
Механическое оборудование предприятий по производству вяжущих строи
..pdfТ а б л и ц а 1. Материалы, применяемые при изготовлении основных деталей технологического оборудования для производства цемента
Оборудо |
Деталь |
Изнашива |
Темпера |
Материал |
|
вание |
ние |
тура |
сре |
||
|
|
|
ды, |
°С |
|
Средний срок служ бы, год
Щеховая |
Броневые |
плиты |
дробилка |
подвижной и |
|
|
неподвижной |
|
|
щек |
|
|
Распорные плиты |
|
Молотковая |
Молоток |
|
дробилка |
Нижние |
колос- |
|
||
|
ники |
колос- |
|
Верхние |
|
|
ники |
|
Сырьевая |
Бронефутеровоч- |
|
трубная |
ные плиты: |
|
мельница |
первой |
ка- |
|
меры |
ка- |
|
второй |
|
|
Междукамерные |
|
|
перегородки |
|
|
Корпус |
мель |
|
ницы |
|
Цементная |
Бронефутеровоч- |
|
мельница |
ные плиты: |
|
|
первой |
ка |
|
меры |
ка |
|
второй |
|
|
меры |
бро- |
|
Прокатная |
|
|
нефутеровка |
|
|
первой камеры |
|
|
Вкладыши |
цап- |
|
фовых |
под |
|
шипников |
Абразивное |
|
|
Усталост- |
|
— |
ное |
|
_ |
Абразивное |
|
|
|
|
— |
|
|
— |
|
|
— |
|
|
— |
|
|
— |
Усталост |
|
|
ное |
|
|
Абразивное |
До |
100 СС |
|
До |
100 °С |
|
До |
100 °С |
Усталост |
До |
100 °С |
ное |
|
|
Вращаю Зубчатый |
венец |
Усталост |
До |
180 °С |
|
щаяся печь |
|
ное |
До |
50 °С |
|
Подвенцовая ше |
То же |
||||
стерня |
|
|
До 300 |
°С |
|
Бандаж |
|
|
|||
Опорный ролик |
|
До |
60 |
°С |
|
Обечайки |
кор |
|
До 350 |
°С |
|
пуса |
и баш |
Коррозион |
Свыше |
||
Сегменты |
|||||
маки |
разгру |
но-механи |
1000 °С |
||
зочного |
порога |
ческое |
Около |
||
Лейки, стаканы |
То же |
||||
рекуператоров |
|
1000 °С |
Сталь 110Г13.Г1 2,5
Чугун СЧ 18 |
0,5 |
Сталь |
0,25 |
120Г13Х2Л |
0,5 |
Сталь 110Г13Л |
|
То же |
3 |
Сталь |
1,5 |
120Г13Х2Л |
2,6 |
Резина |
|
Сталь 110Г13Л |
1 |
Сталь 09Г2С |
18 |
Сталь 110Г13Л |
1 |
То же |
1,8 |
Сталь М75, |
3 |
М76 |
|
Баббит Б83, |
4 |
Б16 |
|
Сталь 35ХМЛ |
15 |
Сталь |
10 |
34ХН1МА |
20 |
Сталь 30ГСЛ |
|
Сталь 35Л |
5 |
Сталь 09Г2С |
8 |
Сталь |
1,5 |
40Х24Н12СЛ |
|
То же |
2 |
|
|
|
|
|
£ |
Оборудо- |
|
Изнашнва- |
Темпера |
|
у- >» |
Деталь |
Материал |
~ Ч ЕС |
|||
ва'н'ие |
ние |
тура сре |
-о О |
||
|
ды, °С |
|
К йй |
||
|
|
|
|
|
о о |
|
|
|
|
|
и 5\о |
Колоснико- |
Колосники зон: |
Коррознон- |
|
вый охла- |
горячей |
||
дитель |
|
|
но-механи- |
клинкера |
средней |
ческое |
|
|
То же |
||
|
холодной |
» |
|
|
Звено транспор- |
Абразивное |
|
|
тера |
уборки |
изнаши- |
|
просыпи |
вание не- |
|
|
|
|
закреплен |
|
|
|
ным абра- |
|
Била дробилки |
зивом |
|
Конвейер |
Абразивное |
||
Колосник |
|
Коррозион |
|
ный каль- |
|
|
но-механи |
цинатор |
Бортовые плиты |
ческое |
|
|
То же |
||
Крановые ' |
Опорные ролики |
» |
|
Ходовые |
колеса |
Усталост |
|
шламовые |
Лопасти |
|
ное |
мешалки |
|
Гидроабра |
|
|
Конические ше |
зивное |
|
|
Усталост |
||
Пневмо- |
стерни |
|
ное |
Шнек |
|
Газоабра |
|
винтовые |
|
|
зивное |
насосы |
|
|
|
Пневмо- |
Гильза |
загру |
То же |
Кольцо |
» |
||
камерный |
зочного |
кла |
|
насос |
пана |
|
|
Шламовый |
То же |
» |
|
Рабочее |
