода
98
имеют недостатки и в условиях современных технологий они отживают свой век.
Современный подход заключается в измерении и отслеживании параметров состояния машины при ее нормальной эксплуатации и проведении ремонта только тогда, когда результаты соответствующих измерений указывают на его необходимость. Этот подход получил название – «техническое обслуживание на основе реального состояния машинного оборудования».
Только применяя современные методы контроля состояния оборудования, можно без больших затрат выполнить те высокие требования, которые предъявляются к его техническому состоянию. При этом основное внимание следует уделять своевременному получению информации о состоянии машины в данный момент, позволяющей своевременно обнаружить возможные поломки, и планированию оптимального графика профилактических осмотров и ремонтов.
При увеличении числа точек замера и сложности выявления неисправностей наиболее экономичным решением становится применение систем на базе ЭВМ. Типичная система включает в себя устройства для проведения замера с последующим анализом полученных результатов и выявления неисправностей на месте эксплуатации оборудования с использованием диагностических возможностей ЭВМ.
Применение программы профилактического технического обслуживания позволяет определить с большой эффективностью состояние машинного оборудования. Такие системы способны выдавать предупредительную информацию на самых ранних стадиях возникновения потенциальных неисправностей и позволяют определить их причину, а также могут использоваться для составления планов технического обслуживания и графиков ремонта. Следовательно, такие системы могут предупредить аварию с катастрофическими последствиями, уменьшить вынужденные перерывы в работе, увеличить срок службы установки и уменьшить стоимость затрат на техобслуживание.
Сегодня на смену традиционным релейным защитам на электромеханической элементной базе всё активнее приходят современные цифровые устройства, сочетающие в себе функции защиты, автоматики, управления и сигнализации. Использование цифровых терминалов дает возможность повысить чувствительность защит и значительно уменьшить время их срабатывания, что в совокупности с высокой
99
надежностью позволяет существенно снизить величину ущерба от перерывов в электроснабжении [2].
Кроме того, появляется возможность построения автоматизированной системы управления технологическим процессом подстанций на базе этих терминалов и интегрирования ее с АСУ ТП верхнего уровня. На основании этого можно говорить о перспективности перехода к использованию цифровых терминалов в качестве основных устройств релейной защиты и автоматики электрических сетей. Микропроцессорные реле обеспечили более высокий уровень надежности электроснабжения и облегчили работу обслуживающего персонала.
FAULT RECORDER разрабатывался как часть (модуль) диагностической системы TDM, системы диагностики трансформаторов в реальном времени.
FAULT RECORDER, модуль регистрации аварийных режимов работы силовых трансформаторов, предназначен для мониторинга, сигнализации состояния и архивации нештатных режимов работающего трансформатора, а также для отслеживания и записи реакции систем релейной защиты на аварийные режимы работы трансформатора. Данный модуль позволит иметь полную информацию о состоянии работающего трансформатора как с данными аварийного режима, так и с предаварийной ситуацией. Что в сочетании с современными методами обработки и накопленными человечеством знаниями даст ответ касательно причин возникновения того или иного отказа оборудования или поможет в устранении такового еще до его возникновения. Это в конечном счете скажется на затратах, необходимых для обслуживания и ремонта трансформаторного оборудования.
Модуль выполняет аварийную регистрацию параметров, необходимых для диагностики первичного оборудования. Все регистрируемые параметры и осциллограммы записываются в энергонезависимую память, где могут храниться без питания в течение 10 лет. Встроенные часы реального времени с энергонезависимым питанием обеспечивают точную регистрацию момента аварии даже без синхронизации от системы верхнего уровня. Это облегчает разбор аварий на удаленных и необслуживаемых подстанциях, которые, как правило, выполнены на переменном оперативном токе, и при локализации повреждения на них возможна потеря оперативного питания.
Важным требованием к устройствам релейной защиты автоматики, применяемым на станциях с переменным оперативным током,
100