колесо |
Гидроабра |
|
насос |
Диск |
|
зивное |
|
|
То же |
До |
1300 °С |
Сталь |
0,75 |
|
- |
50Х24Ы12САЛ |
|
До |
700 °С |
Сталь |
1 |
До |
200 °С |
40Х24Н12САЛ |
1,5 |
Сталь 45Л |
|||
До |
300 °С |
То же |
1 |
До |
150 °С |
Сталь 110Г13Л |
0,25 |
До |
1000 °С |
Чугун ЖЧС 5 |
1,5 |
До |
900 °С |
Сталь Х9С2Л |
2,5 |
До |
1000 °С |
Чугун ЖЧС 5 |
1,2 |
|
— |
Сталь 55Л, |
1,25 |
|
|
45Л |
2 |
|
— |
Сталь 35Л |
|
|
— |
Стали 45Л, |
2 |
До |
180 °С |
40Х |
0,2 |
Сталь 45 с |
|||
|
|
наплавкой |
|
|
|
твердым спла |
|
До |
180 °С |
вом |
0,4 |
То же |
|||
До |
150 °С |
Резина |
0,07 |
|
|
ИРП-1385 |
|
Свыше |
Резина |
0,07 |
|
150 °С |
ИРП-1287 |
|
—Чугун СЧ 18 0,1
— |
То же |
0,07 |
поверхностной закалке термической обработке подвергается только поверхностный слой детали на небольшую глубину; нагрев детали, как правило, производится токами высокой частоты (ТВЧ). Закалка придает стали высокую твердость, но увеличивает ее хрупкость. Для устранения хрупкости, снятия внутренних напряжений, а также для повышения ударной вязкости сердцевины деталей применяют отпуск.
Улучшение состоит из двух операций — закалки и высокотем пературного отпуска и применяется для повышения прочности деталей при сохранении их ударной вязкости или увеличения ее.
12
Стали с содержанием углерода до 0,25 % имеют большую удар ную вязкость, но не воспринимают закалки. Для улучшения меха нических характеристик такие стали подвергают химико-термиче ской обработке.
Широкое распространение получили цементация и азотирование. Цементация заключается в насыщении поверхностного слоя дета лей углеродом на глубину до 0,2 мм. После закалки поверхностный слой цементованных деталей приобретает высокую твердость, а серд цевина остается вязкой. Азотирование заключается в диффузион ном насыщении поверхностных слоев детали азотом. Наибольшее распространение получили газовое и жидкостное азотирование в пе чах и ваннах. В последние годы внедряется более прогрессивный и эффективный способ азотирования — ионное азотирование, обла дающее по сравнению с классическим рядом преимуществ. Основ ными преимуществами являются ускорение процесса в 3—5 раз, большая упругость и прочность слоя.
Механическое упрочнение заключается в упрочнении поверх ностных слоев металла пластическим деформированием. Это простой и эффективный метод упрочнения рабочих поверхностей деталей из стали, чугуна и различных цветных сплавов. Механическое упроч нение производится различными способами: дробеструйным, накат кой гладкими роликами или шариками, чеканкой, ротационно-удар ным наклепом шариками, дорнованием и др. Таким упрочнением удается повысить прочность деталей из недорогостоящих материа лов, избежать применения высоколегированных сталей глубокой прокаливаемое™. Упрочнение повышает предел выносливости де талей, особенно валов, имеющих концентраторы напряжений (вы точки, галтели).
Более широкое распространение получают методы упрочнения, основанные на нанесении на рабочие поверхности деталей износо стойких слоев с помощью наплавки и напыления.
При изготовлении основных деталей оборудования для произ водства вяжущих строительных материалов применяют материалы, приведенные в табл. 1.
§ 5. Основные понятия о надежности оборудования
Для повышения производительности и качества готовой продукции можно реализовать потенциальные возможности техно логической линии производства цемента лишь тогда, когда каждый вид оборудования в отдельности и вся линия в целом будут иметь высокую надежность в работе.
В теории надежности оперируют понятиями «система» и «эле мент». Под системой понимают совокупность элементов, объединен ных функционально и конструктивно, под элементами — недели мые в дальнейшем части системы. Примерами элементов редуктора являются подшипники, зубчатые колеса редуктора (в этом случае редуктор— система); примерами систем — помольный агрегат, где входящие в его состав мельница., редуктор, сепаратор являются
элементами. Когда понятие надежности применяют и к системе и
кее элементам, пользуются общим наименованием — объект. Элемент и система могут иметь два состояния: работоспособное,
при котором объект способен выполнять заданные функции, сохра няя значения эксплуатационных показателей в пределах, уста новленных нормативно-технической документацией (НТД); нера ботоспособное, при котором значение хотя бы одного заданного параметра (функции) не соответствует требованиям^НТД. Нарушение работоспособности и переход объекта из работоспособного состоя ния в неработоспособное называют отказом.
Надежность — комплексное свойство, которое в зависимости от назначения объекта и условий его эксплуатации может включать безотказность, долговечность, ремонтопригодность и сохранность в отдельности или в определенном сочетании этих свойств как для системы, так и для ее элементов. При соблюдении правил транспор тирования и хранения оборудование не теряет своей работоспо собности, поэтому будут рассмотрены только безотказность, долго вечность и ремонтопригодность.
Безотказность — свойство объекта непрерывно сохранять ра ботоспособность в течение некоторого времени или наработки. Под наработкой понимают продолжительность или объем работы объекта, выраженный в циклах, тоннах или других единицах. К показателям безотказности относятся: вероятность безотказной работы, сред няя наработка на отказ, средняя наработка до отказа и др.
Для оборудования цементных заводов безотказность — важный, но не решающий показатель. При возникновении отказов оборудо вание ремонтируют и оно продолжает работать до какого-то пре дельного состояния, которое определяет другой показатель — дол говечность.
Долговечность — свойство объекта сохранять работоспособность до наступления предельного состояния при установленной системе технического обслуживания и ремонта. Под предельным состоянием подразумевают состояние объекта, при котором его дальнейшая эксплуатация должна быть прекращена вследствие неустранимого нарушения требований безопасности, неустранимого выхода задан ных параметров за установленные пределы, неустранимого снижения эффективности эксплуатации ниже допустимой или необходимости проведения капитального ремонта. Долговечность характеризуется техническим ресурсом и сроком службы.
Технический ресурс — это наработка объекта от начала эксплу атации или ее возобновления после капитального ремонта до насту пления предельного состояния. Срок службы — календарная про должительность эксплуатации объекта в те же сроки. Различие между техническим ресурсом и сроком службы заключается в том,
что при расчетах ресурса |
учитывают только |
время работы, а при |
||||
расчетах срока |
службы, |
кроме того, — время |
простоев. |
дроби |
||
Показателями |
долговечности, |
например |
для |
щековых |
||
лок является средний ресурс до |
первого |
капитального |
ремонта |
|||
(в часах или в объемах переработанной породы), |
а пневмовинтовых |
14
насосов — средний ресурс (в часах). При этом предельное состоя ние для щековых дробилок определяется необходимостью замены или ремонта шатуна, подвижной щеки, эксцентрикового вала, а для пневмовинтовых насосов — увеличением радиального зазора между поверхностью броневой гильзы и шнеком более 5 мм.
Долговечность и безотказность — это показатели, дополняющие один другого и связанные между собой.
Ремонтопригодность — свойство объекта, заключающееся в при способлении к предупреждению и обнаружению причин возникно вения его отказов, повреждений и устранению их последствий пу тем проведения ремонта и технического обслуживания.
С точки зрения ремонтопригодности оборудование должно удов летворять следующим требованиям:
конструкция должна быть рационально расчленена на отдельно изготовляемые и обслуживаемые элементы;
конструктивные элементы должны быть доступны для обслужи вания и ремонта;
ответственные подшипниковые узлы должны быть оснащены средствами диагностики, контролирующими давление масла в си стеме и температуру нагрева узла, а также отключающими привод оборудования при повышении температуры подшипникового узла выше допустимой;
в конструкции машины должны быть сменные и регулируемые элементы, подверженные наиболее интенсивному воздействию рабо чих нагрузок, внешней среды и др.
Комплексными показателями надежности являются: коэффи циент готовности, коэффициент технического использования и др. Для оборудования цементной промышленности более важным яв ляется коэффициент технического использования /Ст. и, характери зующий работоспособность оборудования в определенный проме жуток календарного времени:
KT. u = [ T - ( t v + t0)]/T, |
(1) |
где Т — календарное время эксплуатации оборудования; /р и /0 — плановое время соответственно на ремонт и техническое обслуживание, необходимое для восста новления работоспособности оборудования, за время Т
Плановый коэффициент технического использования оборудования определяют по действующим системам планово-предупредительного ремонта (ППР).
При определении фактического Кт.и учитывают все плановые и внеплановые простои оборудования (обычно за месяц, квартал, год).
Отказы оборудования классифицируют по нескольким призна кам. В зависимости от скорости изменения заданных параметров объекта различают внезапные (аварийные) и постепенные отказы. Примерами внезапных отказов могут служить поломки осей опорных роликов вращающихся печей, разрушение зубчатых колес приводов, разрыв звеньев цепей транспортеров уборки просыпи охладителей клинкера и др. Постепенные отказы характеризуются постепенным изменением параметров и проявляются в основном в виде износа
деталей или ухудшения механических характеристик их в резуль тате усталости и воздействия высоких температур (износ пера шнека пневмовинтового насоса, усталостное выкрашивание рабочих по верхностей бандажей и др.).
Кроме того, различают отказы элементов и отказы параметров. Отказы элемента — это выход из строя какого-либо конструктив ного элемента, в результате чего система переходит в неработоспо собное состояние. Например, поломка шламового питателя вращаю щейся печи (при отсутствии дублирующего) приводит к остановке всего печного агрегата. Отказ параметров — это случай, когда фор мально элементы системы и вся техническая система находятся в рабо тоспособном состоянии, но в связи с нарушениями технологических режимов готовая продукция не соответствует требованиям НТД. Например, вследствие невозможности одинакового приготовления сырьевой муки в разных силосах химический состав смеси, подавае мой в агрегат, обычно резко изменяется при переключении питания с одного силоса на другой. Однако, по ряду причин машинист вращаю щейся печи не всегда успевает изменить тепловой режим обжига, что приводит к ухудшению качества выпускаемого клинкера.
Отказы элементов характеризуют надежность технической си стемы, отказы параметров — надежность технологической системы. В задачу технической системы входит обеспечение требуемого коэф фициента технического использования линии, а технологической си стемы — обеспечение заданных режимов технологического процесса.
Комплекс методов и средств, направленных на оптимизацию уровня надежности технической и технологической систем, образует общую систему обеспечения надежности технологической линии.
Уровень надежности технической системы линии зависит не только от надежности каждого вида входящего в нее оборудования, но и от характера их связи между собой. При последовательной связи обору дования в системе отказ любого из них приводит к отказу всей линии. Надежность системы можно повысить введением параллельной связи в ее звеньях. В этом случае при отказе одного звена его функции будет выполнять параллельное (дублирующее) и система не потеряет работоспособности. Дальнейшего повышения надежности системы можно добиться введением в нее склада-накопителя. При отказе одного элемента или одновременно нескольких последующая система будет продолжать функционировать определенное время за счет ре зерва склада-накопителя.
Управление надежностью технической системы путем введения дополнительных связей и складов-накопителей широко используют при проектировании технологических линий. Как правило, дубли руют вспомогательное оборудование: шламовые и цементные насосы, транспортеры, шламо- и цементопроводы. Перед каждым технологи ческим переделом предусматривают промежуточные склады, запасы которых должны учитывать продолжительность возможного отказа предыдущего технологического передела. Для бесперебойного пи тания вращающихся печей сырьевым материалом необходимый запас его на складе готового сырья обеспечивают путем превышения мощ-
16
ности предыдущих технологических переделов по сравнению с мощ ностью обжигового передела.
Для обеспечения работоспособности технологической линии та кое же значение имеет надежность ее технологической системы. Дан ная система должна контролировать основные параметры технологи ческого процесса производства и осуществлять оперативное вмеша тельство при их отклонении от заданных норм.
Технологическая система — это комплекс организационно-тех нических мероприятий, предусматривающих возможность усредне ния сырьевых материалов на стадии добычи, доведение сырьевых материалов перед тепловой обработкой до заданных химического и гранулометрического составов, соблюдение режимов обжига и по мола клинкера. Для контроля технологических параметров произ водственных процессов в настоящее время разработаны и находят широкое применение комплексы приборов, а также автоматические системы управления технологическими процессами (АСУТП).
Техническая и технологическая системы взаимосвязаны: при снижении уровня одной соответственно изменяется уровень и дру гой. Например, при обжиге шлама с неоткорректированным химиче ским составом в печи слабо образуется защитная обмазка, что при водит к преждевременному изнашиванию футеровки печи и прожо гам ее корпуса. Одновременно с этим обжиг некондиционного сырья вызывает образование большого количества мелкого клинкера, что снижает качество полуфабриката, способствует его большей просыпи через щели колосников и подрешеточное пространство охладителя и, как следствие, разрушению колосников и транспортеров уборки про сыпи.
Г л а в а 2
ПРОИЗВОДСТВО ЦЕМЕНТА
§ 6. Способы производства
В зависимости от подготовки сырьевых материалов к об жигу различают мокрый, сухой и комбинированный (полусухой) спо собы производства цемента.
При мокром способе дробленые сырьевые материалы перемеши ваются, измельчаются и корректируются с добавлением воды. Полу чаемая при этом сметанообразная масса влажностью 32—45 % — шлам — подается на обжиг в печной агрегат. При сухом способе дроб леные сырьевые материалы перемешиваются, измельчаются с одно временной сушкой и корректируются. Полученный порошок влаж ностью до 1 % — сырьевая мука — подается на обжиг в печной аг регат.
При комбинированном способе шлам, подготовленный по мокрому способу, подвергается глубокому обезвоживанию в фильтрах. Полу чающийся в результате такой обработки кек влажностью 15—20 %
подается сразу на обжиг в печной агрегат или после измельчения с одновременной сушкой — в печной агрегат с циклонными тепло обменниками или с конвейерным кальцинатором.
Выбор способа производства определяется технологическими и технико-экономическими факторами: химическим составом и физико механическими свойствами сырья, видом и стоимостью топлива, про ектными особенностями цементного завода и др.
Наиболее простым является мокрый способ, который до 60-х гг XX в. был широко распространен в мировой “Практике благодаря простоте подготовки шлама, его корректирования и гомогенизации; отсутствию выделения пыли при дроблении, помоле, смешивании и транспортировании сырьевых материалов; простоте конструкции и управления работой печного агрегата.
Вотечественной промышленности печные агрегаты мокрого спо соба также нашли преимущественное применение. Производство вращающихся печей в СССР было организовано в 1927 г. Печи этого периода имели небольшие размеры (3x51,3, 3x60,5 м и др.) и невы сокую производительность. Наибольшее развитие печные агрегаты мокрого способа получили в послевоенные и особенно в 60-е гг., когда были созданы мощные печи размерами 5x185 м.
Внастоящее время в СССР насчитывается более 350 печных агре гатов мокрого способа, на которых производится значительная доля выпуска цемента.
Сухой способ производства клинкера впервые стали применять в начале XIX в. Тогда в период зарождения цементной промышлен ности этот способ, основанный на использовании шахтных печен периодического действия, был практически единственным. Даль нейшее развитие цементной промышленности с конца XIX в. до первой половины XX в. происходило в основном по пути совершен ствования вращающихся печей цокрого способа, хотя производство цемента по сухому способу не прекращалось. Основными сдержива ющими факторами в расширении производства по сухому способу были трудности в обеспечении сырьевыми материалами необходи мого качества: определенной влажности, однородности химического состава, предельного содержания веществ, несоответствие которого норме ухудшало течение технологического процесса обжига и др.
Развитие в 60—70-е гг. техники сушки минерального сырья и создание разнообразного технологического оборудования (мощных сушильных барабанов, дробилок-сушилок) позволило шире приме нять сухой способ производства при высокой природной влажности сырья.
Создание усреднительных складов, машин для формирования и разработки штабелей, проектирование и строительство установок для пневматической гомогенизации сырьевой муки, внедрение бы стродействующих анализаторов и систем оперативного технологиче ского контроля, создание АСУТП сырьевого передела обеспечили возможность получения сырьевых смесей несбходимсго состава и позволили производить цемент высокого качества по сухому спо собу
18
Опыт эксплуатации современных технологических линий сухого способа производства цемента, накопленный цементной промышлен ностью в СССР и за рубежом, позволил выявить их высокие технико экономические показатели: более низкий расход теплоты на обжиг клинкера (в современных печах с запечными теплообменниками 3350 кДж на 1 кг клинкера, по сравнению с 6281 кДж на 1 кг клин кера в печах по мокрому способу); меньшие размеры печей, в сравне нии с печами мокрого способа при одинаковой производительности и, следовательно, меньшие металлоемкость, капитальные затраты на строительство и потери теплоты через корпус печи; снижение объе мов отходящих печных газов и др.
Вместе с тем расширение производства цемента по сухому спо собу вызвало необходимость решения ряда проблем. Наиболее важ ная из них — повышение требований к техническому уровню проек тирования, качеству изготовления технологического и вспомогатель ного оборудования, его монтажу, наладке и организации правиль ной эксплуатац* и. Это связано с тем, что по проектным, компоновоч ным решениям, набору оборудования, уникальности технологиче ских схем и схем автоматического регулирования технологических процессов современные линии сухого способа производства цемента значительно сложнее, чем линии мокрого способа. Тем не менее бла годаря высоким технико-экономическим показателям сухой способ находит fece более широкое применение в мировой практике. Так, к концу 70-х гг. большую часть цемента в ГДР, ЧССР, ФРГ, Японии
инекоторых других странах производят по сухому способу.
Внастоящее время в СССР намечена программа увеличения вы пуска цемента сухим способом путем строительства новых заводов на базе месторождений кондиционных сырьевых материалов, а также реконструкции ряда действующих цементных заводов мокрого спо соба.
Комбинированный способ пока'не нашел применения в отечест венной практике. В ближайшие годы отдельные цементные заводы мокрого способа, работающие на сырье с большими отклонениями по химическому составу и высокой карьерной влажностью, планируется оснастить фильтрующими установками для глубокого обезвоживания шлама.
§7. Технологические линии цементных заводов
В укрупненном виде цементное производство можно раз делить на следующие технологические переделы.
A.Добыча, первичная обработка сырья в горном цехе (карьере)
идоставка его на территорию цементного завода.
Б. Подготовка сырья в сырьевом цехе — измельчение и обеспе чение однородности сырья заданного химического состава; при су хом способе производства также предварительная сушка сырья в про цессе измельчения.
B. Тепловая обработка сырья в печных агрегатах цеха обжига с получением клинкера — исходного полуфабриката для производ ства цемента.
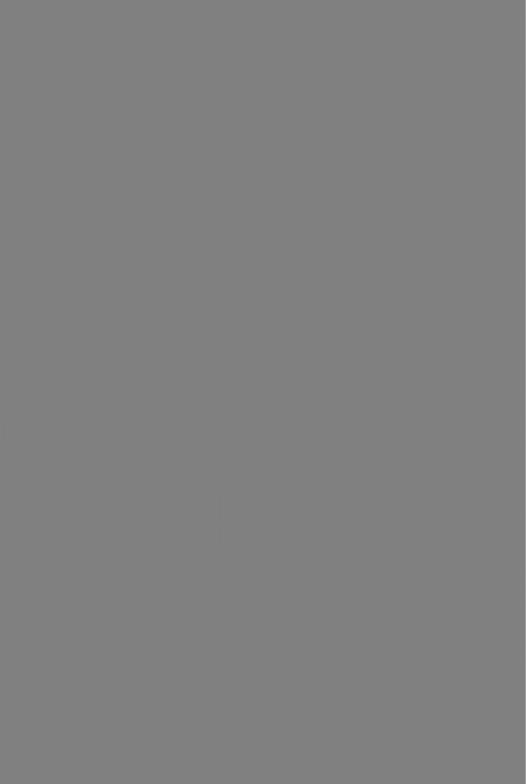